Aluminum nitride ceramic PCB manufacturing. Ceramic Aluminum nitride PCB and Ceramic BGA package substrates Vendor. our cmpany offers this boards from 1 layer to 20 layers. high quality and fast shipping time.
In the world of electronics, Aluminum Nitride Ceramic PCBs stand out for their engineering marvels. Made from advanced materials, these specialized circuit boards play a key role in high-performance electronic devices. However, for many, the complexity of their manufacturing process remains shrouded in mystery. In this comprehensive guide, we’ll delve into the world of aluminum nitride ceramic PCB manufacturing, revealing its nuances and importance.
What is Aluminum Nitride Ceramic PCB?
Aluminum nitride ceramic PCB (Printed Circuit Board) is a special electronic component substrate made of aluminum nitride ceramic material. Compared with traditional fiberglass reinforced epoxy resin (FR-4) materials, aluminum nitride ceramic PCBs have significant advantages, especially in high-power and high-frequency applications.
First, aluminum nitride ceramic PCB has excellent thermal conductivity properties. Aluminum nitride itself is an excellent thermal conductive material, so it can effectively dissipate heat from electronic components in high temperature environments, helping to maintain the stability and reliability of the entire circuit board.
Secondly, aluminum nitride ceramic PCB has excellent mechanical strength. Compared with traditional substrate materials, such as FR-4, aluminum nitride ceramics are stronger and more durable and can withstand higher mechanical stress and vibration, thereby improving the durability and reliability of the entire electronic device.
Most importantly, aluminum nitride ceramic PCBs offer excellent reliability. In high-power and high-frequency applications, electronic components are susceptible to heat and electromagnetic interference, and aluminum nitride ceramic PCBs can effectively cope with these challenges, ensuring stable operation of the circuit and reducing the risk of failure and repair.
Therefore, aluminum nitride ceramic PCBs are widely used in fields such as high-frequency communication equipment, radio frequency modules, power amplifiers, laser drivers, etc., providing solid support for technological innovation and development in these fields. In the future, with the continuous advancement of technology and the expansion of application fields, aluminum nitride ceramic PCB will play a more important role and become an important part of the electronics industry.
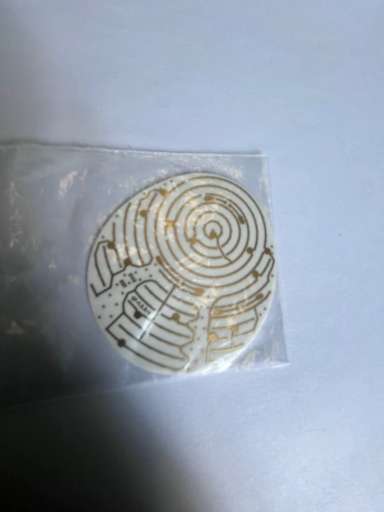
Aluminum nitride ceramic PCB
How to design aluminum nitride ceramic PCB?
Designing an aluminum nitride ceramic PCB is a task that requires extreme attention to detail. During the design process, engineers use various professional software, such as Eagle, Altium Designer or KiCad, to ensure that the final product can meet the requirements of high-performance applications.
First, engineers designing aluminum nitride ceramic PCBs need to create circuit diagrams. This step is the basis of the design process. Engineers draw the connection relationships and circuit structures between various electronic components based on product needs and functional requirements. When drawing circuit diagrams, engineers must ensure the logical correctness and functional integrity of the circuit to meet the performance requirements of the final product.
Next, engineers need to place components. Placing components on the PCB is a critical step. Engineers must place each component in the appropriate location according to the requirements of the circuit diagram. When placing components, engineers need to consider the distance and layout between components to ensure the stability and reliability of the circuit. In addition, engineers need to pay attention to component cooling and routing issues to maximize PCB performance and reliability.
Finally, engineers need to design optimized trace patterns. Traces are an important part of connecting various components, and the design of traces directly affects the performance and stability of PCB. When designing trace patterns, engineers must consider factors such as signal transmission speed, electromagnetic interference suppression, and heat dissipation to ensure that the PCB can operate stably in high-frequency and high-power environments.
