Build A Ceramic Packaging Substrate. Professional Ceramic packaging substrate Supplier, we mainly produce ultra-small bump pitch and ultra-small trace Ceramic Packaging Substrate and Ceramic PCBs.
In the dynamic field of PCB design, Ceramic Packaging Substrate emerges as a vital element, playing a foundational role in the assembly and interconnection of electronic components. This article delves into the characteristics of Ceramic Packaging Substrate and its critical contribution to elevating the performance and dependability of electronic devices.
At the core of PCB design, Ceramic Packaging Substrate assumes a pivotal role, acting as a resilient bridge connecting the semiconductor chip to the broader PCB network. Its primary objective is to enable effective electrical connections among different components within electronic devices, establishing a trustworthy foundation for their optimal functionality.
Analogous to the cornerstone of a building, Ceramic Packaging Substrate provides secure and stable support for electronic components. This not only enables electronic devices to function seamlessly across diverse environmental conditions but also ensures heightened reliability and an extended service life.
The importance of these substrates is manifold. To begin with, Ceramic Packaging Substrate plays a crucial role in establishing reliable connections among electronic components, ensuring the stability and dependability of signal transmission. Additionally, these substrates possess outstanding thermal conductivity properties, efficiently handling the heat produced by electronic devices during operation and preventing potential problems associated with overheating.
Furthermore, Ceramic Packaging Substrate proves adaptable to varying design requirements through its highly customizable features. Whether incorporated into compact consumer electronic devices or intricate industrial applications, these substrates consistently demonstrate outstanding performance, offering designers greater flexibility.
Beyond serving as connectors, the importance of these substrates extends to their contribution to overall system performance. By employing Ceramic Packaging Substrate, electronic designers can realize the development of smaller, higher-performance devices suitable for diverse application scenarios, ultimately delivering an enhanced user experience.
Overall, Ceramic Packaging Substrate is an indispensable element in electronic design. Its key role in PCB is not only reflected in providing reliable electrical connections, but also in its all-round improvement of the performance and reliability of electronic equipment. Through in-depth understanding and application of these substrates, the field of electronic design will usher in a more innovative and reliable future.
What types of Ceramic Packaging Substrate are there?
Ceramic Packaging Substrates are integral components in contemporary PCB engineering, delivering outstanding performance and adaptability. This article delves into the ever-evolving realm of these substrates, examining both conventional and cutting-edge materials.
Traditionally, alumina ceramics have been the preferred option for Ceramic Packaging Substrates. Celebrated for their remarkable thermal conductivity and mechanical strength, alumina ceramics prove to be exceptional in applications demanding heightened reliability and stability. These ceramics offer robust support for electronic components while effectively managing heat dissipation.
This advanced ceramic has become instrumental in expanding the scope of Ceramic Packaging Substrates, finding applications in high-performance electronic equipment where stringent heat dissipation requirements are paramount. As science and technology progress, the adoption of materials like aluminum nitride continues to shape the landscape of Ceramic Packaging Substrates, catering to evolving design needs in electronic manufacturing.
Distinct Thermoelectric Properties:
Each type of Ceramic Packaging Substrate boasts unique thermoelectric properties, playing a pivotal role in setting them apart for various applications. Superior thermal conductivity becomes instrumental in effectively dissipating the heat generated by electronic components, ensuring the stability of equipment during high-load operations.
Different projects and applications place various design requirements on Ceramic Packaging Substrate. From high-density interconnects to stability over specific operating temperature ranges, each type can be customized to project needs, giving designers more options.
Pushing the boundaries of electronic innovation
The diversity of Ceramic Packaging Substrate not only responds to current needs, but also drives the forefront of electronic innovation. By constantly introducing new materials and processes, designers can break through traditional limitations and break technical bottlenecks in various applications.
The extensive range of Ceramic Packaging Substrate options, spanning from conventional to cutting-edge, provides electronic designers with enhanced flexibility and the opportunity for increased creativity. These diverse ceramic substrates not only address the requirements of ongoing projects but also play a pivotal role in propelling the entire field of electronic engineering towards greater sophistication and efficiency.
What are the advantages of Ceramic Packaging Substrate?
In the ever-evolving realm of contemporary electronic design, Ceramic Packaging Substrate has emerged as a central focus in PCB engineering, owing to its exceptional properties that go beyond serving as a mere platform for interconnecting electronic components. This specialized substrate plays a crucial role in elevating the performance and reliability of electronic equipment. Let’s explore three key advantages offered by Ceramic Packaging Substrate.
