Bt laminate PCB manufacturing. the Package Substrate will be made with Showa Denko and Ajinomoto High speed materials.or other types high speed.
BT laminate PCB is a common printed circuit board made of polybutylene terephthalate (PBT) as the base material. It has excellent electrical properties and mechanical strength and is often used in high-frequency and high-speed circuit design. In the manufacturing process of BT laminate PCB, it is necessary to go through key steps such as material preparation, pattern imaging, photolithography, etching, lamination, drilling, electroplating and surface treatment. The cost of manufacturing a BT laminate PCB depends on several factors, including size, number of layers, materials, and production volume. Choosing the right manufacturer and materials is key to ensuring product quality and cost control.
What is BT laminate PCB?
BT laminate PCB is a printed circuit board that uses polybutylene terephthalate (PBT) as the base material. It has excellent electrical properties and mechanical strength and is suitable for various application scenarios, especially high-frequency and high-speed circuits. In the electronics industry, BT laminate PCB plays a vital role. First, it provides a stable and reliable circuit connection to ensure the normal operation of electronic equipment. Whether it is a mobile phone, computer, or industrial control system, reliable circuit boards are needed to support their complex functions. Secondly, BT laminate PCB has high heat resistance and mechanical strength, and can withstand high temperature environments and complex working conditions. This allows it to perform well in various harsh environments, such as automotive electronics, aerospace and other fields. In addition, BT laminate PCB also has better flame retardant properties and can provide higher safety. Today, as the electronics industry increasingly pursues high performance and high security, the importance of BT laminate PCB is self-evident. It is not only a core component of electronic products, but also one of the indispensable key technologies in various fields of modern society.
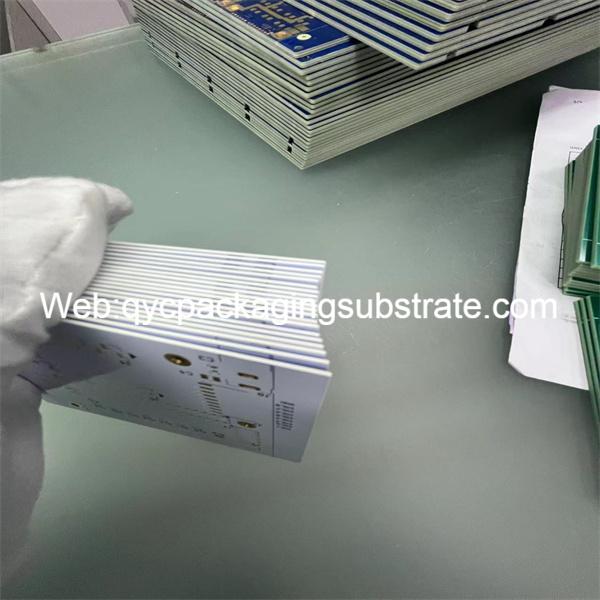
Bt laminate PCB manufacturing
How to design BT laminate PCB?
When designing a BT laminate PCB, a series of carefully planned steps are required to ensure that the final board meets the expected functional and performance requirements. The key steps and considerations for designing BT laminate PCB will be introduced in detail below:
At the beginning of the design, the functional and performance requirements of the board need to be clearly defined. This includes determining the board’s purpose, required functionality, operating environment conditions, etc. A clear definition of requirements helps guide subsequent design work and ensures that the final product meets customer expectations.
Drawing the circuit schematic is the first step in designing a BT laminate PCB. In the schematic diagram, the circuit functions need to be broken down into individual modules and the types, values, and connections of the components must be determined. Schematic design is the basis for subsequent layout and wiring work, so it is necessary to ensure the accuracy and completeness of the schematic.
After completing the schematic design, the circuit needs to be converted into a PCB layout. This involves placing components on a circuit board and connecting them to form a complete circuit. During the layout design process, factors such as the spacing between components, the length of the signal lines, and the feasibility of wiring need to be taken into consideration to ensure that the circuit board has good electrical performance and stability.
After completing the layout design, signal integrity analysis needs to be performed. This involves using simulation tools and techniques to evaluate the transmission performance of the signal on the circuit board, including signal delay, interference and loss. Through signal integrity analysis, layout and routing can be optimized to improve circuit performance and stability.
Routing is one of the key steps in designing a BT laminate PCB. During the wiring process, the various components in the circuit need to be connected and the signal path optimized to minimize signal interference and loss. The quality of wiring directly affects the performance and stability of the circuit, so careful wiring planning and optimization is required.
Throughout the design process, other factors need to be considered, such as PCB size, number of layers, thermal design, EMI/EMC, etc. Taking these factors into consideration and using appropriate tools and techniques can help designers effectively design high-performance and stable BT laminate PCBs.
