Aluminum Nitride PCB manufacturing, we mainly produce ultra-small bump pitch Ceramic Aluminum Nitride PCBs and ceramic BGA substrate, ultra-small trace and spacing packaging substrate.
In the field of modern electronics, aluminum nitride printed circuit board (Aluminum Nitride PCB) is an indispensable core component of electronic equipment. It not only provides mechanical support and electrical connections, but also carries the functions and performance of electronic devices. It is critical for engineers and hobbyists to understand the manufacturing process, materials, costs, and design elements of aluminum nitride printed circuit boards.
What is an aluminum nitride printed circuit board?
Aluminum Nitride Printed Circuit Board (Aluminum Nitride PCB) is a key component widely used in modern electronics. Not only does it provide mechanical support for electronic components, it also provides electrical connections to circuits through precise conductive paths. The design and manufacture of aluminum nitride printed circuit boards is a complex and sophisticated process involving multiple process steps and material selections.
In the manufacturing process of aluminum nitride printed circuit boards, an appropriate aluminum nitride substrate is first selected as the base material. Aluminum nitride substrates have excellent thermal conductivity and mechanical strength, making them ideal for high-power electronics and RF applications. Next, conductive paths are formed on the surface of the aluminum nitride substrate through a precise chemical etching or printing process. These paths will connect various components in the circuit to ensure the transmission of signals and the normal operation of the circuit.
Aluminum nitride printed circuit boards are often used in applications requiring high power processing and excellent thermal management, such as LED lighting, high-frequency communications and power electronics. Its excellent thermal conductivity and high temperature resistance allow it to effectively disperse the heat generated by electronic components and improve the reliability and stability of the system.
In addition to conductive paths, aluminum nitride printed circuit boards also need to be coated with insulating layers to prevent short circuits between wires and mutual interference between the insulating layers. Subsequently, the electronic components are soldered to the printed circuit board through drilling and metallization processes to form the final circuit connections. The entire manufacturing process requires strict quality control and precise process technology to ensure that the performance and reliability of the printed circuit board meet the design requirements.
In short, aluminum nitride printed circuit boards are an indispensable component of modern electronic equipment, and their precise design and manufacturing provide key support for the development and innovation of the electronics industry.
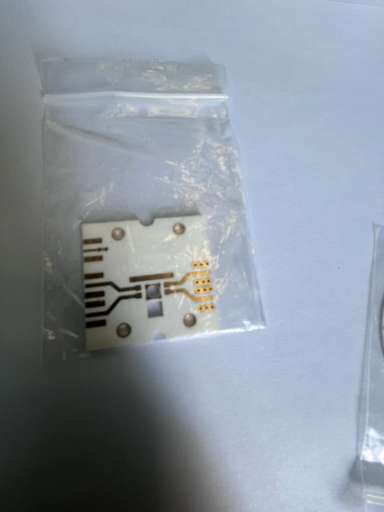
Aluminum Nitride PCB
How to design aluminum nitride printed circuit boards?
Designing aluminum nitride printed circuit boards is a precise and meticulous process that requires engineers to fully understand the principles and design requirements of the circuit, while using specialized software to optimize functionality, space utilization, and manufacturability. The key steps in designing aluminum nitride printed circuit boards are detailed below:
The first step in design is to capture the schematic of the circuit. At this stage, engineers use electronic design automation (EDA) software, such as Altium Designer, Cadence Allegro, etc., to draw the logical connections and functional layout of the circuit. The key to the schematic capture phase is to ensure accuracy and completeness so that subsequent placement and routing work can proceed smoothly.
After the schematic is captured, engineers place the individual components of the circuit on the printed circuit board. This includes the location determination of components such as chips, resistors, capacitors, connectors, etc. When placing components, engineers need to consider factors such as the circuit’s functional requirements, signal transmission paths, and thermal and electromagnetic compatibility.
Wiring is the process of laying out the connections between components. Engineers need to design appropriate wiring paths based on the circuit’s functional and performance requirements and minimize signal interference and transmission delays. During the routing process, engineers also need to consider the board hierarchy and distribution of routing layers to achieve optimal electrical performance and space utilization.
