Build Rigid-Flex BGA Substrates. Professional Rigid-flex BGA substrate Supplier, we mainly produce ultra-small bump pitch and ultra-small trace Rigid-Flex BGA Substrates.
Rigid-Flex BGA Substrates epitomize the forefront of innovation in modern PCB engineering, transforming the landscape of electronic component mounting and interconnection with their unique design. These substrates skillfully integrate flexibility and rigidity, providing a versatile foundation for cutting-edge PCB designs.
Through a creative fusion of rigidity and flexibility, Rigid-Flex BGA Substrates introduce unprecedented flexibility in the positioning and connection of electronic components. This ingenious integration enables the substrate to adapt to diverse design requirements, empowering engineers with expanded freedom in their design processes.
Functioning as the fundamental building blocks of PCBs, Rigid-Flex BGA Substrates deliver a versatile foundation for the mounting and interconnection of electronic components. The substrate’s design not only prioritizes connection performance but also places emphasis on considerations such as space utilization, heat dissipation performance, and overall structural innovation.
Rigid-Flex BGA Substrates exhibit a unique set of properties in advanced PCB designs. Its highly reliable connection performance, superior space utilization and support for complex layouts make it increasingly the first choice for design engineers in modern electronic equipment.
This substrate not only serves as a medium for connecting electronic components but also stands as a trailblazer in cutting-edge design. The design philosophy behind Rigid-Flex BGA Substrates encourages engineers to transcend traditional limitations, fostering a continual enhancement of electronic device performance and functionality.
With their inherent flexibility, Rigid-Flex BGA Substrates empower engineers to adopt more adaptable layouts for electronic components. This flexibility opens up additional space for designing compact equipment, enabling components to operate in closer proximity.
Rigid-Flex BGA Substrates transcend their role as mere substrates; they epitomize innovation in electronic design. By seamlessly integrating flexibility and rigidity, these substrates establish a versatile foundation for mounting and interconnecting electronic components, propelling the ongoing evolution of advanced PCB designs. In today’s realm of electronic engineering, embracing this innovation expands the design landscape for engineers, presenting limitless possibilities for future development.
What types of Rigid-Flex BGA Substrates are there?
In modern PCB engineering, Rigid-Flex BGA Substrates stand out for their superior design flexibility and compactness. This article will delve into the diverse world of Rigid-Flex BGA Substrates and explore their various variants tailored to different design needs, providing new possibilities for the design of electronic components.
Single-sided Rigid-Flex BGA Substrates
Single-sided Rigid-Flex BGA Substrates are a common type that feature only one flexible layer. This design is widely used in scenarios that require basic bendability without being overly complex. Its simple structure makes it suitable for applications with limited space, providing a flexible solution for the design of compact electronic equipment.
Double-Sided Rigid-Flex BGA Substrates
Double-sided Rigid-Flex BGA Substrates are more complex in design and contain two flexible layers. This type is suitable for applications requiring a higher degree of flex and flexibility. Through multi-layer design, it provides more circuit paths and more options for complex electronic designs.
Curved layer design
Rigid-Flex BGA Substrates are unique in their curved layer design. These layers allow the board to adapt to different shapes in space-constrained environments, introducing greater creativity in design. The use of curved layers allows these substrates to better adapt to irregular spatial layouts, opening up new design possibilities for innovative electronic products.
Tailor-made designs are a key feature of Rigid-Flex BGA Substrates, making them highly popular for addressing specific design requirements. Manufacturers have the flexibility to customize the number, arrangement, and configuration of flexible layers based on customer specifications, catering to the unique demands of different projects. This bespoke adaptability renders Rigid-Flex BGA Substrates well-suited for a diverse range of applications.
The versatility offered by various types of Rigid-Flex BGA Substrates opens up novel avenues in electronic component design. Whether applied in medical devices or consumer electronics, their pliability and space-efficient nature enable the attainment of enhanced functionality within constrained spaces. Designers can achieve greater innovation and efficiency in electronic product development by carefully selecting the most suitable Rigid-Flex BGA Substrate type tailored to the project’s specific requirements.