What is the manufacturing process of BT laminate PCB?
Are you curious about how BT laminate PCB is manufactured? Below we will introduce the key steps in the manufacturing process from raw materials to final products, giving you a clearer understanding of the entire process.
Material Preparation: The first step in manufacturing a BT laminate PCB is to prepare the required materials. This includes BT laminate materials and copper foil. BT laminate materials are typically base materials composed of polybutylene terephthalate (PBT). Copper foil is used as the conductive layer of PCB.
Graphical imaging: Next, convert the PCB design into a graphic image file. These files will be used in subsequent manufacturing steps such as photolithography and etching.
Lithography: In the photolithography step, a graphic image is transferred to a photoresist using photolithography techniques. Photoresist protects areas that do not need to be etched.
Etching: Etching is the process of removing portions of copper foil that are not protected by photoresist. This creates the desired circuit pattern.
Lamination: In the lamination step, multiple layers of PCB are stacked together and held together by heat pressing. This ensures a good connection between the layers.
Drilling: The purpose of drilling holes in a PCB is to mount components and connect circuits between different layers. These holes must be precisely located and sized.
Electroplating: Increase the electrical conductivity of PCB through the electroplating process. This involves plating a layer of metal, usually copper, on the PCB surface and hole walls.
Surface Treatment: Finally, surface treatment is performed to improve welding performance and corrosion resistance. This includes coating the PCB surface with a protective material such as solder film or spray coating.
These above steps together constitute the manufacturing process of BT laminate PCB. Every step is critical, and problems at any step may affect the quality and performance of the final product. Through strict quality control and meticulous operations, we can ensure the production of BT laminate PCB products that meet the requirements.
How much does it cost to manufacture a BT laminate PCB?
The cost of manufacturing BT laminate PCB is determined by multiple factors, including board material cost, processing fees, labor costs, and other additional costs. The interaction between these factors determines the final manufacturing cost.
First of all, board material cost is an important factor affecting the manufacturing cost of BT laminate PCB. BT laminate PCB usually uses polybutylene terephthalate (PBT) as the base material and copper foil as the conductive layer. The quality and thickness of the material will directly affect the cost, and high-quality boards usually have higher prices.
Secondly, processing costs are also an important part of manufacturing costs. Processing costs include photolithography, etching, lamination, drilling, electroplating and other links. Among them, lamination and drilling are the more expensive links because they require high temperature and pressure or precision processing equipment to complete.
In addition, labor costs are also a part of manufacturing costs that cannot be ignored. Including the wages of operating workers, technicians and managers, labor costs will fluctuate with changes in the labor market, directly affecting the level of manufacturing costs.
In addition to the above direct costs, there are also some other additional costs, such as equipment maintenance costs, environmental protection costs, transportation costs, etc. Although these costs are not large individually, they will have a certain impact on manufacturing costs when added up.
To reduce the manufacturing cost of BT laminate PCB, there are some effective methods that can be adopted. The first is to optimize the design to minimize the waste of plates and the complexity of processing, thereby reducing material and processing costs. The second is to improve production efficiency and reduce labor costs and processing time through automated equipment and process improvements. In addition, rational selection of suppliers and materials, cost control and negotiation are also important means to reduce manufacturing costs.
To sum up, the cost of manufacturing BT laminate PCB is affected by multiple factors. It is necessary to comprehensively consider the costs of each link and take effective measures to reduce costs and improve competitiveness.
What material is BT laminate PCB made of?
BT laminate PCB is usually composed of a variety of materials, the most important of which are polybutylene terephthalate (PBT) as the base material and copper foil as the conductive layer. In addition, there are filling materials, covering layers and surface treatment materials.
As the base material of BT laminate PCB, PBT has many excellent properties. First of all, it has good mechanical strength and stability, allowing PCB to maintain stable performance in various application environments. Secondly, PBT has high heat resistance and can operate at relatively high temperatures without failure. In addition, PBT also has good chemical resistance and can resist the erosion of many chemical substances, ensuring the long-term reliability of PCB. As a conductive layer, copper foil provides the basis for circuit connection. It has good conductivity and processability and is suitable for the needs of various electronic circuits.
There are several factors to consider when choosing the right material for your project. First, it is necessary to select an appropriate substrate based on the performance requirements and application scenarios of the circuit. If you need to operate in a high temperature environment, you need to choose a material with higher heat resistance; if you need to use it in a harsh chemical environment, you need to choose a material with good chemical resistance. Secondly, the cost and availability of materials need to be considered to ensure the economics and feasibility of the project. In addition, the manufacturing process and technical requirements also need to be considered and materials that match them need to be selected.
To sum up, BT laminate PCB is usually made of materials such as PBT and copper foil, and has good mechanical strength, stability and heat resistance. When selecting materials, comprehensive considerations need to be based on the project’s performance requirements, cost, manufacturing process and other factors to ensure that the PCB can achieve the expected results during use.
