AIN Substrate Manufacturer.As a leading Multilayer Load Testing PCB Manufacturer, we specialize in creating high-performance multilayer PCBs designed for rigorous load testing applications. Our advanced manufacturing processes ensure superior quality and reliability, meeting the stringent demands of various industries, including automotive, aerospace, and telecommunications. Partner with us for innovative solutions that guarantee optimal performance and durability in your critical testing environments.
Aluminum Nitride (AlN) substrates are widely used in high-performance electronics and optoelectronics due to their exceptional thermal and electrical properties. They provide superior thermal conductivity, excellent electrical insulation, and high mechanical strength, making them ideal for applications where heat dissipation and electrical isolation are critical. This article explores the properties, structure, materials, manufacturing process, applications, and advantages of AlN substrates.
What is an AlN Substrate?
An AlN substrate is a type of ceramic substrate composed primarily of aluminum nitride. It is used as a base material in various electronic components and circuits due to its outstanding thermal and electrical properties. AlN substrates are particularly beneficial in high-power and high-frequency applications where efficient heat management and electrical insulation are essential.
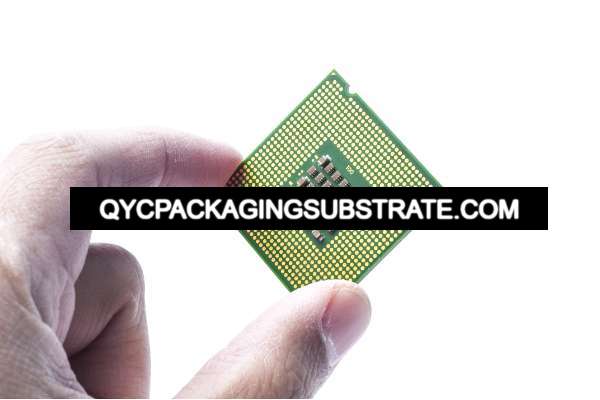
AIN Substrate Manufacturer
The unique properties of AlN substrates make them suitable for use in semiconductor devices, power electronics, microwave and RF components, and optoelectronic devices. They offer a combination of high thermal conductivity, low dielectric constant, and excellent mechanical strength, which is not commonly found in other substrate materials.
Structure of AlN Substrates
The structure of AlN substrates involves several key elements that contribute to their performance and reliability in electronic applications. Key structural components include:
The core material of the substrate, providing the primary thermal and electrical properties. AlN ceramics are formed through sintering processes that create a dense and homogeneous structure.
The surface of the AlN substrate is often polished to achieve a smooth and flat finish, which is essential for effective bonding with other materials and components.
To create electrical connections, metallization layers are applied to the AlN substrate. Common metallization materials include gold, silver, and nickel, which are deposited through various techniques such as sputtering, evaporation, or electroplating.
Vias are holes drilled into the substrate and filled with conductive material to create electrical connections between different layers of a multi-layer circuit.
Protective coatings may be applied to the substrate to enhance its durability and resistance to environmental factors such as moisture and chemicals.
Materials Used in AlN Substrates
The materials used in AlN substrates are selected to optimize their thermal, electrical, and mechanical properties. Key materials include:
The primary material, chosen for its high thermal conductivity, excellent electrical insulation, and mechanical strength.
Metals such as gold, silver, nickel, and copper are used for creating conductive paths on the substrate. These materials are chosen for their conductivity, adhesion properties, and compatibility with the AlN ceramic.
Various bonding materials, such as adhesives or solder, are used to attach components to the AlN substrate. These materials must provide strong adhesion and thermal stability.
Materials such as silicon nitride or silicon dioxide may be used as protective coatings to enhance the durability and environmental resistance of the substrate.
The Manufacturing Process of AlN Substrates
The manufacturing process of AlN substrates involves several precise steps to ensure high performance and reliability. The process includes:
High-purity aluminum nitride powder is prepared through chemical synthesis processes. The powder must have controlled particle size and purity to achieve the desired properties.
The AlN powder is shaped into the desired substrate form using techniques such as tape casting, isostatic pressing, or extrusion. These techniques ensure uniform density and thickness.
The shaped AlN material is sintered at high temperatures in a controlled atmosphere to create a dense and homogeneous ceramic. Sintering enhances the mechanical strength and thermal conductivity of the substrate.
The sintered AlN substrate is machined to precise dimensions and polished to achieve a smooth and flat surface. This step is crucial for ensuring effective bonding and performance.
Conductive metal layers are deposited onto the substrate using techniques such as sputtering, evaporation, or electroplating. These metallization layers create the necessary electrical connections.
The metallized substrate is patterned using photolithography or laser machining to create the desired circuit designs and via structures.
Components are bonded to the AlN substrate using adhesives or solder. This step requires precise alignment and bonding techniques to ensure reliable connections.
The assembled substrates undergo rigorous testing and inspection to ensure they meet performance and reliability standards. Electrical testing, thermal testing, and visual inspection are used to identify defects and ensure quality.
Application Areas of AlN Substrates
AlN substrates are used in a wide range of applications across various industries due to their unique properties. Key application areas include:
AlN substrates are used in power modules and high-power semiconductor devices, where efficient heat dissipation is critical for performance and reliability.
The low dielectric constant and high thermal conductivity of AlN substrates make them ideal for microwave and RF applications, including amplifiers, filters, and antennas.
AlN substrates are used in optoelectronic devices such as LEDs, laser diodes, and photodetectors, where thermal management and electrical insulation are essential.
AlN substrates are used in various semiconductor devices, including transistors, diodes, and integrated circuits, to enhance performance and reliability.
The biocompatibility and high performance of AlN substrates make them suitable for use in medical devices, including diagnostic equipment and implantable devices.
Advantages of AlN Substrates
AlN substrates offer several advantages that make them a preferred choice for high-performance electronic applications. These advantages include:
AlN substrates have exceptional thermal conductivity, which enables efficient heat dissipation and prevents overheating in high-power applications.
AlN substrates provide excellent electrical insulation, ensuring reliable performance and preventing electrical interference.
The high mechanical strength of AlN substrates ensures durability and reliability in demanding applications.
The low dielectric constant of AlN substrates minimizes signal loss and distortion, making them ideal for high-frequency applications.
AlN substrates are resistant to moisture, chemicals, and thermal cycling, ensuring long-term reliability and performance.
FAQ
What are the primary benefits of using AlN substrates in power electronics?
The primary benefits of using AlN substrates in power electronics include their high thermal conductivity, which enables efficient heat dissipation and prevents overheating, and their excellent electrical insulation, which ensures reliable performance and prevents electrical interference. These properties make AlN substrates ideal for high-power semiconductor devices and power modules.
How do AlN substrates enhance the performance of microwave and RF components?
AlN substrates enhance the performance of microwave and RF components by providing a low dielectric constant, which minimizes signal loss and distortion, and high thermal conductivity, which ensures efficient heat dissipation. These properties are crucial for maintaining signal integrity and preventing overheating in high-frequency applications.
What manufacturing techniques are used to create AlN substrates?
The manufacturing techniques used to create AlN substrates include powder preparation, forming (using techniques such as tape casting, isostatic pressing, or extrusion), sintering, machining and surface finishing, metallization, patterning, assembly, and testing and inspection. Each step is carefully controlled to ensure high performance and reliability.
In which industries are AlN substrates most commonly used?
AlN substrates are most commonly used in industries such as power electronics, microwave and RF components, optoelectronics, semiconductor devices, and medical devices. These industries require high-performance, reliable electronic components and systems, and AlN substrates provide the necessary properties to meet these demands.