Layout is the process of connecting placed components and wiring together to form the final physical layout. Engineers need to consider the size, shape and location of external connection interfaces of the circuit board, as well as factors such as heat dissipation and mechanical strength. During the layout process, engineers typically make multiple optimizations and adjustments to ensure the functionality, reliability, and manufacturability of the circuit board.
Overall, designing aluminum nitride printed circuit boards requires engineers to use their creativity and expertise to achieve the functionality, space utilization, and manufacturability of the circuit through the delicate process of schematic capture, component placement, routing, and layout. The best balance of sex. Through reasonable design and optimization, engineers can ensure that aluminum nitride printed circuit boards have excellent performance and reliability to meet the needs of various applications.
What is the aluminum nitride printed circuit board manufacturing process?
The manufacturing process of aluminum nitride printed circuit boards (Aluminum Nitride PCB) is a precise and complex project involving multiple key steps to ensure the quality and reliability of the final product. These steps are detailed below:
First, the process of manufacturing aluminum nitride printed circuit boards begins with substrate selection. The substrate is the main body of the PCB and determines the mechanical strength and thermal conductivity of the circuit board. When selecting a substrate, the operating environment, power needs, and other specific requirements are often taken into consideration.
Next comes the lamination step, where layers of different materials are stacked together. In this process, aluminum nitride substrates are often combined with layers of other materials to achieve higher performance and functionality.
Once the substrate lamination is complete, the next step is copper patterning. This involves covering the surface of the substrate with conductive copper to form the required circuit paths and connections. Using techniques such as chemical etching or electroplating, the unnecessary copper parts are removed, leaving the designed circuit pattern.
After the circuit pattern is made, drilling needs to be done. These drill holes are used to make connections through the different layers of the circuit board and provide access when mounting components.
After drilling is completed, the hole walls need to be copper plated. This ensures that each connection point of the circuit board has good electrical conductivity to ensure the stability and reliability of signal transmission.
The last major step is etching. In this process, chemical etchants or laser technology are used to remove unwanted copper coverings, leaving only the designed circuit pattern. This ensures the accuracy and reliability of the circuit.
Through the above key steps, the manufacturing process of aluminum nitride printed circuit boards has completed the transformation from design to finished product. This process requires a high degree of precision and technical knowledge to ensure that the final product meets design requirements and has excellent performance and reliability.
How to make aluminum nitride printed circuit boards?
Manufacturing aluminum nitride printed circuit boards requires a series of precise and meticulous process steps. From the initial design concept to the final product, each stage is critical and directly affects the quality and reliability of the printed circuit board.
First, the process of manufacturing aluminum nitride printed circuit boards begins in the design phase. At this stage, engineers use professional circuit design software to create circuit schematics and convert them into PCB layout designs. During the design process, they must take into account the complexity of the circuit, the layout of the components, and the connectivity between components on the board to ensure that the final PCB design meets functional requirements and has good manufacturability.
Next comes the substrate preparation stage. Selecting the appropriate substrate material is critical to printed circuit board performance. Aluminum nitride is a premium substrate material with excellent thermal conductivity and insulation properties for high power and high frequency circuit applications. At this stage, engineers also clean and surface-treat the substrate to ensure that the copper layer can adhere firmly to the surface of the substrate.
This is followed by the copper deposition stage. At this stage, the substrate surface is covered with a thin layer of copper foil. This copper foil layer will become the conductive layer on the PCB and is used to connect various components in the circuit. Through processes such as chemical deposition or electroplating, copper foil is evenly deposited on the surface of the substrate and tightly combined with the substrate to ensure good electrical connection and mechanical strength.
Finally comes the final inspection stage. At this stage, the manufacturer performs rigorous quality control and testing on the manufactured aluminum nitride printed circuit boards. This includes using optical inspection and automated test equipment to check for issues such as wire connections, pad quality and electrical performance. Only PCBs that pass various tests and meet the required standards will be considered qualified products and enter the next stage of assembly and application.
In general, manufacturing aluminum nitride printed circuit boards requires a high degree of technical expertise and strict quality management. Each stage must be executed with precision to ensure the final product has excellent performance, reliability and stability to meet the needs of various electronic applications.
How much does an aluminum nitride printed circuit board cost?
The cost of aluminum nitride printed circuit boards is a key issue that directly affects the project budget and production feasibility. Understanding these cost drivers is critical for engineers and project leaders.
