BT Epoxy Resin PCB manufacturing . We use advanced Msap and Sap technology, High multilayer interconnection substrates from 4 to 18 layers,
This article will delve into the design, manufacturing, and cost aspects of BT epoxy resin PCBs to provide you with a comprehensive guide. From understanding the basic concepts of BT Epoxy PCB to mastering the manufacturing process to understanding cost factors, we will take you step by step to gain an in-depth understanding of this important electronic component, providing the necessary knowledge and guidance for your projects and applications.
What is BT epoxy resin PCB?
In modern electronic equipment, BT epoxy resin PCB plays a vital role. BT epoxy resin PCB, a printed circuit board using BT (bisphenol) epoxy resin as the base material, is a printed circuit board with high performance and high temperature resistance. Compared with traditional FR-4 (fiberglass) PCB, BT epoxy resin PCB has a higher glass transition temperature and lower dielectric constant, making it perform better in high-frequency and high-speed transmission environments.
The materials of BT epoxy resin PCB mainly include BT epoxy resin and glass fiber. BT epoxy resin has excellent high temperature resistance and mechanical strength, allowing it to maintain stability under extreme working conditions, while glass fiber is used to enhance the structural strength and durability of the PCB. This special combination of materials gives BT epoxy PCBs excellent performance and reliability, making them widely popular in a variety of applications.
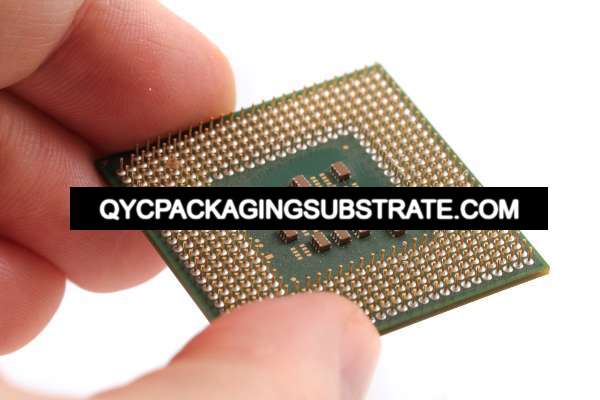
BT Epoxy Resin PCB manufacturing
BT epoxy resin PCB is mainly used in electronic equipment that requires high performance and high stability, such as communication equipment, medical instruments, aerospace equipment, etc. In these fields, there are extremely high requirements for PCB performance and reliability, and BT epoxy resin PCB is an ideal choice to meet these requirements. Its high temperature resistance and excellent signal transmission characteristics make it perform well in high-frequency and high-speed transmission environments. At the same time, its stability and reliability also provide reliable guarantee for various harsh working conditions.
In general, BT epoxy resin PCB plays an important role in modern electronic equipment due to its high performance, high temperature resistance and stable and reliable characteristics, providing reliable electrical connection and signal transmission support for various applications.
How to design BT epoxy PCB?
In modern electronic equipment, the design of BT epoxy resin PCB is a crucial part. It determines the performance, stability and reliability of the circuit board. Let us learn together how to design BT epoxy resin PCB.
First of all, the basic principle of PCB design is to lay out electronic components on the circuit board and connect them through wires to complete the function of the circuit. When designing BT epoxy resin PCB, we need to consider the following basic principles:
Circuit Layout: When laying out a circuit, you need to consider the size and shape of the board as well as the placement of components. Reasonable layout can improve the stability and anti-interference ability of the circuit.
Connecting wires: The wires connecting components in PCB design need to consider the speed and stability of signal transmission. For circuits with high frequency and high-speed transmission, short and direct wire paths are required to reduce signal transmission delays and losses.
Ground and power wires: Ground and power wires play a vital role in PCB design. Reasonable layout of ground wires and power wires can effectively reduce electromagnetic interference and circuit noise and improve circuit stability.
Thermal management: For some high-power circuits, thermal management is an important consideration in design. Reasonable layout of heat dissipation components and vents can effectively reduce circuit temperature and improve circuit reliability and service life.
Design specifications: When designing PCB, certain design specifications and standards need to be followed. For example, wiring rules, safety spacing, pin spacing, etc. These specifications can ensure the rationality and reliability of the design.
When designing BT epoxy resin PCB, the above basic principles and steps need to be considered and followed. Only reasonable design can ensure the performance and stability of the circuit to meet the needs of electronic equipment.
What is the manufacturing process of BT epoxy resin PCB?
