What is POP Package Substrate?
POP Package Substrate Manufacturer and POP package service. the Package Substrate will be made with Showa Denko and Ajinomoto High speed materials.
In today’s PCB engineering field, POP (Package on Package) substrate is a crucial technology. It represents an advanced electronic packaging method in which two or more integrated circuit (IC) packages are stacked together and connected to each other through solder balls or other interconnection methods.
POP Package Substrate is designed to achieve the goal of integrating multiple functional modules in a limited space. By stacking multiple IC packages together, higher performance and more functionality can be achieved in small electronic devices while minimizing form factor. This layered design provides flexibility, allowing electronic product designers to achieve more innovation and functional integration within restricted spaces.
In POP Package Substrate, each IC packaging layer is connected to the underlying substrate and is connected to other layers through solder balls or other interconnection means. This tight stacking structure not only enables vertical integration of the circuit board, but also provides highly reliable electrical connections and thermal management performance.
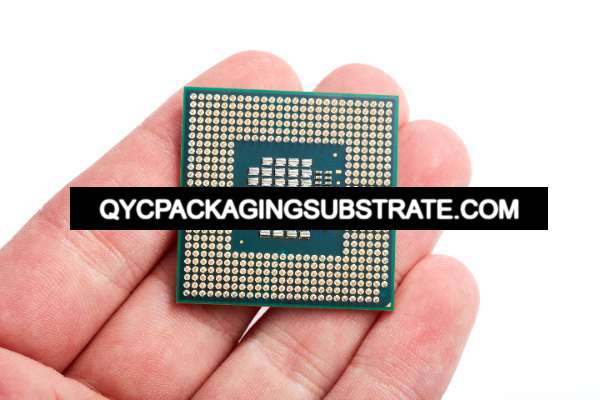
POP Package Substrate
By adopting POP Package Substrate technology, electronic equipment manufacturers can achieve more compact and feature-rich product designs without sacrificing performance and reliability. From smartphones and tablets to medical equipment and automotive electronics, POP Package Substrate has a wide range of applications and provides important support for the development and innovation of modern electronic products.
What are the types of POP Package Substrate?
In the field of modern PCB engineering, POP (Package on Package) substrates have attracted much attention for their diversity and flexibility. It includes the following types:
Organic POP substrates are made from organic materials that are flexible and cost-effective. This makes organic POP substrates ideal for many applications, especially for projects that require lightweight and cost advantages.
Ceramic POP substrates are known for their excellent thermal management and reliability. This type of substrate effectively dissipates heat and ensures components maintain a stable temperature while operating, thereby improving overall system performance and reliability.
Metal-based POP substrates provide enhanced thermal conductivity and are suitable for high-power applications. Its metal base can effectively absorb and dissipate heat, allowing the substrate to work in high-temperature environments for a long time without damage, thereby meeting the demand for high performance and reliability.
Flexible POP substrates are designed to meet applications requiring flexibility and space-saving design. The flexibility of this substrate enables it to adapt to complex assembly structures and tight spaces while maintaining good electrical performance and reliability.
Each type of POP Package Substrate has unique advantages and applicability, and the most appropriate type can be selected based on specific project needs. Whether pursuing cost-effectiveness, thermal management, or space design optimization, POP Package Substrate can provide reliable solutions to promote innovation and development in electronic design.
What are the advantages of using POP Package Substrate?
Using POP Package Substrate brings many advantages in PCB engineering, which make it an important part of modern electronic packaging. Here are a few significant advantages of using POP Package Substrate:
First of all, POP Package Substrate can efficiently utilize space and achieve compact design. By stacking two or more IC packages together, multiple functions can be integrated in a limited space, thereby saving board space and allowing the device to be more compact, which is crucial especially for portable devices.
Secondly, POP Package Substrate has enhanced thermal dissipation, which helps ensure the optimization of device performance. Since electronic devices generate heat during operation, good thermal management is key to ensuring proper operation and extending the life of the device. Through its design and material selection, POP Package Substrate is able to effectively dissipate heat, thereby increasing the reliability and stability of the device.
In addition, POP Package Substrate can improve electrical performance and signal integrity. Through precise wiring and optimized design, the loss in signal transmission can be reduced and the stability and reliability of the signal can be improved, thus improving the overall performance of the device.
In addition, using POP Package Substrate can also achieve miniaturization while ensuring reliability. Due to its compact design and high integration characteristics, POP Package Substrate is able to integrate multiple functional modules into a small package, thereby achieving miniaturization and lightweight of the device, providing greater flexibility for the design of electronic products. and space.
Finally, POP Package Substrate is a cost-effective solution for a variety of electronic applications. Due to its optimization of design and manufacturing processes, as well as material selection and supply chain optimization, POP Package Substrate is able to provide cost-effective solutions that help manufacturers reduce costs and improve competitiveness.
In summary, using POP Package Substrate can bring many advantages in PCB engineering, including efficient use of space, enhanced thermal dissipation, improved electrical performance and signal integrity, miniaturization, and cost-effectiveness. These advantages make it It has become one of the first choices in today’s electronic packaging field.
