Ajinomoto GX92 Package Substrate Manufacturer. the Package Substrate will be made with Showa Denko and Ajinomoto High speed materials.
In today’s electronic field, Ajinomoto GX92 packaging substrate plays a vital role. It not only connects various electronic components, but is also responsible for transmitting electrical signals. This article will delve into the importance of the Ajinomoto GX92 packaging substrate and introduce its wide range of applications in the electronics industry.
What is Ajinomoto GX92 package substrate?
The Ajinomoto GX92 package substrate is a high-quality printed circuit board (PCB) that plays a vital role in modern electronics. Its name comes from its manufacturer, Ajinomoto Fine-Techno Co., Inc., and its specific model number, GX92. This packaging substrate is designed to support and connect electronic components, providing critical support for the normal operation of various electronic devices.
As a type of printed circuit board, the manufacturing process of Ajinomoto GX92 package substrate is very complex and delicate. It is made of a stack of multiple layers of materials, including insulating materials and conductive layers, which are precision machined and processed in different process steps. This multi-layer structure enables the Ajinomoto GX92 package substrate to connect a large number of electronic components in a small space, providing a highly integrated and compact design solution.
To ensure its excellent performance, the Ajinomoto GX92 package substrate uses high-quality materials. It includes high-strength glass fiber as the base material and copper foil with excellent electrical conductivity as the conductor layer. These materials not only have excellent electrical conductivity, but also have excellent mechanical strength and durability, allowing them to maintain stable performance under various environmental conditions.
Due to its excellent design and manufacturing quality, Ajinomoto GX92 packaging substrates are widely used in electronic devices in various fields. Whether it is consumer electronics, such as smartphones and tablets, or industrial automation equipment, such as control systems and robots, Ajinomoto GX92 packaging substrates can meet high performance and reliability requirements.
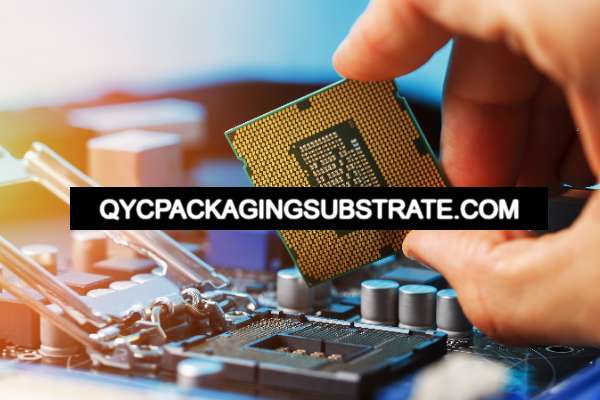
Ajinomoto GX92 Package Substrate Manufacturer
In general, Ajinomoto GX92 packaging substrate, as a high-quality printed circuit board, provides important support and guarantee for the development of modern electronic equipment with its excellent conductive properties, mechanical strength and wide range of application fields.
Ajinomoto GX92 package substrate design Reference Guide.
The design of the Ajinomoto GX92 package substrate is crucial, as it directly affects the performance and stability of electronic devices. When designing, a series of fundamentals and key factors need to be considered to ensure the quality and reliability of the final product.
Wiring layout
Good wiring layout is the basis for ensuring circuit stability and performance. When designing the Ajinomoto GX92 package substrate, it is necessary to consider the optimization of the signal transmission path, the separation of signal lines and power lines, and measures to reduce signal interference. Reasonable wiring layout can minimize signal transitions and crosstalk, and improve the anti-interference ability and stability of the circuit.
Electrical characteristics
The electrical characteristics of the Ajinomoto GX92 package substrate have a direct impact on the performance of electronic devices. During the design process, it is necessary to accurately analyze the electrical parameters of the circuit, including resistance, capacitance, inductance, etc., to ensure that the circuit has stable electrical performance when working. At the same time, it is also necessary to consider the speed and power consumption of signal transmission, as well as the anti-interference ability and anti-electromagnetic interference ability of the circuit, so as to meet the actual working needs of the equipment.
Thermal management
Thermal management is one of the key factors to consider in the design of the Ajinomoto GX92 package substrate. As electronic devices become more integrated, the power consumption of circuit components is also increasing, so the heat generated by the circuit must be effectively managed to prevent the device from overheating and affecting performance and lifespan. During the design process, heat sinks, fans, heat pipes and other heat dissipation devices can be used to effectively dissipate heat and maintain the stability and reliability of the circuit.
In summary, understanding the basic principles and key considerations of Ajinomoto GX92 package substrate design is critical to ensuring the performance and stability of electronic devices. Through reasonable wiring layout, accurate electrical characteristics analysis and effective thermal management measures, high-quality and high-reliability Ajinomoto GX92 packaging substrates can be designed to meet the needs of different application scenarios.
What material is used in Ajinomoto GX92 package substrate?
