Ceramic Packaging Substrate Manufacturing, Not only to use BT base, ABF base, Rogers Base, High TG FR4 base, we also can use the Ceramic base materials to build the Packaging Substrate. Such as: 96 L2O3 Ceramic Substrates, ALN Ceramic Substrates. and other types Ceramic base materials.
Ceramic packaging substrates, as a key component of modern electronic devices that are not often noticed, play an integral role in reliability and performance. In the complex world of electronics, these substrates, constructed with advanced ceramic materials, serve as a solid foundation for integrated circuits and various components.
First, ceramic packaging substrates are silent supporters of electronic devices, with roles that go far beyond what is visible on the surface. These substrates not only provide mechanical support for electronic components, but also create an ideal environment for stable operation of circuits through their superior thermal conductivity properties. By utilizing advanced ceramic materials, these substrates perform exceptionally well in high temperatures, high frequencies and complex environments, making them ideal when facing challenging operating conditions.
Secondly, the key role of ceramic packaging substrates is reflected in the stable platform they provide for integrated circuits. This platform not only supports the physical structure of ICs, but also provides a reliable channel for the transmission of electronic signals. Through the use of ceramic materials, these substrates have excellent insulation properties, effectively preventing interference between electronic components, thus improving the performance and reliability of the entire circuit.
In addition, ceramic packaging substrates show unique advantages when facing the challenges of miniaturization and high integration. The special properties of its material allow the substrate to accommodate more components in a small space, enabling compact designs of electronic devices. This flexibility allows the application of ceramic packaging substrates in modern electronic devices to be widely expanded, from smartphones to medical equipment, all demonstrating its multi-faceted application value.
Overall, ceramic packaging substrates are an indispensable hero in the electronics world, and their critical role in the reliability, performance and miniaturization of integrated circuits and components allows modern electronic devices to operate efficiently. The clever use of design of these substrates and the selection of advanced ceramic materials provide electronic engineers with powerful tools and promote the continuous progress of science and technology. Therefore, behind the various electronic devices we use, ceramic packaging substrates silently play vital responsibilities, paving the way for the future of technology.
What are the types of ceramic packaging substrates?
Diverse ceramic packaging substrates, such as aluminum oxide and aluminum nitride, play distinctive roles in electronic engineering, each tailored to specific applications. Let’s delve into these ceramic substrate types to comprehend their characteristics and advantages.
Conversely, aluminum nitride substrates excel in thermal conductivity and chemical stability. Crucial for high-power density and high-frequency applications like radar systems, communications equipment, and power amplifiers, their low dielectric loss ensures strong performance in high-frequency circuits, contributing to the precision and stability of signal transmission.
Beyond aluminum oxide and aluminum nitride, an array of other ceramic packaging substrate variations exists. Meticulously designed to meet the demands of specific applications, these variants may differ in material composition, thermal conductivity, mechanical strength, providing engineers with a range of options to precisely align with project requirements.
Overall, the diversity of ceramic packaging substrates brings flexibility and innovation to the field of electronic engineering. Engineers need to carefully weigh various factors when selecting the appropriate substrate to ensure it can perform optimally in a specific application and provide a solid foundation for the reliability and efficiency of electronic devices.
What are the advantages of ceramic packaging substrates?
In the field of modern electronic device design and manufacturing, the use of ceramic packaging substrates is not only a choice, but a key decision, and its obvious advantages make it an ideal choice for many projects. From increased thermal conductivity to improved signal integrity, ceramic substrates offer compelling advantages in increasing the overall efficiency and reliability of electronic devices.
First, ceramic packaging substrates have excellent thermal conductivity. Ceramic substrates can transfer and disperse heat more efficiently than traditional alternatives. This property is critical for the ever-decreasing size and increasing power density of today’s electronic devices. By optimizing thermal management, ceramic substrates effectively reduce the operating temperature of electronic components and improve the stability and performance of the overall system.
