What is IC Substrate?
Advanced IC Substrate Vender. Super small trace/spacing and super small tolerance. We use high-precision equipment and BT materials. QYC has produce the IC substrates from 2 layer to 20 layers.
IC Substrate (Integrated Circuit Substrate) is a key component in the field of electronic packaging and plays a fundamental role in ensuring the function and performance of integrated circuits (ICs). In essence, IC substrate serves as the basic component of electronic packaging, providing a solid foundation for the mounting and connection of integrated circuits. It does much more than that, the IC substrate plays a vital role in supporting the electrical and mechanical integrity of the entire system.
The IC substrate assumes a crucial role by facilitating electrical connections. Serving as a bridge, it establishes links between integrated circuits and other system components, enabling seamless collaboration within electronic devices. The precision in its design is paramount, as it not only demands meticulous accuracy but also necessitates a thoughtful approach to transmission speed and signal stability. This meticulous attention ensures the overall reliability of the entire system.
Secondly, the IC substrate plays a key role in thermal management. As electronic devices continue to develop, the power consumption of integrated circuits is also increasing rapidly. In order to maintain good working condition, the IC substrate effectively disperses and conducts the generated heat through its special material and structural design, preventing overheating from adversely affecting system performance.
Simultaneously, the IC substrate delivers crucial mechanical support to guarantee the stable operation of the entire system across diverse environmental conditions. Its design necessitates meticulous consideration of factors like physical vibrations, shocks, and fluctuations in temperature within electronic equipment. This meticulous design approach ensures the safety and stability of integrated circuits and related components.
In the evolution of IC substrates, distinct types have emerged, encompassing organic substrates, ceramic substrates, and laminated substrates. Each variant of IC substrate showcases specific advantages tailored to address particular applications and performance criteria.
In general, IC Substrate, as the core component of electronic packaging, is not only a platform for connecting ICs, but also the cornerstone that supports the stable operation of the entire electronic system. Its continuously evolving design and manufacturing technology promotes the development of electronic equipment and provides solid support for the rapid progress of modern technology. In the future, with the continuous innovation of packaging technology, IC Substrate will continue to play an irreplaceable and important role in the electronic field.
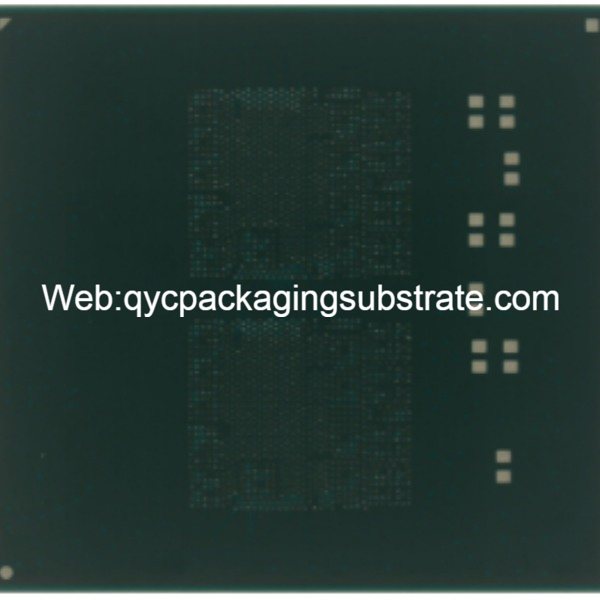
IC Substrate
What is the function of IC Substrate?
IC Substrate, as the core component of integrated circuit packaging, undertakes key functions and provides a solid foundation for the efficient and reliable operation of electronic systems. Its main functions cover three aspects: electrical connection, heat dissipation and mechanical support.
First, the IC substrate plays a key role in electrical connections. In modern electronic equipment, various integrated circuits with complex functions need to be electrically connected through IC substrates to achieve communication and collaborative work with each other. Through tiny and precise circuit paths, IC substrates efficiently pass electrical signals from one part to another, ensuring the coordinated operation of the entire system.
Secondly, the IC substrate also plays an important role in heat dissipation. As integrated circuits continue to develop, their power consumption also increases accordingly. Therefore, timely and effective heat dissipation becomes crucial. Through its exquisitely designed structure, the IC substrate can effectively transfer the generated heat to the surrounding environment to prevent the integrated circuit from overheating, thus ensuring the stability and reliability of the system.
