Aviation PCB Manufacturer.High speed and high frequency material packaging substrate Manufacturer. Advanced packaging substrate.
With the vigorous development of the aviation industry and the rapid advancement of electronic technology, the design and manufacturing of avionics equipment is moving towards more complexity and precision. In this highly competitive and quality-critical industry, aviation PCB, as the representative of printed circuit boards, plays a vital role. It not only provides a solid foundation for avionics equipment, but also directly affects its performance, reliability and safety. With the continuous evolution of technology, aviation PCB is increasingly demonstrating its importance in the field of avionics with its innovation and reliability.
What is Aviation PCB?
Aviation PCB (Printed Circuit Board) is a key component specially designed for avionics equipment. In the aviation field, the stability, reliability and performance of electronic equipment are crucial, and aviation PCB, as the core component of these equipment, undertakes the important tasks of transmitting signals, supporting electronic components and providing electrical connections.
The design of aviation PCB is significantly different from that of ordinary electronic equipment PCB. First, aerospace PCBs must be able to operate under extreme environmental conditions, including wide temperature changes, constant mechanical vibration, and frequent electromagnetic interference. This means that aviation PCB must have excellent high temperature resistance, shock resistance and anti-interference ability to ensure the stable operation of avionics equipment under various extreme conditions.
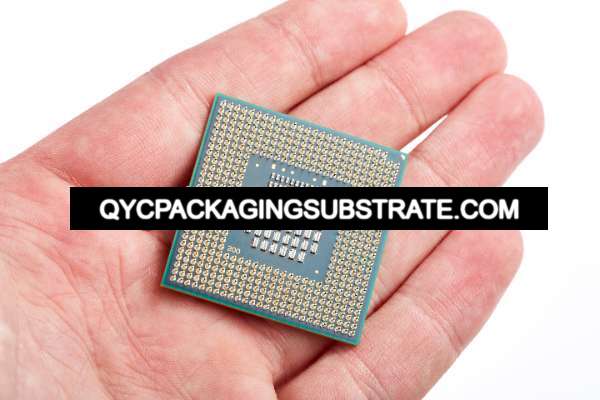
Aviation PCB Manufacturer
Secondly, the design of aviation PCB must also take into account the special requirements of the aircraft itself, such as space restrictions, weight restrictions, and the dynamic characteristics of the aircraft. Therefore, when designing aviation PCBs, the size and weight of the circuit boards need to be precisely controlled to ensure that they can fit perfectly into the aircraft’s fuselage structure and do not add additional load.
In addition, aviation PCBs also need to be highly integrated to meet the requirements of small size and light weight for avionics equipment. By integrating multiple functional modules onto one PCB, it can not only reduce the connections between circuit boards and improve the reliability of the system, but also reduce the volume and weight of the entire system, making the aircraft more lightweight and efficient.
In short, the design and manufacturing of aerospace PCB must undergo careful consideration and rigorous testing to ensure its reliability and stability in extreme environments. As a key component of avionics equipment, the excellent performance of aviation PCB is crucial to ensuring the safe flight and normal operation of aircraft.
Aviation PCB design Reference Guide.
The design of aviation PCB is one of the keys to successfully achieving high performance and reliability in avionics equipment. The design process must strictly follow various standards and guidelines to ensure that the circuit board can operate stably in the extreme aviation environment. Here are some key considerations:
Standards and Guidelines to Follow
Aerospace PCB designs must comply with the aerospace industry’s strict standards and guidelines, such as RTCA DO-254 and MIL-PRF-31032, etc. These standards cover all aspects from design to manufacturing, ensuring the reliability and compliance of aerospace PCBs.
Size and shape
The size and shape of aviation PCBs must be designed according to the space constraints of the aircraft and the needs of the electronic equipment. Typically, aerospace PCBs need to be compact in size and lightweight to maximize space savings and weight reduction.
Hierarchy
The hierarchical design of aerospace PCB is an important factor in ensuring the performance and functional integrity of the board. A reasonable hierarchical structure can reduce the complexity of the circuit board and improve its reliability and maintainability.
Material selection
Material selection for aerospace PCB is crucial and must take into account its performance under harsh conditions such as high temperature, low temperature, vibration and electromagnetic interference. Commonly used materials include special high-temperature fiberglass-reinforced epoxy resin (FR-4) and polyimide (PI), and the selection of metal copper-clad layers also needs to take factors such as thermal conductivity and electromagnetic shielding into consideration.
Signal Integrity and Electromagnetic Compatibility
Aviation PCB design must focus on signal integrity and electromagnetic compatibility to ensure the stability and reliability of the circuit board in high-speed signal transmission and electromagnetic environments. Adopting appropriate routing and shielding techniques to reduce signal interference and crosstalk is one of the key measures to ensure circuit board performance.
Aviation PCB design is one of the key factors in achieving high performance and reliability for avionics equipment. By following strict standards and guidelines and considering factors such as size, hierarchical structure, material selection, and signal integrity and electromagnetic compatibility, aviation PCBs can be ensured to operate stably in extreme environments, providing solid technology for the development and progress of the aviation industry. support.
