What is SIP Package Substrate?
SIP Package Substrate manufacture. we can produce the best samllest bump pitch with 100um, the best smallest trace are 9um.
In the field of PCB engineering, SIP (System-in-Package) Package Substrate represents an important innovation, carrying multiple functions and cleverly integrating them into a single, compact unit. But SIP Package Substrate is more than a simple component stack, it represents a revolutionary change in electronic design. Let’s take a deeper look at the nature and working principle of SIP Package Substrate.
The essence of SIP Package Substrate is to integrate multiple components with different functions in a compact package. These components can include processors, memory, sensors, antennas, etc., as well as various passive components. By integrating these components into a single package, SIP Package Substrate achieves a high degree of integration, greatly increasing system density and performance.
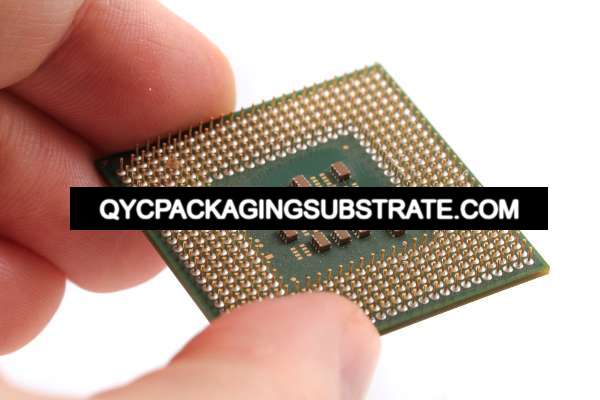
SIP Package Substrate
The working principle of SIP Package Substrate is based on advanced packaging technology and design methods. During the design phase, engineers need to consider how to place different components inside the package to achieve optimal space utilization and electrical performance. Then, during the manufacturing process, the individual components are precisely mounted onto the substrate and connected through interconnect structures to enable communication and collaboration between the individual components.
The advantage of SIP Package Substrate is its compactness and high degree of integration. Compared with traditional PCB design, SIP Package Substrate can integrate multiple components into one package, greatly saving space and simplifying system assembly and wiring. At the same time, SIP Package Substrate can also improve the performance and reliability of the system because it reduces the number of electrical connections and reduces the delay and loss of signal transmission.
Overall, SIP Package Substrate represents a major advancement in electronic design, providing engineers with a new design approach that enables higher performance, more compact systems. With the continuous development of technology, SIP Package Substrate will continue to play an important role and promote the progress and innovation of electronic design.
What types of SIP Package Substrate are there?
In the field of SIP Package Substrate, there are many types, each type has unique characteristics and applicable scenarios. Here are some common SIP Package Substrate types:
Organic substrates use polymers as the base material, usually composed of glass fiber reinforced epoxy resin. This type of substrate is lightweight and low-cost, making it suitable for many consumer electronics products such as smartphones, tablets, and laptops.
Ceramic substrates have excellent high temperature resistance and thermal conductivity and are commonly used in high power and high frequency applications such as radio frequency (RF) modules, power amplifiers and sensors.
Metal core substrates have good heat dissipation properties, and their metal core layers are usually made of aluminum or copper. They are used in high-power LED lighting products and automotive electronic systems that require effective heat dissipation.
Flexible substrates are bendable and flexible and are suitable for applications that require bending or folding, such as wearable devices, flexible displays, and medical sensors.
Each type of SIP Package Substrate has its unique advantages and scope of application, and engineers can choose the most appropriate type based on project needs and performance requirements. By understanding the characteristics of each type, you can better utilize the advantages of SIP Package Substrate to achieve innovation and optimization of electronic system design.
What are the advantages of SIP Package Substrate?
Using SIP (System-in-Package) Package Substrate brings many advantages in electronic design, from thermal management to cost-effectiveness, providing engineers with more choices and flexibility. Here are a few key advantages of SIP Package Substrate:
First, SIP Package Substrate excels in thermal management. Because it integrates multiple components in the same package, it conducts and disperses heat more efficiently. This advantage is critical for high-power applications, ensuring that the system maintains a stable operating temperature under high load conditions, thereby improving system reliability and performance.
