BGA Cavity Substrate Manufacturer. Embedded slot IC PCB and Embedded BGA cavity PCBs provider. We use advanced cavity PCBs technology to produce High multilayer interconnection cavity substrates from 4 to 30 layers.
In modern PCB assembly, BGA cavity substrates play a vital role, providing reliable support for the mounting and interconnection of electronic components. Particularly suitable for components packaged in ball grid arrays (BGA), BGA cavity substrates play an integral role in electronic devices.
BGA cavity substrate is a variant of PCB (Printed Circuit Board), its main feature is that it has a groove or cavity structure to accommodate chips or other components in the BGA package. These recesses provide a platform into which the chip in the BGA package can be safely and securely embedded and make effective electrical connections to other components.
The design and manufacturing process of these substrates are carefully calculated and strictly controlled to ensure that the size and shape of the grooves perfectly match the requirements of the BGA package. This precise matching ensures that electronic components can be tightly embedded in the substrate while maintaining good electrical connections and thermal management properties.
BGA cavity substrates play a crucial role in modern electronic equipment by serving as a robust foundation for chips and vital components. Whether in consumer electronics, communication devices, or industrial control systems, these substrates are integral to ensuring device reliability and optimal performance. Beyond being a significant component in PCB assembly, BGA cavity substrates represent an essential key technology in contemporary electronic devices. Their presence provides electronic engineers with a dependable platform, empowering them to design more intricate and powerful electronic products.
What are the types and variations of BGA cavity substrates?
BGA cavity substrates play a vital role in the electronics industry, and the diversity of their types and variants directly affects the performance and applicable scenarios of circuit boards. The design of these substrates not only includes variations in cavity depth, diameter, and layout, but also takes into account specialized variants for specific application needs, such as thermal management and signal integrity enhancement. The main types and variations of BGA cavity substrates will be discussed in depth below.
One of the first variations of BGA cavity substrates is sized for the depth and diameter of the cavity. Different application scenarios may require different sized cavities to accommodate different sizes and types of chips or components. For example, in high-density integrated circuit (HDI) designs, shallower but dense cavities may be more common, while in applications requiring large components or specific thermal requirements, deeper cavities may be selected.
The layout of the BGA cavity substrate can also vary based on specific application requirements. Layout involves factors such as the distance between cavities, their arrangement, and their relative position to other circuit components. A carefully designed layout can maximize signal transmission paths and improve circuit performance and reliability.
For specific application requirements, BGA cavity substrates may also have specialized variants. For example, in high-power electronics, thermal management is a key consideration. In response to this demand, a BGA cavity substrate with enhanced heat dissipation performance may be designed, such as using higher thermal conductivity materials or special heat dissipation structures. Likewise, for applications with strict signal integrity requirements, specially designed BGA cavity substrates may be used to reduce signal interference and loss.
Finally, as different industries and application scenarios continue to pursue the performance and functionality of electronic products, the demand for customization of BGA cavity substrates is also increasing. In response to the needs of specific industries or application fields, BGA cavity substrates with special functions or characteristics may be customized and developed to meet the individual needs of customers.
Overall, the types and variants of BGA cavity substrates play a vital role in meeting different application needs and industry standards. Through flexible design and manufacturing, these substrates can achieve diverse configurations, providing broad possibilities for the development and application of various electronic products.
What are the advantages of BGA cavity substrates?
As a key component in the field of modern electronic design and manufacturing, BGA cavity substrates (Ball Grid Array Cavity Substrates) provide multiple advantages and provide strong support for the excellent performance and reliability of electronic assembly. The following are the main advantages of BGA cavity substrates:
The design of a BGA (Ball Grid Array) cavity substrate enhances heat dissipation by efficiently conducting and dispersing heat to the substrate surface. The cavity structure facilitates faster transfer of heat to the heat dissipation layer or device surrounding the substrate, resulting in lower operating temperatures for components and increased system stability and reliability.
Additionally, the cavity structure plays a crucial role in reducing the propagation path of electrical signals within the substrate. This effectively minimizes crosstalk and mutual interference between signal lines, improving the circuit’s signal integrity and anti-interference capabilities. This advantage ensures the stability of electronic assemblies operating at high speeds and frequencies.
The design of the BGA cavity substrate provides a stronger and more stable foundation, which can effectively reduce the impact of mechanical stress on electronic assembly during transportation, installation and use. This mechanical stability helps reduce mechanical mismatch and displacement between components, thereby improving assembly reliability and durability.
