Cavity substrate manufacturing.High speed and high frequency material packaging substrate manufacturing. Advanced packaging substrate.
Do you want to know how Cavity Substrate in PCB (Printed Circuit Board) works? Cavity Substrate is a key technology that provides more functionality and flexibility to PCBs. This article will delve into the definition, role and importance of Cavity Substrate in PCB manufacturing. By learning about Cavity Substrate, you will better understand the complexities of PCB manufacturing and master the key factors that improve the performance of electronic devices.
How is Cavity Substrate designed and manufactured?
Do you understand the design and manufacturing process of Cavity Substrate? As a key component in PCB manufacturing, Cavity Substrate’s design and manufacturing process are crucial. Below we will introduce the basic principles and steps of Cavity Substrate manufacturing and how to use CAD software for design.
First, let’s understand the basic principles of Cavity Substrate. Cavity Substrate is usually manufactured by carving out grooves (cavities) on the surface of the PCB board. These grooves are usually used to install specific electronic components or chips. The design of Cavity Substrate needs to take into account the size, layout and connection of electronic components to ensure optimal performance and reliability.
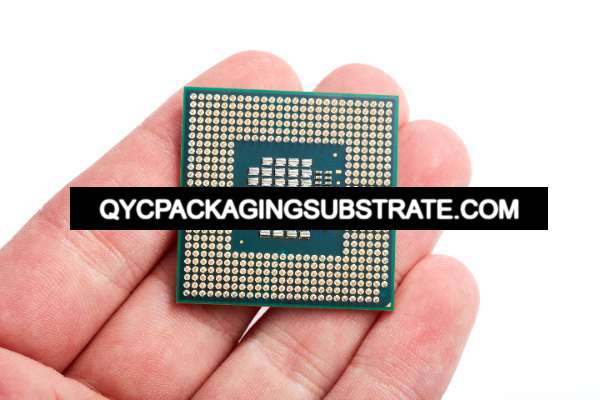
Cavity substrate manufacturing
The manufacturing process of Cavity Substrate usually includes the following key steps:
Material selection and preparation: Select a suitable substrate material and ensure its surface is smooth and flat for subsequent processing.
Cavity design and processing: According to the requirements and layout of electronic components, use processing equipment (such as CNC machine tools) to cut grooves on the surface of the PCB board. Cavity’s design required precise calculations of size and depth to ensure electronic components would fit accurately and connect well with other components.
Hole drilling and solder paste coating: Drill holes on the PCB board to install other electronic components, and apply a layer of solder paste on the surface for subsequent soldering processes.
SMD assembly and welding: Electronic component patches are mounted on the PCB board and connected to the PCB board through soldering processes (such as hot air soldering iron or reflow oven).
In the design and manufacturing process of Cavity Substrate, CAD (Computer-Aided Design) software plays a vital role. Using CAD software, engineers can precisely design the Cavity’s size and shape and simulate how electronic components will be laid out and connected. CAD software can also help engineers optimize Cavity’s design and improve production efficiency and product quality.
In general, the design and manufacturing of Cavity Substrate is a complex and precise process, which requires engineers to have professional knowledge and skills, and to use advanced processing equipment and CAD software for precise design and processing. Through these steps, you can ensure the production of high-quality Cavity Substrate that meets the performance and reliability requirements of electronic devices.
What is the manufacturing process of Cavity Substrate?
When you deeply understand the manufacturing process of Cavity Substrate, you will find that every step is precise and critical. The following will introduce the manufacturing process of Cavity Substrate in detail, from material selection to final patch assembly and welding.
First, the first step in making Cavity Substrate is choosing the right material. Normally, Cavity Substrate requires the use of high-quality substrate materials, such as FR-4 or high-frequency materials, to ensure PCB performance and stability. When it comes to material selection, manufacturers need to consider the circuit board’s use, operating environment, and performance requirements to ensure that the selected materials meet design requirements.
Next is Cavity design and processing. In this step, the manufacturer needs to use CAD software to design the shape and size of the Cavity based on the design requirements provided by the customer. Cavity is usually used to install special components or increase the heat dissipation performance of PCB. Once the design is complete, the manufacturer will utilize advanced processing equipment to cut and process the PCB, ensuring Cavity’s accuracy and quality.
After the Cavity design and processing is completed, the next critical step is to drill the holes. In this step, the manufacturer will use a CNC drill machine to drill holes into the PCB in order to install electronic components and connect circuits. The location and size of the drilled holes must be precisely controlled to ensure smooth subsequent assembly work.
Next comes solder paste application. In this step, manufacturers will use automated equipment to apply solder paste on the PCB pads for subsequent soldering work. Uniform application of solder paste and accurate position control are crucial to ensuring welding quality.
Finally comes patch assembly and soldering. In this step, manufacturers use a placement machine to precisely place electronic components onto the PCB and a reflow oven to solder the components to the pads. The precision and stability of the patch assembly and welding process directly affect the quality and performance of the PCB.
