96AL2O3 Ceramic pcb manufacturer. Ceramic Series material PCB and Ceramic package substrates Vendor, we offer Ceramic PCB and BGA substrates from 2 layer to 20 layers.
In today’s digital era, 96AL2O3 ceramic PCB manufacturing technology is driving the continuous development of the electronic field at an alarming rate. Whether it is high-performance computers or cutting-edge medical equipment, this advanced PCB technology has become a major driver in various industries. This guide aims to delve into all aspects of 96AL2O3 ceramic PCB manufacturing, from design to manufacturing, from materials to cost, to reveal the unique charm and wide range of applications of this technology.
What is 96AL2O3 ceramic PCB?
96AL2O3 ceramic PCB is a printed circuit board whose substrate is composed of 96% alumina ceramic. This material has attracted much attention due to its excellent thermal conductivity, insulation and high temperature resistance. Compared with traditional fiberglass substrates or FR-4 substrates, 96AL2O3 ceramic PCB performs better when dealing with high-power and high-frequency electronic equipment.
First of all, its thermal conductivity is one of its outstanding features. Due to the use of alumina ceramic substrate, 96AL2O3 ceramic PCB can effectively transfer heat, thereby helping to dissipate heat. This is especially important for high-power electronic equipment, which can effectively reduce component temperature and improve the stability and reliability of the equipment.
Secondly, 96AL2O3 ceramic PCB has excellent insulation properties. Ceramic substrates can still maintain good insulation properties in high-temperature environments and are not prone to leakage or breakdown. This makes it particularly suitable for electronic equipment that needs to work under high temperature conditions, such as automotive electronics, aerospace equipment, etc.
In addition, this ceramic PCB has excellent high temperature resistance. In high-temperature environments, traditional fiberglass substrates may deform or melt, while 96AL2O3 ceramic PCBs can easily cope with high-temperature environments and maintain stability and reliability.
Therefore, overall, 96AL2O3 ceramic PCB is a powerful printed circuit board suitable for various high-power and high-frequency electronic devices. Its excellent thermal conductivity, insulation and high temperature resistance make it the preferred solution in many fields, bringing new possibilities and opportunities to the development of the electronics industry.
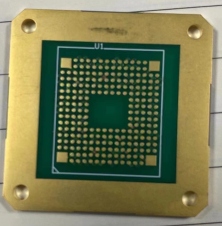
96AL2O3 Ceramic pcb
How to design 96AL2O3 ceramic PCB?
Designing a 96AL2O3 ceramic PCB is a complex and precise process that requires experienced engineers and professional design tools. The following will introduce the key steps and required tools for designing 96AL2O3 ceramic PCB.
First of all, designing 96AL2O3 ceramic PCB requires the use of dedicated circuit design software, such as Altium Designer, Cadence Allegro, etc. These software provide rich functionality to assist engineers with circuit layout, component selection, and routing. When conducting circuit layout, engineers need to consider factors such as the connection relationship between various components, signal transmission paths, and thermal management. Through reasonable layout, signal interference and electromagnetic interference can be minimized and circuit performance and stability can be improved.
Next is the component positioning stage, where engineers need to place various components (such as chips, resistors, capacitors, etc.) on the PCB board according to circuit design requirements. When selecting component locations, you need to consider the connection relationships between components, heat dissipation requirements, and overall circuit layout. Reasonable component positioning can effectively reduce circuit length, reduce signal transmission delay, and improve circuit performance.
Wiring is another key step in designing 96AL2O3 ceramic PCB. Engineers need to route the connecting lines between various components according to the circuit layout. When wiring, factors such as the length of the signal transmission path, impedance matching, and signal integrity need to be considered. During the wiring process, attention must also be paid to avoiding signal crossovers and inter-layer jumpers to ensure the stability and reliability of the circuit.
The last stage is the design verification stage, where engineers need to use simulation tools to verify and optimize the designed PCB. Through simulation analysis, the performance indicators of the circuit, such as signal integrity, power consumption, thermal distribution, etc., can be evaluated, and the design can be adjusted and optimized. The purpose of design verification is to ensure that the designed 96AL2O3 ceramic PCB meets the specifications and can work properly.
In general, designing 96AL2O3 ceramic PCB involves key steps such as circuit layout, component positioning, wiring and design verification, which requires the use of specialized software and sophisticated tools. Through reasonable design and optimization, the high performance and stability of PCB can be achieved to meet various application needs.
What is the manufacturing process of 96AL2O3 ceramic PCB?
When we explore the manufacturing process of 96AL2O3 ceramic PCB, we will find that it is a highly complex and precise process that requires multiple precise steps to ensure the quality and performance of the final product. Here is a detailed description of this process:
The first step in manufacturing 96AL2O3 ceramic PCB is to prepare the ceramic substrate. Typically, these substrates start as raw ceramic blocks of predetermined size and shape. During preparation, the blocks may need to be cut, ground and cleaned to ensure they are the desired size and flatness.
Once the substrate is ready, the next steps involve shaping the ceramic material into the desired PCB shape. This usually involves cutting, grinding and drilling holes into the ceramic block to allow for circuit copper laying and component mounting in later steps.
