Cavity PCB| High Speed PCB Manufacturer. To produce the Cavity PCBs, We can use the BT High Speed materials, Panasonic M2 to M8 materials, or ABF materials, and we also can use other types base materials to produce the Cavity PCBs from 4 layer to 30 layers.
In today’s digital era, the role of Cavity PCB manufacturers is crucial. Not only are they an important part of the PCB ecosystem, they are also key to providing critical performance and stability for electronic devices. Through professional design and manufacturing processes, they are able to provide customers with customized PCB solutions to meet the needs of different industries and promote innovation and technological progress. Therefore, Cavity PCB manufacturers play a key role in providing quality PCB solutions.
What is a Cavity PCB?
A Cavity PCB (cavity printed circuit board) is a printed circuit board with grooves or cavities designed to accommodate electronic components or other components to improve the performance and stability of the circuit. These grooves are typically located on the surface or within the circuit board and can be custom designed to meet specific application needs. The design of Cavity PCB allows electronic components to be more tightly integrated on the circuit board, resulting in higher circuit density and performance.
Cavity PCB’s grooves or cavities can come in different shapes and sizes to accommodate a variety of different components and layout requirements. These grooves can be used to install various components such as package components, heat sinks, sensors, connectors, etc., thereby optimizing the functionality and performance of electronic devices. By embedding components inside the PCB, the overall size of the circuit board can be reduced, the stability and reliability of the circuit can be improved, and the interference and loss of signal transmission in the circuit can be reduced.
Cavity PCB has a wide range of applications, especially in high-performance electronic equipment and packaging-intensive applications. For example, Cavity PCB is commonly used in wireless communication equipment, medical equipment, military aerospace systems, and automotive electronic systems. In these fields, the requirements for circuit performance, reliability and size are very strict, and Cavity PCB is designed to effectively meet these requirements and provide more reliable and high-performance solutions.
In summary, Cavity PCB is a printed circuit board with grooves or cavities that can be used to accommodate various electronic components and components to improve the performance and stability of the circuit. Its design enables electronic devices to be integrated more compactly, achieving higher circuit density and performance, and is widely used in various high-performance electronic devices and packaging-intensive applications.
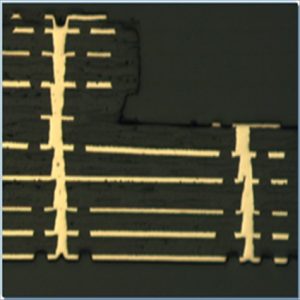
Cavity PCB
How to Design a Cavity PCB?
Designing a Cavity PCB is a complex engineering task that requires experienced engineers and advanced software tools. From determining cavity location to optimizing circuit layout, the design process requires a comprehensive consideration of circuit requirements, material selection, and manufacturing feasibility.
First of all, determining the cavity location is one of the key steps in designing Cavity PCB. Engineers need to carefully analyze circuit functionality and space constraints to determine the optimal cavity location and size. This requires consideration of how circuit components are laid out and connected to ensure optimal performance and stability within the limited space.
Secondly, optimizing circuit layout is another important aspect of the design process. Engineers must place circuit components and connecting wires in cavities and boards to minimize signal interference and electromagnetic radiation. This requires a combination of circuit functionality, performance requirements and space constraints to achieve optimal performance through precise layout design
In addition to this, designing Cavity PCB also needs to consider material selection and manufacturing feasibility. Engineers must select appropriate substrate materials and cavity materials to meet the specific requirements of the circuit and ensure manufacturing feasibility. The material’s thermal conductivity, mechanical properties, and chemical stability will all affect the performance and reliability of the final product and require careful evaluation and selection.
Throughout the design process, engineers need to utilize advanced software tools to assist in design and simulation. These tools help engineers perform circuit layout, signal simulation and thermal analysis to optimize designs and ensure final product performance and reliability. At the same time, these tools can also help engineers evaluate manufacturing feasibility and resolve potential production issues during the design phase.
To sum up, designing Cavity PCB requires experienced engineers and advanced software tools, and requires comprehensive consideration of circuit requirements, material selection, and manufacturing feasibility. Only by fully considering these factors can Cavity PCB products with high performance and high reliability be designed.
What is the Cavity PCB Fabrication Process?
When we talk about Cavity PCB manufacturing process, we need to understand a series of key steps in it. First, manufacturers must carefully select raw materials. This includes selecting a high-quality substrate material such as FR4 or Rogers materials that suit specific application needs. These materials must have excellent thermal conductivity, mechanical properties and chemical stability to ensure the performance and reliability of the final product.
Secondly, cavity processing is a key step in the Cavity PCB manufacturing process. At this stage, manufacturers need to use advanced processing equipment, such as CNC machine tools, to accurately cut or drill the cavity to meet design requirements. High-precision machining is critical to maintaining the integrity and stability of PCB structures.