Superior Thermal Conductivity
A standout characteristic of Ceramic Packaging Substrate is its outstanding thermal conductivity. Particularly, materials like aluminum nitride and aluminum oxide present in ceramics showcase remarkable thermal conductivity properties. This effectively facilitates the efficient transfer and dispersion of heat generated in electronic devices. Such a feature is essential for effectively dissipating heat from high-power electronic components, ensuring that equipment maintains optimal temperature control even during extended operational periods.
High Mechanical Strength
Ceramic Packaging Substrate demonstrates notable mechanical strength, surpassing traditional substrate materials like FR-4. With heightened hardness and strength compared to conventional options, ceramics can withstand greater mechanical stress. This makes Ceramic Packaging Substrate an ideal choice for applications in harsh environments or those subject to frequent vibrations, thereby ensuring the reliability and stability of electronic equipment.
Outstanding Dependability
The exceptional reliability of Ceramic Packaging Substrate is a key attribute that significantly enhances the longevity and efficiency of electronic devices. The inherent stability and corrosion resistance of ceramic materials empower the substrate to sustain optimal performance in various environmental conditions. This remarkable dependability positions Ceramic Packaging Substrate as an ideal choice for a wide range of applications, including challenging environments such as aerospace, medical, and industrial control systems.
These three advantages together make Ceramic Packaging Substrate an ideal choice in electronic design. Its excellent thermal conductivity, high mechanical strength, and excellent reliability provide designers with greater flexibility and reliability, thereby pushing the limits of performance and stability of electronic devices. Whether faced with high power density applications or extreme environmental challenges, Ceramic Packaging Substrate has demonstrated unparalleled advantages and provides electronic engineers with room for innovative design.
Why choose Ceramic Packaging Substrate?
Ceramic Packaging Substrates stand out in the realm of electronic design, surpassing traditional PCBs in various aspects, particularly in thermal management, miniaturization, and compatibility with advanced technologies. One compelling reason to opt for Ceramic Packaging Substrates is their outstanding thermal management capabilities. Leveraging the superb thermal conductivity of ceramic materials, these substrates effectively transfer and dissipate the heat generated by electronic devices. This is a significant advantage over conventional PCB materials, which may struggle in high-temperature settings, leading to potential thermal issues and compromised performance.
Secondly, Ceramic Packaging Substrate shows unique advantages in miniaturization. Ceramic materials allow for a higher density of electrical connections, allowing designers to fit more components into a smaller space. This is crucial as modern electronic devices increasingly pursue thin, light and short sizes, while traditional PCBs may be limited by space constraints.
The Ceramic Packaging Substrate excels in its ability to accommodate cutting-edge technologies. Its material stability and reliability make it an excellent option for seamlessly incorporating advanced technologies like 5G communications and artificial intelligence chips. In contrast, conventional PCBs may encounter difficulties meeting the demands of high frequencies and performance, potentially impacting the overall system’s efficiency.
In some specific situations, Ceramic Packaging Substrate appears to be more competitive. For example, in high-temperature environments, such as automotive electronics and aerospace applications, the stability and thermal management capabilities of ceramic substrates have become irreplaceable advantages. In fields such as medical equipment that require extremely high reliability, Ceramic Packaging Substrate is also capable.
Opting for Ceramic Packaging Substrate over conventional PCBs aligns with the ongoing drive for enhanced performance, compact design, and increased adaptability to advanced technologies in contemporary electronic designs. This shift not only elevates the efficiency and dependability of electronic devices but also propels advancements in electronic engineering, sparking a transformative wave of innovation in both materials and technology.
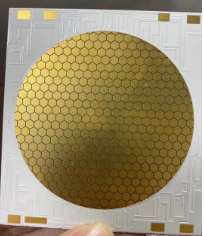
Ceramic Packaging Substrate
How is Ceramic Packaging Substrate made?
Understanding the intricacies of manufacturing Ceramic Packaging Substrates is crucial to unveil the secrets behind their exceptional performance. The journey from motherboard inception to ceramic substrate creation involves a seamless collaboration of key steps, specialized materials, and cutting-edge technologies, ensuring precision and reliability in the final product.
