3D Ceramic Packages Substrate manufacturing. Advanced 3D production process technology. we made the Ceramic Packages Substrate with 3D process.
In the manufacturing of today’s high-tech electronic equipment, 3D ceramic packaging substrates, as an advanced technology, are gradually becoming the mainstream choice in the industry. This packaging technology not only enables high-density packaging, but also has excellent electrical performance and reliability, so it has attracted much attention. This article will delve into the design, manufacturing and production process of 3D ceramic packaging substrates, detailing each key step and providing practical guidance to help readers better understand and apply this advanced technology.
What is a 3D ceramic packaging substrate?
3D ceramic packaging substrate is an advanced packaging technology in today’s electronic field, designed to meet the growing demand for high-performance, high-density packaging in electronic devices. Compared with traditional flat packaging technology, 3D ceramic packaging substrates not only have a higher integration level, but also provide better electrical performance and reliability.
In 3D ceramic packaging substrates, multiple layers of circuit components are stacked together to form complex circuit structures. These circuit components include transistors, capacitors, resistors, etc., which are connected directly to the ceramic substrate instead of through traditional wires. This stacked design not only saves space, but also reduces circuit delays and signal transmission losses, thereby improving the performance and speed of electronic devices.
3D ceramic packaging substrates usually use multi-layer ceramic substrates as carriers. These ceramic substrates have excellent mechanical strength, high temperature resistance and chemical stability. By using high-precision manufacturing processes on ceramic substrates, micron-level circuit lines and gaps can be achieved, ensuring the stability and reliability of the circuit.
In addition, the 3D ceramic packaging substrate also has good heat dissipation performance, which is due to the excellent thermal conductivity of the ceramic material itself and the design of the multi-layer structure. This makes 3D ceramic packaging substrates very suitable for use in high-power and high-density integrated electronic devices, such as servers, communication equipment, and automotive electronics.
In general, 3D ceramic packaging substrate is a high-performance electronic packaging technology that combines advanced manufacturing processes and high-quality materials. Its emergence provides new solutions for the design and manufacturing of electronic equipment and promotes the continuous development of the electronics industry. development and progress.
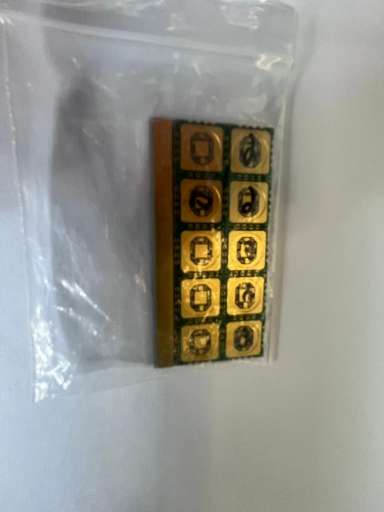
3D Ceramic Packages Substrate
How to design 3D ceramic packaging substrate?
Designing a 3D ceramic packaging substrate is a critical and complex task that requires consideration of multiple factors to ensure the performance and reliability of the final product. Below we will delve into the factors that need to be considered when designing 3D ceramic packaging substrates as well as the tips and precautions when using CAD software for design.
First, the following factors need to be considered when designing a 3D ceramic packaging substrate:
Functional requirements: First, the functional requirements of the product must be clarified, including the type, quantity, layout, etc. of required electronic components. This will directly affect the design and layout of the packaging substrate.
Packaging density: 3D ceramic packaging substrates are usually designed for high-density packaging, so it is necessary to consider how to maximize the use of space so that more electronic components can be integrated in a limited space.
Thermal management: High-density packaging is usually accompanied by higher heat generation, so effective thermal management solutions, such as heat dissipation design, heat conduction paths, etc., must be considered to ensure the stability and reliability of the packaging substrate during operation.
Electromagnetic compatibility (EMC): Electromagnetic interference and electromagnetic compatibility between electronic components need to be considered during the design process to avoid affecting the normal operation of the product due to electromagnetic interference.
Material selection: Choosing the right ceramic material is critical to the performance of 3D ceramic packaging substrates. Materials should have good mechanical properties, thermal properties and chemical stability to meet specific application needs.
When using CAD software for 3D ceramic packaging substrate design, you need to pay attention to the following tips and precautions:
Accurate measurement: During the design process, the size and position of each component must be accurately measured to ensure that they can be mounted correctly on the package substrate and that the spacing and layout between components meet the design requirements.