Next comes the lamination process. At this stage, the manufacturer assembles the pre-processed substrate together with the conductive and insulating layers and laminates them under high temperature and pressure. This ensures good adhesion between the PCB layers, as well as the overall strength and stability of the board. Quality control is particularly important at this step to ensure that pressure and temperature at each level are accurately controlled.
Finally, molding is the last step in the Cavity PCB manufacturing process. At this stage, the PCB will be cut into its final shape and surface treated to protect it from environmental corrosion or mechanical damage. Manufacturers need to ensure that each PCB undergoes rigorous inspection and testing to ensure that it meets design specifications and quality standards.
Overall, the Cavity PCB manufacturing process includes key steps such as raw material selection, cavity processing, lamination, and molding. Manufacturers must ensure high-precision machining and strict quality control to ensure the performance and reliability of the final product. This refined manufacturing process is key to ensuring Cavity PCB meets customer needs and performs well in a variety of application scenarios.
How to Manufacturer a Cavity PCB?
Manufacturing a cavity PCB requires a series of steps and specialized equipment. The following is a rough process:
Design: First, the PCB needs to be designed. This can be done with PCB design software, and the design needs to take into account the location and size of the voids.
Material preparation: Prepare the substrate materials for PCB manufacturing. Commonly used substrate materials include FR4 fiberglass composites.
Photolithography: Transferring the PCB design pattern to the photoresist film. This can be done using a UV exposure machine and photoresist.
Etching: Put the photoetched substrate into an etching machine, and use a chemical solution to etch away the unnecessary copper layer to form a circuit pattern.
Drilling: Use a CNC drill machine to drill holes in the PCB. These holes will be used to mount components and connect wires between different layers.
Via-holes: Holes are created by creating electrical connections between different layers of a PCB. This can be done by using a laser drill.
Chemical treatment: Chemical treatment of PCB, such as removal of photoresist residue, and special treatment of cavity parts to improve electrical connection performance.
Testing: Test the manufactured cavity PCB to ensure that all circuits are connected correctly and there are no shorts or open circuits.
Surface treatment: As needed, surface treatments such as gold plating and tin plating are performed on the PCB surface to improve welding performance and oxidation resistance.
Final inspection and packaging: Finally, the PCB is subjected to final inspection to ensure that the quality meets the requirements, and then is packaged and ready to be shipped to the customer.
The above are the general steps for manufacturing cavity PCB. In actual operation, they may be adjusted according to specific conditions and requirements.
How Much Does a Cavity PCB Cost?
The cost of a cavity PCB depends on multiple factors, including board type, number of layers, size, special process requirements, and production quantity. Typically, smaller single-layer cavity PCBs can cost anywhere from a few dollars to tens of dollars, while more complex multi-layer cavity PCBs can cost more, perhaps hundreds of dollars or more.
To get an accurate quote, you need to provide detailed design documents and requirements to the PCB manufacturer. They will provide you with a quote based on this information and adjust the cost based on your needs. In addition, the production quantity will also affect the price. Generally speaking, the cost of mass production will be lower than the cost of small batch production.
What materials are Cavity PCB made of?
Cavity PCB usually uses high-performance substrate materials, such as FR4 or Rogers materials. These materials are popular in PCB manufacturing because of their excellent thermal conductivity and mechanical properties, making them suitable for a variety of applications.
First, let’s look at FR4 materials. FR4 is a glass fiber reinforced composite material commonly used in the manufacture of PCB substrates. It has excellent insulating properties and mechanical strength and can withstand high temperatures and pressures. FR4 material also has good chemical stability and can resist chemical corrosion and solvent erosion, so it is very suitable for use in harsh environments.
Another commonly used material is Rogers material. Rogers is a company that specializes in high-performance materials, and its PCB substrate materials are known for their excellent electrical performance and stability. Rogers materials have low dielectric constant and low dielectric loss, providing excellent signal transmission performance in high-frequency and high-speed applications. In addition, Rogers material also has good thermal conductivity, which can effectively disperse and dissipate heat in the circuit, ensuring the stability and reliability of the circuit.
Whether it is FR4 or Rogers materials, they are widely used in electronic equipment in various fields, including communications, medical, military and industrial control. Their excellent performance and reliability enable Cavity PCB to perform well in a variety of harsh environments and demanding applications.
In short, Cavity PCB usually uses high-performance substrate materials, such as FR4 or Rogers materials. These materials have excellent thermal conductivity and mechanical properties, making them suitable for a variety of applications. Their stability and reliability provide important support for the design and manufacturing of electronic equipment, making Cavity PCB play a vital role in the field of modern technology.
Who manufactures Cavity PCB?
The manufacturing of Cavity PCB involves highly technical processes and specialized equipment, so choosing the right manufacturer is crucial. So, who exactly makes Cavity PCB? On this critical issue, our company would like to demonstrate our professional capabilities to you.
