What is Alumina PCB?
Alumina PCB |Al2O3 PCB Manufacturer. Ceramic PCB boards and ceramic Alumina PCBs production, we offer high quality ceramic Alumina Al2O3 PCB from 1 layer to 30 layers.
Alumina PCB, also known as aluminum oxide PCB, is a printed circuit board made from an aluminum oxide ceramic substrate. Compared with traditional FR4 materials, Alumina PCB has higher thermal conductivity and better mechanical strength, so it is widely used in applications requiring high performance and reliability. The design and manufacturing process of Alumina PCB is full of challenges, but its excellent thermal management capabilities and excellent electrical performance make it the first choice in many fields.
The properties of Alumina PCBs originate from the material itself. Alumina ceramic has extremely high thermal conductivity, allowing Alumina PCB to effectively conduct and disperse the heat generated in circuits. This is especially important for high-power electronic equipment, as they generate large amounts of heat, which, if not dissipated promptly and effectively, may degrade circuit performance or even damage the equipment. In addition, alumina has excellent mechanical strength and chemical stability, allowing Alumina PCB to operate stably in various harsh environments.
There are several factors to consider when designing an Alumina PCB. The first is thermal management. Designers need to rationally layout the components on the circuit board to maximize the thermal conductivity of Alumina PCB and ensure that the heat generated in the circuit can be effectively conducted to the PCB surface and discharged through a heat sink or other cooling device. Second is electrical performance. The dielectric properties and electrical insulation properties of Alumina PCB need to meet specific requirements to ensure the stability and reliability of the circuit.
Manufacturing Alumina PCB requires advanced technology and equipment. The manufacturing process typically begins with the preparation of an alumina ceramic substrate, followed by the deposition of conductive paths on the surface of the substrate using a special process. Next, a complete circuit structure is formed through multi-layer stacking and processing, and the required circuit pattern is formed through chemical etching or mechanical processing. Finally, Alumina PCBs undergo rigorous quality control and testing to ensure they meet specifications.
Overall, Alumina PCB is a high-performance printed circuit board with excellent thermal management and electrical performance. It is widely used in various fields, including communications, aerospace, medical equipment, etc., providing important support for the development of modern electronic equipment.
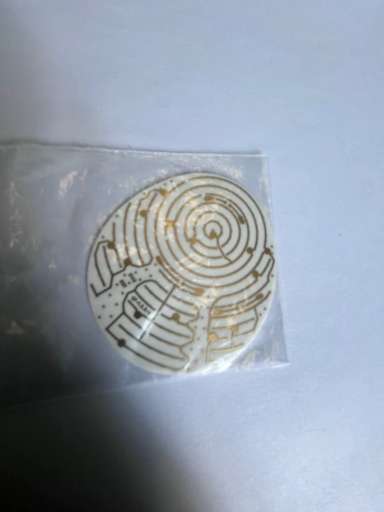
Alumina PCB |Al2O3 PCB
How to design Alumina PCB?
Designing Alumina PCBs requires careful planning and consideration as they play an important role in high performance and reliability. Here are the key factors to consider when designing an Alumina PCB:
Thermal Management: Alumina PCBs are known for their excellent thermal conductivity, so this feature must be taken advantage of during the design process. Designers need to consider the heat generation of components and how to efficiently remove heat from the board. Reasonable component layout and heat dissipation design are the keys to ensuring stable operation of Alumina PCB in high temperature environments.
Signal integrity: The design of Alumina PCB also requires attention to signal integrity, especially in high-frequency applications. Avoiding signal interference and crosstalk is one of the keys to ensuring stable circuit board performance. Signal distortion and loss can be minimized through measures such as proper ground design, differential pair layout, and impedance control.
Package and Component Layout: Choosing the proper package and component layout is critical to the performance of your Alumina PCB. The packaging type not only affects the size and shape of the circuit board, but also directly affects its heat dissipation effect and electrical characteristics. When it comes to component layout, designers need to take care to avoid hot spot concentration and signal interference while ensuring connectivity and accessibility between components.
Environmental adaptability: Alumina PCBs are often used in harsh industrial and aerospace applications, so they must be designed with stability and reliability in different environmental conditions in mind. Dust-proof, waterproof and anti-corrosion properties ensure Alumina PCB’s long-term stable operation in harsh environments.