The IC substrate assumes a crucial role in providing mechanical support. Its structural design must not only bear the weight of the integrated circuit but also withstand external environmental vibrations and impacts. A well-thought-out and robust mechanical support system ensures the stability of IC substrates across various application scenarios, with particular emphasis on mobile devices and automotive electronics where stringent requirements for mechanical support prevail.
In the pursuit of designing efficient and reliable electronic systems, engineers must possess a profound understanding of these critical functions and integrate them comprehensively into the IC substrate design. The stability of electrical connections, the effectiveness of heat dissipation, and the robustness of mechanical support directly impact the performance and lifespan of integrated circuits. Consequently, the IC substrate is not merely a supporter of electronic equipment; it stands as a pivotal assurance for its normal and optimal operation.
What are the types of IC Substrate?
Within the realm of contemporary electronic manufacturing, diverse types of IC substrates abound, each distinguished by unique characteristics tailored to various applications and performance requisites. Principal IC substrate categories encompass organic substrates, ceramic substrates, and laminate substrates.
Organic Substrates
Organic substrates, a prevalent variety of IC substrate, typically employ a base material of glass fiber reinforced epoxy resin. Recognized for their lightweight nature, cost-effectiveness, and commendable electrical insulation properties, these substrates find extensive application in consumer electronics such as smartphones and tablets. The flexibility and affordability of organic substrates make them a popular choice in these devices.
Ceramic Substrates
Ceramic substrates, often crafted from aluminum oxide or aluminum nitride ceramics, distinguish themselves with superior thermal conductivity and enhanced mechanical strength compared to organic substrates. Specifically designed for high-temperature and high-power scenarios, such as in high-performance computers and power amplifiers, ceramic substrates showcase durability and stability, rendering them ideal for deployment in challenging environments. Their robust attributes make ceramic substrates a preferred choice for applications requiring resilience and efficiency.
Laminate Substrates
Laminated substrate is a multi-layer IC substrate, usually composed of fiberglass, epoxy resin and copper foil. This structure provides higher density and more complex circuit design capabilities.
Characteristics and suitability of each type
Organic substrate
Features: lightweight, low cost, good electrical insulation.
Applications: Consumer electronics such as smartphones and tablets.
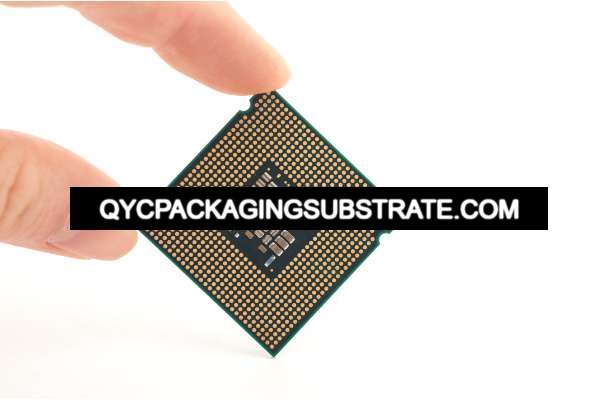
IC Substrate
Ceramic substrate
Characteristics: high thermal conductivity, good mechanical strength.
Applications: High temperature and high power applications such as high performance computers and power amplifiers.
Laminated substrate
Features: High-density, complex circuit design.
Applications of IC substrates extend to high-performance electronic equipment, encompassing servers, communications devices, and embedded systems. Engineers armed with a profound comprehension of diverse IC substrate types and their inherent characteristics can make informed decisions in selecting and designing substrates tailored to specific applications. This strategic approach serves to optimize the performance and reliability of electronic systems. The choices made in this regard play a pivotal role in contemporary electronics manufacturing, exerting a tangible impact on device performance and longevity.
What is the relationship between IC Substrate and packaging technology?
When exploring the connection between IC Substrate (IC substrate) and packaging technology, we need to delve into the classification of chip packaging technologies and their close relationship with IC substrates. IC substrates are not only the physical support of integrated circuits (ICs), but also play a vital role in the evolution of packaging technology.
Fundamentally, grasping the classification of packaging technology serves as the foundation for comprehending IC substrates. Packaging technology encompasses a diverse array of methods and processes, with chip packaging standing out as a key focal point. Various types of chip packaging technology emerge based on distinct applications and performance criteria, including ball grid array packaging (BGA), lead-free packages, chip-scale packaging, among others. The progression of these packaging technologies significantly influences the design and manufacturing of IC substrates.
