What exactly are Chip Substrates?
Chip Substrates Manufacturer. We use advanced Msap and Sap technology to produce the High multilayer interconnection bga substrates from 4 to 20 layers.
In the field of modern electronics, Printed Circuit Boards (PCBs) play a vital role. They are the core components of electronic equipment and are responsible for connecting and supporting various electronic components, such as resistors, capacitors, integrated circuits, etc. PCBs provide a structured platform that makes the connection between electronic components simple and reliable, thereby realizing the function of the circuit. However, getting the most out of PCBs relies on one key component: Chip Substrates.
Chip Substrates are a basic material used to secure chips (integrated circuits) to PCBs. They provide support and connections for the chip, allowing it to communicate with other components and transmit power and signals through the circuit board. Simply put, Chip Substrates are the medium for integrating chips into PCB designs, providing a solid foundation for the functionality of modern electronic devices.
In modern electronic devices, such as smartphones, tablets, computers, and automotive electronic systems, the use of chips is increasingly common because they enable more complex and efficient functions. As a key component for integrating these chips into devices, Chip Substrates play an indispensable role in the field of modern electronics.
Considering the wide application of PCBs and the key role of Chip Substrates, we can conclude that in today’s electronic field, PCBs and Chip Substrates are closely related. Together they form the core of modern electronic equipment, driving the progress of science and technology and Implementation of innovation.
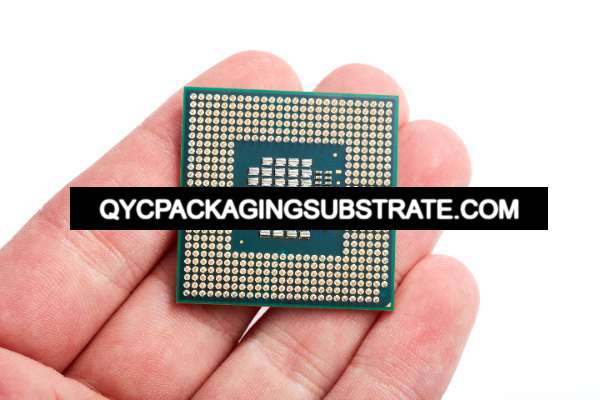
Chip Substrates
Through an in-depth understanding of Chip Substrates, we can better understand the working principles of modern electronic devices, providing an important foundation for the design and manufacture of more advanced and reliable electronic products. Therefore, for anyone involved in electronic engineering or interested in electronic devices, awareness of Chip Substrates is crucial.
How to design PCB with Chip Substrates?
Designing a PCB with Chip Substrates requires engineers to consider multiple factors. From layout to material selection to optimization of signal integrity, every step is critical.
First and foremost, layout design is one of the first considerations during the design process. Engineers need to determine the location and orientation of the chip to maximize signal transmission and power distribution. Reasonable layout can minimize signal interference and crosstalk and ensure the stability and reliability of circuit performance. In addition, the layout design should also take heat dissipation needs into consideration to ensure that the chip can effectively dissipate heat during operation and avoid performance degradation or failure caused by excessive temperature.
Secondly, material selection is critical to the success of the design. Engineers need to select Chip Substrates materials suitable for specific application scenarios, considering factors such as the material’s thermal conductivity, dielectric constant, mechanical strength and high temperature resistance. Different application scenarios may require different materials. For example, high-frequency applications usually require materials with lower dielectric constant and loss to ensure the stability and reliability of signal transmission.
Finally, signal integrity optimization is an important part of the design process. Engineers need to minimize signal delay, waveform distortion, and crosstalk through reasonable layout design and circuit connections. In addition, proper ground design and power distribution are also one of the key factors to ensure signal integrity. Engineers can improve the performance and reliability of their circuits by optimizing signal integrity through the use of techniques such as ground planes, differential signaling, and good power supply decoupling.
In summary, designing PCBs with Chip Substrates requires engineers to comprehensively consider multiple factors such as layout, material selection, and signal integrity. Through reasonable design and optimization, circuit performance can be maximized and stability guaranteed.
What is Chip Substrates’ PCB manufacturing process?
Chip Substrates’ PCB manufacturing process involves a series of critical steps, each stage must be handled with precision and detail to ensure the final product meets high quality standards.
Design Verification: The first step in manufacturing a Chip Substrates PCB is to perform design verification. This includes careful review and validation of circuit layout, signal paths, and material selection to ensure the design meets specifications and performance requirements.
Material Procurement: Before manufacturing Chip Substrates’ PCB, suitable substrate materials, metallization layers, and other necessary components need to be procured. The quality and characteristics of materials are critical to the performance of the final product.
Substrate preparation: Next, the substrate material needs to be prepared, including cleaning and surface preparation. This ensures that patterns and conductive paths can be successfully printed onto the substrate in subsequent steps.
Circuit imaging: After the substrate preparation is completed, the circuit pattern is imaged onto the substrate surface. This is usually achieved through photolithography techniques, where light-sensitive coatings and masks are used to protect or expose the desired areas.