Manufacturing Feasibility: When designing Alumina PCB, manufacturing feasibility and cost-effectiveness also need to be taken into consideration. Proper design solutions should minimize complexity and cost in the manufacturing process and ensure that circuit board production cycles and quality control meet expectations. Working closely with manufacturers to fully understand their production capabilities and technical levels can help designers develop more practical and feasible design solutions.
To sum up, designing Alumina PCB requires comprehensive consideration of factors such as thermal management, signal integrity, packaging and component layout, environmental adaptability, and manufacturing feasibility. Only by fully understanding these key factors can designers create Alumina PCB products with excellent performance, stability and reliability.
What is the manufacturing process of Alumina PCB?
What is the manufacturing process of Alumina PCB? This problem involves a series of precise and complex steps, each of which is critical and directly affects the performance and reliability of the final product. Let’s take a closer look at the manufacturing process of Alumina PCB.
Preparing the substrate: The first step in manufacturing Alumina PCB is to prepare the substrate. Alumina PCBs typically use alumina ceramic substrates, a material that has excellent thermal conductivity and mechanical strength, making it ideal for high-performance applications. In this step, the substrate is cut to the required size and undergoes rigorous cleaning and processing to ensure the surface is smooth and clean, ready for subsequent processes.
Printing the conductive pattern: Next comes the step of printing the conductive pattern. At this stage, a conductive material, usually copper, is coated on the surface of the substrate using techniques such as screen printing or chemical vapor deposition. These conductive patterns will become the wires of the circuit, connecting various components and parts.
Depositing a dielectric layer: Once the conductive pattern is formed, a dielectric layer is applied to isolate the wires and ensure proper operation of the circuit. These dielectric layers are usually ceramic or polymer substrates with excellent insulating properties. The selection and application of dielectric layers is critical to the stability and performance of the circuit.
Form the circuit structure: After the dielectric layer is formed, the excess parts on the dielectric layer are removed through processes such as photolithography and etching, leaving the required wires and circuit structure. This step requires highly sophisticated equipment and process control to ensure circuit accuracy and consistency.
Perforation and metallization: In order to realize the connection of multi-layer circuits, holes need to be drilled in the dielectric layer, and the hole walls are coated with conductive material, usually copper, through a metallization process. These conductive vias, called “vias,” establish electrical connections between different layers, enabling complex circuit functions.
Quality Control and Inspection: Strict quality control and inspection are carried out at every stage of Alumina PCB manufacturing. From inspection of raw materials to every step in the manufacturing process, and inspection of the final finished product, product reliability and performance are ensured. Any substandard products will be discovered and dealt with promptly to ensure the production of high-quality Alumina PCBs.
Through these steps, Alumina PCB undergoes a series of precise and complex processes from the initial substrate to the final product, ultimately presenting excellent performance and reliability to meet the needs of various high-performance electronic applications.
How are Alumina PCBs made?
The manufacturing of Alumina PCB is a precise and complex process that requires experienced technicians and advanced equipment. The following will introduce the manufacturing process of Alumina PCB:
Material preparation: The first step in manufacturing Alumina PCB is to prepare the materials. The core of Alumina PCB is composed of an alumina ceramic substrate, a material with excellent thermal conductivity and mechanical strength. During the manufacturing process, metallic materials such as copper or gold are also needed to create conductive traces, as well as ceramic or polymer-based insulating materials.
Design and Layout: Engineers use computer-aided design (CAD) software to design and lay out Alumina PCBs before proceeding with actual manufacturing. This includes determining the layout of the circuit, the location of components, and how they are connected to ensure optimal function and performance of the circuit.
Fabricating the conductive layers: Once the design is complete, the next step is to fabricate the conductive layers. This step typically involves depositing metallic conductive traces onto an Alumina substrate using techniques such as printing or chemical vapor deposition (CVD). These conductive lines will serve as connections between electronic components.
Add an insulating layer: In order to prevent short circuits between conductive layers, an insulating layer needs to be added on the conductive layer. These insulating layers are usually made of ceramic or polymer-based materials and are stacked and pressed layer by layer to ensure isolation from the conductive layer.
