ABF GL102R8HF Package Substrates Manufacturer.ABF GL102R8HF Package Substrates Manufacturer is renowned for its cutting-edge solutions in the realm of electronic packaging. With a relentless pursuit of excellence, this manufacturer pioneers advanced substrate technologies that underpin the efficiency and reliability of electronic devices worldwide. Their commitment to innovation is evident in every aspect of their products, ensuring optimal performance in diverse applications. From compact consumer electronics to intricate industrial systems, ABF GL102R8HF Package Substrates stand as a testament to precision engineering and quality craftsmanship, meeting the ever-evolving demands of the modern tech landscape with unparalleled expertise and ingenuity.
In today’s electronics field, ABF GL102R8HF packaging substrate is one of the key solutions for connecting electronic components. Its high performance, stability and flexibility make it an indispensable component in various electronic devices. This article will introduce in detail the characteristics of the ABF GL102R8HF packaging substrate and its wide application in the electronics industry.
What are ABF GL102R8HF Package Substrates?
ABF GL102R8HF packaging substrate is a high-performance packaging substrate based on polyimide film (ABF), which is widely used in modern electronic equipment. Polyimide film is a high-performance engineering plastic with excellent mechanical properties, chemical stability and high-temperature performance, making it one of the most respected materials in the electronics industry.
First, the ABF GL102R8HF package substrate is known for its excellent mechanical properties. Its high strength and wear resistance ensure the stability and reliability of the packaging substrate in long-term use. This mechanical property allows the packaging substrate to withstand complex electronic component layout and connections and is less susceptible to damage from the external environment.
Secondly, the ABF GL102R8HF package substrate has excellent high temperature performance. In high-temperature environments, the packaging substrate can maintain stable electrical characteristics and structural integrity and is not prone to deformation or damage. This high-temperature performance allows the packaging substrate to be used in electronic equipment in various high-temperature working environments, such as automotive electronics, industrial control systems, etc.
In addition, the ABF GL102R8HF packaging substrate exhibits excellent chemical stability. Its corrosion resistance and chemical inertness enable the packaging substrate to operate stably for a long time in harsh chemical environments and is not susceptible to corrosion and damage by chemical substances. This chemical stability ensures the reliability and durability of the packaging substrate in various application scenarios.
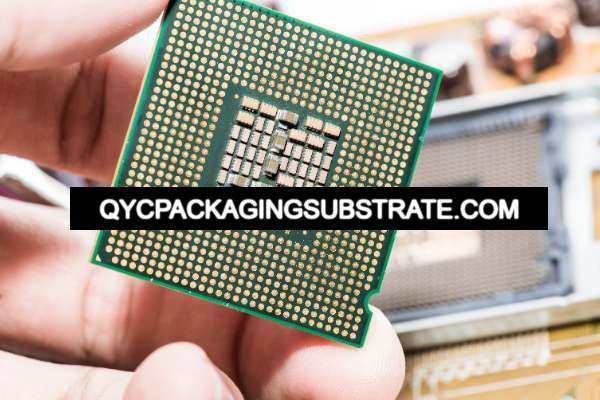
ABF GL102R8HF Package Substrates Manufacturer
In summary, ABF GL102R8HF packaging substrate has become an ideal choice for many electronic devices due to its excellent mechanical properties, high temperature performance and chemical stability. Its wide application in the modern electronics industry provides a reliable foundation for the design and manufacturing of various electronic products and promotes the continuous progress and development of electronic technology.
ABF GL102R8HF Package Substrates design Reference Guide.
The ABF GL102R8HF package substrate is an important technical solution in modern electronics, and its design process requires multiple factors to be considered to ensure performance and reliability. The following is a reference guide for designing the ABF GL102R8HF package substrate:
ABF GL102R8HF packaging substrate uses polyimide film as the base material, which has excellent thermal stability and chemical stability. During the design process, the appropriate substrate thickness and laminate structure should be selected based on the application needs to ensure the required mechanical and electrical properties.
When designing the layout of the packaging substrate, factors such as the placement of electronic components, signal transmission paths, and power distribution should be taken into consideration. Reasonable layout design can minimize signal interference and electromagnetic interference and improve system performance and stability.
When defining line width and line spacing, factors such as the operating frequency, signal transmission rate, and inter-layer distance of the packaging substrate need to be taken into consideration. Proper line width and line spacing design can ensure stable signal transmission and prevent electrical short circuits.
Good grounding design is key to ensuring the stability and performance of the packaging substrate. During the design process, ground pins and ground planes should be properly planned to reduce ground return impedance and improve the system’s anti-interference capability.
Considering the high-temperature performance of the ABF GL102R8HF package substrate, the heat dissipation structure and heat dissipation channels need to be properly planned during the design process to ensure that the electronic components can effectively dissipate heat and maintain stable performance during operation.
For applications that need to transmit high-speed signals, special attention needs to be paid to issues such as signal integrity and clock distribution during the design process. Signal distortion and crosstalk can be minimized with proper differential pairing, impedance matching, and signal layer stacking design.
