Ceramic Packages for MEMS Sensors Vendor. We offer Ceramic package substrates. we also have the Ceramic Packages service.
Ceramic packaging is a key technology used to package MEMS sensors. It provides good mechanical support and environmental protection, protecting the sensor from the external environment. By using ceramic materials with high temperature stability and chemical stability, ceramic packaging can ensure the reliability and stability of MEMS sensors under harsh conditions, making them widely used in automotive electronics, industrial control, medical equipment and other fields.
What is a ceramic package?
Ceramic packaging is a key technology that is widely used to package microelectromechanical systems (MEMS) sensors, providing them with good mechanical support and environmental protection. In the field of modern science and technology, MEMS sensors have become indispensable components in many applications. They are able to sense, measure and process various physical quantities at the microscopic scale and convert them into electrical signals or other forms of output. However, as miniature devices, the sensitivity and vulnerability of MEMS sensors to environmental influences make their packaging critical.
Ceramic packaging provides the necessary mechanical support for MEMS sensors by providing a strong outer shell, protecting their internal structure from external shock and vibration. This kind of mechanical support not only helps maintain the performance stability of the sensor, but also extends its service life and reduces performance degradation or failure caused by external mechanical damage.
In addition to mechanical support, ceramic packaging can also provide effective environmental protection, protecting MEMS sensors from external environmental factors such as humidity, chemicals, dust, etc. Through reasonable design of packaging structure and material selection, ceramic packaging can prevent external impurities and liquids from entering the inside of the sensor, thereby ensuring that it operates stably and reliably in various working environments.
Overall, ceramic packaging plays a vital role in MEMS sensor manufacturing. It not only provides necessary mechanical support and environmental protection, but also ensures the performance stability and reliability of the sensor, thus providing solid guarantee and support for MEMS sensors in various application scenarios.
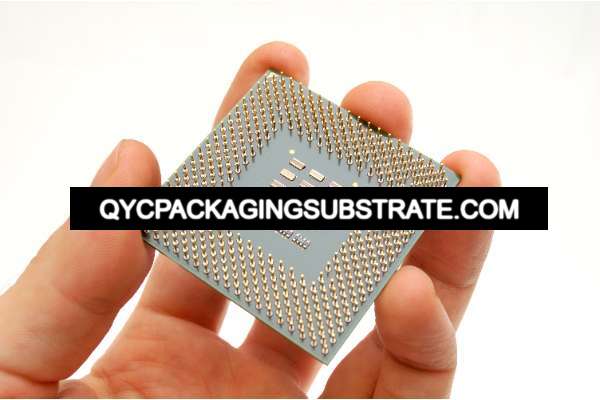
Ceramic Packages for MEMS Sensors
How to design a ceramic package?
Designing ceramic packages is a complex and critical process that directly affects the performance and reliability of MEMS sensors. The main steps in designing ceramic packages are detailed below:
First, engineers need to carefully select suitable ceramic materials. Commonly used ceramic materials include high-temperature stability materials such as aluminum oxide and silicon nitride. They have good mechanical strength and chemical stability and can meet the requirements of MEMS sensors in various environments.
The size of the ceramic package is determined based on the size and functional requirements of the MEMS sensor. This includes the overall dimensions of the package, the internal spatial layout, and the relative position between the device and the package. Reasonable size design can ensure a compact package structure without affecting the performance and sensitivity of the sensor.
Based on determining the size, engineers need to design a suitable packaging structure. This includes the package’s shell shape, internal space separation, interface locations, etc. Through three-dimensional modeling using CAD software, engineers can visually display the structure of the package and make necessary adjustments and optimizations.
After the structural design is determined, engineers need to further optimize the ceramic process parameters to ensure that the packaging manufacturing process is stable and reliable. This includes the optimization of sintering temperature, pressure, time and other parameters, as well as the selection and proportion of ceramic materials. Through simulation and experimental verification, engineers can find the optimal combination of process parameters to ensure packaging quality and consistency.
Through the above steps, engineers can accurately design a ceramic packaging structure that meets the performance requirements of MEMS sensors. These packaging structures not only protect the sensor from the external environment, but also improve the stability and reliability of the sensor, providing reliable solutions for various application scenarios.
What is the manufacturing process of ceramic packaging?