Forming connection holes: In order to establish electrical connections between different layers, conductive layers need to be connected through connection holes. This is often achieved through high-precision machining techniques such as laser drilling to ensure the accuracy and consistency of connecting holes.
Perform metallization: Once the connection hole is formed, it needs to be metallized to ensure the reliability and stability of the electrical connection. This usually involves coating a metal layer, such as copper or nickel, within the connection hole to enhance the conductivity of the electrical connection.
Inspection and Quality Control: Quality control is a vital part of the Alumina PCB manufacturing process. Upon completion, each PCB undergoes rigorous inspection and testing to ensure that dimensional accuracy, electrical performance and reliability meet specified standards.
Final processing and packaging: Once it passes quality control, Alumina PCB will undergo final processing and packaging. This includes steps such as trimming edges, punching holes, milling and cleaning, ultimately placing the PCB in appropriate packaging ready for shipment to the customer.
Overall, the manufacturing process of Alumina PCB requires a high degree of technology and precision equipment to ensure that the final product has excellent performance and reliability. Through strict quality control and exquisite craftsmanship, Alumina PCB can meet the needs of various applications and become an important part of the electronics industry.
How much does Alumina PCB cost?
How much does Alumina PCB cost? This question involves several factors, including board size, complexity, and quantity, as well as the manufacturer’s pricing strategy. Let’s take a closer look.
First, Alumina PCB may have a higher cost compared to traditional FR4 boards. This is because Alumina PCB uses a highly thermally conductive ceramic substrate, as well as other high-performance materials and manufacturing processes. The cost of these materials and processes is usually higher than conventional materials.
Secondly, the cost of Alumina PCB is also affected by the design complexity. If the board has a complex circuit layout, a large number of layers, or special requirements, manufacturing costs may increase accordingly. Because these requirements may require more processing steps and higher levels of technology to achieve.
In addition, the quantity of Alumina PCB produced will also affect the cost. Typically, large-volume orders can enjoy lower unit prices because manufacturers can reduce production costs through economies of scale. Conversely, low-volume orders may face higher unit prices because manufacturers need to spread fixed costs.
In addition to these factors, there are other factors that may affect the cost of Alumina PCBs, such as special processing requirements, additional testing or quality control needs, etc.
To sum up, the cost of Alumina PCB is a relatively complex issue and multiple factors need to be considered. However, while the cost may be higher, the superior performance and reliability of Alumina PCBs often provide excellent value, especially in applications with strict thermal management and performance requirements.
What materials are Alumina PCBs made of?
What materials are Alumina PCBs made of? This question sparked our curiosity about the makeup of this remarkable circuit board. Alumina PCB is made of special materials with excellent thermal conductivity and electrical insulation properties. Let’s explore it together.
First of all, the base of Alumina PCB is made of alumina ceramic. This ceramic material is known for its high thermal conductivity and mechanical strength, which can effectively disperse heat and ensure the stability and reliability of circuit boards in high-temperature environments. Alumina substrates have higher thermal conductivity and better high-temperature resistance than traditional fiberglass-reinforced FR4 substrates, making them ideal for high-power electronic devices.
In addition to the base material, Alumina PCB also includes conductive traces. These conductive lines are usually made of metal, such as copper or gold. Copper is a common choice because it conducts electricity well and is workable, providing a stable electrical connection on the circuit board. In some applications, precious metals such as gold are also used to improve the corrosion resistance and reliability of conductive lines.
Additionally, Alumina PCBs include insulating materials to isolate conductive lines to prevent short circuits and interference. These insulating materials are usually ceramic or polymer-based films that have good insulating properties and mechanical strength and are able to protect the circuit board from the external environment.
During the manufacturing process of Alumina PCB, these materials are precision processed and assembled to ensure the best quality and performance of the circuit board. Through careful selection and optimization of materials, Alumina PCB is able to achieve its excellent thermal management and electrical performance, making it the first choice for many high-end electronic devices.
In general, the material composition of Alumina PCB is a careful combination of alumina ceramic substrate, metal conductive lines and insulating materials, which provides the circuit board with excellent thermal conductivity and electrical performance, ensuring the reliability of the equipment in various harsh environments. run.
Who makes Alumina PCBs?