Secondly, SIP Package Substrate improves electrical performance. By integrating multiple components directly into the same package, the signal transmission distance and resistance can be reduced, thereby reducing signal attenuation and delay, and improving the response speed and stability of the circuit. This direct-connect design also reduces inductance and crosstalk in the circuit, further improving electrical performance.
Additionally, SIP Package Substrate saves valuable space. Compared with traditional PCB, SIP Package Substrate can achieve higher component density and more compact packaging, thus containing more functions and features in the same size space. This is very beneficial for applications that require miniaturized designs, such as portable electronic devices and embedded systems.
In addition, SIP Package Substrate improves the reliability of the system. By reducing connection points and contact between components, SIP Package Substrate reduces potential points of failure and risk of failure. At the same time, integrating multiple components into the same package also reduces the contact between components, further improving the stability and reliability of the system.
Finally, SIP Package Substrate brings cost benefits. Although the initial investment may be slightly higher than a traditional PCB design, SIP Package Substrate often delivers better price/performance and long-term savings given its advantages in thermal management, electrical performance, space utilization, and reliability. cost.
In summary, SIP Package Substrate excels in thermal management, electrical performance, space utilization, reliability and cost-effectiveness, providing engineers with a powerful tool for achieving innovative, high-performance and reliable solutions. electronic design.
Why choose SIP Package Substrate?
In the field of modern electronic design, SIP (System-in-Package) Package Substrate is increasingly becoming the first choice of engineers instead of traditional PCB. This is no accident, but rather because SIP Package Substrate offers an unparalleled set of advantages, making it ideal for electronic system integration and design.
First, one of the biggest advantages of SIP Package Substrate is its ability to integrate multiple functional components into a single package. Traditional PCBs can only carry a limited number of components, while SIP Package Substrate can integrate multiple chips, sensors, and passive components into a compact package. This integration capability not only saves space, but also simplifies the system design and assembly process, reduces interconnections between circuit boards, and improves overall reliability.
Secondly, SIP Package Substrate performs outstandingly in thermal management. Because multiple components are integrated into a single package, overall heat can be managed more efficiently. This is particularly important for high-performance electronic systems that need to work in compact spaces. Through good thermal management, SIP Package Substrate is able to ensure that components maintain stable temperatures over long periods of operation, thereby improving system reliability and performance.
In addition, SIP Package Substrate can improve electrical performance by reducing interconnect lengths and impedance matching. This optimization can reduce losses and interference in signal transmission and improve the response speed and stability of the system. This is particularly important for applications with high signal quality requirements, such as high-speed communications and data processing.
To sum up, SIP Package Substrate has obvious advantages in integration capabilities, thermal management and electrical performance, making it the first choice for modern electronic system design. By choosing SIP Package Substrate, engineers can implement more compact, more reliable and higher-performance electronic products to meet growing market demands and drive technological advancement.
What is the manufacturing process of SIP Package Substrate?
The manufacturing process of SIP Package Substrate is a complex and precise process involving multiple critical steps to ensure the quality and performance of the final product. These steps are detailed below:
The first step in manufacturing SIP Package Substrate is to prepare the substrate. Typically, the substrate is constructed from an organic material, ceramic or metallic core, the choice of which depends on the application requirements. At this stage, the substrate needs to be cleaned and surface treated to ensure good adhesion and surface flatness.
Next, the layers of different materials are combined together via layer stacking to form the complete substrate structure. These layers can include dielectric layers, metal layers, insulating layers, etc., and can be customized according to design requirements. The layer stacking process requires highly precise control to ensure that the thickness and position of each layer is within specification.
Once the layer stacking of the substrate is complete, next comes the integration of the components. This includes the precise mounting of various components, such as chips, sensors and passive components, onto the substrate. In this process, advanced automation equipment and technology are required to ensure the precise alignment and positioning of components.
After completing the component integration, the SIP Package Substrate needs to be surface treated. This includes process steps such as applying protective layers, soldering joints, and adding pins. The purpose of surface treatment is to enhance the durability, corrosion protection and connectivity of the substrate to meet specific application requirements.
Precise alignment and interconnection are critical steps throughout the manufacturing process. This involves the use of high-precision equipment and technology to ensure that each component is positioned accurately in its designated location and has reliable electrical connections to other components.