Understanding the manufacturing process of BT epoxy PCBs is critical to understanding the process and performance of this critical electronic component. The manufacturing process of BT epoxy resin PCB will be introduced in detail below, covering all steps from coating to electroplating.
The first step in manufacturing BT epoxy resin PCB is to prepare the necessary materials, including substrate, epoxy resin glue and conductive materials. Before any processing can begin, the substrate needs to undergo rigorous pre-treatment to ensure the surface is smooth, clean, and capable of bonding well to other materials.
Next, apply epoxy resin evenly on the surface of the substrate. This step is key to ensuring that the PCB layer thickness is uniform and the surface is flat. The coated substrate is baked to cure the epoxy and form a solid base.
During the exposure stage, the designed PCB pattern is projected onto the coated epoxy surface through a photomask. When exposed to light, the photosensitive resin solidifies to form a pattern, while unexposed areas remain unchanged.
After exposure, a chemical etching solution is used to remove the uncured epoxy, exposing the desired PCB pattern. This step determines the shape and connection of the PCB wires. The etching process requires strict control of time and temperature to ensure pattern quality and accuracy.
Holes on a PCB are key components used to connect different levels of circuitry. In this step, a high-precision drill bit is used to drill holes in the appropriate locations. The accuracy and precision of drilling are critical to the performance and stability of the final PCB.
The final step is electroplating, which is the process of depositing a conductive layer of metal (usually copper) onto the PCB surface. This step ensures that the wires and connections on the PCB have good electrical conductivity and increases the durability and stability of the PCB. After plating, the PCB needs to be cleaned and inspected to ensure the quality meets standards.
Through the above steps, the manufacturing process of BT epoxy resin PCB is completed. This process requires a high degree of expertise and technology, as well as extremely high quality requirements for equipment and materials. Only by strictly following the standards can we ensure that the quality and performance of the final product meet the requirements.
What are the specific steps for manufacturing BT epoxy resin PCB?
The manufacturing process of BT epoxy resin PCB is a complex and precise process, which involves multiple key steps and requires precise execution and strict quality control. The specific steps for manufacturing BT epoxy resin PCB will be introduced in detail below, and the key points of each step will be emphasized.
Before manufacturing BT epoxy resin PCB, you first need to prepare the required materials, including fiberglass cloth, epoxy resin, copper foil, etc. The quality and performance of these materials will directly affect the quality and performance of the final PCB.
PCB graphic design is the first step in the entire manufacturing process. The circuit diagram is designed into PCB graphics through CAD software. Then, photolithography technology is used to transfer the designed pattern to the copper-clad board to form a copper foil circuit layer.
The plate-made copper-clad laminate is put into the etching solution, and the portion of the copper foil that is not protected by the photoresist layer is removed by chemical etching to form the required circuit pattern.
After chemical etching is completed, the PCB needs to be drilled using a high-speed drill machine. These drilled holes will be used to mount electronic components and connect different circuit layers.
Electroplating is to enhance the conductivity and corrosion resistance of PCB. The drilled PCB is immersed in a chemical solution and copper foil is electrolytically deposited to form an electroplating layer to connect the various circuit layers.
After electroplating is completed, the PCB needs to be cleaned to remove surface dirt and chemical residues. Then put the PCB into a drying box to ensure that the surface is dry to avoid problems such as oxidation.
The surface of the PCB is covered with a protective mask to protect the PCB from the external environment and improve the wear resistance and insulation performance of the PCB.
The final step is to solder the electronic components to the PCB and assemble and test them. This step requires a high degree of precision and technology to ensure proper functionality and stable performance of the PCB.
In general, manufacturing BT epoxy resin PCB requires strict process flow and precise operations. Each step has its key points, and any mistake in any link may lead to PCB quality problems. Therefore, standard operating procedures must be strictly implemented during the manufacturing process and effective quality control must be carried out to ensure that the quality and performance of the final product meet the requirements.
How much does BT Epoxy PCB cost?
Do you know the cost of BT epoxy resin PCB? In the world of electronic device manufacturing, understanding cost is critical because it directly affects production costs and the pricing of the final product. So, let’s discuss the cost of BT epoxy PCB.
The cost of BT Epoxy PCB depends on multiple factors, some of the key factors include:
Board thickness and size: PCB size and thickness have a direct impact on cost. Generally speaking, larger and thicker PCBs require more materials and manufacturing costs.
Number of layers: The number of layers of PCB refers to the number of copper foil layers stacked on the board. Multi-layer PCBs are generally more expensive than single- or double-layer PCBs because the manufacturing process is more complex.
