What is Rogers 3010 PCB?
Rogers 3010 PCB Supplier. RO3010 laminates are competitively priced products with exceptional mechanical and electrical stability. This stability simplifies the design of broadband components and allows the materials to be used in a wide range of applications over a very broad range of frequencies. This material’s characteristics make RO3010 laminates excellent for circuit miniaturization.
Features
- Dk of 10.2 +/- .30
- Dissipation factor of .0022 at 10 GHz
- Low X, Y and Z axis CTE of 13, 11 and 16 ppm/°C, respectively
Benefits
- Material exhibits dimensional stability with expansion coefficient matched to copper
- ISO 9001 Certified
- Suitable for use with multi-layer board designs
Rogers 3010 PCB stands as a pivotal Package Substrate within the contemporary electronics landscape, renowned for its high-performance attributes stemming from Rogers Corporation’s proprietary materials. This circuit board material boasts exceptional electrical and mechanical properties, rendering it indispensable across various electronic domains, including communication, medical, and aerospace sectors.
At the core of its significance lies its role as a Package Substrate, pivotal for supporting and interconnecting diverse chips, devices, and components within modern electronic devices. Rogers 3010 PCB furnishes a dependable and stable operational milieu for these elements through its superior performance characteristics, thereby safeguarding the stability and efficacy of the entire electronic system.
This discourse undertakes a comprehensive exploration of Rogers 3010 PCB, delving into its classifications, merits, and applications, providing readers with insights into this foundational technology. By delineating its variants, we unravel the manifold application contexts of Rogers 3010 PCB, spanning single-layer, double-layer, and multi-layer configurations. In elucidating its advantages, emphasis is placed on the remarkable differentiators of Rogers 3010 PCB vis-à-vis conventional FR-4 PCB, encompassing heightened frequency performance, reduced signal attenuation, and enhanced thermal resilience, elucidating the rationale behind opting for Rogers 3010 PCB.
Whether it is achieving higher data transmission rates in the communications field or ensuring higher accuracy and reliability in medical equipment, Rogers 3010 PCB plays an indispensable role. By understanding its application cases, readers will more fully understand the importance and value of Rogers 3010 PCB.
In essence, the Rogers 3010 PCB, serving as a crucial Package Substrate, holds indispensable significance in today’s electronic landscape. This article delves deeply into its various types, merits, and applications, offering readers a comprehensive comprehension. By assimilating this information, individuals can enhance their utilization of Rogers 3010 PCBs in real-world projects, thereby augmenting product performance and competitiveness.
What are the types of Rogers 3010 PCBs?
The Rogers 3010 PCB serves as a critical substrate in modern electronics, offering tailored types to meet specific requirements. Understanding these types is essential for selecting the optimal board. The Rogers 3010 PCB primarily consists of three categories: single-layer, double-layer, and multi-layer boards, each with distinct characteristics and applications.
Firstly, a single-layer board is one of the simplest types, comprising a single layer of conductive copper foil adhered to a Rogers 3010 base material. These boards are suitable for straightforward circuit designs, offering low cost and compatibility with basic electronic products or simple connections.
Secondly, the double-layer board features two layers of conductive copper foil on both sides of the Rogers 3010 base material, interconnected via through holes. Providing more flexibility than single-layer counterparts, double-layer boards accommodate more complex layouts, making them suitable for applications such as industrial control systems and medical equipment.
Lastly, multi-layer boards represent the most intricate type, comprising three or more interconnected layers. These boards excel in high-density circuit designs, providing exceptional signal integrity and electrical performance. They find extensive use in communication equipment, aerospace electronic systems, and similar applications requiring superior performance and stability.
In summary, single-layer boards suit basic circuit connections with cost-effectiveness, double-layer boards accommodate medium-complexity designs with enhanced flexibility, while multi-layer boards are optimal for complex and high-density circuits, delivering top-tier performance and stability. Hence, selecting the appropriate Rogers 3010 PCB type hinges on specific application needs and design requirements.
What is the manufacturing process of Rogers 3010 PCB?
The manufacturing process of Rogers 3010 PCB involves a series of precise steps to ensure quality and performance. It starts with carefully selecting specialized high-performance materials from Rogers Corporation, known for their exceptional electrical and mechanical properties.
The lamination process involves stacking and bonding multiple layers of materials together under high temperature and pressure. Precise control of parameters such as temperature, pressure, and time ensures uniform pressing and proper bonding of each layer, ensuring the quality and stability of the lamination process.
Forming and machining represent another critical stage in Rogers 3010 PCB manufacturing. This involves cutting the material into the required size and shape according to design specifications, as well as performing hole processing and edge trimming. High-precision equipment and skilled operating techniques are necessary to maintain processing accuracy and consistency throughout this stage.
Finally, rigorous quality control and inspection are imperative to uphold product quality and performance standards. Comprehensive evaluation and testing of materials, workmanship, and finished products are conducted to ensure adherence to design specifications and customer requirements. Strict quality control measures are essential to produce dependable and consistent Rogers 3010 PCBs capable of meeting diverse application needs.
In summary, the manufacturing process of Rogers 3010 PCB is characterized by its technological complexity and meticulous attention to detail. Through precise control of every aspect, including material selection, lamination, forming, and quality control, the final product’s quality and performance are optimized to meet the highest standards.