Why choose POP Package Substrate?
When we face scenarios that require compactness, enhanced performance and reliability, there are obvious advantages to choosing POP Package Substrate instead of traditional PCB. The design of POP Package Substrate takes into account how to integrate multiple functions in a limited space, making it an ideal choice for portable devices and high-density applications.
Although the traditional PCB (Printed Circuit Board) has been the main carrier of electronic devices in the past few decades, with the continuous development of technology, modern electronic equipment continues to require smaller and higher performance. promote. In this case, traditional PCB often faces problems such as low space utilization and limited heat dissipation performance, while POP Package Substrate can solve these problems well.
First, the stacked design of POP Package Substrate allows multiple packages to be stacked vertically to maximize space utilization. This design makes it possible to implement multiple functions within a limited size, thus meeting the increasingly compact design needs of modern electronic devices. For example, portable devices such as smartphones and tablets need to integrate multiple functions such as processors, memories, and sensors in a limited space, and POP Package Substrate can effectively achieve this goal, making the devices thinner, lighter, and more portable.
Secondly, the design of POP Package Substrate also takes into account the needs for enhanced performance and reliability. By adopting optimized heat dissipation design and electrical connection scheme, POP Package Substrate can provide better thermal management and electrical performance, thereby ensuring that the equipment remains stable and reliable during long-term operation and high-load operation. This is particularly important for some high-density, high-performance application scenarios, such as data center servers, automotive electronic systems, etc.
To sum up, compared with traditional PCB, POP Package Substrate has obvious advantages in terms of compactness, enhanced performance and reliability. Its stacked design makes it possible to implement multiple functions in a limited space, while the optimized heat dissipation design and electrical connection scheme also ensure the stability of the equipment during long-term operation and high-load work. Therefore, for portable devices and high-density applications, choosing POP Package Substrate is a wise choice.
What is the manufacturing process of POP Package Substrate?
The manufacturing process of POP Package Substrate is a complex and precise process that involves multiple critical steps to ensure the quality and performance of the final product. The main stages of this process are described below:
The first step in manufacturing POP Package Substrate is to prepare the substrate. This typically involves selecting appropriate materials and surface treatments to ensure accuracy and reliability in subsequent layer build-up and assembly of components. Common substrate materials include organic, ceramic, or metallic substrates, with the choice depending on the application requirements and design specifications.
After substrate preparation is complete, the next step is layer deposition. This involves layering various layers together to build the complete POP Package Substrate. These layers may include conductive, insulating and other functional layers, each of which is precisely designed and machined to ensure the performance of the final product.
Once the layer stacking of the substrate is complete, next comes the component assembly stage. At this stage, IC packages and other electronic components are precisely placed on the substrate and connected through soldering or other interconnection methods. This process requires a high degree of precision and automation to ensure the correct position and connection of each component.
The last critical step is surface preparation. At this stage, the assembled POP Package Substrate will undergo surface treatment to improve its electrical performance, durability and reliability. This may include cleaning, gold plating or other chemical treatments to ensure the final product meets quality standards and is suitable for the specific application.
Throughout the manufacturing process, advanced technology plays a key role. For example, laser drilling can be used to create tiny holes in substrates to facilitate the mounting and interconnection of electronic components. Photolithography can be used to precisely define the patterns and structures of various layers. Automatic assembly equipment can efficiently and accurately place components on substrates, improving production efficiency and product quality.
To sum up, the manufacturing process of POP Package Substrate is a complex and precise process that requires a high degree of technology and automated equipment to ensure the quality and performance of the final product. Through careful design and precise processing, POP Package Substrate can meet the needs of various electronic applications and plays an important role in the field of modern electronic engineering.
What are the applications of POP Package Substrate?
In modern electronic design, POP Package Substrate has become an indispensable component in various industries due to its versatility and reliability. They play an important role in various fields, from smartphones and tablets to automotive electronics and medical equipment.
First, let’s look at the smartphone and tablet space. These portable devices require compact designs to accommodate a large number of functions and electronic components. The stacked design of POP Package Substrate allows the integration of multiple IC packages in a limited space, thereby enabling smaller device designs. In addition, POP Package Substrate’s excellent thermal management capabilities ensure high-performance operation of the device, making it the first choice for mobile phone and tablet manufacturers.
In terms of automotive electronics, POP Package Substrate also plays a key role. Modern cars are equipped with an increasing number of electronic systems for driver assistance, entertainment and communication. Due to limited space and harsh environments in automobiles, POP Package Substrate’s compact design and excellent reliability make it an ideal choice for automotive electronic systems. It is able to withstand high temperatures and vibration while maintaining stable performance.
The medical device field is also actively adopting POP Package Substrate. Medical devices have extremely high performance and reliability requirements because they are directly related to the health and safety of patients. Since medical devices often require miniaturized designs to fit into clinical environments, POP Package Substrate’s compact design and high-performance characteristics are ideal for use in the manufacturing of medical devices.