Exploration of the diverse options in Rigid-Flex BGA Substrates not only underscores their inherent flexibility and customization capabilities but also highlights their transformative impact on electronic design possibilities. These substrates not only contribute to addressing a variety of design needs but also serve as catalysts for future innovation in electronic product development.
What are the advantages of Rigid-Flex BGA Substrates?
Tailor-made designs are a hallmark of the popularity of Rigid-Flex BGA Substrates, allowing for customization to precisely meet specific design requirements. Manufacturers have the flexibility to adjust the quantity, arrangement, and configuration of flexible layers in accordance with customer specifications, catering to the unique demands of diverse projects. This bespoke adaptability positions Rigid-Flex BGA Substrates as an ideal choice across various applications.
The versatility offered by different types of Rigid-Flex BGA Substrates introduces novel opportunities in electronic component design. From medical devices to consumer electronics, the inherent flexibility and compact nature of these substrates enable the achievement of enhanced functionality within confined spaces. Designers can leverage this flexibility to create more innovative and efficient electronic products, selecting the most suitable substrate type based on the specific project requirements.
Upon investigating different options for Rigid-Flex BGA Substrates, it becomes clear that their adaptability and customizable features surpass traditional limits. These substrates not only meet a wide range of design requirements but also act as a driving force for future innovations in electronic product design.
In general, Rigid-Flex BGA Substrates brings new possibilities to electronic design with its advantages of improving reliability, solving space constraints, optimizing thermal performance and being applicable in multiple scenarios. This innovative substrate not only meets the stringent performance and reliability requirements of modern electronic devices, but also opens the way for future technological development.
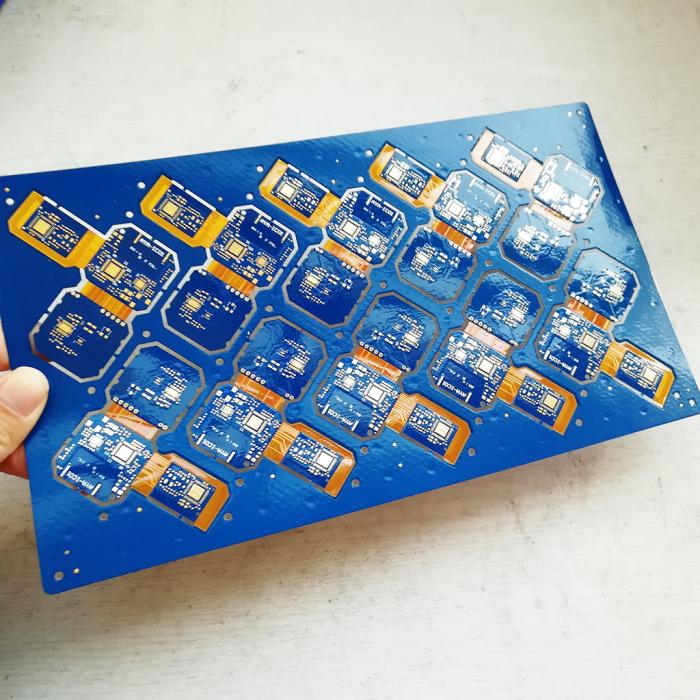
Build Rigid-Flex BGA Substrates
Why choose Rigid-Flex BGA Substrates?
In the swiftly advancing realm of electronic engineering, designers are increasingly favoring Rigid-Flex BGA Substrates as their primary choice. These substrates outperform traditional PCBs, showcasing superior adaptability, space efficiency, and overall performance. This article will unveil the advantages of Rigid-Flex BGA Substrates through a comparative analysis, delving into situations where their indispensability becomes apparent.
One of the things that stands out about Rigid-Flex BGA Substrates is their exceptional adaptability. Traditional rigid PCBs have design limitations, while Rigid-Flex BGA Substrates achieve design freedom through flexible bending layers and can adapt to various complex shapes and space constraints. This flexibility makes Rigid-Flex BGA Substrates perform even better in tight spaces or odd-shaped design scenarios.