What material is used in Aviation PCB?
The manufacturing of aerospace PCBs must use high-quality materials to ensure their reliability and stability in extreme environments. In the aviation field, electronic equipment often faces severe challenges, such as high and low temperatures, humidity changes, mechanical vibration, and electromagnetic interference. Therefore, choosing the right materials is critical to the performance of aerospace PCBs.
Special fiberglass reinforced epoxy resin (FR-4) is one of the most commonly used substrate materials for manufacturing aerospace PCBs. FR-4 has good mechanical strength and heat resistance, maintaining stability over a wide temperature range. It also has high insulation performance, which can effectively prevent circuit interference between circuit boards and improve the reliability of the system. In addition, the price of FR-4 is relatively low and suitable for mass production, so it has been widely used in aerospace PCB manufacturing.
In addition to substrate materials, metal copper clad layers are also a crucial part of aerospace PCB manufacturing. The copper clad layer is usually covered with copper foil on the surface of the substrate, and is chemically etched to form the required circuit pattern. Copper has excellent electrical and thermal conductivity and can effectively transmit current and dissipate heat, thereby ensuring the stability and reliability of the circuit. In addition, the copper clad layer can also provide good solderability to facilitate connection with other electronic components, and at the same time enhance the mechanical strength of the circuit board, helping to resist the influence of the external environment.
In short, the materials used in the manufacturing of aviation PCBs must have a high degree of temperature resistance, moisture resistance and mechanical strength to cope with the extreme aviation environment. Special fiberglass reinforced epoxy resin (FR-4) and metal copper-clad layers are commonly used materials and play an important role in aviation PCB manufacturing, providing a solid guarantee for the performance and reliability of avionics equipment.
What size are Aviation PCB?
The size of the aerospace PCB is one of the important factors that is carefully considered during the design stage. Because avionics equipment often needs to be installed in a limited space, the weight limit of the aircraft also needs to be taken into consideration. Therefore, aerospace PCBs are often designed to be compact and lightweight to meet these stringent requirements.
First, the size of the aviation PCB is determined based on the functional and layout requirements of the specific avionics equipment. Different equipment may require PCBs of different shapes and sizes to accommodate various circuit components and accommodate the specific airframe structure and aircraft interior space layout.
Secondly, the compact design of aviation PCB allows the circuit board to achieve higher integration within limited space. This means that more electronic components and circuit connections can be accommodated on a small PCB, allowing for more complex functions. This highly integrated design helps reduce the overall size of the avionics while increasing its performance and functionality.
In addition, lightweight is also one of the important considerations in aviation PCB design. The weight of an aircraft is critical to flight performance and fuel efficiency. Therefore, aviation PCBs usually use lightweight materials and optimize the design to reduce unnecessary weight. This lightweight design not only helps reduce the overall weight of the aircraft, but also improves its load capacity and flight efficiency.
To sum up, the size design of aviation PCB takes into account the functional requirements, space constraints and weight requirements of avionics equipment. Through compact and lightweight design, aviation PCB can provide high-performance, reliable and safe electronic solutions for aircraft, promoting the continued development and progress of the aviation industry.
The Manufacturer Process of Aviation PCB.
The manufacturing process of aviation PCB is a complex and delicate project involving multiple links and professional technologies. The manufacturing process of aviation PCB will be introduced in detail below:
Design phase
The first is the design phase, which is one of the key steps in aerospace PCB manufacturing. At this stage, engineers use CAD software for circuit design and layout planning based on the functional and performance requirements of the avionics equipment. The special requirements of the aviation environment need to be taken into consideration during the design process, such as anti-vibration, anti-electromagnetic interference, etc.
Purchase of raw materials
After the design is completed, various raw materials need to be purchased, including substrate materials, metal copper-clad materials, chemicals, etc. Selection of high-quality raw materials is critical to guarantee the performance and reliability of the final product.
Printing
Printing is one of the core steps in manufacturing PCBs. During the printing process, the designed circuit pattern is first transferred to the surface of the substrate through photolithography technology, and then chemical etching is used to remove unnecessary metal copper to form the circuit pattern.
Plating
Electroplating is to enhance the conductivity and corrosion resistance of PCB. In this step, a metal layer is deposited over the exposed conductive areas by immersing the substrate in an electrolyte, thereby forming a continuous conductive layer.
Forming
Molding is the process of cutting a PCB into the desired size and shape. Depending on the design requirements, the PCB is precisely cut using mechanical or laser cutting equipment to meet aircraft space constraints and weight requirements.
Test
The final stage is testing, which is a critical step to ensure aerospace PCB performance and quality. By using various test equipment and technologies, PCBs are tested for functionality, electrical performance, reliability, etc. to ensure that they meet design specifications and can operate stably in the aviation environment.
To summarize, the manufacturing process of aerospace PCBs involves multiple critical steps, each of which must be performed precisely to ensure the quality and performance of the final product. Only under strict quality control can aviation PCBs meet the high requirements of avionics equipment and contribute to the development of the aviation industry.