The manufacturing process of ceramic packages is a precise and complex process that goes through multiple key steps from raw materials to final products. First of all, the first step in manufacturing ceramic packages is raw material preparation. At this stage, high-quality ceramic materials need to be selected, often including high-temperature stable materials such as aluminum oxide and silicon nitride. These materials need to undergo strict quality control to ensure that their chemical composition and physical properties meet packaging requirements.
Next comes the shaping stage. During the molding process, the ceramic raw materials prepared in advance are processed into the required packaging structure. This is usually done through methods such as injection molding, extrusion or molding to ensure that the shape and dimensions of the package match the design requirements.
This is followed by the sintering stage, a crucial step in ceramic package manufacturing. In a high-temperature environment, the formed ceramic parts are sintered into a solid structure. During the sintering process, the temperature and atmosphere need to be strictly controlled to ensure that ceramic parts can be sintered evenly and fully, thereby obtaining excellent mechanical strength and chemical stability.
The last step is the surface treatment stage. At this stage, the surface of the ceramic package is machined and treated to meet specific functional and application requirements. This may include surface roughness adjustment, protective coating, drilling and other processes. The purpose of surface treatment is to improve the package’s wear resistance, corrosion resistance, and connectivity with other components.
Through precise process control and equipment operation, ceramic packaging manufacturers can ensure the high quality and stability of packaging products. Each manufacturing step must be strictly executed and subjected to comprehensive quality inspections to ensure that the final product meets customer requirements and expectations. This refined manufacturing process is one of the important reasons why ceramic packages are widely used in MEMS sensors and other high-end electronic devices.
How much does a ceramic package cost?
The cost of ceramic packaging is one of the key factors that need to be considered during the manufacturing process, and it is affected by multiple factors. Aspects such as size, complexity, material selection and manufacturing processes will have a direct impact on cost.
First of all, size is one of the important factors that determine the cost of ceramic packaging. Typically, the larger the package size, the greater the required ceramic materials and production costs. This is because large-size packages require more raw materials and production processes, and may require larger equipment to complete production tasks.
Secondly, the complexity of packaging will also directly affect the cost. Complex packaging designs may require more processes and technical requirements, resulting in increased production costs. For example, ceramic packages with multiple layers, complex structures, or special shapes often require more advanced manufacturing processes and more sophisticated equipment to complete.
Material selection is another important cost factor. Different types of ceramic materials can vary significantly in cost. Generally speaking, high-quality, high-temperature-stable ceramic materials cost more, while relatively lower-cost materials may sacrifice certain performance and reliability. Therefore, performance needs and cost budget need to be weighed when selecting packaging materials.
Finally, the manufacturing process also has a direct impact on the cost of ceramic packages. The use of advanced manufacturing processes and equipment often improves production efficiency and product quality, but may also increase manufacturing costs. Therefore, when formulating the manufacturing process and selecting manufacturing manufacturers, factors such as production efficiency, quality control, and cost control need to be comprehensively considered.
Overall, high-quality ceramic packages usually come with a relatively high cost, but the performance and reliability they bring are worth the investment. When formulating packaging solutions and budgets, factors such as size, complexity, materials, and manufacturing processes need to be fully considered to ensure an ideal balance between final cost and performance.
What materials are used in ceramic packages?
Ceramic packaging plays a vital role in MEMS sensor manufacturing, and its choice of material is critical to packaging performance and stability. Commonly used ceramic packaging materials mainly include high-temperature stability materials such as aluminum oxide and silicon nitride.
Alumina is a common ceramic material with excellent mechanical strength and chemical stability. Due to its good insulation properties and high temperature resistance, aluminum oxide packaging is widely used in demanding MEMS sensors. Its high-temperature stability enables alumina packaging to maintain stable performance in high-temperature environments, making it suitable for applications in automotive electronics, industrial control and other fields.
Another common ceramic packaging material is silicon nitride. Silicon nitride has excellent thermal conductivity properties and chemical stability, making it an ideal choice for high-performance MEMS sensor packaging. Silicon nitride packaging has good high temperature resistance and corrosion resistance, and can operate stably for a long time in harsh environments. Therefore, silicon nitride packaging is widely used in high-end MEMS sensors in aerospace, medical equipment and other fields.
In general, aluminum oxide and silicon nitride are commonly used high-temperature stability materials. They have good mechanical strength and chemical stability and are suitable for demanding MEMS sensor packaging. Choosing appropriate packaging materials is crucial to ensuring the performance and reliability of MEMS sensors, so reasonable selections need to be made based on specific application requirements and environmental conditions in packaging design.