Secondly, the improvement of signal integrity of ceramic substrates is also one of its eye-catching advantages. In high-frequency applications, signal transmission quality is critical to device performance. Ceramic substrates’ low dielectric losses and low signal propagation delays make them ideal for high-frequency circuits. This feature helps ensure accurate signal delivery, thereby improving the overall performance of the device.
In addition, ceramic packaging substrates offer excellent mechanical properties and durability. Its high strength and hardness make it resistant to physical damage that can occur in a variety of environments. This durability is especially critical for equipment operating in harsh conditions, such as automotive electronics, aerospace equipment, etc.
As electronic equipment continues to pursue thinner, lighter and smaller designs, the high degree of integration of ceramic substrates also shows unique advantages. Its thin design and flexible manufacturing process enable ceramic substrates to meet the requirements for space efficiency and design flexibility, providing more possibilities for innovation in electronic devices.
Overall, the advantages brought by choosing ceramic packaging substrates are manifold and comprehensive. From thermal management to signal transmission to mechanical performance and design flexibility, ceramic substrates provide a solid foundation for performance improvements and innovation in electronic devices. In future electronic engineering, ceramic packaging substrates will continue to play an important role and become an indispensable part in promoting technological progress.
Why choose ceramic packaging substrates over other board materials in a specific application?
In the field of electronic design, application-specific material selection is critical, and ceramic packaging substrates stand out in this regard as ideal for solving complex electronic design needs. The rationality of this choice is reflected in high-frequency applications, thermal management and miniaturization requirements.
Secondly, effective thermal management is a critical consideration in electronic design, especially in the face of escalating power consumption. Ceramic packaging substrates excel in this aspect due to their excellent thermal conductivity properties. In contrast to some conventional materials, ceramic substrates efficiently conduct and disperse generated heat, ensuring the stable operation of electronic components under high-load conditions. This makes ceramic substrates prevalent in high-power consumption equipment like power amplifiers and power modules, providing vital support for system reliability and performance.
Ceramic packaging substrates come in a range of materials, each with distinct pricing dynamics. Notably, aluminum nitride substrates typically command a higher price compared to aluminum oxide substrates. The selection process is further nuanced by project-specific demands, where material properties such as thermal conductivity and electrical characteristics play a crucial role. These specified requirements not only influence the choice of material but also contribute to the variability in material costs.
Furthermore, as the pursuit of electronic product miniaturization continues, ceramic packaging substrates emerge as an ideal choice owing to their exceptional mechanical properties. Characterized by high strength, hardness, and excellent bending and compression resistance, ceramic substrates play a pivotal role in designs aimed at miniaturization. This is particularly noteworthy in mobile devices, medical equipment, and other products that prioritize lightweight construction and exceptional performance, where the miniaturization advantages of ceramic substrates prove to be significantly impactful.
Therefore, in terms of high-frequency applications, thermal management and miniaturization needs, ceramic packaging substrates have become the first choice to solve complex electronic design needs due to their excellent electrical, thermal conductivity and mechanical properties. Whether you are pursuing higher performance, smaller size, or more reliable and stable electronic devices, you can benefit a lot from the choice of ceramic substrates. This choice not only provides electronic engineers with more design flexibility, but also promotes continuous innovation and development of electronic technology.
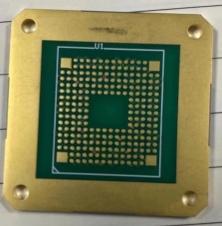
Ceramic Packaging Substrate
What is the manufacturing process of ceramic packaging substrates?
The manufacturing process of ceramic packaging substrates is a highly precise and complex project, which involves careful processing of two key components: motherboard and substrate. The individual steps of this manufacturing process are described in detail below.
Motherboard manufacturing
Material Selection: The first step in manufacturing a ceramic packaging substrate is selecting the appropriate material.
Lamination process: Selected materials are stacked layer by layer through a lamination process. Each layer is precisely engineered to ensure the final motherboard structure meets the requirements of the specific application.