With the substrate formed, the next step is to apply a layer of copper on the surface. This process is usually achieved through techniques such as chemical vapor deposition (CVD) or physical vapor deposition (PVD). The coating of the copper layer needs to be very uniform to ensure the quality of subsequent circuit connections.
Once the copper layer is applied, the next step is to use chemical or mechanical etching to remove excess copper material from the substrate surface, leaving the desired circuit pattern. This step requires very precise control to ensure that only the copper layer is removed without damaging the substrate.
After completing the circuit pattern, holes need to be drilled on the PCB to facilitate subsequent component installation and connection. This step requires the use of a high-precision drill press and drill bits to ensure the location and size of the holes are accurate.
The final step is to treat the PCB surface to enhance its electrical performance and durability. This may include applying a protective solder paste or gold plating layer to prevent oxidation and corrosion and improve soldering quality and reliability.
Overall, manufacturing 96AL2O3 ceramic PCB is a complex process that requires multiple precision steps and strict quality control. Only under the guidance of precise mechanical equipment and professional technology can 96AL2O3 ceramic PCB products with high quality, reliability and stable performance be produced.
How much does 96AL2O3 ceramic PCB cost?
When it comes to the cost of 96AL2O3 ceramic PCB, we need to consider multiple factors. The first is substrate size. Larger substrates typically increase material costs and difficulty in the manufacturing process, thereby increasing the overall cost. The second is the level of complexity. If the design contains complex circuit layout, multi-layer structure or special technical requirements, the manufacturing cost will increase accordingly. Material selection is also an important factor. Different materials have different prices and properties, which directly affect the cost of the final product. Finally, manufacturing volume will also have an impact on costs. Generally speaking, large-volume production can reduce unit costs, while small-volume production is relatively more expensive.
Based on these factors, the price of 96AL2O3 ceramic PCB ranges from a few dollars to tens of dollars. The cost may be lower for simple, small-sized substrates, or higher for complex, large-sized substrates. In addition, customization needs and special technical requirements can also have an impact on costs, as they may require additional engineering and processing steps.
In general, the cost of 96AL2O3 ceramic PCB is the result of comprehensive considerations and needs to be determined based on specific design requirements and manufacturing volume. Therefore, before starting a project, it is best to communicate with the manufacturer to obtain detailed quotes and proposals to ensure that the project can go smoothly and within budget.
What materials are used in 96AL2O3 ceramic PCB?
When it comes to the materials of 96AL2O3 Ceramic PCB, there are several key components that are essential to ensure its performance and reliability. Below we’ll take a closer look at these materials and their role in PCB manufacturing.
First, let’s take a look at the 96AL2O3 ceramic substrate. This is one of the main components of the 96AL2O3 ceramic PCB, which is made of alumina material. Alumina ceramic substrates have excellent thermal conductivity and insulation properties and can maintain stability in high-temperature environments, making them ideal for high-power and high-frequency electronic devices.
Secondly, metallized conductors are another vital component. These conductor layers are deposited or printed on the surface of ceramic substrates and are used to connect electronic components and carry electrical current. Metallized conductors are usually made of copper or silver materials, which have good electrical conductivity and reliable connectivity, ensuring the stability and performance of the circuit.
In addition, high temperature resistant solder is also an integral part. During the PCB manufacturing process, solder is used to connect electronic components and metallized conductors to form circuit connections. For 96AL2O3 ceramic PCB, it is necessary to choose solder that can maintain stability and reliability in high temperature environments to ensure the durability and performance of the circuit connection.
Overall, the performance and reliability of 96AL2O3 ceramic PCB depends on the selection and use of various materials. An alumina ceramic substrate provides a stable foundation, metallized conductors ensure good electrical connections, and high-temperature tolerant solder ensures circuit durability and performance. By rationally selecting and using these materials, stable and reliable 96AL2O3 ceramic PCBs suitable for high temperature and high frequency environments can be produced.
Who is making 96AL2O3 ceramic PCB?
In the field of 96AL2O3 ceramic PCB manufacturing, there are a series of professional manufacturers dedicated to producing high-quality products and providing solutions to the needs of different industries. In this, our company plays an important role.
We are a professional 96AL2O3 ceramic PCB manufacturer with many years of experience and excellent technical strength. We are committed to providing customers with high-quality, customized ceramic PCB solutions that meet their unique needs and requirements.
As a leading manufacturer, we have advanced production equipment and technical teams that can flexibly respond to various complex manufacturing needs. We focus on product quality and technological innovation, constantly optimize production processes and improve production efficiency to ensure that customers receive satisfactory products and services.
Our manufacturing process strictly follows international standards and industry norms. From raw material procurement to production and manufacturing to quality control, every link is carefully designed and strictly controlled. We work closely with our customers to understand their needs and provide personalized solutions to ensure products are at their best in design, performance and reliability.
As a responsible company, we actively advocate the concept of green manufacturing and are committed to reducing the impact on the environment. We adopt environmentally friendly production processes, such as recycling waste and using lead-free solder, to contribute to sustainable development.