Rigid-Flex BGA Substrates offer significant advantages in spatial efficiency compared to traditional PCBs. Unlike conventional PCBs that often require connectors and wires for connections, Rigid-Flex BGA Substrates boast a curved design that minimizes the need for additional connecting components, thereby substantially reducing overall size. This characteristic renders Rigid-Flex BGA Substrates particularly well-suited for contemporary electronic devices with stringent space requirements, such as portable gadgets and smart wearable technology.
Rigid-Flex BGA Substrates exhibit remarkable performance characteristics, offering exceptional capabilities in various applications. Their flexible design plays a pivotal role in minimizing electrical parameters like resistance and inductance, thereby elevating the stability and reliability of signal transmission. Furthermore, the flexible nature of these substrates facilitates superior heat dissipation, a critical feature for high-performance equipment that demands prolonged operation.
These substrates have proven to be invaluable in diverse fields. For example, in medical devices where space and reliability are paramount concerns, Rigid-Flex BGA Substrates align seamlessly with designers’ requirements. Similarly, in the aerospace sector, where lightweight construction and high reliability are pivotal considerations, these substrates emerge as the preferred choice. In such contexts, the limitations of traditional PCBs, such as rigidity and connector issues, become particularly evident, underscoring the adaptability of Rigid-Flex BGA Substrates to address and overcome these challenges.
Overall, through comparative analysis, Rigid-Flex BGA Substrates is gradually becoming a star choice in today’s electronic engineering due to its excellent adaptability, space efficiency and performance. In various design and application scenarios, Rigid-Flex BGA Substrates can show unique advantages, providing broad space for performance improvement and innovative design of electronic devices.
How are Rigid-Flex BGA Substrates made?
Rigid-Flex BGA Substrates represent a pinnacle of innovation in contemporary PCB engineering, seamlessly combining flexibility and rigidity. This article delves into the intricate manufacturing process of these substrates, encompassing the production of motherboards and substrates, highlighting pivotal steps steering their evolution through advanced technologies and materials.
Precision technology takes center stage in crafting the rigid components of Rigid-Flex BGA Substrates, ensuring unparalleled accuracy and reliability. Employing cutting-edge manufacturing techniques such as laser drilling and highly automated assembly lines is imperative to uphold precision in constructing the rigid segments of the motherboard.
Simultaneously, enhancing durability necessitates the utilization of advanced materials. Employing high-strength, high-temperature-resistant composite materials, such as FR-4 (fiberglass cloth covered with flame-retardant tetrafluoroethylene), fortifies the physical properties of the rigid motherboard section, enabling it to thrive in challenging working conditions.
The fabrication of the flexible layer is a critical phase in Rigid-Flex BGA Substrates manufacturing. Leveraging innovative technologies like the Flexible Flexible Circuit Board manufacturing process facilitates precise control over the flexible layers. This technology involves the utilization of flexible substrates, films, and specialized laminate designs to ensure the substrate maintains electrical stability even when subjected to bending and twisting.
Key materials, such as polyimide, play a pivotal role in fostering flexibility. These high-performance polymers exhibit exceptional resistance to high temperatures and chemicals, rendering them ideal for manufacturing the flexible components of Rigid-Flex BGA Substrates. The strategic combination of these materials enables substrates to achieve flexibility without compromising performance, catering to the demands of intricate design requirements.
The manufacturing process of Rigid-Flex BGA Substrates encompasses crucial steps like design, lamination, molding, gold plating, mask preparation, and more. The infusion of advanced technology is pivotal in these steps, with CAD (computer-aided design) software facilitating meticulous control and precision over flexible layers by managing the arrangement of films and substrates.
In the production phase, the deployment of advanced automation equipment, such as automatic forming machines and automatic welding machines, significantly enhances production efficiency and product consistency. The integration of these technologies effectively propels the evolution of the Rigid-Flex BGA Substrates manufacturing process.
In conclusion, crafting Rigid-Flex BGA Substrates demands not only innovative technology but also exemplary expertise in engineering and materials science. The precision manufacturing process of these substrates marks a significant milestone in electronic design, enabling the deployment of high-performance applications across diverse industries.