Overall, designing an aluminum nitride ceramic PCB is a complex and delicate job. Engineers need to fully understand the needs and performance requirements of the product, and use professional software to design circuit diagrams, place components, and optimize trace patterns to ensure that the final product has excellent performance and stability.
What is the manufacturing process of aluminum nitride ceramic PCB?
The manufacturing process of aluminum nitride ceramic PCBs is a highly sophisticated process involving multiple critical steps, each of which plays a vital role in the quality and performance of the final product.
First, the process of manufacturing an aluminum nitride ceramic PCB begins with the preparation stage of the substrate. At this stage, high-quality aluminum nitride ceramics are selected as the substrate material, because the quality of the material directly affects the performance and reliability of the final PCB. The substrate then undergoes rigorous cleaning and surface treatment to ensure the surface is smooth and clean for smooth subsequent processes.
Next comes the laser drilling stage. In this step, advanced laser technology is used to accurately drill holes to form wire holes and component mounting holes on the circuit board. Laser drilling technology can achieve precise hole diameter and position, ensuring the accuracy of PCB electrical connections and component installation.
This is followed by the metallization process. At this stage, the wires and pads on the circuit board are formed by depositing a metal layer on the surface of the substrate. The metallization process uses advanced technologies such as vacuum evaporation or chemical deposition to ensure the uniformity and adhesion of the metal layer. These wires and pads will be used to connect electronic components and transmit signals and power.
After metallization is completed, strict quality inspection and surface treatment are also required. These steps include using high-resolution microscopy to inspect the quality of wires and pads, and applying high-temperature resistant protective coatings to improve PCB durability and stability.
Finally, after all processing and inspection, the aluminum nitride ceramic PCB will enter the final finishing and packaging stage. At this stage, the PCB will be cut to appropriate size, labeled and packaged for shipping and use.
To summarize, the manufacturing process of aluminum nitride ceramic PCBs involves multiple critical steps, each of which requires advanced technology and equipment to ensure the highest level of quality and performance of the final product. Through careful design and precision processing, aluminum nitride ceramic PCB has become the first choice for many high-performance electronic devices, making important contributions to the development of modern technology.
How much does an aluminum nitride ceramic PCB cost?
How much does an aluminum nitride ceramic PCB cost? There are many factors involved in this question, including board size, complexity, and manufacturing quantity. Before we delve into the impact of these factors on cost, let us first understand the characteristics and advantages of aluminum nitride ceramic PCBs.
Aluminum nitride ceramic PCBs are favored for their excellent thermal conductivity, mechanical strength and reliability. This type of PCB is suitable for applications requiring high power and high frequency performance, such as high-end communication equipment, medical instruments, and automotive electronic systems. Aluminum nitride ceramic PCBs are able to efficiently dissipate heat, provide better electrical performance, and have a longer service life than traditional substrates, making them the first choice for many critical applications.
However, this superior performance and reliability often comes with increased costs. First of all, the size and complexity of the board are one of the important factors that affect the cost. Larger board sizes typically require more materials and processing steps, so the cost increases accordingly. Complex designs, such as dense wiring, multi-layer structures and special processing requirements, will also increase manufacturing costs.
In addition, manufacturing quantity will also have an impact on costs. Typically, high-volume production reduces the cost per unit because fixed costs can be spread over more products. Conversely, low-volume production may result in higher unit costs because fixed costs need to be spread over fewer products.
Although aluminum nitride ceramic PCBs may be more expensive than traditional alternatives, their superior performance and reliability provide good justification for the investment in many applications. In high-end electronic equipment, stable performance and long-term reliability are often more important than cost. Therefore, although the cost of aluminum nitride ceramic PCBs may be higher, for critical applications, this additional investment is often worth it.
To sum up, the cost of aluminum nitride ceramic PCB is affected by many factors, including board size, complexity and manufacturing quantity. Although the price may be higher, its superior performance and reliability provide good reasons for investment in many applications. When selecting aluminum nitride ceramic PCBs, companies should weigh cost versus performance and make an informed decision based on the needs of their specific application.