During the manufacturing process of SIP Package Substrate, the above steps require strict quality control and precise process control to ensure that the performance and reliability of the final product reach the expected level. Through careful execution of these steps, SIP Package Substrate can achieve high integration, high reliability and superior performance to meet the needs of various electronic applications.
How to find SIP Package Substrate?
When looking for a reliable SIP Package Substrate supplier, there are several key factors to consider. First, you can build a list of suppliers through web searches or industry contacts. These suppliers are usually professional manufacturers or distributors with extensive experience and good reputations.
Within our company, we also offer SIP Package Substrate and are committed to meeting the specific needs of our customers. Our product range covers various standard and customized SIP Package Substrate, which can be customized as per the project requirements. Whether you need specific sizes, materials, layers or other special requirements, we can provide a solution.
Our SIP Package Substrate utilizes advanced manufacturing technology to ensure the highest standards of product quality and performance. We have a professional engineering team and production facilities that can provide flexible production solutions to meet customers’ different mass production needs.
In addition to providing products, we also provide professional technical support and customer service to ensure that customers can receive timely and effective help when selecting, using and maintaining SIP Package Substrate.
So, if you are looking for a reliable SIP Package Substrate supplier and want to get customized solutions, our company will be your ideal choice. We are committed to providing customers with high-quality products and excellent services, and establishing long-term cooperative relationships with customers.
What is the quote for SIP Package Substrate?
Cost estimation of SIP Package Substrate is a complex issue affected by many factors. Among them, substrate type, complexity and quantity are key factors that determine cost. First, substrate type has a direct impact on cost. Different types of substrates, such as organic substrates, ceramic substrates and metal substrates, have huge differences in manufacturing processes and material costs, thus leading to different cost levels.
Secondly, the complexity of the substrate is also one of the important factors that determine the cost. Complex SIP Package Substrates, such as those with multi-layer structures, high-density component layouts and fine lines, usually require more processes and higher-precision manufacturing equipment, which increases manufacturing costs.
Finally, quantity also has an impact on cost. Generally speaking, high-volume production can enjoy more economies of scale, thereby lowering average costs. However, the need for low-volume production or customization may lead to higher costs, as more customized processes and personalized services are required.
Interested parties can determine the feasibility of integrating SIP Package Substrate into their projects by requesting quotes from vendors. Suppliers usually provide customized quotes based on the specific requirements of the project and volume production. Therefore, it is recommended to contact multiple suppliers before starting a project and compare the quotes and services of different suppliers to find the most competitive solution.
Overall, while the cost of SIP Package Substrate can fluctuate, by carefully evaluating factors such as substrate type, complexity, and quantity, as well as working with suppliers, costs can be effectively controlled and the successful implementation of the project ensured. .
Frequently Asked Questions (FAQs)
How reliable are SIP Package Substrates compared to traditional PCBs?
SIP Package Substrates undergo rigorous testing and quality control measures to ensure reliability and performance. Their integrated design reduces the risk of signal interference and increases overall system reliability compared to traditional PCBs, making them a preferred choice for demanding applications.
Can SIP Package Substrates withstand harsh operating conditions?
SIP Package Substrates are engineered to withstand a wide range of operating conditions, including temperature fluctuations, mechanical stresses, and vibration. However, it’s essential to consult with manufacturers regarding specific environmental specifications to ensure optimal performance in challenging operating environments.
What are the longevity and durability of SIP Package Substrates?
SIP Package Substrates are designed for long-term reliability and durability. With proper design considerations and adherence to manufacturing standards, SIP Package Substrates can provide years of uninterrupted operation in various applications, ensuring consistent performance over time.
How do SIP Package Substrates contribute to cost-effectiveness in electronic designs?
SIP Package Substrates offer cost-effectiveness through their integrated design, which reduces the need for additional components and assembly processes. By consolidating multiple functionalities into a single package, SIP Package Substrates streamline manufacturing processes and reduce overall production costs.
How can I ensure the quality of SIP Package Substrates for my project?
To ensure the quality of SIP Package Substrates, it’s essential to collaborate with reputable manufacturers and suppliers with a track record of delivering high-quality products. Requesting samples, conducting thorough testing, and verifying compliance with industry standards can help ensure the reliability and performance of SIP Package Substrates for your project.