Through the above detailed introduction, do you have a clearer understanding of the manufacturing process of Cavity Substrate? Every step carries the manufacturer’s exquisite skills and pursuit of quality, ensuring that the final Cavity Substrate can meet customer needs and maintain a high level of quality.
How to control the manufacturing cost of Cavity Substrate?
When it comes to Cavity Substrate manufacturing, controlling costs is crucial. So, are you concerned about how to control the manufacturing costs of Cavity Substrate? This section will delve into the factors that affect the cost of Cavity Substrate and provide cost control strategies and methods.
First, one of the factors that affects the cost of Cavity Substrate is material selection. Different materials have different costs and properties. When choosing a Cavity Substrate material, you should weigh the balance between performance and cost. Some high-performance materials may increase manufacturing costs but may also provide better performance and reliability. Therefore, when selecting materials, product requirements and budget need to be considered.
Secondly, the scale of production will also affect the manufacturing cost of Cavity Substrate. Typically, large-scale production enables higher efficiency and lower costs. Therefore, if possible, consider increasing the order quantity to reduce the manufacturing cost per unit. In addition, optimizing production processes and improving production efficiency can also reduce costs.
In addition, manufacturing processes and equipment are also important factors affecting costs. The use of advanced manufacturing processes and equipment can improve production efficiency and reduce labor costs and energy consumption. In addition, optimizing process flow and reducing scrap rates can also effectively control costs.
In addition, supply chain management is also the key to controlling Cavity Substrate manufacturing costs. Establish long-term cooperative relationships with reliable suppliers to get better prices and more stable supply. In addition, just-in-time purchasing and inventory management can also reduce logistics and inventory costs.
Finally, continuous optimization and improvement are key to controlling Cavity Substrate manufacturing costs. Regularly evaluate the cost structure and look for opportunities to reduce costs, while continuously improving product design and manufacturing processes to improve production efficiency and reduce costs.
To sum up, by considering factors such as material selection, production scale, manufacturing process and equipment, supply chain management, and continuous optimization and improvement, the manufacturing cost of Cavity Substrate can be effectively controlled, thereby improving product competitiveness and achieving better economic benefits.
What materials are used in Cavity Substrate?
Cavity Substrate is an important part of the PCB (Printed Circuit Board) manufacturing process, and its material selection is crucial to its performance and cost. Understanding the materials used in Cavity Substrate is a critical step in gaining insight into its manufacturing process and performance characteristics.
In the manufacturing process of Cavity Substrate, commonly used materials mainly include:
Substrate material: Glass fiber reinforced epoxy resin is usually used as the substrate material. This material has good mechanical strength and heat resistance, is suitable for PCB manufacturing, and can provide sufficient support and stability in Cavity Substrate manufacturing.
Filling materials: The cavity part of Cavity Substrate usually needs to be filled with some special materials to provide additional support and insulation properties. Commonly used filling materials include epoxy resin, polyimide (PI), etc. These materials have good high temperature resistance and mechanical strength and can meet the requirements of PCB in complex working environments.
Conductive material: As a PCB, Cavity Substrate needs to be coated with a layer of conductive material on the surface to achieve connection between electronic components. Commonly used conductive materials include copper, silver, etc., which have good conductivity and welding properties and can ensure stable connection of electronic components on the PCB.
Surface coating material: In order to protect the PCB surface from oxidation and corrosion, it is usually necessary to apply a protective surface coating on the surface. Commonly used surface coating materials include tin, gold, nickel, etc., which can effectively improve the corrosion resistance and reliability of PCBs.
Other auxiliary materials: In addition to the above main materials, some auxiliary materials are also needed during the Cavity Substrate manufacturing process, such as etchants, solvents, cleaning agents, etc., to ensure the smooth progress of the manufacturing process and the quality of the final product.
In the manufacturing process of Cavity Substrate, professional PCB manufacturers or electronic component manufacturers are usually responsible for manufacturing. These manufacturers have advanced production equipment and technology, and have rich experience and expertise to meet the needs and requirements of different customers.
In addition to traditional PCB manufacturers, some companies focusing on high-performance PCB manufacturing have also begun to get involved in the manufacturing field of Cavity Substrate. These companies generally have more advanced technology and higher production capabilities and are able to provide customers with higher quality Cavity Substrate products.
In general, the manufacturing of Cavity Substrate involves multiple professional fields and requires the synergy of various materials and technologies. Only through strict process flow and quality control can high-quality Cavity Substrate products be produced.
Who is making Cavity Substrate?
Large multinational companies usually have advanced manufacturing equipment and technology, as well as rich experience and financial support. They have high visibility and market share in Cavity Substrate manufacturing, can provide one-stop solutions, and have a global production and sales network. Choosing a large multinational company as a manufacturer can usually provide stable product quality and reliable supply guarantee.