Alumina PCB, as a high-performance circuit board, is widely used in various industries, and its production is undertaken by professional manufacturers. In this field, supplier selection is crucial because it directly affects product quality, performance and reliability. When it comes to Alumina PCB manufacturing, there is one highly recognized supplier – our company.
As one of the major manufacturers of Alumina PCB, our company enjoys a high reputation in the industry for its excellent manufacturing processes and technical strength. The company is committed to providing high-quality, reliable Alumina PCB products to meet the various needs and application scenarios of customers.
The company has advanced production equipment and technical team, which can realize full process control from design to production, ensuring that every Alumina PCB meets strict quality standards. At the same time, the company focuses on research and development innovation and continuously introduces the latest technologies and processes to meet the changing market needs.
In addition to technical strength, the company also focuses on customer service. We are customer-centric and provide customers with customized solutions and professional technical support. Whether it is for large enterprises or small startups, we are committed to providing customers with the best quality services and establishing long-term and stable cooperative relationships.
In short, as a leading manufacturer of Alumina PCB, our company has won the trust and recognition of customers with its excellent manufacturing capabilities, advanced technology level and excellent customer service. We will continue to work hard to continuously improve product quality and service levels to create greater value for customers.
What are the 5 qualities of great customer service?
Excellent customer service is one of the key elements to the success of any business. By providing excellent customer service, businesses can build a good reputation, increase customer satisfaction, and develop a loyal customer base. Here are five key qualities of great customer service:
Excellent customer service starts with a timely response to customer needs. When customers raise inquiries, questions or complaints, it is crucial to respond promptly and provide solutions. Through fast and effective communication, customers feel valued and respected, and a good relationship of trust is established.
Excellent customer service requires specialized knowledge and skills. The customer service team should understand the company’s product or service and be able to provide accurate and clear answers. Through continuous training and learning, customer service personnel can continuously improve their professional level and better meet customer needs.
Reliability is one of the core attributes of great customer service. Customers hope to rely on companies to provide stable and reliable products and services. Therefore, companies should ensure product quality, ensure delivery time, and provide reliable after-sales support. By consistently delivering quality service, businesses can earn the trust and loyalty of their customers.
Great customer service requires flexibility to meet the individual needs of different customers. Customer needs may change at any time, so companies need to flexibly adjust their service methods and strategies. From customized products to flexible payment options, businesses should strive to meet customers’ specific needs to drive customer satisfaction and loyalty.
Great customer service is not only about performance during the sales process, but also about the quality of after-sales support. Customers may encounter problems or need help while using products or services, and good after-sales support can help customers solve problems and maintain satisfaction. Enterprises should establish a complete after-sales support system, including providing online or telephone support, maintenance services, product updates, etc., to ensure that customers can receive support and attention throughout the entire use cycle.
To sum up, great customer service is an integral part of a successful business. Through prompt response, expertise, reliability, flexibility and good after-sales support, companies can build a good reputation, enhance customer satisfaction, and win long-term support and loyalty from customers.
FAQS
Can the thickness of Alumina PCB be customized?
Yes, the thickness of Alumina PCB can be customized according to customers’ specific needs. Different application scenarios may require PCB boards of different thicknesses, so Alumina PCB manufacturers usually provide customization services to ensure that customers’ design requirements and performance needs are met.
What is the typical lead time for ordering Alumina PCBs?
Alumina PCB delivery times will vary based on the specific requirements of the order and the manufacturer’s production capabilities. Typically, standard specification Alumina PCBs may have shorter lead times, while custom or high-volume orders may require longer production lead times. Manufacturers usually provide an estimated delivery time after order confirmation to ensure that customers can arrange production and delivery plans in a timely manner.
Is Alumina PCB suitable for high temperature environments?
Yes, Alumina PCB performs well in high temperature environments due to its excellent thermal conductivity and heat dissipation capabilities. They are often used in applications requiring high temperature stability, such as automotive electronics, aerospace and other fields.
Is Alumina PCB suitable for high temperature environments?
Yes, Alumina PCB performs well in high temperature environments due to its excellent thermal conductivity and heat dissipation capabilities. They are often used in applications requiring high temperature stability, such as automotive electronics, aerospace and other fields.