Who makes BT laminate PCBs?
When choosing a supplier to manufacture BT laminate PCBs, it is important to find a reliable partner that can provide high-quality products and excellent customer service. In this regard, our company offers you the perfect solution.
Our company is a professional PCB manufacturer with many years of industry experience and rich technical knowledge. We are committed to providing the best quality BT Laminate PCB to our customers and ensuring that their specific needs and requirements are met.
Professional technical team: We have a high-quality technical team that is proficient in PCB manufacturing processes and technologies. Whether it’s design, manufacturing or customer service, we are able to provide our customers with professional support and advice.
Advanced production equipment: We use advanced production equipment and processes to ensure product quality and stability. From material handling to finished product delivery, we strictly control every link to ensure the efficiency and reliability of the production process.
Quality Assurance System: We have established a strict quality management system, and all products undergo strict quality inspection and testing. We are committed to providing products that meet international standards and customer requirements, and provide customers with reliable protection.
Customized service: We are able to customize BT laminate PCBs of various specifications and requirements according to customer needs. Whether it is samples or mass production, we are able to meet our customers’ individual needs.
Excellent customer service: We value our customers’ needs and feedback and always put our customers’ interests first. We provide timely and professional customer service to ensure that customers have a satisfactory experience throughout the entire cooperation process.
Choose our company as your BT laminate PCB manufacturing supplier, you will get high-quality products, excellent services and a reliable partner. We look forward to working with you to develop together and create a better future!
What are the five qualities of great customer service?
In the PCB manufacturing industry, quality customer service is one of the keys to business success. Here are five traits that define good customer service and are critical to customer satisfaction and long-term relationships.
Great customer service starts with proactive communication. Enterprises should proactively communicate with customers and respond to customer needs and questions in a timely manner. This includes understanding customer expectations and providing real-time information on order status, delivery times and technical support. Through timely communication, businesses can build trust and provide the support and information their customers need.
In the PCB manufacturing industry, professional technical support is an important part of providing excellent customer service. Customers may need professional advice on design optimization, material selection, process advice, etc. Therefore, companies should have an experienced team of engineers who can provide customers with professional technical support and solutions. By helping customers solve problems and optimize designs, companies can win their customers’ trust and respect.
Every customer has different needs and requirements, so personalization is key to providing excellent customer service. Enterprises should understand their customers’ business models, project needs and preferences and provide them with customized solutions and services. This may include customized production plans, quality control for special requirements and flexible delivery arrangements. By providing personalized services, businesses can meet customers’ specific needs and build long-term relationships.
During the PCB manufacturing process, problems and challenges are inevitable. Therefore, enterprises need to have the ability to respond and solve problems quickly. When customers encounter problems or have urgent needs, businesses should be able to respond immediately and provide timely solutions. This may involve adjusting production plans, working overtime or providing emergency distribution. By responding and resolving issues quickly, companies can demonstrate their professionalism and responsibility, winning customers’ trust and satisfaction.
Finally, quality customer service requires companies to have continuous improvement and feedback mechanisms in place. Enterprises should constantly seek feedback and suggestions from customers to understand customer satisfaction and changes in needs. At the same time, companies should continue to improve product quality, service levels and production efficiency based on customer feedback and market changes. Through continuous improvement and feedback mechanisms, companies can continuously improve customer service levels, maintain competitive advantages, and achieve long-term development.
Overall, in the PCB manufacturing industry, excellent customer service is one of the key factors for business success. Through proactive communication, professional technical support, personalized services, rapid response and problem-solving capabilities, and continuous improvement and feedback mechanisms, companies can provide excellent customer experience and win customer trust and long-term cooperation.
Frequently Asked Questions
What materials are used in BT laminate PCBs?
BT laminate PCBs primarily consist of a BT resin substrate and copper foil. The BT resin offers excellent thermal stability and mechanical properties, while copper foil serves as the conductive layer for electrical connections.
Who manufactures BT laminate PCBs?
BT laminate PCBs are manufactured by various PCB manufacturers worldwide. These manufacturers specialize in producing high-quality PCBs using advanced fabrication techniques and adhere to industry standards to ensure reliability and performance.
What are the advantages of BT laminate PCBs?
BT laminate PCBs offer several advantages, including high electrical insulation, low dielectric loss, good thermal stability, and excellent dimensional stability. These properties make them ideal for applications requiring high-frequency performance and reliability.
What applications are suitable for BT laminate PCBs?
BT laminate PCBs are commonly used in telecommunications, aerospace, automotive, medical devices, and industrial electronics. They are particularly well-suited for applications requiring high-speed signal transmission and thermal management.