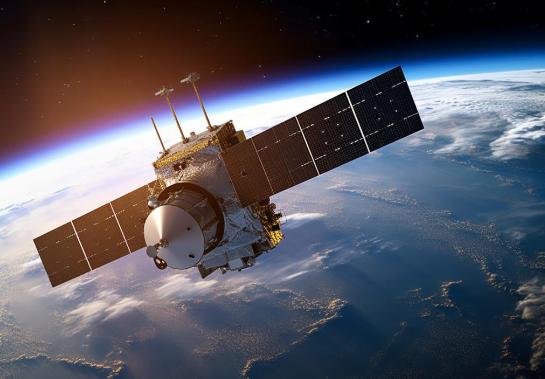
Rogers 3010 PCB
In what fields is Rogers 3010 PCB widely used?
Rogers 3010 PCB is extensively utilized in wireless communications, medical equipment, aerospace, and other industries due to its outstanding electrical properties, reliability, and excellent high-frequency signal processing capabilities. In wireless communications, particularly in 5G systems, it is widely employed in critical components like antennas and RF front-end modules. Its low loss, high signal integrity, and stable dielectric constant facilitate effective signal transmission at high frequencies, enhancing communication system performance and stability.
In the medical equipment sector, Rogers 3010 PCB finds application in key devices such as medical imaging equipment and life monitoring instruments. These devices demand high signal accuracy and stability, and the exceptional characteristics of Rogers 3010 PCB ensure equipment precision and reliability, meeting stringent standards for product quality and safety in the medical industry.
Rogers 3010 PCB is widely employed within the aerospace sector, particularly in critical systems such as flight control and satellite communication. Aerospace applications demand electronics capable of maintaining stable operation amidst extreme environmental conditions. Rogers 3010 PCB is favored for its commendable resistance to high temperatures, coupled with exceptional vibration and impact resilience. These attributes facilitate consistent functionality in harsh environments, thus ensuring the safety and reliability of aerospace systems.
The extensive utilization of Rogers 3010 PCB in these industries can be attributed to its outstanding electrical performance, operational stability, and adaptability to harsh environments. Consequently, it serves as a dependable foundation for systems in wireless communications, medical equipment, aerospace, and various other domains, thereby enhancing overall system performance and reliability.
How to get Rogers 3010 PCB?
If you’re in need of Rogers 3010 PCBs, we suggest collaborating with a reputable manufacturer or supplier for reliable quality and consistent supply. Our company fits this profile, specializing in high-quality Rogers 3010 PCBs tailored to your requirements. With advanced production equipment and a proficient technical team, we can customize PCBs to a range of specifications.
Choosing us offers you:
Quality Assurance:We uphold strict quality control processes, ensuring each PCB meets the highest standards, from material procurement to production.
Customized Services:Our professional engineering team offers tailored solutions to meet your specific requirements, whether it’s board thickness, layers, surface treatment, or other needs.
Timely Delivery: With efficient production lines and supply chain management, we guarantee on-time delivery regardless of order size.
Technical Support: We provide comprehensive technical support and after-sales service, ready to assist with any issues or guidance you may need during use.
Collaborating with us guarantees top-notch Rogers 3010 PCBs, delivering dependable support and assurance for your projects. Whether you’re a startup or a sizable enterprise, we are well-equipped to offer a satisfactory solution. We eagerly anticipate the opportunity to work with you!
What factors affect the quotation of Rogers 3010 PCB?
The quotation for Rogers 3010 PCBs is influenced by various factors, including board thickness, number of layers, surface treatment, and more. It’s essential to thoroughly analyze these factors to obtain accurate pricing information.
Firstly, board thickness plays a crucial role in Rogers 3010 PCB quotations. Different applications and requirements may demand varying thicknesses, directly impacting material and processing costs. Hence, thorough consideration of thickness requirements is necessary when determining the quotation.
Moreover, surface treatment also influences the quotation of Rogers 3010 PCBs. Various surface treatment processes like HASL, ENIG, OSP, etc., come with different costs and performance characteristics. Choosing a surface treatment that aligns with project needs, balancing performance requirements and cost control, is pivotal in ensuring accurate quotations.
They can provide customized quotation plans based on the specific requirements of the project and mass production quantities. In addition, you can obtain more comprehensive and accurate quotation information by comparing with multiple suppliers, thereby providing a reference for project budget and cost control.
To sum up, the factors that affect Rogers 3010 PCB quotation include board thickness, number of layers, surface treatment and other aspects. By fully considering these factors and working with professional suppliers, accurate quotation information can be obtained to provide strong support for the smooth progress of the project.
Frequently Asked Questions (FAQs)
How do I choose the right Rogers 3010 PCB for my project?
Choosing the right Rogers 3010 PCB involves considering factors such as application requirements, operating environment, and budget constraints. Working closely with PCB experts can help in selecting the most suitable solution for your project needs.
Are there common challenges in using Rogers 3010 PCB, and how can they be addressed?
Common challenges may include selecting the right type for specific applications and addressing issues that may arise during the manufacturing process. Guidance from experienced professionals and thorough understanding of the material properties can help overcome these challenges.
How does the manufacturing process of Rogers 3010 PCB differ from that of other PCB types?
The manufacturing process of Rogers 3010 PCB involves specific steps tailored to its unique material properties. This includes material selection, lamination processes, shaping, and machining. These steps ensure the desired electrical and mechanical performance of the final product.
What factors affect the pricing of Rogers 3010 PCBs?
Several factors influence the pricing of Rogers 3010 PCBs, including board thickness, number of layers, surface finish, and production volume. Customizations and special requirements may also impact the overall cost.
How is the manufacturing process of Rogers 3010 PCB different from other types of PCB?
The manufacturing process of Rogers 3010 PCB involves specific materials and techniques tailored to its unique properties. This includes material selection, lamination process, and precision machining to ensure consistent performance and reliability.