The forefront of manufacturing is occupied by the production of ceramic motherboards, employing advanced technologies and specialized materials to achieve unparalleled results. This involves sophisticated techniques such as high-precision cutting, multi-layer lamination, and micro-circuit production, guaranteeing both structural stability and exceptional electrical performance in the motherboard.
Selecting professional materials, notably high-purity ceramics, is a critical aspect of manufacturing ceramic motherboards to impart excellent thermal conductivity and mechanical strength. Achieving minute structures and high-density connections requires the utilization of state-of-the-art manufacturing processes like laser shaping and chemical etching.
The ceramic substrate, a pivotal component of Ceramic Packaging Substrate, exemplifies the synergistic interplay between technology and materials in its manufacturing process. Leveraging advanced technologies such as laser drilling and thin film deposition is essential to achieve high-density interconnects on ceramic substrates, enhancing both connection performance and substrate compactness.
Key materials like aluminum oxide and aluminum nitride play pivotal roles in the manufacturing of ceramic substrates. While aluminum oxide contributes excellent insulation properties, aluminum nitride enhances thermal conductivity. Together, these materials ensure the substrate can operate stably and reliably in diverse working environments.
The intricacy and sophistication of these manufacturing processes enable Ceramic Packaging Substrate to realize its full potential in modern electronic designs. The utilization of advanced processes and professional materials seamlessly integrates electronic components, establishing a robust foundation for the stability, performance, and reliability of electronic equipment. A profound understanding of these processes allows for a deeper appreciation of Ceramic Packaging Substrate’s leading position in the electronics industry.
What are the application areas of Ceramic Packaging Substrate?
Ceramic Packaging Substrate, a pivotal element in electronic design, goes beyond its traditional function in PCB engineering, gaining extensive use across various industries. This article delves into the multifaceted applications of Ceramic Packaging Substrate within aerospace, telecommunications, and other sectors, shedding light on its significance in elevating the performance and reliability of electronic systems.
Deployed in spacecraft and satellites, these substrates not only ensure reliable electrical connections but also effectively tackle thermal management challenges posed by extreme temperatures and pressures. Illustrated through real-world examples, Ceramic Packaging Substrate emerges as a pivotal element in space exploration missions, ensuring the stable operation of electronic systems in harsh environmental conditions.
In the telecommunications sector, marked by an essential need for high performance and reliability, the Ceramic Packaging Substrate emerges as a transformative element in the manufacturing of communication equipment. With its exceptional performance attributes, this substrate proves to be highly advantageous for use in radio frequency (RF) modules and microwave devices, particularly in the context of 5G and Internet of Things (IoT) devices. Through real-world examples, this article will illustrate the significant influence of Ceramic Packaging Substrate in enhancing the performance of communication equipment and minimizing signal loss.
Performance improvements and reliability guarantees
By providing excellent electrical performance and stable material properties, Ceramic Packaging Substrate effectively improves the overall performance of electronic systems while ensuring system reliability in harsh environments.
The wide application of Ceramic Packaging Substrate brings new possibilities to electronic design in different industries. From aerospace to telecommunications, these substrates advance modern electronic systems by improving performance and reliability. Through in-depth study of actual cases, we can better understand the key role of Ceramic Packaging Substrate in different application fields, which indicates its continued influence in future electronic engineering.
Where to find Ceramic Packaging Substrate?
Start by giving priority to companies with a stellar reputation in the field. Reputable companies usually boast extensive experience and a proven track record as reliable sources of top-notch materials.
Look for manufacturers recognized for their excellence in Ceramic Packaging Substrate production. These companies employ cutting-edge manufacturing techniques and rigorous quality control standards to meet the highest industry benchmarks. Evaluate a manufacturer’s reputation through industry reviews, customer feedback, and discussions in professional forums.
In addition to manufacturers, reliable distributors play a vital role in acquiring high-quality Ceramic Packaging Substrate. These distributors often maintain partnerships with multiple manufacturers, offering a diverse selection and providing customers with expert advice and support. Evaluate a distributor’s reputation by checking customer reviews and industry recommendations.
When exploring Ceramic Packaging Substrate suppliers, be sure to consider our company. We bring a wealth of experience and a strong reputation in PCB engineering, committed to delivering superior electronic materials. Our product line encompasses various types of Ceramic Packaging Substrate, suitable for diverse application scenarios. Choosing us as your supplier brings several advantages:
Excellent Quality:Our use of advanced production technology and rigorous quality control processes ensures that our products meet or surpass industry standards.