As a manufacturer of Cavity PCB, our company has strong technical strength and rich experience, and is committed to providing customers with high-quality PCB solutions. We have advanced equipment and technology to meet the manufacturing needs of various complex PCBs, including Cavity PCBs with grooves or cavities.
Our manufacturing process strictly follows international standards. From the selection of raw materials to the quality control of the final product, every link is strictly controlled to ensure product performance and reliability. Our team consists of experienced engineers and technicians, able to provide customers with a full range of technical support and solutions.
At the same time, we focus on customer needs and provide personalized design and manufacturing services to meet the specific needs of different customers. We work closely with our clients and maintain open lines of communication from project inception to completion to ensure the highest level of client satisfaction.
As a professional Cavity PCB manufacturer, we are committed to providing customers with high-quality products and services to help customers succeed in market competition. Choose us and you will get a reliable partner to jointly develop a better future.
In this era of challenges and opportunities, it is crucial to choose a reliable Cavity PCB manufacturer. Our company will wholeheartedly provide you with the best quality solutions and work with you to create a better future!
What are 5 qualities of a good customer service?
Quality Cavity PCB manufacturers are customers’ reliable partners in PCB projects. They not only provide high-quality products, but also ensure that customers have the best experience throughout the entire cooperation process through excellent customer service. Below we explore five key attributes of great customer service:
Professionalism: A high-quality Cavity PCB manufacturer should be highly professional. Their team should be composed of experienced engineers and technical experts who can provide customers with professional advice and solutions. No matter what technical difficulties or challenges customers face, manufacturers should be able to support them with professionalism and technical prowess.
Timely response: In a fast-paced business environment, timely response is very important. A quality manufacturer should be able to respond promptly when customers have questions or needs and provide prompt solutions. This includes prompt responses to various communication channels such as emails, phone calls, and online messages.
Personalized care: Each customer has their own unique needs and requirements, and a quality manufacturer should be able to provide personalized care and services based on the customer’s specific situation. This may include customized design solutions, flexible delivery schedules, or even a dedicated technical support team.
Problem Solving Skills: In any project, problems and challenges are inevitable. A quality manufacturer should be able to identify and resolve problems quickly and work closely with customers to find the best solution. They should have sufficient technical capabilities and resources to handle various issues and ensure the smooth progress of the project.
Continuous improvement: Customer needs and technical standards are constantly changing, and quality manufacturers should be able to keep pace with the times and continuously improve and optimize their products and services. Through continuous improvement, they can improve product quality, shorten lead times, and provide a better customer experience.
The combination of these qualities ensures customers have the best experience when working with Cavity PCB manufacturers. Professionalism, prompt response, personalized care, problem-solving skills and continuous improvement are not only the basis for providing quality products, but also the key to building long-term relationships. Therefore, when choosing the right manufacturer, customers should pay attention to these qualities and ensure that they can meet their needs and provide quality services.
FAQS
How much does Cavity PCB manufacturing cost?
The manufacturing cost of Cavity PCB is affected by many factors. The first is material selection. Different materials have different costs. For example, the cost of FR4 and Rogers materials may be different. The second is the complexity of the design. More complex designs may require more processing steps and higher costs. In addition, the scale of production will also affect the cost. Generally speaking, the unit cost of high-volume production will be lower. Therefore, it is recommended to discuss these factors in detail when communicating with the manufacturer to obtain an accurate cost estimate.
How to choose the right Cavity PCB manufacturer?
Choosing the right Cavity PCB manufacturer is very important. First consider the manufacturer’s experience and professional capabilities, whether they have extensive experience and advanced technology to meet your needs. Second is the level of customer service. A good manufacturer should be able to respond to your needs in a timely manner and provide personalized service. In addition, the manufacturer’s quality control and continuous improvement capabilities must also be considered. Whether they can guarantee the quality and performance of the product and continuously improve the production process. Finally, price is also one of the factors to consider when choosing a manufacturer, but it shouldn’t be the only one. Taking the above factors into consideration, it is crucial to choose the manufacturer that best suits your needs.
What are the common applications of Cavity PCB?
Cavity PCB has a wide range of applications in many fields. For example, they are commonly used in high-frequency and high-speed circuit designs such as wireless communications equipment, radar systems, and high-speed computer networks. In addition, Cavity PCB is often used in applications that require high-density integration and thermal performance, such as avionics in aerospace and military fields. Overall, Cavity PCB plays an important role in various demanding applications.
How is Cavity PCB different from ordinary PCB?
The main difference between Cavity PCB and ordinary PCB is that it has a groove or cavity structure. This design allows Cavity PCB to accommodate more electronic components or other components and provide better heat dissipation performance. In addition, Cavity PCB is often used in applications that require higher circuit performance and stability, such as high-frequency and high-speed circuit design. Therefore, compared with ordinary PCB, Cavity PCB is more suitable for some specific application scenarios.