What is Cavity Packaging Substrate?
Cavity packaging substrate manufacturing. We have made the Cavity PCBs with Rogers base, Panasonic(M7) base, BT Base, metal base, High TG FR4 base and other types PCB base materials.
Cavity Packaging Substrate, as a new technology in the field of PCB engineering, represents an advanced packaging method. Its unique feature is that it achieves higher integration of electronic devices and superior electrical performance by cleverly creating a cavity structure inside the substrate. The introduction of this technology has brought revolutionary changes to IC packaging, not only making the packaging more compact, but also providing better heat dissipation effects.
Key Features of Cavity Packaging Substrate
Before taking a deeper look at Cavity Packaging Substrate, we might as well take a look at its main features. This innovative technology mainly forms a cavity structure inside the substrate, in which electronic devices are cleverly placed. This structure makes the IC package more compact and provides a shorter electrical connection path for the circuit, thereby improving electrical performance.
Higher integration and compact packaging
Cavity Packaging Substrate facilitates enhanced integration of electronic devices by incorporating a cavity structure within the substrate. This heightened integration not only results in a more compact overall package but also diminishes the distance between circuit components, thereby boosting signal transmission efficiency. Such advancements are particularly pivotal for contemporary electronic devices, aligning with the prevailing trend toward smaller and lighter-weight designs.
Superior electrical properties
The innovative design of the cavity structure provides strong support for improving electrical performance. Because the distance between circuit components is reduced, signals travel more quickly, reducing signal transmission delays and thus improving overall electrical performance. This makes Cavity Packaging Substrate technology outstanding in high-performance, high-frequency application scenarios, such as communication equipment and high-performance computing.
Excellent heat dissipation
Beyond its elevated integration capabilities and enhanced electrical performance, Cavity Packaging Substrate distinguishes itself with its exceptional heat dissipation efficiency. The presence of the cavity structure facilitates more effective heat dissipation, resulting in an overall reduction in temperature. This feature holds paramount importance for ensuring the prolonged and stable operation of electronic devices, particularly in demanding environments characterized by high-performance and heavy workloads.
Its advantages in integration, electrical performance and heat dissipation effect pave the way for more advanced and higher-performance electronic devices in the future. Therefore, we can expect to see more innovative applications based on Cavity Packaging Substrate in the near future, promoting further development in the field of electronic engineering.

Cavity Packaging Substrate
What functions does Cavity Packaging Substrate have?
Cavity Packaging Substrate (CPS), as an advanced packaging technology, demonstrates its diverse functions and provides engineers with more flexible options through different materials, layers and structures to meet the needs of various application fields.
Primarily, one of the pivotal functions of CPS (Chip Package System) is the enhancement of heat dissipation performance. Through the creation of a cavity structure within the substrate, CPS significantly improves the efficiency of heat dissipation. This enhancement proves crucial in domains like high-performance computing, communications, and embedded systems, ensuring the integrated circuit operates more stably, particularly under high load conditions.
Second, CPS is designed to enhance signal integrity. Due to the increasing demand for high-speed and high-frequency communications in electronic equipment, CPS effectively reduces interference and distortion in signal transmission through a carefully designed cavity structure, improving the reliability of signal transmission.
Furthermore, the versatile design capabilities of Cavity Packaging Substrate (CPS) enable it to seamlessly meet the diverse packaging requirements of devices with varying densities and sizes. This encompasses the incorporation of different levels and structures, such as multi-level and multi-cavity designs, facilitating the creation of highly integrated electronic components. This design diversity empowers engineers with substantial flexibility, allowing CPS to adeptly adapt to a wide array of application scenarios.
In terms of material selection, CPS offers a range of options, including high-performance resins and thermal conductive materials. This flexibility empowers engineers to choose the most suitable material based on the specific requirements of an application, ensuring optimal performance.
In summary, Cavity Packaging Substrate emerges not just as a technological innovation but as a solution that provides engineers with a wealth of choices to address the increasingly intricate and diverse needs of electronic equipment. The integration of its multifaceted functions positions CPS to play an ever-expanding role in the future of electronic engineering, fostering continuous progress and development within the electronics industry.
What are the different types of Cavity Packaging Substrate?
In the field of PCB engineering, Cavity Packaging Substrate (CPS) has taken solid steps on the road of innovation with its diverse types. This advanced packaging technology not only dazzles engineers, but also shows a wide range of potential in different application fields. Let’s take a closer look at the various types of CPS, including materials, layers, and structures.
Different materials
One of the first features of CPS is its wide variety of material options. Engineers can select different materials based on specific application needs to achieve better performance and adaptability. From traditional organic substrates to advanced ceramic substrates, CPS’s wide range of materials provides designers with greater flexibility.
Multi-level design
A significant breakthrough in CPS lies in its multi-level design. Engineers strategically incorporate multi-level structures within the substrate, enabling a heightened level of integration. This innovation empowers electronic devices to execute more intricate functions within a confined space. Beyond enhancing performance, this multi-layered design contributes to a reduction in the overall package size, optimizing the compactness of electronic components.