Rich Experience:With a wealth of experience in PCB engineering, our company provides professional technical support and customized solutions.
Reliable Delivery:We are committed to timely product delivery, ensuring your project stays on schedule.
By selecting us as your Ceramic Packaging Substrate supplier, you can be confident that your project is in the hands of a reliable, experienced partner, ensuring its successful implementation.
How to get a quote for Ceramic Packaging Substrate?
Achieving excellence in PCB engineering design heavily relies on the crucial role played by Ceramic Packaging Substrate, as its performance and reliability are indispensable in electronic devices. To harness the full potential of these high-performance substrates, obtaining accurate and competitive quotes becomes a critical aspect. This article delves into the intricacies of securing quotes for Ceramic Packaging Substrate, offering readers valuable insights to consider costs and make well-informed decisions in their pursuit of optimal electronic device design.
The most significant include substrate type, complexity and throughput. Substrate types span different ceramic materials, such as aluminum oxide and aluminum nitride, each with unique physical and electrical properties. Complexity involves factors such as substrate design, hierarchy, and interconnect density. The production volume directly affects the cost-effectiveness of mass production. Therefore, these factors need to be fully considered when seeking a quote.
In order to obtain an accurate Ceramic Packaging Substrate quote, it is first recommended to communicate with multiple manufacturers and suppliers. Different companies may use different materials and manufacturing processes, so their quotes may vary. Through multi-party inquiry, readers can gain a more comprehensive understanding of the market and thus better choose a solution that suits their needs.
When requesting a quote, make sure to describe the project requirements in detail, including substrate specifications, quantity, delivery time, etc. Clear and detailed project descriptions can help manufacturers more accurately assess workloads and provide quotes accordingly. At the same time, asking about the quotation differences for different substrate types and complexities, as well as price discounts under different production volumes, will help readers better understand the internal logic of price formation.
Additionally, given the high-performance nature of Ceramic Packaging Substrate, it’s worth asking the manufacturer for information on quality assurance and testing standards. High-quality substrates may be a little pricey, but for some applications that require extremely high performance, it is a well worth the investment.
Finally, we should not only pay attention to the quotation figures, but also comprehensively consider the manufacturer’s reputation and service quality. Choosing a reputable, full-service manufacturer can ensure successful project implementation and subsequent technical support.
In the process of obtaining a quote for Ceramic Packaging Substrate, readers will be able to make informed decisions that take full advantage of these high-performance substrates in electronic designs by considering substrate type, complexity, production volume, and manufacturer’s reputation.
Common problem
Can Ceramic Packaging Substrates be customized for specific project requirements?
Absolutely. Manufacturers provide customization options to meet specific project needs. This includes tailoring the substrate’s material composition, dimensions, and interconnect technologies to align with the unique demands of diverse electronic designs.
Where can reliable sources for high-quality Ceramic Packaging Substrates be found?
Reputable manufacturers and distributors play a crucial role in sourcing reliable Ceramic Packaging Substrates. Exploring established industry contacts and suppliers ensures access to substrates that meet stringent quality standards.
How do Ceramic Packaging Substrates contribute to miniaturization in electronic devices?
Ceramic Packaging Substrates facilitate miniaturization by providing a compact and efficient platform for mounting electronic components. This is crucial in contemporary electronic designs where space optimization is a key consideration.
Can Ceramic Packaging Substrates be used in consumer electronics?
Yes, Ceramic Packaging Substrates are versatile and find applications in various consumer electronic devices. Their compact size, excellent thermal properties, and reliability make them suitable for modern consumer electronics.
Why choose Ceramic Packaging Substrates over other board types?
In comparison to traditional PCBs, Ceramic Packaging Substrates excel in thermal management, miniaturization, and adaptability to advanced technologies. They offer a distinct edge in scenarios where performance and reliability are paramount.
Where can one find reliable Ceramic Packaging Substrates?
Readers can source high-quality Ceramic Packaging Substrates from reputable manufacturers and distributors in the industry. This ensures access to solutions that meet the highest standards for their projects.
How can I obtain a quote for Ceramic Packaging Substrates?
Obtaining accurate and competitive quotes involves understanding factors such as substrate type, complexity, and production volumes. This information empowers readers to make informed decisions for their projects.