This includes precision processing equipment and exquisite craftsmanship to ensure the motherboard has a high degree of precision and performance. Advanced process technologies, such as laser cutting and precision printing, are used in the manufacturing of motherboards to achieve precise layout of tiny structures and complex circuits.
Substrate manufacturing
Material selection: Similar to motherboards, the first step in manufacturing a substrate is selecting the appropriate material. The substrate is typically made from the same or similar high-purity ceramic material to ensure consistent performance characteristics throughout the package structure.
Manufacturing Process: The manufacturing process of the substrate involves precision machining of selected ceramic materials. This may involve steps such as cutting, drilling, and surface treatment to form the final substrate structure.
This includes a complete inspection of the structure’s appearance, dimensions and electrical performance. Any defects or substandard parts discovered are quickly repaired or eliminated to ensure superior reliability of the final ceramic packaging substrate.
Through the above steps, the manufacturing process of the ceramic packaging substrate is completed, and the final product has a high degree of thermal stability, electrical performance and structural strength, making it one of the indispensable core components in modern electronic equipment.
What are the applications of ceramic packaging substrates?
Ceramic packaging substrates have showcased a remarkable array of applications across diverse industries, owing to their outstanding performance and adaptability. From consumer electronics to communication systems and medical devices, these substrates play a pivotal role in the dynamic landscape of evolving technologies.
In the field of communications, ceramic packaging substrates also play a key role. Whether in antenna systems, radio frequency modules or communication base stations, ceramic substrates can meet high frequency and stability requirements. Its superior electrical characteristics make it the first choice for wireless communication equipment, helping to improve the performance and coverage of communication networks.
In addition, ceramic packaging substrates also play an important role in medical device manufacturing. Medical electronic devices have extremely high requirements for stability, durability and accuracy, and ceramic substrates excel in meeting these demands. They are widely used in medical imaging equipment, laser treatment equipment and vital signs monitoring devices, providing solid support for technological innovation in the medical field.
The versatility of ceramic packaging substrates is key to their wide application in different industries. The flexibility of its material selection and manufacturing process makes it suitable for a variety of environments and working conditions. Moreover, ceramic substrates can also meet the trends of miniaturization and lightweight, making them widely used in modern electronic devices.
Overall, ceramic packaging substrates are used in a wide range of applications, from personal consumer electronics to communications infrastructure to the medical field. Its successful application in various industries highlights its unique position in electronic engineering and injects vitality into the constantly innovative technology field. With the advancement of technology, it is believed that ceramic packaging substrates will continue to play a key role in promoting the development of the electronics industry in a more advanced and reliable direction.
How to obtain high-quality ceramic packaging substrates?
When looking for a high-quality ceramic packaging substrate supplier, choosing a reliable partner is crucial, as this is directly related to the success of the PCB engineering project. In the vast supplier market, understanding how to accurately select suppliers will help ensure that the project proceeds smoothly and product quality reaches the expected level.
First, in order to find a high-quality ceramic packaging substrate supplier, you can consider the following key factors:
Industry reputation
Finding a supplier with a good reputation within the industry is a top priority. A company’s reputation directly reflects the quality of its products and service levels. A vendor’s reputation can be assessed by looking at customer reviews, industry forums, and peer recommendations.
Technical skills
The technical capabilities of the supplier are an important consideration in the selection process. Ensure that suppliers have advanced technical equipment and professional technical teams to ensure that the manufacturing of ceramic packaging substrates meets the latest industry standards and quality requirements.
Product quality
Carefully review suppliers’ product quality standards and production processes. Ask your supplier to provide samples or visit their production facilities to ensure that the ceramic packaging substrates they produce meet your quality standards.
Delivery time
Timely delivery is critical to the progress of engineering projects. Choose a supplier that can deliver products on time to avoid unnecessary delays and project risks.
Cost-effectiveness
Take cost factors into consideration to ensure the supplier’s price is reasonable and compare with other competitors. Be careful not to just pursue low cost and ignore product quality and service.