What materials are used in aluminum nitride ceramic PCBs?
Aluminum nitride ceramic PCB is a technologically advanced printed circuit board whose constituent materials play a vital role in its performance. These PCBs are primarily composed of aluminum nitride ceramic substrates and conductive traces. When selecting these materials, engineers considered their advantages in thermal conductivity, electrical performance and reliability in harsh environments.
First, let’s look at aluminum nitride ceramic substrates. Aluminum nitride ceramic has excellent thermal conductivity properties, which means it can effectively conduct and disperse the heat generated by electronic devices, thereby helping to maintain the stability of the entire circuit board. In addition, aluminum nitride ceramics also have good mechanical strength and chemical stability, allowing them to maintain good performance under various environmental conditions.
Second, conductive traces are often made of metals like copper or gold. Copper is a commonly used conductive material because it has good conductivity and processability, and can form complex circuit structures on PCBs. As a high-quality conductive material, gold has higher conductivity and better corrosion resistance, so it is often used in applications with special requirements, such as medical devices and aerospace fields.
These materials were chosen based on their respective merits and suitability. The aluminum nitride ceramic substrate provides excellent thermal conductivity and stability, while copper or gold conductive traces ensure good electrical connections and signal transmission. This combination enables aluminum nitride ceramic PCBs to operate stably in high-temperature, high-frequency and high-power environments while maintaining good performance and reliability.
Therefore, choosing aluminum nitride ceramic PCB is a wise decision for electronic device manufacturers who require high performance and reliability. These PCBs can not only meet the design needs of complex circuits, but also maintain stability under extreme conditions, providing reliable guarantee for the long-term operation of the equipment.
Who is making aluminum nitride ceramic PCBs?
In the field of manufacturing aluminum nitride ceramic PCBs, supplier selection is crucial. As a PCB engineer with ten years of experience, we know the importance of the supply chain. Therefore, we carry out the manufacturing of aluminum nitride ceramic PCBs in-house to ensure product quality and reliability.
Professional experience: We have a professional team and advanced equipment that can skillfully handle the aluminum nitride ceramic PCB manufacturing process. We have rich experience and expertise in material selection, process control and quality assurance.
Independent research and development: As a supplier, we are not only a manufacturer, but also a promoter of technological innovation. We have independent research and development capabilities and can continuously improve product performance and quality according to customer needs and market changes.
Flexibility and customization: We focus on communication and cooperation with customers and can flexibly respond to different needs and requirements. Whether it is small batch customization or mass production, we are able to provide customized solutions that meet customer needs.
Quality Assurance: We strictly control every production link to ensure that products meet high standards of quality requirements. From raw material procurement to finished product inspection, we strictly implement the quality management system to provide customers with reliable product guarantees.
Integrity cooperation: We adhere to the principle of integrity cooperation and establish long-term and stable cooperative relationships with customers. We focus on credibility and reputation and have established a good brand image in the industry.
As a leader in the field of aluminum nitride ceramic PCB manufacturing, we will continue to uphold the concepts of professionalism, quality, flexibility and integrity to provide customers with quality products and services. We look forward to working with you to create a brilliant future together!
What are 5 qualities of a good customer service?
In the aluminum nitride ceramic PCB manufacturing industry, providing excellent customer service is crucial. Here are five key qualities of great customer service:
When faced with customer inquiries and questions, timely response is crucial. Effective communication builds customer trust and ensures their needs are addressed promptly. Providing timely and accurate information and support through quick responses to emails, phone calls or online chats is the foundation of good customer relationships.
Having deep knowledge and expertise is a prerequisite for providing excellent customer service. During the aluminum nitride ceramic PCB manufacturing process, customers may encounter various technical problems or challenges, so a professional technical support team must have solid knowledge and rich experience to be able to provide customers with professional guidance and support.