As packaging technology undergoes continuous evolution, there is a concurrent refinement in the design and manufacturing of IC substrates. The march of progress in packaging technology has resulted in more compact and powerful chip packaging formats, thereby elevating the demands placed on IC substrates. Notably, advancements in high-density interconnect (HDI) technology enable the realization of a greater number of connection points within confined spaces, thereby imposing heightened requirements on the design of IC substrates.
An improved semi-additive method and advanced HDI manufacturing technology are adopted to make the manufacturing of IC substrates more precise and efficient. This not only improves production efficiency, but also enhances the performance and reliability of IC substrates.
In general, IC Substrate is inseparable from packaging technology. The classification and continuous advancement of packaging technology directly shape the design and manufacturing direction of IC substrates. Engineers need to constantly keep up with the latest trends in packaging technology to ensure that IC substrates can meet the changing needs of integrated circuits, thereby promoting innovation and development in the electronics field.
What is the difference between IC Substrate and PCB?
In today’s electronics field, IC substrate (Integrated Circuit Substrate) and traditional printed circuit board (PCB) play different roles in circuit design and manufacturing. We’ll delve into the differences between them, especially in the context of motherboards and electronic devices, and explore the rise of some specialized substrates, such as Substrate PCBs (SLP) and High Density Interconnect (HDI) substrates.
Basic differences between IC substrate and PCB
Although both IC substrates and PCBs are critical elements in electronic devices, they have significant differences in design and functionality. An IC substrate is a foundation specifically designed to support and connect integrated circuits (ICs), while a PCB is more general and used to connect a variety of electronic components. IC substrates are more optimized in electrical, thermal and mechanical properties to meet the special needs of ICs.
The rise of specialized substrates
As electronic equipment undergoes constant evolution, there is a burgeoning demand for substrates that are more advanced and high-performance. In response to this need, specialized substrates like Substrate-Like PCB (SLP) and High-Density Interconnect (HDI) substrates have emerged. These substrates are specifically engineered to overcome the density, performance, and size constraints associated with traditional PCBs, catering to the ever-growing requirements of modern electronic devices.
Substrate PCB (SLP)
Substrate PCB, referred to as SLP, is a new generation of substrate technology that is smaller, thinner, and more flexible. Compared with traditional PCB, SLP has higher density and shorter signal transmission path, which improves the performance and response speed of the circuit. This makes SLP ideal for use in modern mobile devices and other high-performance electronics.
High Density Interconnect (HDI) Substrate
HDI substrate is another specialized substrate that achieves higher circuit density through the use of fine lines and interconnection technology. This substrate design allows more components to be integrated into a smaller space, improving the performance of electronic devices. HDI substrates excel in high-frequency and high-speed applications and are suitable for communication equipment, medical devices, and other areas with extremely high performance requirements.
Advantages of dedicated substrates
Compared with traditional PCBs, dedicated substrates bring a series of advantages, including higher performance, smaller size, lighter weight and more flexible design. This makes them increasingly popular in industries pursuing advanced technologies, becoming the engine driving continuous progress in the electronics field.
What are the main structures and production technologies of IC Substrate?
As a core component of electronic packaging, IC Substrate (Integrated Circuit Substrate) covers a number of key technologies in its structural design and manufacturing process, which directly affects the performance and reliability of integrated circuits. Below we will delve into the main structure of IC Substrate and related advanced production technologies.
Structure and composition
The structure of IC Substrate is a complex and precise system, its main components include substrate, conductor layer, insulating layer and solder ball. The substrate serves as the basic support. Common organic substrates, ceramic substrates and laminated substrates are used. Different types of substrates are selected in different application scenarios to meet specific requirements. The conductor layer is responsible for circuit connections and organically organizes various components together through fine lines. The insulating layer forms insulating isolation between the conductor layers and prevents short circuits in the circuit.
Manufacturing process
The manufacturing process of IC Substrate consists of multiple steps, including advanced technologies such as improved HDI (High Density Interconnect) and semi-additive methods.
HDI technology
High-density interconnect technology is a method of improving circuit board performance by increasing the density of interconnect lines. In the manufacturing of IC Substrate, HDI technology allows more components to be integrated in a limited space by using fine lines and apertures. This technology can increase the signal transmission speed of the circuit board and reduce signal distortion, thereby enhancing the overall performance of the integrated circuit.