When designing, the manufacturability of the packaging substrate should be taken into consideration, and appropriate processes and materials should be selected to ensure that the design can be successfully transformed into actual products and meet production cost and cycle requirements.
By comprehensively considering the above factors and combining them with actual application requirements, designers can develop an optimized design solution that conforms to the characteristics of the ABF GL102R8HF packaging substrate, thereby ensuring that the final product has excellent performance and reliability.
What material is used in ABF GL102R8HF Package Substrates?
The ABF GL102R8HF packaging substrate uses high-quality polyimide film as the base material, which is an advanced material highly respected in the electronics industry. Polyimide films are known for their excellent performance and stability, providing a reliable foundation for packaging substrates. Its excellent performance in high-temperature environments is one of its eye-catching features. Temperature is a key consideration in modern electronics, especially in high-performance devices and harsh operating environments. The polyimide film used in the ABF GL102R8HF packaging substrate maintains stability over a wide temperature range, ensuring the reliability and long-term operation stability of electronic devices.
In addition to its excellent performance in high-temperature environments, the polyimide film of the ABF GL102R8HF packaging substrate has excellent chemical stability. This means it is highly resistant to many chemicals and is less susceptible to corrosion or damage. In some special industrial environments, you may be exposed to various chemicals, and the material properties of the ABF GL102R8HF packaging substrate ensure its reliability and stability in these environments.
This high-performance polyimide film enables the ABF GL102R8HF packaging substrate to be widely used in various application scenarios. From aerospace to medical equipment, from industrial automation to communication equipment, ABF GL102R8HF packaging substrate has demonstrated its unique value in different fields. Its stable performance and reliability make it the preferred packaging substrate material for many electronic products.
In summary, the polyimide film material used in the ABF GL102R8HF packaging substrate has excellent thermal and chemical stability, making it one of the most highly regarded packaging substrate solutions in the electronics industry. Its excellent performance characteristics provide a reliable foundation for the design and manufacturing of electronic equipment and promote the development and progress of modern electronic technology.
What size are ABF GL102R8HF Package Substrates?
The size of the ABF GL102R8HF packaging substrate can be described as diverse and flexible, fully adapting to the different application requirements of various electronic devices. From small portable devices to large industrial equipment, ABF GL102R8HF package substrates provide the right size options to provide a solid foundation for device performance and functionality.
For small electronic devices, such as smartphones, tablets, wearable devices, etc., the packaging substrate needs to be small in size and lightweight to accommodate the compact space layout and lightweight design of the device. ABF GL102R8HF packaging substrate can meet these needs, providing precise size control and highly integrated circuit design to ensure that the device can achieve complex functions in a compact size.
For medium-sized electronic equipment, such as household appliances, industrial controllers, etc., the packaging substrate needs to have certain size flexibility to adapt to the design of equipment of different models and specifications. The ABF GL102R8HF package substrate is available in multiple size options and can be customized to the needs of the device for optimal performance and compatibility.
For large-scale industrial equipment, such as communication base stations, industrial automation equipment, etc., packaging substrates often require larger sizes and higher load-bearing capabilities to support complex circuit layouts and high-power electronic components. The ABF GL102R8HF packaging substrate has excellent mechanical properties and thermal stability, and can withstand extreme working environments and load requirements, ensuring stable operation and long-term reliability of the equipment.
In short, the size of the ABF GL102R8HF packaging substrate is flexible and diverse, which can meet the different needs of various electronic devices and provides a reliable foundation for the design and manufacturing of equipment. Whether it is a small portable device or a large industrial equipment, you can achieve the best performance and functionality by selecting the appropriate package substrate size.
The Manufacturer Process of ABF GL102R8HF Package Substrates.
The manufacturing process of the ABF GL102R8HF package substrate is a precise and complex process involving multiple critical steps, each of which is critical to the quality and performance of the final product.
The first step in the manufacturing process is substrate pretreatment. At this stage, the substrate surface is cleaned and chemically treated to ensure that it has a smooth, clean surface and provides good adhesion. The key to this step is to accurately control the processing conditions to ensure the quality and consistency of the substrate surface.
Next is copper foil patterning, also known as circuit patterning. This step involves transferring the patterned pattern on the copper foil layer to the surface of the substrate, forming paths for electrical connections. Patterning is usually achieved using photolithography or printing techniques, with the key being precise pattern transfer and good pattern resolution. ABF GL102R8HF package substrate requires high-precision and high-resolution patterning to ensure the reliability and stability of circuit connections.
After patterning is complete, component assembly is the next critical step in the manufacturing process. At this stage, the electronic components are accurately mounted to predetermined positions on the substrate and connected to the substrate through soldering or other connection methods. During the manufacturing process of the ABF GL102R8HF package substrate, advanced automated assembly technology is used to ensure efficient and precise assembly of each electronic component.
The final stage of the manufacturing process is quality control and testing. At this stage, the package substrate undergoes rigorous quality inspection and functional testing to ensure that it meets design specifications and performance requirements. By using advanced inspection equipment and technologies, such as X-ray inspection, AOI (automated optical inspection), etc., the packaging substrate is comprehensively inspected and tested to ensure that its quality and reliability meet standard requirements.
