What are Ceramic BGA Substrates?
Ceramic BGA substrates Manufacturer. We produce the Ceramic PCB boards, and Ceramic package Substrates from 1 layer to 30 layers.
Ceramic BGA Substrates (Ceramic Ball Grid Array Substrate) is a type of printed circuit board made of ceramic, which has excellent performance and excellent thermal conductivity properties. This substrate plays a key role in the manufacturing of electronic equipment, providing a solid and reliable foundation for the connection and support of various electronic components.
The basic concept of Ceramic BGA Substrates is to use ceramic materials as substrates to replace traditional fiberglass or resin substrates. Ceramic materials have high strength, high temperature resistance and excellent thermal conductivity, which makes Ceramic BGA Substrates widely used in high-performance and high-reliability electronic devices.
In terms of structural features, Ceramic BGA Substrates usually have a multi-layer structure, and each layer contains wires and insulation layers to achieve circuit connection and isolation. Compared with traditional substrates, Ceramic BGA Substrates have better thermal conductivity and can effectively dissipate heat, thereby improving the performance and stability of electronic devices.
In terms of applications in electronic equipment, Ceramic BGA Substrates are widely used in various high-end products, such as computers, communication equipment, medical equipment, and automotive electronics. Its excellent performance and reliability make it an indispensable part of many critical applications. For example, in high-performance computers, Ceramic BGA Substrates can provide stable circuit connections and effective heat dissipation, ensuring long-term stable operation of the equipment.
Overall, Ceramic BGA Substrates, as a type of printed circuit board, are popular in the field of electronic equipment manufacturing for its excellent performance and reliability. It is made of ceramic materials with high strength and excellent thermal conductivity. It is suitable for the manufacturing of various high-end products and plays an important role in improving the performance and stability of electronic equipment.
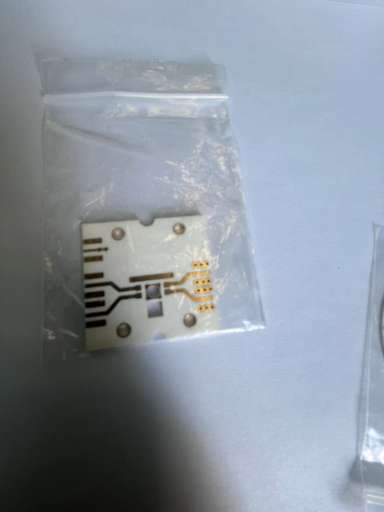
Ceramic PCB
How are Ceramic BGA Substrates designed?
Designing Ceramic BGA Substrates is a complex and critical task that involves many aspects, including material selection, routing planning, and thermal management. The following details the key considerations and common methods for designing Ceramic BGA Substrates.
Selecting the appropriate materials is critical to the design of Ceramic BGA Substrates. Normally, ceramic is one of the main materials for manufacturing Ceramic BGA Substrates due to its excellent thermal conductivity and mechanical strength. In addition, considering the electrical performance and stability, the characteristics of other ceramic materials also need to be considered, such as aluminum oxide, silicon nitride, etc.
When designing Ceramic BGA Substrates, routing planning is a crucial part. Good wiring design can ensure good connections between electronic components and reduce signal interference and electromagnetic interference. During the wiring planning process, factors such as signal transmission path, length, layer spacing, and impedance matching need to be considered to ensure the stability and reliability of circuit performance.
Since Ceramic BGA Substrates are often used in high-performance electronic devices, thermal management is one of the key factors that cannot be ignored during the design process. Good thermal management design can effectively disperse and remove the heat generated on the circuit board and maintain the stable operating temperature of electronic components. In order to achieve effective thermal management, designers can adopt various methods, such as increasing heat dissipation holes, adding heat dissipation layers, using thermal pads, etc.
In addition to the above factors, designing Ceramic BGA Substrates also requires consideration of specific technical performance requirements. This includes the number of layers of the circuit board, apertures, line width and spacing, surface treatment, etc. According to different application requirements, designers need to weigh various technical parameters and choose an appropriate design solution.
Finally, cost and manufacturing feasibility also need to be considered when designing Ceramic BGA Substrates. Designers need to reduce manufacturing costs as much as possible while meeting technical performance requirements and ensure the achievability and manufacturability of the design solution.
To sum up, designing Ceramic BGA Substrates involves many aspects, including material selection, wiring planning, thermal management, technical performance requirements and cost manufacturing feasibility. Designers need to comprehensively consider various factors and adopt appropriate methods and strategies to ensure the stability, reliability and manufacturability of the design solution.
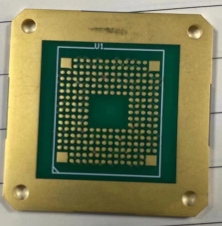
Ceramic BGA Substrates
What is the manufacturing process of Ceramic BGA Substrates?
The manufacturing process of Ceramic BGA Substrates is a complex and delicate process that requires multiple steps to reach the final product. This process, as well as the key technologies and precautions involved, will be analyzed in detail below.