Understanding and empathizing with your customers’ needs and challenges is key to delivering customized solutions. When communicating with customers, listen to their needs and strive to understand the challenges they face. By building good relationships with customers, manufacturers can better meet their needs and provide customized solutions, thereby enhancing customer satisfaction.
Manufacturers must remain flexible and provide customized solutions in the face of changing needs and challenges. Customers may have different requirements and priorities, so manufacturers should be flexible in adapting manufacturing processes to meet customers’ specific needs and provide customized solutions to best meet customer expectations.
Transparent and honest communication about aspects such as delivery times, pricing, and technical capabilities are critical to building healthy customer relationships. Manufacturers should provide accurate information to customers and communicate promptly when encountering problems or delays to ensure customers understand the manufacturing process and maintain good credibility and reputation.
In summary, excellent customer service is one of the key factors for the success of aluminum nitride ceramic PCB manufacturing companies. Through responsive communication, deep knowledge and expertise, empathic understanding of customer needs, flexibility and customized solutions, and transparent and honest communication, manufacturers can build strong customer relationships, increase customer satisfaction, and achieve long-term business success.
FAQS
What are the advantages of Aluminum Nitride Ceramic PCBs over traditional PCB materials?
Aluminum Nitride Ceramic PCBs offer several distinct advantages over traditional PCB materials. Firstly, their exceptional thermal conductivity allows for efficient heat dissipation, making them ideal for high-power applications where heat management is critical. Additionally, Aluminum Nitride Ceramic PCBs exhibit excellent mechanical strength and reliability, ensuring long-term performance even in harsh operating environments. Moreover, their superior electrical insulation properties and low dielectric loss make them well-suited for high-frequency and high-voltage applications, minimizing signal loss and improving overall system performance.
Is Aluminum Nitride Ceramic PCB manufacturing environmentally friendly?
While Aluminum Nitride Ceramic PCB manufacturing involves advanced processes and materials, efforts are made by many manufacturers to prioritize environmental sustainability. One of the key aspects of environmentally friendly manufacturing is the adoption of lead-free soldering processes, reducing the environmental impact of hazardous substances. Additionally, some manufacturers implement recycling programs to minimize waste generation and utilize energy-efficient production practices. Furthermore, advancements in manufacturing technologies enable the optimization of resource utilization and waste reduction, contributing to a more sustainable production process overall.
What industries benefit most from Aluminum Nitride Ceramic PCBs?
Aluminum Nitride Ceramic PCBs find applications across a wide range of industries due to their unique properties and performance characteristics. One industry that particularly benefits from Aluminum Nitride Ceramic PCBs is the aerospace and defense sector. In aerospace applications, where weight reduction, thermal management, and reliability are critical factors, Aluminum Nitride Ceramic PCBs excel, enabling the development of lightweight and high-performance electronic systems for aircraft and spacecraft. Similarly, the telecommunications industry relies on Aluminum Nitride Ceramic PCBs for their ability to handle high-frequency signals with minimal loss, ensuring the efficient transmission of data in communication networks. Additionally, the automotive industry utilizes Aluminum Nitride Ceramic PCBs in electric vehicle power electronics, where their high thermal conductivity helps to dissipate heat generated by power electronics components, improving overall system efficiency and reliability.
How can I ensure the reliability of Aluminum Nitride Ceramic PCBs in my application?
Ensuring the reliability of Aluminum Nitride Ceramic PCBs in your application involves several key considerations. Firstly, it is essential to work with a reputable PCB manufacturer with expertise in Aluminum Nitride Ceramic materials and fabrication processes. By selecting a trusted manufacturer, you can be confident in the quality and consistency of the PCBs produced. Additionally, thorough design validation and testing are crucial steps in ensuring the reliability of Aluminum Nitride Ceramic PCBs. Conducting rigorous performance testing under simulated operating conditions can help identify any potential issues and ensure that the PCBs meet the requirements of your application. Furthermore, proper handling, installation, and maintenance practices are essential for maximizing the lifespan and reliability of Aluminum Nitride Ceramic PCBs in real-world operating environments.