The Application area of Aviation PCB.
As the core component of avionics equipment, aviation PCB is widely used in various aircraft, including airplanes, helicopters, spacecraft and drones. Its applications in the aviation field cover multiple key systems, including communications, navigation, radar and flight control.
First of all, aviation PCB plays an important role in communication systems. Modern aircraft communication systems require high reliability and good signal transmission performance to ensure flight safety and data transmission stability. Aviation PCB provides stable circuit support for communication equipment, including radio, satellite communications and data links, etc. through optimized design and material selection.
Secondly, aviation PCB plays a key role in navigation systems. The aircraft navigation system requires precise positioning and navigation functions to ensure the accuracy and safety of the navigation path. The high-density wiring and precision manufacturing technology of aviation PCB provide reliable electronic support for navigation equipment, including inertial navigation systems, global satellite navigation systems (GNSS) and radar positioning systems.
Third, aviation PCB also plays an indispensable role in radar systems. Radar systems are important sensing and monitoring equipment for aircraft, used to detect and track targets and obstacles in the surrounding airspace. Aviation PCB provides a stable and reliable electronic foundation for radar equipment, including weather radar, terrain tracking radar and stealth detection radar, etc. by providing high frequency, high speed and high sensitivity circuit design.
Finally, aviation PCBs also play a vital role in flight control systems. The flight control system is the intelligent core of the aircraft, responsible for monitoring the flight status, adjusting the heading and attitude, and ensuring the stability and safety of the aircraft. Aviation PCB provides reliable electronic support for flight control systems, including autopilot systems, flight attitude control and guidance systems, etc. by providing high-performance computing and real-time control functions.
In general, the wide application of aviation PCB in the aviation field provides key electronic technical support for modern aircraft and promotes the continuous development and progress of aviation technology. With the continuous development of the aviation industry and the continuous innovation of electronic technology, aviation PCB will continue to play an important role in providing a higher level of guarantee for the performance, safety and reliability of aircraft.
What are the advantages of Aviation PCB?
Aviation PCB has obvious advantages in avionics equipment, and these advantages make it the first choice for the aviation industry. The following are the advantages of aerospace PCB over traditional wiring methods:
Highly integrated
Aerospace PCB uses printing technology to integrate complex circuit board designs into a small, lightweight board. This highly integrated design allows avionics equipment to have more functions and performance in a restricted space.
High reliability
The manufacturing process of aerospace PCBs undergoes strict quality control and testing to ensure that they can maintain stable performance in extreme environments. For aircraft, reliability is crucial because it is related to flight safety and the safety of passengers.
Light in size
Compared with traditional wiring methods, aviation PCBs are made of lightweight materials, which can significantly reduce the weight of electronic equipment. In aviation, reducing aircraft weight is critical to fuel efficiency and flight performance.
Easy to maintain
Aviation PCBs are designed with clear structures and compact wiring, making it easier for maintenance personnel to identify and solve problems. On aircraft, timely maintenance and repairs are critical to ensuring the normal operation of equipment.
Troubleshooting
Aviation PCB has good fault diagnosis capabilities. When the equipment fails, the problem can be quickly located and repaired. This rapid fault diagnosis capability helps reduce the time the aircraft spends on the ground and improves flight punctuality and efficiency.
In general, aviation PCB has obvious advantages over traditional wiring methods in terms of integration, reliability, lightweight, maintenance and fault diagnosis. In the design and manufacturing of avionics equipment, aviation PCB has become an indispensable and important component, providing solid technical support for the development and progress of the aviation industry.
FAQ
Is the manufacturing of aerospace PCB restricted by special environmental conditions?
Yes, the manufacturing of aviation PCB must take into account the special environmental conditions of the aircraft, such as high temperature, low temperature, high humidity and mechanical vibration. Therefore, special attention needs to be paid when selecting materials and manufacturing processes to ensure that the PCB can still maintain stability and reliability under these extreme conditions.
How to ensure the reliability of aviation PCB?
In order to ensure the reliability of aviation PCBs, every link in the manufacturing process needs to be strictly controlled, including the selection of raw materials, the execution of the production process, and the testing of the final product. In addition, it is also necessary to comply with relevant standards and specifications of the aviation industry, such as AS9100, etc., to ensure that the product meets industry requirements.
Is it difficult to maintain and repair aviation PCBs?
Maintenance and repair of aviation PCBs is relatively complex because aircraft electronic equipment is often installed in difficult working environments, such as inside the aircraft fuselage. Therefore, when designing aviation PCBs, it is necessary to consider the convenience of maintenance and repair, and try to adopt a modular design to facilitate replacement and repair.
What are the environmental protection requirements for aviation PCBs?
The manufacturing and use of aviation PCBs must comply with strict environmental requirements, including the Restriction of Hazardous Substances (RoHS) directive. Manufacturers need to ensure that the materials and processes used do not pollute the environment and do a good job in the processing and recycling of discarded products to reduce negative impacts on the environment.