Ajinomoto GX92 packaging substrate is a high-performance material widely used in the modern electronics industry. Its manufacturing process uses a series of precision processes to ensure the stability and reliability of the final product. The following is a detailed introduction to the key materials used in the Ajinomoto GX92 package substrate:
Glass Fiber
Glass fiber is one of the basic materials for the Ajinomoto GX92 package substrate. It has excellent mechanical strength and heat resistance, and can effectively support electronic components and maintain the stability of the substrate structure.
Copper Foil
Copper foil is used as the main material for the conductive layer in the Ajinomoto GX92 package substrate. Its high conductivity and good processability allow circuits to reliably transmit electrical signals and perform well in high-frequency applications.
Solder Mask
Solder mask is a material coated on the surface of a PCB to cover areas that do not require soldering to prevent short circuits and corrosion. The solder mask layer of the Ajinomoto GX92 package substrate is usually made of high-temperature resistant and chemically stable materials to ensure that its integrity is maintained during the soldering process.
Silkscreen
The silk screen printing layer is used to print information such as text, logos, and component location marks on the Ajinomoto GX92 package substrate. This helps simplify the assembly process and improves production efficiency. Abrasion- and chemical-resistant materials are typically used to create screen-printed layers to ensure long-term readability and durability.
Overall, the high-performance materials used in the Ajinomoto GX92 package substrate, such as fiberglass, copper foil, solder mask and screen printing layers, together ensure the stability, reliability and durability of the substrate. These materials are not only widely used in the electronics industry, but also play a key role in various application fields, providing solid support for the development of modern science and technology.
What size are Ajinomoto GX92 package substrate?
The size of the Ajinomoto GX92 package substrate is an important consideration in the design process. Their size and shape can be customized according to the requirements of a specific application, allowing great flexibility and adaptability. From tiny earphone internal circuits to complex aerospace electronic systems, the Ajinomoto GX92 packaging substrate can be customized to meet different space constraints and functional requirements.
In the field of consumer electronics, Ajinomoto GX92 packaging substrates are often designed in small and exquisite shapes to fit into the compact spaces of small devices such as mobile phones, tablets and portable audio equipment. These small-sized substrates require highly integrated circuits and precise wiring to ensure the performance and stability of the device while maximizing space savings, making the device thinner, lighter, and more portable.
In fields such as industrial control systems, communication equipment, and medical instruments, the size of the Ajinomoto GX92 packaging substrate may be larger and more complex. These applications typically require more connection points, more circuit components, and more complex signal processing capabilities. Therefore, the packaging substrate requires a larger surface area to accommodate these components and provide sufficient space for wiring and heat dissipation to ensure system stability and reliability.
Whether it is a small or large Ajinomoto GX92 package substrate, its design needs to fully consider factors such as circuit performance, thermal management, EMI (electromagnetic interference) and wiring layout. Through careful design and optimization, the Ajinomoto GX92 packaging substrate can achieve optimal performance in different application scenarios, providing a solid foundation for the smooth operation of various electronic devices.
The Manufacturer Process of Ajinomoto GX92 package substrate.
The manufacturing process of the Ajinomoto GX92 package substrate is a complex and precise process involving multiple critical steps that require careful handling from design to final assembly. Here’s a detailed look at the manufacturing process:
Design
The first step in manufacturing the Ajinomoto GX92 package substrate is design. The design team uses computer-aided design (CAD) software to create the layout and routing of the circuit board. At this stage, they take into account the board’s functional requirements, connections, size, and layout.
Sample making
Once the design is complete, the next step is to make samples. This stage usually involves converting the design into an actual physical sample. Manufacturers may use special software and equipment to convert design files into graphic files needed for sample production.
Etching
Next comes the etching process. At this stage, the fiberglass substrate is placed into a chemical solution to remove unwanted copper foil, creating conductive paths on the circuit board. This step requires strict control and monitoring to ensure the accuracy and stability of the etching process.
Drilling
Once the circuit board’s copper foil layer has been etched with the desired circuit pattern, drilling is next. In this step, a high-precision drill bit is used to drill holes into the circuit board for mounting electronic components and connecting wires. These holes must be in precise locations to ensure the functionality and performance of the circuit board.
Assemble
The last critical step is assembly. At this stage, electronic components such as resistors, capacitors, integrated circuits, etc. are mounted onto the surface of the circuit board and connected by soldering. The assembly process also includes the application of solder mask and screen printing layers to protect the circuit board and mark component location and function.
Through these key steps, Ajinomoto GX92 packaging substrates can produce high-quality, high-reliability circuit boards that meet the needs of various electronic devices. Each step in the manufacturing process requires precise process control and quality management to ensure the performance and reliability of the final product.
The Application area of Ajinomoto GX92 package substrate.
Ajinomoto GX92 packaging substrate is a high-performance printed circuit board that is widely used in various industries. Its applications in consumer electronics, automotive, aerospace, medical equipment and communications are discussed in detail below.
In the field of consumer electronics, Ajinomoto GX92 packaging substrates are widely used in smartphones, tablets, home appliances and other products. Their high-density wiring and stable electrical characteristics enable these devices to implement more complex functions with higher performance and reliability.