Overall, POP Package Substrate is widely used in various industries. Its compact design, excellent thermal management capabilities and reliable performance make it ideal for modern electronic designs. With the continuous development of technology, we can foresee that POP Package Substrate will continue to play an important role in future electronic devices, driving progress and innovation in the industry.
How to obtain POP Package Substrate?
When it comes to acquiring POP Package Substrate, our company, as a reputable supplier and manufacturer, provides customers with various types of POP Package Substrate to meet different needs. We have advanced manufacturing facilities and a professional team to provide customized options for personalized production as per the specific requirements of our customers.
Customers can obtain our POP Package Substrate through the following channels:
Official website purchase: Our official website provides detailed product information and specifications, and customers can purchase and place orders directly on the website. Our online shopping platform is easy to use and allows for a quick purchase process.
Contact Sales Team: Customers can directly contact our sales team stating their needs and requirements. Our sales representatives will provide professional advice based on customer needs and assist customers with the order and delivery process.
Customized production: For POP Package Substrate that requires customization, customers can work with our engineering team to jointly design and develop products that meet their specific requirements. We will fully understand our customers’ needs and provide tailor-made solutions.
In addition, our company also provides bulk purchasing facilities to provide customers with more flexible purchasing options and more competitive prices. Whether customers require small quantities of samples or large batch orders, we can meet their needs and ensure timely delivery and quality reliability of products.
In short, by obtaining POP Package Substrate through our company, customers will receive high-quality products, professional technical support and excellent customer service. We are committed to providing our customers with the best solutions to help them succeed in the electronics assembly field.
Cost estimate for POP Package Substrate?
Cost estimation of POP Package Substrate is a complex issue involving multiple factors. Its cost is affected by factors such as substrate material, manufacturing complexity and order quantity. Nonetheless, POP Package Substrate is often significantly cost-effective compared to other packaging solutions, making it the first choice in many applications.
First of all, substrate material is one of the main factors affecting cost. Organic, ceramic, metal-based and flexible materials each have different manufacturing costs. Ceramic substrates are generally more expensive, but have excellent performance in high temperature environments and may be suitable for certain applications. In comparison, organic substrates are lower cost and suitable for many general applications.
Second, manufacturing complexity also has an impact on cost. Manufacturing POP Package Substrate requires precision processing technology and equipment to ensure precise alignment and connection between stacked components. Highly automated production lines and advanced processing technologies may increase manufacturing costs, but also improve production efficiency and quality.
Finally, order quantity is one of the important factors affecting costs. Generally speaking, high-volume orders enjoy lower unit costs because they reduce fixed and unit costs through mass production. In contrast, unit costs for small batch orders may be higher because the fixed costs of the production process need to be spread over fewer products.
Overall, while the cost of POP Package Substrates is affected by a variety of factors, they are generally more cost-effective than other packaging solutions. By selecting the appropriate substrate material, optimizing the manufacturing process, and considering order volume, the cost of POP Package Substrate can be effectively controlled and cost-effective electronic packaging solutions can be achieved in various applications.
Frequently asked questions about POP Package Substrate?
Are POP Package Substrates compatible with various components?
Absolutely. POP Package Substrates are designed to accommodate a wide range of components commonly used in electronic devices. Whether it’s integrated circuits (ICs), resistors, capacitors, or other electronic elements, POP Package Substrates offer versatile compatibility.
What environmental considerations should be taken into account?
POP Package Substrates are manufactured using materials that comply with environmental regulations and standards. However, it’s important to consider factors such as temperature extremes, moisture exposure, and chemical resistance to ensure optimal performance and longevity in different environmental conditions.
How durable and long-lasting are POP Package Substrates?
POP Package Substrates are engineered to withstand the rigors of various applications, offering durability and long-term reliability. The choice of substrate material, surface finishes, and assembly techniques significantly influences their robustness and lifespan. Proper handling, storage, and usage also contribute to extending their longevity.
Can POP Package Substrates facilitate advanced thermal management?
Indeed. One of the key advantages of POP Package Substrates is their ability to enhance thermal dissipation, particularly in compact electronic assemblies where heat management is critical. Through optimized designs and materials selection, POP Package Substrates effectively dissipate heat, ensuring stable performance and prolonging the lifespan of electronic components.
What are the cost implications of adopting POP Package Substrates?
While the initial investment in POP Package Substrates may vary based on factors such as substrate type, complexity, and volume, they offer compelling cost-effectiveness in the long run. The benefits of space savings, improved performance, and reliability often outweigh the upfront costs, making POP Package Substrates a prudent choice for diverse electronic applications.
Can POP Package Substrates be customized to specific requirements?
Certainly. Many manufacturers offer customization options for POP Package Substrates to meet unique design specifications and application needs. From substrate materials and thicknesses to interconnection methods and surface finishes, customization allows for tailored solutions that optimize performance and functionality.