What are the application scenarios of Rigid-Flex BGA Substrates?
Rigid-Flex BGA Substrates, as a pioneering element in the field of electronics design and manufacturing, have witnessed widespread adoption across a spectrum of industries, encompassing aerospace and medical devices. The incorporation of these state-of-the-art substrates not only brings flexibility and dependability to diverse sectors but also serves as a catalyst for innovative designs and functionalities, ushering in a new era of possibilities.
In the aerospace sector, where the imperative for lightweight structures, high strength, and unwavering reliability is paramount, Rigid-Flex BGA Substrates have become ubiquitous in spacecraft, navigation systems, and communication equipment. Leveraging their distinctive structure, these substrates enable electronic components to function with stability even in harsh environmental conditions, thereby providing crucial support for projects like space exploration and satellite communications.
Rigid-Flex BGA Substrates have become a cornerstone within the realm of medical device manufacturing, where stringent demands for reliability and flexibility of electronic components prevail. These substrates are extensively utilized in various medical applications, such as medical imaging equipment, implantable medical devices, and vital sign monitoring devices. Their flexible design allows for seamless adaptation to the intricate morphology of living organisms. Moreover, these substrates demonstrate exceptional performance in signal transmission and power management, significantly augmenting their effectiveness in critical medical applications.
In industrial automation, Rigid-Flex BGA Substrates provide the ideal electronic foundation for a variety of control systems, sensors and robotics. Their flexibility and high-density interconnectivity make these systems more compact and reliable, providing solid technical support for factory automation and smart manufacturing.
Modern automotive electronic systems need to cope with extreme environmental conditions and complex electronic interconnection requirements. The application of Rigid-Flex BGA Substrates in automotive electronic control units (ECUs), driver assistance systems and infotainment systems provides vehicles with more efficient electronic solutions while improving overall system reliability.
The demand for thin, flexible, and high-performance solutions in the consumer electronics market is steadily rising. Rigid-Flex BGA Substrates play a pivotal role in meeting these requirements, particularly in smartphones, wearables, and portable electronics. Their exceptional performance within confined spaces empowers designers to push the boundaries of creativity and achieve more advanced product designs.
Rigid-Flex BGA Substrates find widespread applications across various industries, serving as a crucial foundation for innovative designs and enhanced functionality. From space technology to medical care, and from the automotive sector to personal consumer electronics, these advanced substrates have become an essential and pioneering technology in today’s electronic landscape, owing to their distinctive structure and flexibility. The versatility of their applications not only underscores the breadth of their technological capabilities but also creates ample room for future advancements in electronic design.
Where to get Rigid-Flex BGA Substrates?
Selecting high-quality Rigid-Flex BGA substrates is crucial in contemporary PCB engineering, directly influencing project success. The choice of a reliable supplier is paramount, and this guide emphasizes the importance of careful selection.
It is essential to verify that chosen manufacturers and distributors adhere to industry standards and possess relevant quality certifications. Our company, as a supplier, is dedicated to providing top-notch Rigid-Flex BGA substrates. With extensive industry involvement and accumulated experience, we prioritize maintaining exceptionally high standards.
Effective project planning hinges on accurate and competitive quotes. When selecting a supplier, ensure they furnish a comprehensive quote covering material costs, production processes, and customization requirements. Our company is recognized for transparent and competitive quotes, facilitating meticulous project budgeting.
Comprehensive understanding of a manufacturer’s production capabilities is indispensable for ensuring a seamless project. The supplier should possess ample production capacity to meet requirements and deliver high-quality Rigid-Flex BGA Substrates punctually. Our company boasts advanced manufacturing equipment and streamlined production processes, ensuring the fulfillment of customer specifications.
In the quest for a Rigid-Flex BGA Substrates supplier, meticulous consideration of reputation, quality certifications, quotes, and production capabilities is essential. With an outstanding industry reputation, superior product quality, and comprehensive services, our company emerges as the preferred choice for a trustworthy supplier. Opt for our company to infuse innovation into your project and ensure its successful progression.