Structural diversity
The structural design of CPS is very diverse to meet the needs of different application fields. From simple planar structures to complex three-dimensional cavities, CPS structures can be customized to meet the requirements of specific applications. This versatility allows CPS to excel in both high-density integrated circuits and high-frequency applications.
Provide options for different application areas
The diversity of CPS not only gives engineers more choices in the design process, but also provides tailor-made solutions for different application fields. For example, in the field of high-frequency communications, engineers can choose materials and structures with excellent electromagnetic properties; while in embedded systems, multi-level designs can meet the needs of complex circuits.
The diverse types of Cavity Packaging Substrate bring new possibilities to PCB engineers. Through flexible choices of materials, layers and structures, engineers can customize designs to meet the needs of high-performance packaging in different fields. This diversity not only expands the design space of engineers, but also drives PCB technology to continuously move forward.
This is just a preliminary discussion of the various types of Cavity Packaging Substrate. As technology continues to advance, I believe we will see more exciting innovations in this field.
What is the relationship between Cavity Packaging Substrate and IC packaging?
In today’s rapidly developing electronic technology field, the introduction of Cavity Packaging Substrate has brought significant changes to the IC packaging field. Compared with traditional IC packaging technology, Cavity Packaging Substrate exhibits higher integration and more advanced heat dissipation performance, pushing our chip packaging experience to a new level.
Higher integration
Cavity Packaging Substrate achieves the ultimate utilization of space by introducing a cavity structure inside the substrate. This allows different functional units to be more compactly integrated, effectively reducing the overall package size. Compared with traditional IC packaging, Cavity Packaging Substrate has a higher degree of integration, providing designers with greater freedom, making it possible to accommodate more functions in a limited space.
Advanced cooling performance
As the power consumption of electronic devices continues to increase, heat dissipation issues have become an important factor restricting chip performance. Cavity Packaging Substrate provides a more effective heat dissipation channel by introducing cavities into the packaging structure. This design reduces thermal interaction between components, allowing the chip to dissipate heat more efficiently under high loads. Compared with traditional packaging, Cavity Packaging Substrate is advanced in thermal management, providing the feasibility of long-term high-performance operation of electronic devices.
In-depth discussion of chip packaging technology
To understand the position of Cavity Packaging Substrate in the field of IC packaging, we need to delve into the classification of chip packaging technology. Traditional packaging technologies mainly include passive packaging and active packaging, while Cavity Packaging Substrate is an innovative form of active packaging.
In active packaging, the cavity structure of Cavity Packaging Substrate provides a more flexible connection method for internal chips and promotes rapid communication between different functional units. This design makes signal transmission more efficient, reduces the loss of signal integrity, and provides strong support for the high performance of electronic equipment.
The introduction of Cavity Packaging Substrate marks a new round of changes in IC packaging technology. Its higher integration level and advanced heat dissipation performance make it increasingly popular in electronic device design. By in-depth study of the classification of chip packaging technology, we can better understand Cavity Packaging Substrate’s unique position in this field, bringing broader possibilities to the development of future electronic devices.
What is the difference between Cavity Packaging Substrate and PCB?
Cavity Packaging Substrate (CPS) stands out as a pioneering packaging technology, marked by distinctive features that set it apart from traditional Printed Circuit Boards (PCB). This article will explore the unique attributes of CPS, particularly focusing on its applications in motherboards, substrates, as well as Substrate-like PCB (SLP) and High-Density Interconnect (HDI) Substrate.
The evolution of motherboards
CPS introduces new elements into the motherboard design and achieves a higher degree of integration through its internal cavity structure. Compared with traditional PCB, CPS motherboard is not only more compact, but also performs well in signal transmission and heat dissipation. This makes CPS motherboards more widely used in high-performance computing and advanced electronic equipment.
Substrate innovation
At the substrate level, CPS uses advanced materials and manufacturing technologies to ensure higher reliability and performance. Its cavity structure not only provides more space for component placement, but also improves heat dissipation. This provides strong support for the long-term stable operation of electronic equipment.
Substrate-like PCB (SLP) flexibility
The difference of CPS in Substrate-like PCB (SLP) is mainly reflected in its flexibility and adaptability. Due to the design of its cavity structure, CPS can more flexibly meet the needs of different shapes and sizes, making the design of SLP more creative and diverse.
Improvements in High-Density Interconnect (HDI) Substrate
Compared with traditional HDI Substrate, CPS introduces more advanced packaging technology. Through the clever design of the internal cavity, CPS is better at realizing high-density interconnections, thereby improving signal integrity and electrical performance. This is crucial for applications in modern electronic devices that increasingly require high-speed data transmission.
Overall, the emergence of Cavity Packaging Substrate not only leads the trend of innovation in the field of PCB engineering, but also opens up new possibilities for the design and performance improvement of electronic devices. Its unique characteristics in motherboard, substrate, SLP and HDI Substrate make CPS an important technology that cannot be ignored in today’s advanced electronic engineering.