In the automotive industry, Ajinomoto GX92 packaging substrates are used in vehicle electronic systems, such as engine control units (ECUs), airbag systems, entertainment systems, etc. They can withstand vibration and temperature changes during vehicle driving and ensure the stable operation of automotive electronic equipment.
In the aerospace field, Ajinomoto GX92 packaging substrates are widely used in key components such as aircraft and spacecraft control systems, communication systems, and navigation systems. Its lightweight design and high reliability ensure the safety and stability of aerospace vehicles.
In the field of medical equipment, Ajinomoto GX92 packaging substrates are used in medical imaging equipment, life monitoring equipment, diagnostic instruments and other equipment. These devices have extremely high requirements for precise signal transmission and stable electrical performance, and the Ajinomoto GX92 packaging substrate can meet these requirements.
In the field of communications, Ajinomoto GX92 packaging substrates are widely used in communications base stations, network equipment, wireless routers and other equipment. Its high-density wiring and excellent signal transmission performance can ensure stable connections and high-speed data transmission of communication equipment.
Overall, Ajinomoto GX92 packaging substrates have important applications in various industries, and their high performance and reliability provide key support for the development and progress of modern electronic equipment.
What are the advantages of Ajinomoto GX92 package substrate?
As an advanced electronic connection technology, Ajinomoto GX92 packaging substrate has many advantages in the modern electronics industry, making it one of the first choices for many electronic devices.
First, the Ajinomoto GX92 package substrate offers excellent compactness. Due to its highly integrated design, the Ajinomoto GX92 packaging substrate can accommodate more electronic components in a limited space, thereby streamlining and lightweighting the overall size of the device. This compact design not only helps improve the portability of the device, but also reduces product costs and material waste.
Secondly, the Ajinomoto GX92 package substrate has excellent reliability. Using high-quality materials and advanced manufacturing processes, the Ajinomoto GX92 package substrate has excellent electrical performance and mechanical strength, and can operate stably in harsh environmental conditions. This reliability ensures long-term stability and durability of the equipment, reducing the need for maintenance and repairs, thereby reducing usage costs.
In addition, the Ajinomoto GX92 package substrate offers the convenience of mass production. Compared with the traditional manual wiring method, the Ajinomoto GX92 packaging substrate adopts an automated production process, which can achieve large-scale, high-efficiency production, greatly improving production efficiency and product consistency. This advantage of mass production can not only meet the rapid growth of market demand, but also reduce production costs and improve competitiveness.
Finally, the Ajinomoto GX92 package substrate offers design flexibility. Designers can flexibly adjust the layout, layer and connection methods of the Ajinomoto GX92 package substrate according to specific application needs and technical requirements, thereby achieving functional customization and optimized design. This kind of design flexibility can effectively improve the performance and functions of products, meet the personalized needs of different customers, and enhance the market competitiveness of products.
To sum up, the Ajinomoto GX92 packaging substrate has become an indispensable and key component of modern electronic equipment due to its many advantages such as compactness, reliability, convenience of mass production and design flexibility, and has contributed to the development and development of the electronics industry. Innovation provides strong support.
FAQ
What is the cost of the Ajinomoto GX92 package substrate?
The cost of the Ajinomoto GX92 package substrate depends on several factors, including size, materials, design complexity and production volume. Generally speaking, the cost of customized packaging substrates may be higher, but as the scale of production increases, the cost will gradually decrease. You can get accurate cost information by asking the manufacturer or supplier for a specific quote.
What is the environmental impact of the Ajinomoto GX92 package substrate?
The Ajinomoto GX92 package substrate is manufactured from high-quality materials and has a low environmental impact. However, environmental pollutants such as waste materials and wastewater may be generated during manufacturing and processing. To reduce environmental impact, manufacturers usually take a series of measures, such as using environmentally friendly materials, optimizing production processes and implementing waste recycling.
How to recycle Ajinomoto GX92 package substrate?
Because Ajinomoto GX92 packaging substrates typically contain a variety of materials, such as metal, plastic, and fiberglass, effective separation and processing are required during recycling. Generally, methods for recycling Ajinomoto GX92 packaging substrates include mechanical treatment, chemical treatment, and thermal treatment. The recycled materials can be used to manufacture new packaging substrates or other products, helping to reduce resource waste and environmental pollution.
What are the common faults of Ajinomoto GX92 package substrate?
Common Ajinomoto GX92 package substrate failures include open circuit, short circuit, poor welding and component damage. These failures can be caused by design flaws, material quality issues, or errors in the manufacturing process. During use, the packaging substrate should be inspected and maintained regularly, and faults should be discovered and repaired in a timely manner to ensure the normal operation of the equipment.
How to solve common faults of Ajinomoto GX92 package substrate?
Methods to resolve Ajinomoto GX92 package substrate failures include checking connections, replacing damaged components, repairing poor soldering, and rewiring. For more complex faults, specialist equipment and techniques may be required to diagnose and repair them. It is recommended to contact the manufacturer or technical support team for help when encountering a fault.