The first step in manufacturing Ceramic BGA Substrates is to prepare the required raw materials. Typically, these raw materials include ceramic powders, conductive materials (such as metal powders), insulating materials, solvents, etc. The quality and ratio of these raw materials will directly affect the performance and quality of the final product.
In the printing stage, the prepared mixed material is coated on the substrate. This step usually uses screen printing technology or calendering technology to ensure that the coating is even and meets the design requirements. At this stage, care needs to be taken to control coating thickness and uniformity, as well as to avoid bubbles and defects.
Sintering is one of the most critical steps in the manufacturing process of Ceramic BGA Substrates. In a high-temperature environment, the material coated on the substrate is sintered to form a strong ceramic base. This process requires precise control of temperature and time to ensure that the material is fully sintered without deformation or cracking.
The sintered Ceramic BGA Substrates also need to be processed to meet specific design requirements and application needs. The machining process may include surface smoothing, hole drilling, wire connection, etc. At this stage, attention needs to be paid to processing accuracy and surface quality to ensure the stability and reliability of the final product.
In general, manufacturing Ceramic BGA Substrates is a comprehensive process that requires precision equipment and strict operating procedures. Only by strictly controlling quality and paying attention to details in every link can we produce high-quality Ceramic BGA Substrates products.
How much does Ceramic BGA Substrates cost to manufacture?
The manufacturing cost of Ceramic BGA Substrates is one of the important factors that need to be carefully considered during the entire production process. These costs are affected by a variety of factors, including material costs, manufacturing processes and specification requirements.
First of all, material cost is one of the main factors affecting the manufacturing cost of Ceramic BGA Substrates. Ceramic materials are generally more expensive than traditional substrates (such as FR4), which increases the cost of the entire manufacturing process to a certain extent. In addition, if special ceramic materials or high-performance ceramic substrates are required, the cost may be higher. Therefore, material selection must be considered during the design stage to control costs while ensuring quality.
Secondly, the manufacturing process will also have an impact on the cost of Ceramic BGA Substrates. Different manufacturing processes may require different investment in equipment, technology and human resources, which directly affects the cost. For example, using advanced sintering processes may increase manufacturing costs, but it can also improve product performance and reliability. Therefore, when selecting a manufacturing process, a balance between cost and product quality needs to be considered.
Finally, specification requirements are also one of the important factors affecting the cost of Ceramic BGA Substrates. Products of different specifications may require different processing techniques and equipment, which directly affects the cost. For example, if a customer requires customized special specifications or high-density wiring, this may increase manufacturing costs. Therefore, when determining product specifications, there is a need to weigh the relationship between customer needs, product performance, and cost.
In response to the above influencing factors, we provide the following suggestions for reducing the cost of Ceramic BGA Substrates:
By comprehensively considering the above factors and taking corresponding cost reduction measures, the manufacturing cost of Ceramic BGA Substrates can be effectively reduced, thereby improving the competitiveness and market share of the product.
What materials are Ceramic BGA Substrates made of?
Ceramic BGA Substrates is a type of printed circuit board, and its material selection is crucial, directly affecting its thermal conductivity, mechanical strength, and application range in electronic equipment. Typically, Ceramic BGA Substrates are mainly made of ceramic materials, which have excellent thermal conductivity and mechanical strength and are suitable for high-temperature, high-frequency and high-power electronic applications.
Aluminum oxide is a commonly used ceramic material with good thermal conductivity and insulation properties. Due to its moderate cost and ease of processing, aluminum oxide is one of the common choices for manufacturing Ceramic BGA Substrates. In addition, aluminum oxide also has good chemical stability and mechanical strength, making it suitable for various high-temperature and high-power applications.
Silicon nitride is another ceramic material commonly used in the manufacture of Ceramic BGA Substrates and has excellent thermal conductivity and mechanical strength. Compared with aluminum oxide, silicon nitride has higher thermal conductivity and lower thermal expansion coefficient, so it is more suitable in some applications that require higher thermal performance.
Aluminum oxide aluminum nitride is a composite material that combines the advantages of aluminum oxide and aluminum nitride. It has good thermal conductivity and insulation properties, and also has a low thermal expansion coefficient. Due to its special material composition, aluminum oxide aluminum nitride excels in some applications that require strict thermal management.
Zirconia is a ceramic material with high high-temperature stability and mechanical strength, and is often used to manufacture high-performance Ceramic BGA Substrates. Zirconia has good insulation properties and corrosion resistance, and is suitable for use in some electronic equipment with high environmental requirements.
Silicon carbide is a special ceramic material with extremely high thermal conductivity and high temperature resistance. Although silicon carbide is more expensive to manufacture, its superior performance in high-temperature, high-frequency and high-power electronic applications makes it an important option.