Many professional PCB manufacturers also offer Cavity Substrate manufacturing services. They usually have advanced production equipment and technical teams, and have rich experience and expertise in the PCB field. By choosing a professional PCB manufacturer as your manufacturer, you can get customized solutions and flexible production capabilities while enjoying a high cost performance.
Small specialty chemical plants are typically smaller but have deep expertise and experience in a specific field or technology. They may be more flexible, more focused on customer needs, and able to provide personalized service. Choosing a small specialized chemical factory as a manufacturer can provide you with more customized services and faster response times, but you need to pay attention to its production capacity and quality assurance.
When choosing a suitable Cavity Substrate manufacturer, various factors should be considered comprehensively, including technical strength, production capacity, quality assurance, cost-effectiveness, and customer service. Fully communicate with manufacturers and conduct on-site visits and sample testing to ensure that the selected manufacturer can meet the needs and standards of the project.
As a Cavity Substrate manufacturer, we are committed to providing high-quality, reliable Cavity Substrate products, focusing on customer needs, providing customized solutions and excellent customer service. We have advanced production equipment and a professional technical team to meet the various needs of customers and ensure product quality and delivery cycle. Feel free to contact us to learn more about our Cavity Substrate manufacturing services.
What are the five characteristics of great customer service?
In the modern business environment, providing excellent customer service is one of the keys to business success. Especially in the Cavity Substrate manufacturing industry, excellent customer service not only meets customer needs, but also builds long-term relationships and enhances corporate reputation. Here are five characteristics of great customer service:
The first characteristic of great customer service is providing professional support to customers. This includes a thorough understanding of the Cavity Substrate design and manufacturing process and the ability to provide professional advice and solutions to customers. By possessing extensive industry knowledge and experience, manufacturers are able to help customers optimize designs, improve production efficiency, and ensure product quality is at the highest level.
Prompt response and communication are keys to excellent customer service. Manufacturers should be able to respond promptly to customer inquiries and needs and ensure smooth communication between both parties. This proactive approach to communication helps build trust and partnership while also reducing misunderstandings and unnecessary delays.
Every customer’s needs are unique, so providing customized solutions is an important part of great customer service. Manufacturers should be able to tailor the design and manufacturing process to the customer’s specific requirements to meet their specific needs and budget. By working closely with customers, manufacturers are able to provide them with the most suitable solutions, resulting in a win-win situation.
Excellent customer service must be based on product quality. Manufacturers should be able to provide high-quality Cavity Substrate products and strictly adhere to relevant quality standards and processes. By adopting advanced production technology and strict quality control measures, manufacturers are able to ensure stable and reliable product quality, thereby winning customer trust and satisfaction.
The final feature is comprehensive after-sales support. Manufacturers should continue to maintain contact with customers after delivering products and provide them with necessary support and services. This includes resolving issues and questions that may arise, providing technical support and repair services to ensure long-term customer satisfaction and trust in the product.
To sum up, excellent customer service is one of the keys to the success of a Cavity Substrate manufacturing company. Through five characteristics: professional support, timely communication, customized solutions, quality assurance and after-sales support, manufacturers are able to meet customer needs, establish good cooperative relationships, and succeed in the fiercely competitive market.
Frequently Asked Questions
What is a Cavity Substrate and why is it used in PCB manufacturing?
A Cavity Substrate is a specialized type of printed circuit board that includes cavities or recessed areas within its structure. These cavities are designed to accommodate electronic components or other elements of a device. Cavity Substrates are utilized in PCB manufacturing to provide a compact and efficient layout for electronic assemblies, allowing for increased functionality and reduced footprint in electronic devices.
What are the key considerations in designing a Cavity Substrate?
Designing a Cavity Substrate requires careful consideration of factors such as component placement, cavity dimensions, thermal management, and electrical connectivity. Engineers must ensure that the layout optimizes space utilization while maintaining proper clearance and isolation between components. Additionally, considerations for manufacturability and cost-effectiveness play a crucial role in the design process.
What materials are commonly used in Cavity Substrate manufacturing?
Common materials used in Cavity Substrate manufacturing include FR-4 (fiberglass-reinforced epoxy), metal-core substrates, ceramic substrates, and flexible substrates. The choice of material depends on factors such as thermal conductivity, mechanical strength, dielectric properties, and cost considerations.
How does the manufacturing process for Cavity Substrates differ from traditional PCB manufacturing?
The manufacturing process for Cavity Substrates involves additional steps compared to traditional PCB manufacturing, primarily to create the cavities within the substrate. These steps may include precision machining or laser drilling to remove material and create the desired cavity shapes. Additionally, processes such as plating and solder mask application may be adjusted to accommodate the unique features of Cavity Substrates.
What are the advantages of using Cavity Substrates in electronic assemblies?
Cavity Substrates offer several advantages, including improved thermal management, reduced electromagnetic interference (EMI), enhanced mechanical stability, and increased design flexibility. By incorporating cavities, electronic components can be placed closer together, leading to shorter interconnect lengths and improved signal integrity.