Hierarchical design: Breaking down a design into multiple levels, each focused on a specific feature or component, to better manage complexity and increase design efficiency.
Simulation: Conducting simulation in CAD software can help discover potential design problems and optimize design solutions, improving the accuracy and reliability of the design.
Version control: During the design process, different versions of design files are regularly saved and version controlled so that they can be reviewed and modified when necessary.
Communicate with manufacturers: Work closely with 3D ceramic packaging substrate manufacturers to communicate design requirements and technical details in a timely manner to ensure that the design can be smoothly transformed into actual products.
To sum up, designing a 3D ceramic packaging substrate requires comprehensive consideration of various factors and the flexible use of various techniques and precautions in CAD software to ensure that the final design meets the requirements and has high performance and reliability.
What is the manufacturing process of 3D ceramic packaging substrate?
The manufacturing process of 3D ceramic packaging substrates is a complex and delicate process, involving multiple key steps. From material preparation to final processing, multiple processes are required. This is explained in detail below.
First, the first step in manufacturing 3D ceramic packaging substrates is material preparation. At this stage, high-performance ceramic materials need to be selected and finely processed and processed. These materials typically have excellent thermal stability, mechanical strength and chemical stability to ensure good performance and reliability of the final packaging substrate.
Next comes the lamination and sintering stage. At this stage, multiple layers of ceramic substrates and other component layers are bonded into a monolithic structure by laminating them and then sintering them at high temperatures. This process requires strict control of parameters such as temperature, pressure and time to ensure bonding strength and dimensional accuracy between the layers.
This is followed by the machining and surface treatment stages. At this stage, the 3D ceramic packaging substrate needs to be precisely machined and surface treated to meet specific design requirements and application needs. This may involve cutting, drilling, grinding, polishing and other processes to ensure the dimensional accuracy and surface quality of the packaging substrate.
Finally comes the quality inspection and testing stage. At this stage, strict quality inspection and performance testing of the manufactured 3D ceramic packaging substrate is required to ensure that it meets the design requirements and standards. This may include visual inspection, dimensional measurements, electrical testing, etc. to ensure the quality and reliability of the package substrate.
In general, the process of manufacturing 3D ceramic packaging substrates is a complex and delicate process that requires strict control and coordination of all aspects. Only when each critical step is effectively executed and managed can 3D ceramic packaging substrates with high performance and reliability be produced.
What material is the 3D ceramic packaging substrate made of?
When manufacturing 3D ceramic packaging substrates, it is crucial to select suitable high-performance ceramic materials. These materials must have excellent electrical, thermal and mechanical properties to ensure the reliability and stability of the final product. The following are the main materials commonly used in 3D ceramic packaging substrates:
Alumina: Alumina is one of the most commonly used 3D ceramic packaging substrate materials. It has good insulation properties, high thermal conductivity and chemical stability, making it suitable for high temperature and high frequency applications. Aluminum oxide is relatively low-cost to manufacture and is one of the common substrate materials found in many electronic devices.
Silicon Nitride: Silicon nitride is another material commonly used in 3D ceramic packaging substrates. It has excellent mechanical strength, high temperature stability and chemical inertness, making it suitable for high power and high frequency applications. Silicon nitride has high thermal conductivity and helps to dissipate heat effectively, so it is widely used in packaging applications that require heat dissipation performance.
Aluminum Nitride/Aluminum Oxide: Aluminum Nitride is a composite material that combines aluminum oxide and aluminum nitride. It inherits the excellent insulation properties of aluminum oxide and the high thermal conductivity of aluminum nitride, and has good comprehensive properties. Aluminum oxide aluminum nitride packaging substrates are suitable for high-performance packaging applications requiring comprehensive performance.
Zirconia: Zirconia is a high-temperature ceramic material with excellent thermal stability and mechanical strength. Despite higher manufacturing costs, zirconia packaging substrates are suitable for high-reliability applications in extreme environments, such as aerospace and automotive electronics.
Choosing the right material has an important impact on the performance of 3D ceramic packaging substrates. For example, for high-power applications, materials with higher thermal conductivity can be selected to improve heat dissipation; while for high-frequency applications, materials with lower dielectric loss and lower dielectric constant need to be selected to reduce signal attenuation. In addition, the thermal expansion coefficient, mechanical strength and chemical stability of the material also need to be considered to ensure that the packaging substrate can work stably and reliably under various working conditions. Therefore, during the design and manufacturing process, various performance indicators of materials need to be comprehensively considered to meet the needs of specific applications.