In general, the material selection of Ceramic BGA Substrates depends on the specific application requirements, including factors such as working environment, temperature range, frequency characteristics, and mechanical strength. By choosing the right materials, Ceramic BGA Substrates can be ensured to have excellent performance and reliability to meet the needs of different electronic devices.
Who makes Ceramic BGA Substrates?
In the field of manufacturing Ceramic BGA Substrates, suppliers are a crucial part. As a company specializing in electronic materials manufacturing, we have extensive experience and expertise in this field. We are committed to providing customers with high-quality Ceramic BGA Substrates and customized solutions to meet various application needs.
As a leading supplier of Ceramic BGA Substrates, we have advanced manufacturing equipment and technical teams to meet our customers’ strict requirements for quality and lead time. Our manufacturing process strictly follows international standards and adopts the latest technology and processes to ensure stable and reliable product quality.
In addition to high-quality products, we also focus on communication and cooperation with customers. Our customer service team is always ready to answer customers’ questions and provide them with technical support and solution suggestions. We know that our customers’ needs are the driving force for our development, so we are always committed to providing our customers with the best products and services.
At the same time, we are also working with other suppliers around the world to jointly promote the development of the Ceramic BGA Substrates industry. By cooperating with other companies, we are able to better integrate resources, improve product quality and production efficiency, and create greater value for customers.
All in all, as a professional Ceramic BGA Substrates supplier, we will continue to adhere to the principle of “quality first, customer first”, constantly improve our technical strength and service levels, and provide customers with better products and more satisfactory services.
Five Characteristics of Great Customer Service
In the modern business environment, providing excellent customer service is crucial in any industry. Especially in the field of PCB manufacturing and Ceramic BGA Substrates, excellent customer service can not only enhance customer satisfaction, but also establish good cooperative relationships and enhance corporate reputation. Here are five hallmarks of great customer service:
Timely response: The number one characteristic of quality customer service is timely response to customer needs and problems. Whether it’s a phone call, email, or online chat, customers expect a quick response when they have an issue. Therefore, an effective customer service team should ensure that customers’ inquiries and complaints are responded to in a timely manner to demonstrate that the company values and cares about its customers.
Professionalism: Professionalism is one of the important indicators to measure the quality of customer service. The customer service team should have extensive product knowledge and industry experience, and be able to provide professional solutions and suggestions based on customer needs. In addition, good communication skills and courtesy are also key to demonstrating professionalism.
Customized services: Every customer has their own unique needs and requirements, so providing customized services is one of the important features of good customer service. The customer service team should provide personalized solutions based on customers’ specific needs and be flexible in responding to customers’ changing needs during product design, manufacturing and delivery.
Continuous follow-up: Excellent customer service doesn’t just end when the transaction is completed, but requires continuous follow-up and care for customers throughout the entire cooperation cycle. The customer service team can maintain close contact with customers through regular communication, customer satisfaction surveys and after-sales support, discover and solve potential problems in a timely manner, and ensure continued customer satisfaction.
Provide value-added services: In addition to meeting basic needs, quality customer service should also provide value-added services to create more value and competitive advantage for customers. This may include support in technical training, product customization, design optimization and supply chain management to help customers improve product quality, reduce costs and improve market competitiveness.
To sum up, quality customer service is one of the keys for companies to win customer trust and loyalty. Through timely response, professionalism, customized services, continuous tracking and provision of value-added services, companies can continuously improve customer satisfaction, establish long-term and stable cooperative relationships, and achieve win-win development.
FAQs
What are Ceramic BGA Substrates?
Ceramic BGA Substrates are a special type of printed circuit board made of ceramic materials. It has high strength, excellent thermal conductivity and good mechanical stability, and is often used in high-performance and high-reliability electronic equipment, such as communication equipment, aerospace devices, etc.
What are the advantages of Ceramic BGA Substrates compared to traditional FR-4 circuit boards?
Compared with traditional FR-4 circuit boards, Ceramic BGA Substrates have higher thermal conductivity and mechanical strength, and can better resist temperature changes and mechanical stress. In addition, Ceramic BGA Substrates also have better high-frequency characteristics and flame retardant properties, making them suitable for a wider range of application scenarios.
What factors need to be considered when designing Ceramic BGA Substrates?
When designing Ceramic BGA Substrates, factors such as material selection, routing planning, thermal management and packaging technology need to be considered. In addition, the appropriate number of layers, plate thickness, size and other parameters need to be selected according to the requirements of the specific application scenario.
What is the typical process for manufacturing Ceramic BGA Substrates?
The typical process for manufacturing Ceramic BGA Substrates includes multiple steps such as raw material preparation, ceramic material molding, printing, sintering, processing and testing. Each step requires strict control and precise operation to ensure the quality and performance of the final product.
How to choose the right Ceramic BGA Substrates manufacturer?
Choosing the right Ceramic BGA Substrates manufacturer requires consideration of multiple factors, including product quality, lead time, customization capabilities, and customer service. It is recommended to conduct evaluation and comparison by referring to customer reviews, industry reputation, and manufacturer’s qualification certification.