Aluminum Nitride Substrate Manufacturer.An Aluminum Nitride Substrate Manufacturer specializes in producing high-performance substrates that offer exceptional thermal conductivity and electrical insulation. These substrates are ideal for advanced electronic applications, including power electronics, LEDs, and RF components. The manufacturer utilizes state-of-the-art technology and rigorous quality control processes to ensure the reliability and efficiency of their products, catering to the growing demands of the electronics industry.
Aluminum nitride (AlN) substrates are an integral part of modern electronic and thermal management solutions. Known for their excellent thermal conductivity and electrical insulation properties, AlN substrates are widely used in high-power electronic applications, LEDs, and other devices that require efficient heat dissipation. This article delves into the properties, structure, materials, manufacturing process, applications, and advantages of aluminum nitride substrates.
What is an Aluminum Nitride Substrate?
An aluminum nitride substrate is a type of ceramic substrate made from aluminum nitride material. It serves as a foundational platform for mounting and interconnecting electronic components, particularly in applications where high thermal conductivity and electrical insulation are crucial. AlN substrates are characterized by their ability to efficiently dissipate heat while maintaining electrical isolation, making them ideal for high-power and high-frequency applications.
Structure of Aluminum Nitride Substrates
The structure of aluminum nitride substrates is designed to optimize thermal performance and mechanical stability. Key structural elements include:
The primary structure of the substrate is composed of aluminum nitride ceramic. This material provides the necessary thermal conductivity and electrical insulation.
To enhance the solderability and protect the substrate from oxidation, surface finishes such as metallization layers (e.g., silver, gold, or nickel) are applied to the contact areas.
Conductive layers are patterned on the substrate surface to form electrical circuits. These layers are typically made from metals like copper or gold, deposited through processes such as sputtering or electroplating.
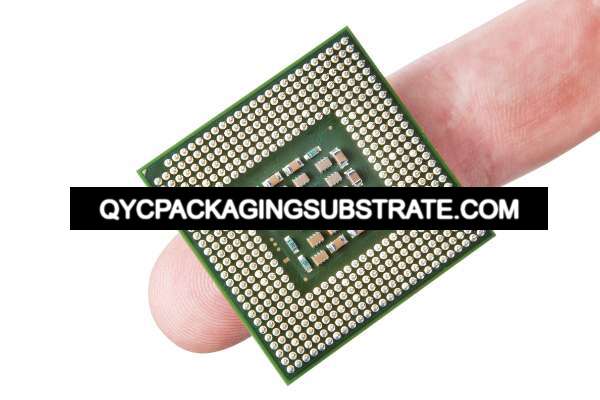
Aluminum Nitride Substrate Manufacturer
Vias are vertical interconnects that connect different layers of the substrate, allowing for complex circuit designs. They are created using precision drilling and metallization techniques.
Protective coatings, such as dielectric layers or passivation layers, may be applied to protect the substrate and conductive traces from environmental damage and enhance overall durability.
Materials Used in Aluminum Nitride Substrates
The primary material used in aluminum nitride substrates is aluminum nitride ceramic, known for its exceptional properties. Additional materials include:
The core material, AlN, offers high thermal conductivity (typically above 170 W/m·K) and excellent electrical insulation. It also possesses good mechanical strength and chemical stability.
Metals like copper, silver, gold, and nickel are used for the conductive traces and contact pads. These materials ensure reliable electrical connections and enhance solderability.
Advanced dielectric materials may be used in multi-layer AlN substrates to provide additional electrical insulation and improve overall performance.
Materials such as silicon dioxide (SiO2) or silicon nitride (Si3N4) are used for protective coatings to shield the substrate from environmental factors and mechanical wear.
The Manufacturing Process of Aluminum Nitride Substrates
The manufacturing process of aluminum nitride substrates involves several precise and controlled steps to ensure high quality and performance. Key steps include:
High-purity aluminum nitride powder is prepared and mixed with suitable binders and additives to form a homogeneous mixture.
The AlN mixture is shaped into the desired substrate form using techniques such as tape casting, pressing, or extrusion. This step creates the green body, an unfired ceramic substrate.
The green body is sintered at high temperatures (typically above 1600°C) in a controlled atmosphere to achieve full densification and optimize the thermal and mechanical properties of the AlN ceramic.
Conductive layers are deposited on the substrate surface using processes such as sputtering, screen printing, or electroplating. These layers are then patterned to form the required circuit traces.
Vias are created by precision drilling and subsequent metallization to establish vertical interconnections between different layers of the substrate.
Surface finishes, such as gold or nickel plating, are applied to the contact pads to improve solderability and protect against oxidation.
The final substrates undergo rigorous inspection and testing to ensure they meet all performance and reliability standards. Electrical testing, visual inspection, and automated optical inspection (AOI) are used to identify any defects or irregularities.
Application Areas of Aluminum Nitride Substrates
Aluminum nitride substrates are used in a wide range of electronic applications across various industries. Key application areas include:
AlN substrates are ideal for high-power electronic devices such as power transistors, IGBTs, and RF power amplifiers. Their excellent thermal conductivity ensures efficient heat dissipation, enhancing device reliability and performance.
In LED applications, AlN substrates provide efficient thermal management, improving the lifespan and performance of the LEDs. They are also used in other optoelectronic devices such as laser diodes and photodetectors.
AlN substrates are used in high-frequency and microwave circuits, such as RF modules and filters, due to their low dielectric constant and high thermal conductivity.
In the automotive industry, AlN substrates are used in advanced driver-assistance systems (ADAS), power modules, and other high-reliability applications that require efficient thermal management and electrical insulation.
AlN substrates are employed in medical devices that require high reliability and efficient heat dissipation, such as imaging equipment and implantable electronics.
Advantages of Aluminum Nitride Substrates
Aluminum nitride substrates offer several advantages that make them indispensable for modern electronic applications. These advantages include:
AlN substrates provide excellent thermal conductivity, enabling efficient heat dissipation and enhancing the reliability of high-power electronic devices.
The high electrical insulation properties of AlN substrates prevent electrical interference and ensure reliable operation of electronic components.
AlN substrates possess good mechanical strength and stability, making them suitable for demanding applications and harsh environments.
The chemical stability of AlN substrates ensures long-term reliability and resistance to environmental factors such as moisture and corrosive chemicals.
The ability to support high-density integration and complex circuit designs allows for the miniaturization of electronic devices, improving performance and functionality.
FAQ
What makes aluminum nitride substrates suitable for high-power electronic applications?
Aluminum nitride substrates are suitable for high-power electronic applications due to their high thermal conductivity, excellent electrical insulation, mechanical strength, and chemical stability. These properties enable efficient heat dissipation, reliable electrical performance, and long-term durability in demanding environments.
Can aluminum nitride substrates be used in high-temperature environments?
Yes, aluminum nitride substrates are highly suitable for high-temperature environments. Their excellent thermal conductivity and mechanical stability ensure reliable performance under thermal stress, making them ideal for applications such as high-power electronics and LEDs.
How do aluminum nitride substrates ensure effective thermal management?
Aluminum nitride substrates ensure effective thermal management through their high thermal conductivity, which allows efficient heat dissipation from the electronic components to the substrate. This prevents overheating and enhances the reliability and performance of the devices.
What industries benefit the most from using aluminum nitride substrates?
Industries that benefit the most from using aluminum nitride substrates include high-power electronics, LEDs and optoelectronics, telecommunications, automotive electronics, and medical devices. These industries require efficient thermal management, electrical insulation, and reliable performance, which AlN substrates provide.