First, the size of aluminum nitride printed circuit boards is one of the main factors affecting cost. Generally speaking, larger size PCBs require more materials and production processes, so the cost will be relatively higher. Smaller size PCBs are relatively less expensive.
Secondly, the complexity of PCB also directly affects the cost. When the PCB layout is more complex and requires more layers, denser wiring, and finer manufacturing processes, the cost will increase accordingly. For example, multi-layer PCBs are more expensive than single-layer PCBs because their manufacturing process is more complex.
Materials are also one of the important factors that determine PCB cost. Aluminum nitride printed circuit boards usually use high-performance materials, such as aluminum nitride substrates, high-purity copper wires, etc. These materials are more expensive than ordinary PCB materials.
Finally, the number of PCBs will also have an impact on cost. Generally speaking, the cost of mass-produced PCBs will be relatively low because the manufacturing cost of a single PCB can be reduced through mass production. The cost of PCB produced in small batches is relatively high.
Therefore, for budget preparation and optimization of production costs, engineers and project leaders need to comprehensively consider the above factors and make reasonable decisions based on the specific needs of the project. Optimizing the size and complexity of the PCB as much as possible during the design stage, selecting appropriate materials, and rationally planning the production quantity are all effective ways to reduce costs.
What materials are aluminum nitride printed circuit boards made of?
The material composition of aluminum nitride printed circuit boards is one of the keys to ensuring their performance and reliability. When manufacturing aluminum nitride PCBs, choosing the right material is critical to ensuring the stability and functionality of the board. The main materials include substrate material, conductive layer and surface treatment layer.
Substrate material: Aluminum nitride printed circuit boards usually use fiberglass reinforced epoxy resin (FR-4) as the substrate material. FR-4 is a commonly used fiberglass composite material with excellent insulation properties, mechanical strength and heat resistance, and is suitable for most electronic applications. In addition to FR-4, there are also some advanced materials such as flexible substrates and metal matrix composite panels. Flexible substrates have good flexibility and bendability and are suitable for the application of curved electronic products, while metal matrix composite boards have good heat dissipation properties and are suitable for the heat dissipation needs of high-power electronic equipment.
Conductive layer: The conductive layer of aluminum nitride printed circuit boards usually uses conductive copper wires. Conductive copper wire is used to draw circuit patterns and connect electronic components. Its excellent conductivity and processability make it one of the preferred materials in PCB manufacturing.
Pad solder mask: Pad solder mask is an important layer used to protect and secure electronic components. It usually consists of solder pads and solder resist. The solder pads are used to connect the pins of the components and provide electrical connections between the electronic components and the PCB, while the solder resist is used to cover the solder pads to prevent short circuits and oxidation, and also provides a certain protective layer to protect the solder pads. Protected from corrosion and damage in the environment.
In general, the material selection of aluminum nitride printed circuit boards greatly affects the performance, stability and reliability of the circuit board. By selecting the appropriate substrate materials, conductive layers and pad solder masks, you can ensure that aluminum nitride printed circuit boards can perform optimally and function in a variety of application scenarios.
Who makes aluminum nitride printed circuit boards?
The manufacturing of aluminum nitride printed circuit boards is a critical link that determines the quality and reliability of the final product. In this area, supplier selection is crucial as they bear the responsibility of providing customers with high-quality, customized printed circuit boards. At our company, we strive to be your trusted aluminum nitride printed circuit board supplier, and the following are our core strengths:
We have an experienced engineering team that is proficient in the design and manufacturing of aluminum nitride printed circuit boards. They have profound technical accumulation and innovation capabilities, can cope with various complex project needs, and provide professional technical support.
Our company is equipped with advanced manufacturing equipment and technology, capable of achieving high-precision processing and production. From raw material processing to final inspection, we strictly control every manufacturing link to ensure product quality and stability.
We take quality as our life and ensure that every aluminum nitride printed circuit board meets the highest standards through a strict quality control system. From raw material procurement to production process, we implement strict quality management to ensure product performance and reliability.
We provide customized aluminum nitride printed circuit board services, designed and manufactured to our customers’ specific needs. Whether it’s low-volume production or mass customization, we can provide a solution to meet your needs.
We pay attention to customers’ time and progress requirements, and adopt efficient production planning and supply chain management to ensure timely delivery. No matter how urgent your project is, we are able to complete production on time and ensure product quality.