Due to the design of the cavity structure, the BGA cavity substrate can achieve higher integration and more compact layout. This miniaturization capability enables electronic assembly to achieve more functions and higher performance in a smaller space, meeting the continuous pursuit of size and weight of modern electronic products, while improving the market competitiveness of products.
In summary, the BGA cavity substrate serves as a dependable foundation for electronic assembly, offering benefits such as enhanced thermal dissipation, minimized electrical parasitic effects, heightened mechanical stability, and the ability for miniaturization. These advantages not only enhance the performance and reliability of assemblies but also align with the requirements of contemporary electronic products for elevated performance and dependability. This, in turn, fosters the ongoing development and innovation of electronic technology.
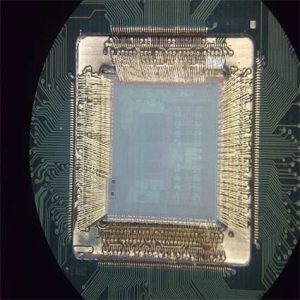
BGA Cavity Substrate
What is the manufacturing process of BGA cavity substrate?
The manufacturing process of BGA cavity substrates involves a complex series of process steps designed to ensure the high quality and precision of the substrates. Here are the key steps and techniques involved:
Precision machining technology plays a vital role when manufacturing BGA cavity substrates. These include:
The process of CNC milling and drilling involves the use of advanced machines to accurately shape the substrate according to design specifications, creating cavities and holes. Laser ablation utilizes laser technology to precisely generate fine feature patterns on the substrate, ensuring accurate positioning and component connection.
To enhance substrate insulation and signal integrity, dielectric materials are deposited and processed. Thin film deposition technology is employed to create an insulating layer on the substrate, protecting circuit components from external factors. Controlled impedance manufacturing processes ensure stable impedance characteristics in high-frequency environments, thereby improving signal transmission reliability.
For circuit interconnection and electrical signal transmission, the substrate’s surface is metallized. This involves the formation of a conductive metal layer through chemical plating and electrolytic plating technologies. Surface treatment options, such as solder shields and treatments enhancing metal adhesion, are utilized to improve substrate solderability and connection reliability.
The above steps and technologies together form a key link in the BGA cavity substrate manufacturing process. Through precision machining, material processing and metallization, the high quality and performance stability of the substrate are ensured.
What are the applications of BGA cavity substrates?
BGA cavity substrates find extensive applications across various industries due to their superior performance and versatile design. In the telecommunications sector, these substrates are commonly employed in network equipment, communication base stations, and high-performance routers and switches within data centers. Their high-density layout and effective thermal management features make them well-suited for addressing the demands of high-speed data transmission and processing, ensuring the stability and reliability of communication networks.
Automotive electronics is another important area in which BGA cavity substrates play an important role. In modern cars, more and more electronic devices are used in vehicle control, infotainment, driver assistance and safety systems, and BGA cavity substrates can provide stable electrical connections and efficient thermal management to meet the needs of on-board electronic systems requirements for performance and reliability.
BGA cavity substrates find extensive application in critical aerospace equipment such as flight control systems, navigation systems, communication systems, and radar systems due to their lightweight design and high reliability. Their ability to withstand extreme environmental conditions makes them ideal for aerospace electronics.
In the realm of medical equipment, BGA cavity substrates are utilized in diverse diagnostic, monitoring, and treatment devices, including medical imaging equipment, pacemakers, ventilators, and surgical navigation systems.
Continuous innovation and optimization in BGA cavity substrate technology are anticipated to bring new vitality to technological development across various industries, fostering advanced and sustainable progress in the entire electronics industry.
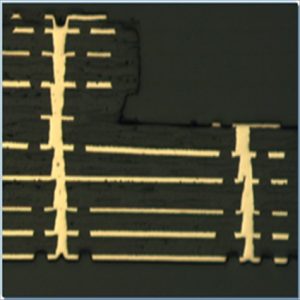
BGA Cavity Substrate
Where can I find BGA cavity substrates?
In the domain of BGA cavity substrates, it is crucial to choose a reliable manufacturer and distributor. As a dedicated supplier, our focus is on providing outstanding products and services that adhere to the most rigorous industry standards.
Within the BGA cavity substrate domain, there exist renowned manufacturers and distributors acclaimed for their expertise and innovation. These entities offer top-notch products and solutions derived from years of experience and technological advancements.