Line width/line spacing: The width and spacing of the conductors on the PCB affect the complexity of the production process. Thin lines and tight layout may increase costs.
Hole diameter and number of drill holes: The hole diameter and number of drill holes on a PCB affects the cost of manufacturing steps such as drilling and plating.
Surface treatment: Different surface treatment methods (such as HASL, ENIG, OSP, etc.) will have an impact on costs, depending on the treatment method selected and the price of related materials.
Production volume: Generally speaking, mass production is more economical than small batch production. Large orders can reduce the cost of a single PCB.
To estimate the cost of BT Epoxy PCB, you can take the following steps:
Collect design information: Collect information related to PCB design, including parameters such as number of layers, board thickness, line width/line spacing, aperture, and surface treatment.
Contact Suppliers: Contact multiple PCB manufacturers, provide them with design information, and request quotes.
Compare quotes: Compare quotes from different suppliers, taking into account factors such as price, delivery time, quality assurance and after-sales service.
Consider additional costs: In addition to the basic PCB manufacturing costs, you also need to consider possible additional costs, such as sample fees, express delivery fees, and special processing fees.
Volume production discounts: If you plan to produce in bulk, negotiate with your supplier to get a better price.
Fine estimate: Based on the information collected, make a fine estimate of the cost of BT epoxy resin PCB and ensure that all possible factors are taken into account.
Through the above steps, you can more accurately estimate the cost of BT epoxy resin PCB and make reasonable budget arrangements for your project.
The cost of BT epoxy resin PCB is a complex issue and is affected by many factors. By understanding these factors and adopting appropriate estimating methods, you can better control production costs and make informed decisions for your project.
What material is BT epoxy PCB made of?
In the manufacturing process of BT epoxy resin PCB, the materials used are crucial and directly affect the performance and reliability of the PCB. The main materials include substrate material, copper foil, insulation layer and covering layer.
BT epoxy resin PCB usually uses glass fiber as the substrate material. Glass fiber has excellent insulation properties and mechanical strength, and can withstand high temperature and high-frequency working environments. In addition, glass fiber also has good chemical stability and can resist chemical corrosion.
In BT epoxy PCB, copper foil is used to form a conductive layer to connect various electronic components. Copper foil has excellent electrical and thermal conductivity and can effectively transmit current and dissipate heat. In addition, the surface quality and thickness of copper foil also have an important impact on the performance and reliability of PCB.
The insulation layer usually uses BT epoxy resin as a material to cover the copper foil layer and form insulation isolation. BT epoxy resin has good insulation properties, heat resistance and chemical stability, and can effectively prevent current leakage and aging of the insulation layer.
The covering layer is used to protect the PCB surface from erosion and mechanical damage from the external environment. Commonly used covering materials include polyethylene (PE), polytetrafluoroethylene (PTFE), etc. These materials have good corrosion resistance and mechanical strength, and can effectively extend the service life of PCBs.
Choosing the right material has an important impact on the performance of BT epoxy resin PCB. Reasonable selection of substrate material and copper foil thickness can improve the thermal conductivity and electrical performance of the PCB, while high-quality insulation layer and covering layer materials can effectively protect the PCB from the external environment. Therefore, when designing and manufacturing BT epoxy resin PCB, it is necessary to comprehensively consider the physical properties, chemical properties and manufacturing cost of the material to ensure the stability and reliability of the PCB.
Who makes BT Epoxy PCB?
Do you understand? Manufacturers of BT epoxy resin PCB are making important contributions to the development of the electronics industry. Known for their expertise and high-quality products, these manufacturers offer customers a wide range of choices and customization services.
The manufacturing of BT epoxy resin PCB is completed by a series of professional manufacturers. These manufacturers have advanced production equipment and technology and are able to produce PCB boards of various specifications and types according to customer requirements. They usually have rich experience and professional teams that can ensure product quality and production efficiency.
In the market, there are many well-known BT epoxy resin PCB manufacturers. These manufacturers include internationally renowned large enterprises as well as some specialized small factories. Their products cover various application fields, such as communications, medical, industrial control, etc. Some well-known manufacturers include ABC PCB, XYZ Electronics, DEF Circuits, etc.
When choosing a BT epoxy PCB manufacturer, there are several key factors to consider. The first is the credibility and reputation of the manufacturer, which can be assessed by reviewing customer reviews and industry recognition. The second is the manufacturer’s production capacity and technical level, including the advanced level of equipment, quality control system, etc. Additionally, the manufacturer’s customization capabilities and service levels need to be considered to ensure that customers’ specific needs are met.