As a leading supplier in the field of aluminum nitride printed circuit boards, we will continue to strive to innovate and improve service levels to provide customers with better products and more satisfactory services. By choosing us, you will get a reliable partner to achieve business success and development together.
What are the five qualities of great customer service?
Excellent customer service is one of the key factors in the success of any business. Effective customer service not only improves customer satisfaction, but also enhances customer loyalty and helps a business build a positive reputation. Here are five key qualities of great customer service:
Responsiveness is one of the cornerstones of customer service. Respond to customer inquiries and concerns promptly and effectively so customers feel their needs are valued. Whether by phone, email, or online chat, responding promptly to customer questions and feedback is an important step in building good customer relationships. Continuously paying attention to and actively solving customer problems can enhance customers’ trust in the company and improve customer satisfaction.
Empathy is key to understanding your customers’ needs. Ability to build closer customer relationships by approaching customer problems and challenges with compassion and understanding. Listening to customers’ needs, deeply understanding their pain points and expectations, and then providing solutions that fit their actual situation can effectively enhance customer satisfaction and loyalty.
Reliability is one of the basic requirements for customer service. Continuously delivering on promises and commitments to customers is an important step in building trusting relationships. Customers expect to be able to rely on businesses to provide stable, consistent service, so maintaining reliability not only meets customer expectations but also builds a good reputation for the business.
Clear and transparent communication is key to building good customer relationships. Maintaining close communication with customers throughout the service process and providing timely relevant information and updates can reduce misunderstandings and dissatisfaction and ensure customer satisfaction with the service. Establishing open and transparent communication channels to keep customers informed of service progress and solutions to related problems will help enhance customers’ trust and loyalty to the company.
Proactive problem solving and striving to achieve customer satisfaction are at the core of great customer service. When facing customer complaints or problems, you must not only respond in a timely manner, but also take quick action to find solutions and ensure that the problem is properly resolved. By actively solving problems, companies can not only regain the trust of customers, but also establish a good reputation and attract more potential customers.
In a highly competitive market environment, quality customer service is one of the key factors for a company to stand out. Through key attributes such as responsiveness, empathy, reliability, communication and problem-solving skills, companies can build good customer relationships, improve customer satisfaction, and gain a competitive advantage in the market.
Frequently Asked Questions
What are the primary advantages of Aluminum Nitride PCBs compared to traditional FR-4 PCBs?
Aluminum Nitride PCBs offer several advantages over traditional FR-4 PCBs. Firstly, Aluminum Nitride has significantly higher thermal conductivity compared to FR-4, making it ideal for applications requiring efficient heat dissipation, such as high-power LED lighting and power electronics. Additionally, Aluminum Nitride provides excellent thermal stability, ensuring reliable performance under extreme temperature conditions. Furthermore, Aluminum Nitride PCBs exhibit superior dielectric properties, enabling high-frequency operation and low signal loss in RF and microwave applications.
Is Aluminum Nitride PCB fabrication more expensive than FR-4 fabrication?
Generally, Aluminum Nitride PCB fabrication tends to be more expensive than FR-4 fabrication due to the higher cost of materials and the specialized manufacturing processes involved. However, the overall cost depends on various factors such as board size, complexity, and order quantity. Despite the higher initial cost, Aluminum Nitride PCBs offer long-term cost savings by improving reliability and reducing the need for additional thermal management components.
Can Aluminum Nitride PCBs be used in flexible or rigid-flex applications?
Aluminum Nitride PCBs are typically not suitable for flexible or rigid-flex applications due to their inherent rigidity and brittleness. However, Aluminum Nitride can be used as a substrate material in combination with flexible substrates such as polyimide or polyester for hybrid applications requiring thermal management and high-performance characteristics. In such cases, proper design considerations and material compatibility testing are essential to ensure the reliability and durability of the final product.
What surface finish options are available for Aluminum Nitride PCBs?
Common surface finish options for Aluminum Nitride PCBs include electroless nickel immersion gold (ENIG), immersion silver, and immersion tin. These surface finishes provide excellent solderability, corrosion resistance, and flatness, ensuring reliable assembly and long-term performance in various environments. The choice of surface finish depends on specific application requirements, budget constraints, and compatibility with assembly processes.