To meet your BGA cavity substrate requirements, we recommend opting for manufacturers with extensive experience and advanced production capabilities. Such manufacturers can tailor high-quality substrates to your specific needs, ensuring compliance with industry standards and quality benchmarks.
Selecting a distributor renowned for their outstanding reputation and top-notch service is a wise choice. These distributors not only offer prompt technical support and post-sales assistance but also play a crucial role in addressing various technical and application challenges.
As your reliable supplier for BGA cavity substrates, we are committed to delivering high-quality products and comprehensive services. With advanced production tools and skilled technical teams at our disposal, we can meet a wide range of customer requirements while maintaining strict standards for quality and delivery timelines.
Whether you are in need of a customized BGA cavity substrate or prefer adhering to standard specifications, we can provide a satisfactory solution. Feel free to contact us anytime to explore our products and services—we look forward to the opportunity to collaborate with you for a brighter future!
Quotation of BGA cavity substrate
When choosing a BGA cavity substrate, it is critical to understand the price factor. This article will explore the key factors that influence BGA cavity substrate quotes and provide some insight into cost considerations.
The cost estimate for a BGA (Ball Grid Array) cavity substrate is influenced by factors such as the cavity design (including depth, diameter, and layout), material selection, and manufacturing processes. More intricate designs may lead to higher manufacturing costs. The choice of substrate material, with high-performance options increasing costs compared to more economical alternatives like FR-4, is a crucial factor in the quotation. Additionally, the manufacturing process employed, whether it involves advanced techniques such as precision machining, metallization, and surface treatments, can impact costs, while simultaneously enhancing substrate quality and performance.
Quantity and lead time: Order quantity and lead time will also have an impact on the quote. Generally speaking, large quantity orders will get better prices, while urgent delivery may incur additional charges.
Supplier Selection: Quotations from different suppliers may vary. Choosing a supplier with a good reputation and rich expertise can ensure the quality and stability of the substrate, but it may affect the quotation accordingly.
Customized requirements: If a customized design or special requirements are required, such as special impedance control or specific surface treatment, it may increase the manufacturing cost and thus affect the quotation.
Cost considerations: When considering a quote for a BGA cavity substrate, in addition to direct costs, potential indirect costs should also be considered, such as repair and delay costs that may result from quality issues. Taking price and quality into consideration, choosing the best supplier that meets your needs is a wise choice.
By understanding these key factors and cost considerations, you can better evaluate BGA cavity substrate quotes and make informed decisions that fit your project needs and budget.
BGA cavity substrate FAQS
Can BGA Cavity Substrates be customized for specific project requirements?
Yes, BGA Cavity Substrates are highly customizable to meet specific project needs. Manufacturers often offer tailored solutions, allowing for variations in cavity dimensions, materials, and configurations to accommodate diverse application requirements.
How does the manufacturing process of BGA Cavity Substrates differ from traditional PCBs?
The manufacturing process involves precision machining, dielectric material deposition, and metallization techniques. CNC milling and drilling are employed for cavity formation, and advanced thin-film deposition methods ensure the creation of reliable insulating layers. Electroless and electrolytic plating contribute to metallization, distinguishing the process from traditional PCB manufacturing.
Can BGA Cavity Substrates be customized to specific requirements?
Yes, BGA Cavity Substrates can be customized to meet specific design and application requirements. Design modifications may include cavity dimensions, layout optimization for signal integrity, thermal vias placement, and selection of substrate materials tailored to environmental conditions and performance objectives.
How do BGA Cavity Substrates impact signal integrity in high-speed electronic devices?
The design of BGA Cavity Substrates minimizes signal losses and distortions, making them well-suited for high-speed electronic devices. The controlled impedance fabrication processes contribute to maintaining signal integrity, crucial for applications requiring precise and fast data transmission.
What factors influence the cost of BGA Cavity Substrates?
The cost of BGA Cavity Substrates is influenced by factors such as substrate material, cavity specifications, production volumes, and additional features. Understanding these factors helps in obtaining accurate quotes and ensuring cost-effectiveness for specific projects. In conclusion, BGA Cavity Substrates offer a sophisticated solution in PCB engineering, addressing various challenges and unlocking new possibilities for electronic design.
The FAQs above aim to provide clarity and insights into the diverse aspects of BGA Cavity Substrates, empowering professionals to make informed decisions in their projects.