In short, as a professional 96AL2O3 ceramic PCB manufacturer, we have won the trust and support of our customers with our excellent quality, professional technology and excellent service. We will continue to work hard to continuously improve our own strength, provide customers with better products and services, and jointly create a better future.
What are 5 qualities of a good customer service?
In 96AL2O3 Ceramic PCB Manufacturing, providing excellent customer service is a key factor in ensuring customer satisfaction and business success. Here are a few key qualities of good customer service:
Responding quickly to customer needs and questions is critical. In 96AL2O3 ceramic PCB manufacturing, customers may have urgent project requirements or technical questions, so timely response is essential. Providing customers with fast and effective solutions through timely responses to emails, phone calls, or online chats can greatly increase customer satisfaction.
It is crucial to have expertise and experience in the field of 96AL2O3 ceramic PCB manufacturing. Customers often seek advice and guidance from manufacturers, particularly during the design phase and material selection. Therefore, manufacturers need to have in-depth industry knowledge and be able to provide customers with professional technical support and advice to help them solve various challenges and make informed decisions.
Every customer’s needs are unique, so providing personalized solutions is crucial. In 96AL2O3 ceramic PCB manufacturing, manufacturers should have the flexibility to adapt to the specific requirements of their customers, tailoring solutions to meet their unique needs and requirements. This may involve custom designs, special process requirements, or low-volume production, but this customization can help customers achieve their project goals and strengthen their relationships with manufacturers.
In 96AL2O3 ceramic PCB manufacturing, quality is a crucial factor. Customers expect consistent performance and high-quality manufacturing standards from the products they purchase. Therefore, manufacturers need to implement strict quality control measures to ensure that each PCB meets the prescribed standards and requirements. Providing quality assurance can enhance customers’ trust in manufacturers and establish long-term and stable cooperative relationships.
Clear and effective communication is the foundation of good customer relationships. In 96AL2O3 ceramic PCB manufacturing, manufacturers need to maintain close contact with customers and communicate important information such as project progress, technical issues, and order status in a timely manner. Ensuring open lines of communication between both parties, through regular updates, progress reports, and project meetings, can help resolve issues and prevent potential misunderstandings or dissatisfaction.
To sum up, good customer service is crucial in 96AL2O3 ceramic PCB manufacturing. Through key attributes such as responsiveness, expertise, customized services, quality assurance and effective communication, manufacturers can build strong relationships with customers and jointly drive business growth and success.
Frequently Asked Questions
What are the advantages of 96AL2O3 ceramic PCB?
96AL2O3 ceramic PCB has many advantages, including excellent thermal conductivity, high temperature stability, good mechanical strength and excellent insulation properties. Due to the high thermal conductivity of its ceramic substrate, it is suitable for high-power electronic devices that require efficient heat dissipation. At the same time, its high temperature stability gives it excellent performance in harsh environmental conditions. In addition, ceramic substrates also have good mechanical strength and can withstand high mechanical stress and vibration, thereby improving product reliability. The most important thing is that 96AL2O3 ceramic PCB has excellent insulation properties, which can effectively prevent electrical short circuits between circuit boards and ensure the safe operation of the equipment.
How to choose the right 96AL2O3 ceramic PCB manufacturer?
Choosing the right 96AL2O3 ceramic PCB manufacturer is the key to ensuring product quality and delivery time. When choosing a manufacturer, first consider its experience and expertise in the field of 96AL2O3 ceramic PCB manufacturing. Manufacturers with extensive experience are often able to provide higher quality products and more reliable service. Secondly, the manufacturer’s equipment and technical level should be considered. Advanced equipment and technology can improve production efficiency and product quality. In addition, the manufacturer’s quality control system and after-sales service support also need to be considered. A manufacturer with a complete quality management system and good after-sales service can provide customers with better support and protection.
What are the application fields of 96AL2O3 ceramic PCB?
96AL2O3 ceramic PCB is widely used in various high-performance and high-reliability electronic equipment due to its excellent performance characteristics. These include aerospace, defense industry, medical equipment, communication equipment, industrial control and other fields. In the aerospace field, due to its high temperature stability and mechanical strength, 96AL2O3 ceramic PCB is used to manufacture electronic equipment in high temperature and high space environments such as spacecraft and satellites. In the field of medical equipment, it is used to manufacture various medical diagnostic equipment and treatment equipment, such as medical imaging equipment, pacemakers, etc. In the field of communication equipment, it is widely used in manufacturing high-frequency wireless communication equipment, such as base station antennas, satellite communication equipment, etc.
What are the design considerations for 96AL2O3 ceramic PCB?
When designing 96AL2O3 ceramic PCB, there are some key factors that need to be paid attention to to ensure the stability and reliability of the design. First of all, it is necessary to lay out the circuit rationally, optimize the location of components, minimize the length and intersection of signal lines, and reduce electromagnetic interference and crosstalk. Secondly, we need to pay attention to thermal conductivity issues and rationally design the heat dissipation structure and heat dissipation paths to ensure the normal operating temperature of the device. Additionally, material selection needs to be considered, selecting the appropriate ceramic substrate and metallized conductor materials to meet the specific requirements and environmental conditions of the device.