What factors go into quoting Rigid-Flex BGA Substrates?
When evaluating a quote for Rigid-Flex BGA Substrates, several crucial factors converge to determine the cost of this highly sophisticated technology. The production of Rigid-Flex BGA Substrates incorporates advanced methodologies and technologies, particularly in achieving seamless transitions between rigid and flexible layers. The intricacies of design and manufacturing processes directly influence costs, making manufacturing complexity a pivotal determinant in the quotation process.
More layers usually mean a more complex structure, and each additional layer will also bring challenges in terms of material cost and manufacturing difficulty. These factors directly affect the formulation of quotations.
The scale of production of Rigid-Flex BGA Substrates also has a significant impact on the quote. Large-scale production often reduces the manufacturing cost per substrate, while small-scale production may increase costs. Therefore, volume production scale is a key factor that needs to be carefully considered during the quotation stage.
The selection of materials for manufacturing Rigid-Flex BGA Substrates plays a crucial role in cost determination. Opting for high-performance or specialized substrate materials can result in elevated expenses. During the quotation process, there is a detailed discussion about material choices to ensure that project performance requirements are met while maintaining cost control.
With the ongoing evolution of technology, new manufacturing processes and technologies continually emerge. While adopting the latest technology can enhance production efficiency, it may also necessitate additional investments and expenses. Therefore, when quoting the use of technological innovations, it is essential to carefully assess the benefits in comparison to the associated extra costs.
Customer customization requirements for Rigid-Flex BGA Substrates may have an impact on quoted prices. Custom designs, special layer stacks and dimensional requirements may require additional engineering and manufacturing costs. Therefore, the quotation stage requires an accurate understanding of the customer’s customization needs.
Taking these factors into consideration, developing a quote for Rigid-Flex BGA Substrates is a complex and delicate process. Manufacturers need to fully understand their customers’ needs while balancing multiple aspects such as technological innovation, production scale and material selection to ensure that their quotes meet quality and performance standards while remaining competitive. This combined consideration makes Rigid-Flex BGA Substrates an exciting choice for highly advanced PCB technologies.
Frequently Asked Questions
Can Rigid-Flex BGA Substrates be customized for specific design requirements?
Yes, Rigid-Flex BGA Substrates offer a high degree of customization. Designers can tailor them to meet specific project needs, including varying layer counts, flexible configurations, and intricate form factors.
How do Rigid-Flex BGA Substrates enhance thermal performance?
The design flexibility of Rigid-Flex BGA Substrates allows for optimized thermal management. By distributing heat more efficiently, these substrates contribute to enhanced reliability and longevity of electronic components.
Are Rigid-Flex BGA Substrates suitable for high-density applications?
Absolutely. Rigid-Flex BGA Substrates excel in high-density applications due to their compact design and ability to accommodate multiple layers, making them ideal for modern electronic devices with intricate circuitry.
What factors influence the cost of Rigid-Flex BGA Substrates?
Several factors impact the cost, including substrate complexity, layer count, and production volumes. Understanding these factors allows project planners to obtain accurate and competitive quotes.
Can Rigid-Flex BGA Substrates replace traditional PCBs in all applications?
While Rigid-Flex BGA Substrates offer numerous advantages, the choice depends on specific project requirements. In certain scenarios, traditional PCBs may still be more suitable.
How do the advantages of Rigid-Flex BGA Substrates contribute to electronic designs?
The advantages, including enhanced reliability, space optimization, and superior thermal performance, play a crucial role in elevating electronic designs. These substrates empower designers to create innovative and reliable products across various applications.
Can Rigid-Flex BGA Substrates be customized for specific project requirements?
Yes, Rigid-Flex BGA Substrates offer a high degree of customization. Designers can tailor these substrates to meet specific project needs, considering factors like layer count, flexibility, and space constraints.
How do Rigid-Flex BGA Substrate quotes vary, and what factors influence pricing?
Rigid-Flex BGA Substrate quotes depend on factors like substrate complexity, layer count, and production volumes. Understanding these factors is crucial for obtaining accurate and competitive quotes aligned with project budgets.