Through precise control and strict execution of the above steps, the manufacturing process of ABF GL102R8HF packaging substrate ensures product quality and reliability. This advanced manufacturing technology provides key technical support to the electronics industry and promotes the continuous innovation and development of electronic products.
The Application area of ABF GL102R8HF Package Substrates.
ABF GL102R8HF packaging substrate has a wide range of applications, and its excellent performance and stability provide a reliable foundation for the design and manufacturing of various electronic products.
In the field of consumer electronics, ABF GL102R8HF packaging substrates are widely used in smartphones, tablets, digital cameras and other devices. These devices require high-performance packaging substrates to support complex circuit designs and compact component layouts to achieve smaller and more efficient products.
In terms of communication equipment, ABF GL102R8HF packaging substrates are used to manufacture routers, switches, base stations and other equipment. These devices have extremely high requirements for stable signal transmission and reliable performance. The excellent performance of the ABF GL102R8HF packaging substrate ensures the reliability and stability of the device.
In the field of automotive electronics, ABF GL102R8HF packaging substrates are widely used in automotive electronic control units (ECUs), in-vehicle entertainment systems, driving assistance systems, etc. The automotive environment places stringent requirements on the working conditions of electronic equipment, such as temperature changes, vibration, etc., and the high-temperature performance and mechanical properties of the ABF GL102R8HF packaging substrate can meet these requirements.
In the field of medical equipment, ABF GL102R8HF packaging substrates are used in medical imaging equipment, life monitoring equipment, medical diagnostic equipment, etc. These devices have extremely high requirements on the stability and reliability of electronic components. The ABF GL102R8HF packaging substrate can provide stable circuit connections and signal transmission to ensure the normal operation and accuracy of the equipment.
In general, the wide application of ABF GL102R8HF packaging substrate in consumer electronics, communication equipment, automotive electronics, medical equipment and other fields fully demonstrates its important position and value in the electronics industry. Its excellent performance and stability provide a reliable foundation for the design and manufacturing of various electronic products, and promote the continuous progress and innovation of electronic technology.
What are the advantages of ABF GL102R8HF Package Substrates?
The ABF GL102R8HF packaging substrate offers many advantages, making it a favored technology solution in the electronics industry.
First of all, its outstanding high performance is one of its biggest advantages. Using high-quality polyimide film as the base material, the packaging substrate has excellent thermal and chemical stability and can perform well under various extreme environmental conditions. Regardless of harsh conditions such as high temperature, high humidity, or chemical corrosion, the ABF GL102R8HF packaging substrate can maintain stable performance and ensure the reliable operation of electronic equipment.
Secondly, the packaging substrate offers excellent flexibility. Design engineers can customize the size and shape according to specific application requirements, making it flexibly adaptable to various application scenarios. Whether it is small electronic products or large industrial equipment, ABF GL102R8HF packaging substrates can meet different size and shape requirements, providing greater freedom for product design.
Finally, the ABF GL102R8HF package substrate offers extremely high reliability. Stable manufacturing processes and high-quality materials ensure the quality and reliability of packaging substrates. Through strict quality control and testing processes, we ensure that each packaging substrate can meet high standard performance requirements, thereby ensuring the stable operation of the entire electronic system.
Overall, ABF GL102R8HF packaging substrate has become the material of choice in the design of many electronic products due to its advantages such as high performance, flexibility and reliability. It provides a stable and reliable foundation for various application scenarios and promotes the continuous development and innovation of the electronics industry.
FAQ
What is the difference between ABF GL102R8HF package substrate and other package substrates?
ABF GL102R8HF packaging substrate uses polyimide film as the base material, which has excellent thermal stability and chemical stability, and has higher performance and reliability compared with traditional glass fiber-based packaging substrates. In addition, the ABF GL102R8HF package substrate also has low dielectric loss and excellent high-frequency performance, making it suitable for high-speed circuits and RF applications.
How to choose the right packaging substrate material for a specific application?
Selecting packaging substrate materials should consider the application’s operating environment, performance requirements, and cost budget. ABF GL102R8HF packaging substrate is an ideal choice for applications requiring high temperature performance and chemical stability. For applications requiring flexible or high-density wiring, consider using polyimide films or other specialty materials.
What are the cost factors in packaging substrate manufacturing?
The manufacturing cost of packaging substrates is affected by many factors, including material cost, manufacturing process complexity, size and number of layers, special process requirements, etc. Generally, the cost of packaging substrates increases with the number of layers and special process requirements, but the cost can also be reduced by optimizing the design and process.
What is the environmental impact of the production and processing of packaging substrates?
The production and processing of packaging substrates may involve chemical substances and energy consumption, causing certain environmental impacts. In order to reduce environmental burden, manufacturers usually take a series of measures, such as optimizing process flow, improving resource utilization, using environmentally friendly materials, etc. In addition, appropriate recycling and disposal measures can also reduce the environmental impact of discarded packaging substrates.