Semi-additive method
The semi-additive method is a process for manufacturing circuit boards by first adding a thin layer of metal to the surface of the substrate and then forming an interconnect structure on the metal layer. Compared with the traditional full additive method, this method saves more materials and improves the manufacturing accuracy. In the manufacturing of IC Substrate, the semi-additive method is widely used, effectively improving the performance of the circuit board.
These advanced manufacturing technologies enable IC Substrate to achieve higher performance and reliability in electronic devices. By optimizing the structural design and manufacturing process, engineers can integrate more functions in a limited space, thereby promoting the continuous development of integrated circuit technology. Therefore, an in-depth understanding of IC Substrate structure and production technology is crucial to ensure the advancement and reliability of electronic devices.
IC Substrate FAQs
In the field of IC Substrate, frequently asked questions involve several key aspects, and understanding these issues is crucial to a deep understanding of the importance of the modern electronics and semiconductor industry.
What is the difference between IC substrate and traditional PCB?
The primary distinction between an IC substrate and a conventional printed circuit board (PCB) lies in their design and functionality. While a traditional PCB serves the basic purposes of electrical connections and mechanical support, an IC substrate goes beyond these functions by playing a crucial role in heat dissipation. This differentiation becomes especially noteworthy in contemporary applications involving high-performance and high-density integrated circuits. In essence, the IC substrate serves as a multifaceted component, addressing not only connectivity and structural support but also actively participating in the efficient management of heat in advanced electronic systems.
How important is the heat dissipation function of the IC substrate?
One of the key responsibilities of IC substrates in electronic devices is to efficiently handle the heat generated by integrated circuits. Good heat dissipation design ensures that electronic components maintain proper temperatures while operating, thereby improving system reliability and performance.
What are the key innovations in IC substrate manufacturing technology?
The continuous innovation of IC substrate manufacturing technology is one of the engines driving the development of the electronics industry. Improved HDI manufacturing technology and semi-additive methods provide the possibility to design more compact and superior-performance IC substrates, meeting the needs of modern electronic products for miniaturization and high performance.
What is the role of IC substrate in chip packaging?
IC substrate and chip packaging technology are closely related and influence each other. Understanding their relationship is crucial for designing advanced chip packaging solutions, which directly affects the performance and reliability of integrated circuits in various applications.
What are the main challenges in IC substrate manufacturing?
Challenges faced in the IC substrate manufacturing process include high-density wiring, fine apertures, high integration and thermal management. Overcoming these challenges requires continuous technological innovation and improvement of manufacturing processes.
What is the future development trend of IC substrates in the electronics industry?
As electronic products continue to evolve, IC substrates will continue to play a key role. Future trends include higher integration, more compact designs, more advanced materials, and more efficient thermal management technologies.
In what modern applications is the importance of IC substrates reflected?
The importance of IC substrates is widely reflected in modern applications, especially in fields such as smartphones, computers, automotive electronics, and Internet of Things devices. Understanding how IC substrates support these critical applications helps to understand their indispensability in the modern electronics industry.
Full text overview of IC substrates
In summary, a deep understanding of IC substrates is crucial for optimizing the performance and reliability of electronic systems. In the increasingly complex electronic field, engineers and designers must realize the criticality of IC substrates in the entire system architecture. IC substrate is not only a platform for connecting and supporting integrated circuits, but also a key factor in achieving excellent performance in electronic systems.
With the continuous development of packaging technology, the evolution of IC substrates has become the engine driving innovation in semiconductor equipment. The cutting edge of packaging technology not only improves the manufacturing process of IC substrates, but also improves its performance and reliability. The introduction of new materials, design concepts and manufacturing methods enables IC substrates to better meet the high performance and reliability requirements of future electronic systems while adapting to different environments and application needs.
IC substrates are gradually becoming an indispensable cornerstone in the field of semiconductor equipment. Its role in electronic products is becoming increasingly important, from personal consumer electronics to industrial automation, all without the critical support of IC substrates. Engineers need to fully consider the characteristics of the IC substrate during the design stage to ensure that electronic systems can operate stably under various challenges and environments.
The dynamic development of packaging technology has found broader application scenarios for IC substrates in semiconductor equipment. As the basis for future technological progress, the continuous innovation of IC substrates will lead the development direction of the electronics industry.