Who makes 3D ceramic packaging substrates?
In the manufacturing process of 3D ceramic packaging substrates, supplier selection is crucial. As a technology-leading and experienced company, we are proud to provide high-quality 3D ceramic packaging substrate manufacturing services.
As a supplier to our company, you can expect the following key benefits:
Technology leadership: We have advanced manufacturing equipment and technical teams, dedicated to providing customers with the most advanced 3D ceramic packaging substrate manufacturing services. We constantly pursue technological innovation and progress to meet the evolving needs of our customers.
Quality Assurance: We strictly control every production link to ensure that the quality of 3D ceramic packaging substrates meets international standards and customer requirements. From the selection of raw materials to the delivery of final products, we always pay attention to quality details to ensure customer satisfaction.
Customized solutions: We focus on communication and cooperation with customers, and provide customized 3D ceramic packaging substrate manufacturing solutions based on customers’ specific needs and application scenarios. Whether it is sample customization or mass production, we can provide customers with satisfactory solutions.
Timely delivery: Our efficient production process and management team ensure timely delivery of orders. We understand that time is of the essence for our customers, so we always strive to maintain the stability and reliability of our production schedule.
Excellent Customer Service: We are committed to providing our customers with an excellent customer service experience. Our team provides technical support and consulting services to customers at any time to ensure that customers receive timely help and support throughout the entire cooperation process.
In general, as a supplier of our company, you can choose us with confidence, and we will wholeheartedly provide you with high-quality, customized 3D ceramic packaging substrate manufacturing services to help you achieve the success and development of your project.
What are the five characteristics of great customer service?
Excellent customer service is crucial in the 3D ceramic packaging substrate manufacturing industry. It can not only enhance customers’ trust in the enterprise, but also improve customer satisfaction and win more business opportunities for the enterprise. So, what exactly does good customer service include?
No matter how simple or complex a customer’s question or need is, timely response is critical. A good customer service team should be able to respond quickly to customers’ emails, phone calls, or online messages and provide solutions or answers in the shortest possible time to meet customer needs.
The customer service team must possess specialized knowledge and skills in order to effectively resolve customer issues and provide professional advice. They should understand the process flow, material selection, design requirements, etc. of 3D ceramic packaging substrate manufacturing in order to provide customers with accurate information and guidance.
Every customer has unique needs and requirements, so customized solutions are critical to providing excellent customer service. The customer service team should work closely with customers to understand their needs and provide personalized solutions based on the actual situation to meet the customer’s specific needs.
Good communication is the basis for building good customer relationships. The customer service team should be able to communicate clearly, listen to customer opinions and feedback, and promptly communicate any issues or changes that may affect the progress of customer projects.
Excellent customer service should not stop at the end of the sales process but should provide ongoing post-sales support. The customer service team should pay attention to the problems customers encounter when using 3D ceramic packaging substrates and provide timely technical support and assistance to ensure that customers can use the product smoothly and obtain a satisfactory experience.
Overall, providing excellent customer service is not only a business responsibility, but also a competitive advantage. Through characteristics such as timely response, professional knowledge, customized solutions, good communication and continuous after-sales support, companies can establish a good brand image, win the trust and support of customers, and achieve long-term business relationships.
FAQS
What factors affect the cost of 3D ceramic packages substrates?
The cost of 3D ceramic packages substrates depends on various factors, including material costs, manufacturing complexity, and volume production. Higher material purity and tighter tolerances may increase the cost, while economies of scale and efficient manufacturing processes can help reduce overall expenses.
How can I ensure the quality of 3D ceramic packages substrates from manufacturers?
When selecting a manufacturer for 3D ceramic packages substrates, it’s essential to consider their experience, reputation, and quality control processes. Requesting samples, conducting site visits, and reviewing customer feedback can help evaluate the manufacturer’s capabilities and ensure the desired level of quality.
What are some common challenges in the manufacturing of 3D ceramic packages substrates?
Some common challenges in the manufacturing of 3D ceramic packages substrates include achieving uniform layer thickness, controlling sintering shrinkage, and minimizing defects such as cracks and delamination. Addressing these challenges requires advanced process control techniques and material expertise.
What future trends can we expect in the development of 3D ceramic packages substrates?
Future trends in the development of 3D ceramic packages substrates may include the adoption of advanced materials, such as silicon carbide (SiC) and gallium nitride (GaN), to further improve performance and reliability. Additionally, advancements in additive manufacturing techniques could enable the production of more complex and customized substrate designs.