Alumina substrates are a key component in modern electronics and high-performance applications due to their exceptional properties such as high thermal conductivity, electrical insulation, and mechanical strength. Made from aluminum oxide (Al2O3), these substrates are commonly used in industries like telecommunications, automotive, aerospace, and power electronics.
What is an Alumina Substrate?
An alumina substrate is a ceramic material composed primarily of aluminum oxide. It serves as a foundation for electronic circuits and components, offering a range of advantages that make it ideal for demanding applications.
High Thermal Conductivity:Efficient heat dissipation to prevent overheating in electronic devices.
Electrical Insulation:Excellent electrical insulation properties, ensuring safe and reliable operation.
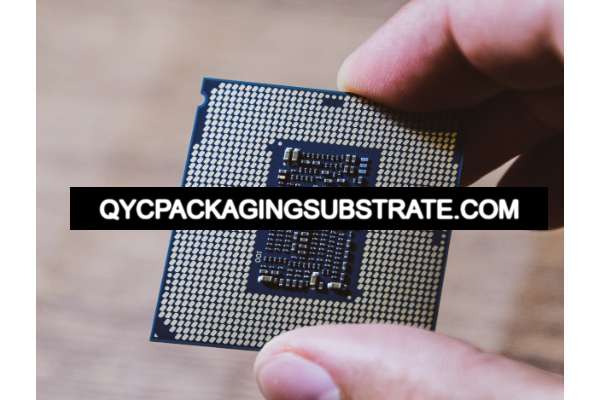
Alumina substrate Manufacturer
Mechanical Strength:High strength and durability to withstand mechanical stress.
Chemical Stability:Resistant to corrosion and chemical degradation, providing longevity in various environments.
Dimensional Stability:Maintains structural integrity under thermal cycling and mechanical loads.
Applications of Alumina Substrates
Power Electronics:Alumina substrates are widely used in power modules and devices due to their ability to handle high temperatures and dissipate heat effectively. They provide reliable performance in applications such as power transistors, diodes, and rectifiers.
Telecommunications:These substrates are essential in RF and microwave components, including antennas, filters, and oscillators. Their high-frequency performance and stability are crucial for telecommunications infrastructure.
Automotive Industry:Alumina substrates are utilized in sensors, ignition systems, and electronic control units (ECUs) within the automotive sector. Their durability and thermal management capabilities are vital for automotive electronics.
Aerospace:In aerospace applications, alumina substrates are used in sensors, communication systems, and electronic warfare components. Their robustness and reliability are critical for performance in extreme conditions.
Medical Devices:Alumina substrates are employed in medical devices such as imaging equipment, diagnostic instruments, and implantable electronics. Their biocompatibility and stability make them suitable for medical applications.
The Manufacturing Process of Alumina Substrates
The manufacturing process of alumina substrates involves several precise steps to ensure the final product meets the stringent requirements of various applications.
Powder Processing:High-purity aluminum oxide powder is prepared, often with additives to enhance specific properties.
Mixing and Milling:The powder is mixed and milled to achieve a uniform particle size distribution.
Tape Casting: A slurry of alumina powder is cast into thin sheets using a tape-casting process. This method allows for the production of thin and uniform substrates.
Pressing:The powder can also be pressed into the desired shape using isostatic or uniaxial pressing techniques.
High-Temperature Firing:The formed alumina is sintered at high temperatures (typically between 1500°C and 1700°C) to achieve densification and improve mechanical properties.
Controlled Atmosphere:Sintering is often done in a controlled atmosphere to prevent contamination and ensure uniformity.
Precision Machining: Post-sintering, the substrates undergo precision machining to achieve the required dimensions and surface finish.
Surface Treatment: Additional surface treatments, such as polishing or coating, may be applied to enhance specific properties like adhesion or thermal conductivity.
What Materials are Used in Alumina Substrates?
Aluminum Oxide (Al2O3):The primary material used in alumina substrates is high-purity aluminum oxide. This ceramic material provides the essential properties required for high-performance applications.
Additives:Various additives may be included in the alumina powder to enhance specific properties. These can include:
Magnesium Oxide (MgO): Used to improve sintering behavior and mechanical strength.
Silicon Dioxide (SiO2):Added to control grain growth and improve thermal stability.
Titanium Dioxide (TiO2): Enhances electrical insulation properties and chemical resistance.
What Size are Alumina Substrates?
The size of alumina substrates can vary widely based on the application and design requirements. Factors influencing the size include:
Application Requirements:Different applications, such as power modules or RF components, have specific size constraints and performance criteria.
Manufacturing Capabilities:The limitations of the manufacturing process, such as the size of the tape-casting equipment or the pressing molds, can influence the dimensions of the substrates.
Component Density: The number and type of components to be mounted on the substrate will determine the required size.
Advantages of Alumina Substrates
High Thermal Conductivity:Alumina substrates offer excellent heat dissipation, which is crucial for high-power and high-frequency applications.
Electrical Insulation:Their superior electrical insulation properties ensure reliable performance in electronic circuits and high-voltage applications.
Mechanical Strength:Alumina substrates are highly durable and can withstand mechanical stress, making them suitable for harsh environments.
Chemical Stability:These substrates are resistant to chemical corrosion, ensuring longevity and reliability in various applications.
Dimensional Stability: Alumina maintains its structural integrity under thermal cycling and mechanical loads, providing consistent performance.
FAQ
What are the main benefits of using alumina substrates in electronic applications?
Alumina substrates provide high thermal conductivity, excellent electrical insulation, mechanical strength, chemical stability, and dimensional stability, making them ideal for a wide range of electronic applications.
How are alumina substrates manufactured?
The manufacturing process involves material preparation (powder processing and milling), forming (tape casting or pressing), sintering at high temperatures, and precision machining and finishing to achieve the desired dimensions and properties.
What industries benefit most from alumina substrates?
Industries such as power electronics, telecommunications, automotive, aerospace, and medical devices benefit significantly from the unique properties of alumina substrates.
What materials are commonly used in alumina substrates?
High-purity aluminum oxide (Al2O3) is the primary material, often with additives like magnesium oxide (MgO), silicon dioxide (SiO2), and titanium dioxide (TiO2) to enhance specific properties.
How do alumina substrates improve thermal management in electronic devices?
Alumina substrates’ high thermal conductivity allows them to efficiently dissipate heat generated by electronic components, preventing overheating and ensuring reliable operation.