Etching: After imaging is complete, the substrate is exposed to a chemical etching solution to remove areas not protected by the photosensitive paint. This step is related to the accuracy and clarity of the pattern and needs to ensure the control and monitoring of the etching process.
Metallization: After etching, the conductive paths on the surface of the substrate need to be metallized, usually using gold plating or other metallization techniques. This ensures the reliability and conductivity of the circuit.
Assembly: Finally, the electronic components are mounted onto the Chip Substrates’ PCB, usually via soldering or other connection methods. The assembly process requires precision operations and strict quality control to ensure components are installed correctly and connections are reliable.
Through the above steps, Chip Substrates’ PCB can achieve efficient production while ensuring quality. Each stage requires precision and meticulous handling to ensure the final product meets design requirements and industry standards.
What is the manufacturing process of Chip Substrates?
The manufacturing process of Chip Substrates involves a variety of advanced technologies and processes, including key steps such as photolithography, chemical etching and metallization. These steps ensure that complex patterns and conductive paths are created on the surface of the substrate, providing a reliable foundation for chip mounting and connection.
First, the process of manufacturing Chip Substrates usually starts with the preparation of the substrate. The substrate can be of a variety of materials, such as fiberglass-reinforced epoxy (FR-4), polyimide (PI), or ceramic. Selecting the appropriate substrate material depends on the application requirements and performance needs.
Next, photolithography is used to coat the substrate surface with photoresist, and a photomask is used to project the desired pattern onto the photoresist. This step determines the final chip layout and formation of conductive paths. The precision and accuracy of photolithography techniques are critical to the quality of patterns.
Subsequently, chemical etching is performed. During this stage, the substrate surface is exposed to a chemical etchant, which strips away the portions not protected by the photoresist. This allows pre-designed patterns and conductive paths to appear on the substrate surface. The parameters and conditions of chemical etching require precise control to ensure the clarity and accuracy of the pattern.
After chemical etching is complete, metallization is next. This step involves depositing a metal layer on the surface of the substrate. Commonly used metals include copper or silver. The metal layer fills the pattern and conductive paths, forming electrical connections and conductive pathways. Metallization uniformity and adhesion are critical to chip stability and performance.
Finally, after surface treatment and final inspection, Chip Substrates are ready for use. Each step in these manufacturing processes requires strict quality control and precise process control to ensure that the quality and performance of the final product meet requirements.
In general, the manufacturing process of Chip Substrates involves a series of complex processes and technologies, from photolithography to chemical etching to metallization. Each step is critical and directly affects the quality and performance of the final product.
How much do Chip Substrates cost?
When considering the cost of Chip Substrates, there are several key factors to consider. The first is material cost. Different types of substrate materials will have an impact on cost. For example, high-performance materials such as ceramics will be more expensive than regular fiberglass-reinforced epoxy (FR-4). Second is the complexity of the manufacturing process. Some special processes or high-precision requirements may increase manufacturing costs. In addition, manufacturing volume is also an important factor. High-volume production can reduce unit costs, while small-volume production can result in higher costs.
Beyond these factors, whether high-performance Chip Substrates are worth the investment depends on the specific application and needs. For some areas with extremely high performance and reliability requirements, such as the aerospace, medical device or automotive industries, investing in high-performance Chip Substrates may be necessary. These industries have extremely high requirements for circuit board stability and long-term reliability, and high-performance Chip Substrates can usually meet these requirements. In addition, high-performance Chip Substrates may also provide better signal transmission, thermal management and durability, thereby extending device life and improving performance.
However, in some other application scenarios, such as consumer electronics or low-cost products, investing in high-performance Chip Substrates may not be necessary. In these cases, cost effectiveness may be more important and choosing a relatively lower cost substrate may be more appropriate. Therefore, when deciding whether to invest in high-performance Chip Substrates, factors such as cost, performance requirements, industry standards, and expected product life and use environment need to be considered.
To summarize, the cost of Chip Substrates is affected by a variety of factors, and while high-performance Chip Substrates may be worth the investment in some areas, they may not be necessary in others. Therefore, specific application needs and budget constraints need to be carefully evaluated before making a decision.
What materials are Chip Substrates typically made of?
Chip Substrates are an important component of printed circuit boards (PCBs), and their material selection is critical to circuit performance and reliability. Materials commonly used to make Chip Substrates include:
FR-4 (fiberglass reinforced epoxy): FR-4 is one of the most common Chip Substrates materials and has good mechanical strength and heat resistance. Its advantages include low cost, easy processing, corrosion resistance and good insulation properties. FR-4 is suitable for most general electronic applications such as consumer electronics and communications equipment.
Polyimide: Polyimide is a high-performance engineering plastic with excellent high temperature resistance, chemical stability and mechanical strength. The main advantage of using polyimide materials for Chip Substrates is its stability in high-temperature environments, making it suitable for applications in aerospace, automotive electronics, and medical equipment.