Who makes ceramic packages?
The manufacturing of ceramic packages is usually carried out by professional packaging manufacturers or MEMS sensor manufacturers. These suppliers have extensive experience and advanced equipment to provide high-quality custom packaging solutions.
In the case of our company, we strive to become one of the leading suppliers in the field of ceramic packaging. We have advanced production lines and technical teams to meet customers’ various needs for ceramic packaging.
As a professional ceramic packaging manufacturer, our main advantages include:
Rich experience: We have many years of experience in the field of ceramic packaging manufacturing and have accumulated rich technical and industry knowledge.
Advanced Equipment: We have invested in advanced production equipment and technology to enable an efficient and precise manufacturing process.
Customized services: We can provide customized ceramic packaging solutions according to customer needs, including customization of size, materials, processes, etc.
Quality Assurance: We strictly control product quality to ensure that each batch of products meets customer requirements and standards.
Timely delivery: We have efficient production management and supply chain management systems to ensure on-time delivery of customer orders.
By working with us, customers can obtain high-quality, reliable ceramic packaging products to provide superior packaging protection for their MEMS sensors. We always take customer satisfaction as our primary goal and strive to become a long-term, trusted partner of our customers.
What are the five qualities of great customer service?
Excellent customer service is one of the keys to business success. It is not just a response to customers, but an ongoing relationship building and maintenance process. In the field of microelectromechanical systems (MEMS) sensor manufacturing, it is particularly important to provide quality service to customers. Here are five qualities of great customer service:
Rapid response: In the MEMS sensor manufacturing industry, it is crucial to respond to customer inquiries and concerns in a timely and effective manner. Customers may have various problems or emergencies that need to be resolved. A quick response can demonstrate the company’s professionalism and service attitude, and enhance customer trust and satisfaction.
Empathy: Treat customers’ needs with empathy and provide full understanding and care. In the manufacturing process of MEMS sensors, customers may face various challenges and pressures, and showing understanding and concern for the customer’s situation can shorten the distance between the customer and the enterprise and establish a good cooperative relationship.
Reliability: Consistently delivering on promises to ensure customer trust. In the manufacturing of MEMS sensors, ensuring product quality and delivery cycle is the basic responsibility of the company. Regarding customer needs, companies should adhere to high standards to ensure stable product quality and on-time delivery to win customer trust and long-term cooperation.
Communication skills: Maintain clear and transparent communication during the service process. Good communication skills are the basis for building effective partnerships. During the manufacturing process of MEMS sensors, providing customers with information such as project progress and technical solutions in a timely manner can increase the trust of both parties and reduce misunderstandings and unnecessary doubts.
Problem-solving skills: Actively solve problems and strive to achieve customer satisfaction. In the manufacturing of MEMS sensors, it is inevitable to encounter various problems and challenges, but how to proactively face and properly solve these problems is an important criterion for measuring the service level of an enterprise. Enterprises should promptly respond to customer complaints or opinions and actively seek solutions to ensure customer satisfaction and loyalty.
To sum up, high-quality customer service is crucial for MEMS sensor manufacturing companies. By demonstrating the five characteristics of rapid response, empathy, reliability, communication skills and problem-solving skills, companies can establish long-term and stable cooperative relationships with customers and jointly promote the development and progress of the industry.
Frequently Asked Questions
What are the differences between ceramic packaging and plastic packaging for MEMS sensors?
Ceramic packaging offers superior temperature stability and chemical resistance compared to plastic packaging, making it suitable for applications in harsh environments. While ceramic packaging tends to be more expensive, it provides enhanced durability and performance over plastic alternatives.
How long does it typically take to manufacture ceramic packaging for MEMS sensors?
The manufacturing timeline for ceramic packaging varies depending on factors such as size, complexity, and production volume. Generally, it can range from several weeks to a few months to complete the entire manufacturing process, including design, fabrication, and testing.
Are ceramic packaging materials environmentally friendly?
Ceramic packaging materials typically exhibit good environmental compatibility, with high recyclability and minimal impact on the environment. Additionally, ceramic materials are non-toxic and inert, making them suitable for eco-friendly applications.
How can I select a reliable manufacturer for ceramic packaging of MEMS sensors?
When choosing a manufacturer for ceramic packaging, consider factors such as technical expertise, manufacturing capabilities, quality assurance processes, and customer service. Look for companies with a proven track record in producing high-quality ceramic packages and offering tailored solutions to meet your specific requirements.