We emphasize choosing our company as a reliable supplier of ceramic packaging substrates in the following ways:
Company advantage
Highlight the company’s advantages in the industry, including advanced manufacturing technology, rich experience and excellent product quality. Emphasize the company’s position as an industry leader to increase customer trust.
Pledge
Choosing our company as a reliable supplier will lay a solid foundation for the success of PCB engineering projects.
How is the quotation of ceramic packaging substrate affected?
When selecting a ceramic packaging substrate, it is critical to understand the factors behind its quote. The price of ceramic substrates is affected by many factors, which directly affect the cost of PCB engineering projects. Here are some key factors that have a profound impact on ceramic packaging substrate prices
Manufacturing process
The process of manufacturing ceramic packaging substrates is complex, and different manufacturing processes may require different equipment and technologies. Advanced manufacturing processes and technologies tend to increase manufacturing costs, therefore, choosing a specific process will directly affect the final price of ceramic substrates.
Size and number of layers
The size and number of layers of a ceramic packaging substrate are important factors that determine its price. Substrates with larger sizes and more layers generally require more materials and more complex manufacturing processes, and therefore are more expensive to manufacture.
Skills requirement
Some applications have higher technical requirements for ceramic substrates, such as high-frequency applications or use in special environments. Meeting these technical requirements may require more precise manufacturing and higher quality materials, increasing the overall cost of the substrate.
Customized needs
If a project requires a custom ceramic substrate, such as a special layer sequence, shape or surface treatment, this will increase manufacturing complexity and cost. Customized production often drives up the price of a product.
The quotation of ceramic packaging substrates is a complex and multi-layered process, affected by many factors. Understanding these factors is critical to developing a sound project budget. When selecting ceramic substrates, the project team should weigh various factors to ensure that the selected product meets the project requirements and strikes a balance between cost and performance. Such a comprehensive understanding will help ensure successful project implementation.
Hopefully, the above insights provide readers with a general understanding of ceramic packaging substrate price formation to make informed decisions in PCB engineering projects.
Frequently Asked Questions (FAQs)
The following are answers to some frequently asked questions to help readers better understand and apply ceramic packaging substrates.
What is the difference between ceramic packaging substrates and traditional substrates?
This makes them more suitable in high-performance electronic devices, especially in scenarios where high-frequency signal processing and intensive thermal management are required.
Why are ceramic packaging substrates chosen in some applications?
The choice of ceramic packaging substrate depends on the specific needs of the application. In high-frequency communication equipment, ceramic substrates can provide lower signal loss; and in high-temperature environments, they perform well to ensure the reliability of electronic components.
Is ceramic packaging substrate suitable for miniaturization design?
Yes, ceramic substrates are ideal for miniaturized designs due to their high degree of integration and miniaturization. Not only do they offer higher density of electronic components, they also meet extreme requirements on device size and weight.
Is the manufacturing of ceramic packaging substrates complicated?
The manufacturing of ceramic packaging substrates involves a series of advanced processes and technologies, including material selection, lamination processes, and quality inspection and testing. Although complex, these steps ensure the high quality and performance of the final product.
How to choose a suitable ceramic packaging substrate supplier?
Choosing the right ceramic packaging substrate supplier is critical. Ensure suppliers have extensive experience, high-quality manufacturing processes and reliable quality inspection measures to meet the project’s technical and time requirements.
What is the cost of ceramic packaging substrates?
The cost of ceramic packaging substrates is affected by a variety of factors, including the material selected, the complexity of the manufacturing process, and order volume. When considering costs, these factors need to be taken into consideration and full communication with suppliers is required to obtain an accurate quote.
What are the applications of ceramic packaging substrates in medical equipment?
Ceramic packaging substrates are widely used in medical equipment, such as medical imaging equipment in high-frequency signal transmission and high-temperature environments. Its reliability and performance make it one of the top choices in medical electronics.
These questions and answers provide insight into some key aspects of ceramic packaging substrates, helping readers better understand the applications and benefits of this technology. If readers have any other questions, we welcome further discussion.