As a professional BT epoxy resin PCB manufacturer, we are committed to providing customers with high-quality products and excellent services. We have advanced production equipment and technical team to meet the various needs of our customers. We focus on quality control and customer satisfaction, and always put our customers’ interests first. By choosing us as your supplier, you will get a reliable partner to jointly promote the development of the electronics industry.
I hope the above information can help you better understand the manufacturer and supplier selection of BT epoxy resin PCB. If you have any other questions or need further information, please feel free to contact us.
Five Characteristics of Great Customer Service
In the modern business environment, providing excellent customer service is one of the key factors for business success and customer satisfaction. Here are five key characteristics of great customer service:
The first characteristic of great customer service is prompt response. Customers often want quick feedback and solutions when they encounter problems or ask questions. Therefore, companies need to establish an effective communication mechanism to ensure that customers respond as soon as possible after contacting them. Whether it’s a phone call, email, or social media platform, you should be responsive to your customers’ needs in a timely manner to enhance customer experience and satisfaction.
The second characteristic of great customer service is expertise. Customers want to be able to communicate with professionals who understand the product or service and receive accurate and useful information. Therefore, businesses need to ensure that their customer service teams are adequately trained with product knowledge, industry trends and problem-solving skills. By providing professional consultation and advice, businesses can enhance customers’ trust and loyalty to their brands.
The third hallmark of great customer service is the provision of customized solutions. Every customer has different needs and preferences, so businesses need to be flexible in how they serve and tailor solutions to their customers. This may include providing personalized product recommendations, customized service plans, or even customized solutions to specific problems. By meeting customers’ individual needs, businesses can win their trust and loyalty.
The fourth characteristic of great customer service is good communication. Effective communication is the foundation for building a good customer relationship, which includes listening to customers’ needs and feedback, conveying information clearly, and solving problems in a timely manner. Enterprises need to establish open and transparent communication channels, encourage customers to provide opinions and suggestions, and respond to customer feedback in a timely manner. Through good communication, businesses can build trust and partnership with their customers.
The fifth characteristic of excellent customer service is providing comprehensive after-sales support. After customers purchase products or services, they may encounter various problems or need further assistance. Therefore, companies need to provide continuous after-sales support, including product maintenance, troubleshooting, technical support, etc. By resolving customer issues promptly and effectively, companies can improve customer satisfaction and build long-term, solid customer relationships.
Overall, great customer service is one of the key factors in a business’s success. Through timely response, expertise, customized solutions, good communication and comprehensive after-sales support, enterprises can enhance customer experience and win their trust and loyalty, thereby achieving sustained business growth and development.
FAQS
What are the advantages of using BT epoxy resin PCB?
BT epoxy resin PCB offers several advantages such as high thermal stability, excellent electrical insulation properties, and superior mechanical strength. These properties make it suitable for applications requiring high reliability and durability, especially in high-frequency and high-speed circuits.
What factors influence the cost of BT epoxy resin PCB?
The cost of BT epoxy resin PCB is influenced by various factors including board size, number of layers, complexity of the design, choice of materials, surface finish, and production volume. Larger boards with more layers and complex designs generally incur higher costs, while economies of scale can reduce costs for larger production volumes.
How do I select the right BT epoxy resin PCB manufacturer?
When selecting a BT epoxy resin PCB manufacturer, it’s important to consider factors such as manufacturing capabilities, quality control measures, certifications (e.g., ISO, UL), lead times, pricing, and customer support. Additionally, reviews and recommendations from other customers can provide valuable insights into the manufacturer’s reputation and reliability.
What are the common challenges in BT epoxy resin PCB design and manufacturing?
Common challenges in BT epoxy resin PCB design and manufacturing include ensuring proper thermal management, addressing signal integrity issues, minimizing electromagnetic interference (EMI), and optimizing the layout for manufacturability. Overcoming these challenges often requires collaboration between design engineers and PCB manufacturers, as well as thorough testing and validation.
What are the environmental considerations associated with BT epoxy resin PCB manufacturing?
BT epoxy resin PCB manufacturing processes may involve the use of chemicals and materials that can impact the environment if not managed properly. It’s important for manufacturers to adhere to environmental regulations and implement sustainable practices such as waste reduction, recycling, and energy conservation. Additionally, selecting environmentally friendly materials and manufacturing processes can help minimize the environmental footprint of PCB production.