Ceramic: Ceramic materials have good thermal conductivity and high temperature resistance, so they are suitable for applications that require strict thermal management. The main advantages of using ceramic materials for Chip Substrates are their high-frequency characteristics and excellent signal integrity, making them suitable for high-frequency applications such as radio frequency (RF) and microwave circuits.
Each material has its own unique properties and range of applications. Selecting the appropriate Chip Substrates material depends on specific application needs and performance requirements. When deciding on materials, factors to consider include operating environment temperature, frequency requirements, mechanical strength, cost, and manufacturing processes.
Overall, Chip Substrates material selection is critical to PCB performance and reliability, and engineers need to consider various factors based on specific project needs to ensure the most suitable material is selected.
Who are the major players in Chip Substrates manufacturing?
In the modern electronics industry, the main players in the manufacturing of Chip Substrates include a series of suppliers, of which our company is a prominent representative. As one of the important players in this field, the company is committed to providing high-quality Chip Substrates products to global customers and maintaining a leading position in technological innovation, quality management and customer service.
As one of the suppliers, our company focuses on innovation and technological leadership. We continuously invest in R&D funds to develop new manufacturing processes and materials to meet changing market demands. Through continuous technological innovation, the company is able to provide Chip Substrates products that comply with the latest industry standards and provide reliable basic support for customers’ designs.
In addition to technological innovation, our company also focuses on quality management. We adopt strict quality control standards and strictly control every aspect from raw material procurement to final product delivery to ensure that our products meet our customers’ quality requirements and expectations. By continuously improving and optimizing the production process, the company strives to improve product quality and production efficiency and provide customers with better products and services.
In addition, the company also focuses on cooperation and communication with customers. We actively listen to our customers’ needs and feedback, tailor solutions for customers, and provide timely technical support and after-sales service. By establishing long-term and stable cooperative relationships with customers, the company continues to improve customer satisfaction and achieve win-win development.
Overall, as one of the major players in the field of Chip Substrates manufacturing, the company is committed to providing customers with high-quality, high-performance products and solutions through technological innovation, quality management and continuous improvement of customer service to help customers Succeed in a competitive market.
What are the key attributes of excellent customer service?
In today’s highly competitive business environment, providing excellent customer service has become the key for companies to win customer trust and maintain competitive advantage. Here are the key attributes that build great customer service:
Responsiveness: Customers expect prompt feedback and support when they encounter problems or have questions. An excellent customer service team should respond to customer needs quickly and efficiently, reducing waiting times and improving customer satisfaction.
Expertise: Customers often seek professional advice and solutions. Team members who excel in customer service should have in-depth product knowledge and industry expertise and be able to provide accurate, comprehensive information and advice to help customers solve their problems.
Reliability: Customer trust is the cornerstone of business success. An excellent customer service team should earn the trust of customers with consistent performance and reliable commitment, ensure timely delivery of products and services, and provide support when customers need it.
Flexibility: Every client is unique and their needs and requirements may vary. An excellent customer service team should be flexible and provide personalized solutions based on the customer’s specific situation and needs to meet customer expectations.
Customer focus: An excellent customer service team should always put customers first, pay attention to customer needs and feedback, actively listen to customer opinions and suggestions, continuously improve products and services, and provide customers with a better experience.
Through customer service that embodies the above key attributes, companies can win the trust and loyalty of customers, build a good brand reputation, and achieve sustained business growth and success.
FAQS
How does the choice of Chip Substrates affect PCB performance?
The choice of Chip Substrates directly affects the performance of PCB. Quality Chip Substrates can provide better thermal management and signal integrity, thereby improving circuit stability and reliability. Choosing appropriate Chip Substrates can also reduce the complexity of circuit layout and improve circuit integration.
How complex is the manufacturing process for Chip Substrates?
The manufacturing process of Chip Substrates typically involves multiple complex steps, including substrate preparation, pattern imaging, chemical etching, and metallization. These steps require highly sophisticated equipment and technology, and the parameters and conditions of each step need to be strictly controlled to ensure the quality and performance of the final product.
How are the costs of Chip Substrates calculated?
The cost of Chip Substrates is usually determined by multiple factors, including material cost, manufacturing process complexity, design requirements and manufacturing volume. High-performance chip substrates may come at a higher cost, but in certain applications the investment is often worth it because they provide better performance and reliability.
How to choose Chip Substrates that fit your project needs?
When selecting Chip Substrates that fit your project needs, there are several factors to consider, including circuit layout, thermal management requirements, signal integrity requirements, and cost budget. The best option is often to work with a supplier to create a custom design based on the specific requirements and goals of the project.
Who are reliable Chip Substrates suppliers?
There are many reliable Chip Substrates suppliers in the market, such as Shinko Electric Industries, Unimicron Technology Corporation, and Ibiden Co., Ltd, etc. These suppliers usually have extensive experience and advanced manufacturing technology, and can provide high-quality products and professional technical support.