What are the main structures and production technologies of Cavity Packaging Substrate?
In the field of Cavity Packaging Substrate (CPS), its unique structure and innovative manufacturing technology bring new possibilities to the field of electronic packaging. This section will provide an in-depth introduction to the main structure and manufacturing technology of CPS, including improved high-density interconnect (HDI) manufacturing technology and advanced semi-additive methods.
Structure of Cavity Packaging Substrate
The structural design of CPS aims to achieve a higher degree of integration and excellent electrical performance. Its main structure includes:
Cavity design: The core feature of CPS is the creation of a cavity structure inside the substrate. These cavities can be customized into different shapes and sizes to accommodate a variety of devices and components. The design of the cavity allows electronic components to be laid out more compactly and achieve higher device density.
Hierarchical structure: CPS usually adopts a multi-layer structure, with each layer carrying different functions. By cleverly designing the connection methods of different layers, CPS can achieve more flexible circuit layout and improve signal integrity.
Heat dissipation layer: In order to solve the heat dissipation problem caused by high integration, the CPS structure usually contains a specially designed heat dissipation layer. The existence of this layer effectively improves the heat dissipation effect of the device and ensures the stability and reliability of the system.
Manufacturing technology of Cavity Packaging Substrate
HDI technology plays a key role in the manufacturing of CPS. By improving HDI manufacturing technology, CPS can achieve finer lines and smaller apertures, thereby increasing the wiring density of circuit boards. This further promotes compact integration of devices and helps achieve smaller electronic products.
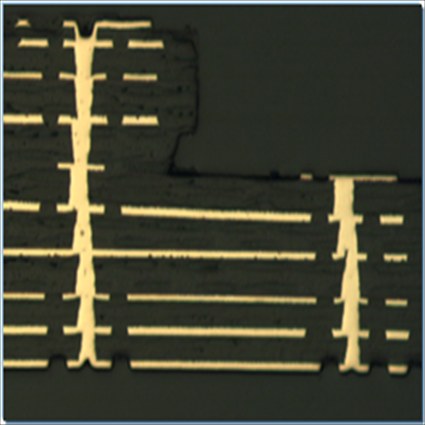
Cavity Packaging Substrate
The semi-additive method is another innovative technology in CPS manufacturing. This method adds materials layer by layer on a substrate, and then uses process steps such as photolithography and etching to accurately form the required circuit pattern. The improved semi-additive method not only improves manufacturing efficiency, but also reduces manufacturing costs and provides feasibility for large-scale production.
By combining these two advanced manufacturing technologies, CPS achieves more flexible control over device layout while ensuring high performance and reliability. The continuous innovation of these technologies has promoted the wide application of CPS in the electronic field, from mobile devices to industrial control systems, showing its huge potential.
In the research and application of CPS, we can see the continuous evolution of structure and manufacturing technology, bringing more advanced and efficient solutions to the field of electronic packaging. With the continuous advancement of technology, Cavity Packaging Substrate will continue to play a pivotal role in the electronics industry.
What are the common problems with Cavity Packaging Substrate?
When discussing the advantages, application fields and future development trends of Cavity Packaging Substrate (cavity packaging substrate), the following are some issues that may cause readers to pay attention.
What are the advantages of Cavity Packaging Substrate compared to traditional packaging?
The advantages of Cavity Packaging Substrate are mainly reflected in the higher integration and excellent heat dissipation performance it provides. Through the internal cavity structure, the device can be packaged more compactly, improve electrical performance, and effectively enhance heat dissipation to cope with the thermal challenges of high-performance chips.
In which application areas does Cavity Packaging Substrate perform outstandingly?
Cavity Packaging Substrate has performed well in high-performance computing, artificial intelligence, communications and other fields. Its superior heat dissipation performance makes it an ideal choice for high-power, high-density electronic devices, providing key support for the development of these fields.
What is the production cost of Cavity Packaging Substrate?
Although Cavity Packaging Substrate has improved in performance, its production costs have gradually become more reasonable. As the technology matures and is widely used, its cost is expected to be further reduced, prompting more industries to adopt this technology.
Is Cavity Packaging Substrate suitable for small electronic devices?
Yes, Cavity Packaging Substrate is not just for large devices. Its flexibility allows it to meet a variety of size and power requirements, including small portable devices. Using Cavity Packaging Substrate in small electronic devices helps improve performance and reduce heat generation.
How does Cavity Packaging Substrate meet the challenges of future electronic devices?
Cavity Packaging Substrate is considered a key technology for the development of future electronic devices. It is expected to meet the challenges of growing performance demands and smaller size by providing higher integration and improved heat dissipation. In the future, we can expect to see Cavity Packaging Substrate play an important role in a wider range of application fields and promote innovation and development in the electronics industry.
What are the potential innovation directions of Cavity Packaging Substrate in its future development?
Future development of Cavity Packaging Substrate may involve continuous improvements in materials, production processes and design methods. As technology continues to evolve, we can expect more advanced and efficient Cavity Packaging Substrate technology to emerge to provide more innovative solutions for electronic engineers.