CPCORE Structure substrates Manufacturer. the Package Substrate will be made with BT base and Showa Denko and Ajinomoto High speed materials. or other types Structure Structure materials.
Packaging substrates are essential components in contemporary electronic devices, serving crucial functions in supporting, interconnecting, and safeguarding chips and other electronic elements. As a member of CPCORE structure manufacturers, we grasp the significance of packaging substrates within the electronics sector. They are not merely support materials; instead, they serve as the foundational element that links diverse components and ensures stability and dependability.
The role of packaging substrates can be likened to the skeletal framework of an electronic device. They furnish a stable platform for chips and other components, facilitating efficient operation and inter-component communication. Utilizing conductive materials like copper foil, packaging substrates establish electrical connections, while their base material and covering layers provide mechanical support and shield components from external damage or interference.
Within our CPCORE structure manufacturing process, we are dedicated to producing diverse packaging substrates tailored to meet varying customer requirements. Whether rigid or flexible, thick film or thin film substrates, we customize production to ensure adherence to the highest quality standards and performance criteria.
The significance of packaging substrates extends beyond their supportive and protective roles; they find extensive application across a spectrum of electronic devices, including communication equipment, automotive electronics, consumer electronics, and medical devices.
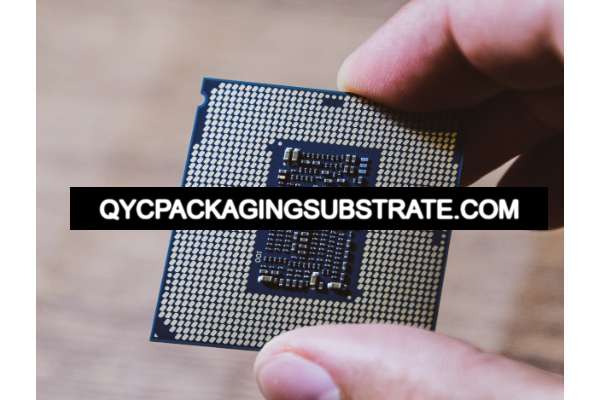
CPCORE Structure substrates Manufacturer
We carefully oversee every aspect of the manufacturing process for packaging substrates, ensuring that the quality and performance of the product meet the highest standards expected by our customers. From selecting materials to monitoring production processes, we implement rigorous controls to guarantee that each packaging substrate meets stringent requirements.
In summary, packaging substrates are integral to modern electronic devices, playing a pivotal role in supporting, connecting, and safeguarding chips and electronic components. As a CPCORE structure manufacturer, we remain committed to delivering high-quality, dependable packaging substrate products and services to advance sustainable development within the electronics industry.
What types of packaging substrates are available for CPCORE structures?
CPCORE structure manufacturers provide various types of packaging substrates to meet the needs of different application scenarios. These packaging substrates include, but are not limited to:
Rigid substrates are composed of tough materials, offering strong mechanical properties and stability. They excel in applications demanding robustness and dimensional steadiness, such as computer motherboards, servers, and industrial control systems.
Thick film substrates feature thicker insulating and conductive layers, catering to applications requiring superior electrical performance and thermal regulation. They find common use in sectors like power modules, power supplies, and automotive electronics.
Thin film substrates, made from lightweight materials, offer enhanced flexibility and are suitable for applications with strict size and weight limitations, such as mobile devices, medical equipment, and drones.
These diverse packaging substrate types are tailored to specific material properties and manufacturing processes, ensuring they meet the varied needs of different application scenarios. As a CPCORE structure manufacturer, our commitment lies in furnishing customers with top-quality, varied packaging substrate products to support their innovation and advancement.
What are the advantages of packaging substrates?
Compared with other boards, packaging substrates have many advantages in the electronics industry. These advantages make them an indispensable key component in modern electronic equipment. The following are the main advantages of packaging substrates:
First, the packaging substrate provides good electrical connection and conduction properties. Through its well-designed structure, the packaging substrate can effectively transmit current and signals, ensuring the normal operation of electronic devices. Its excellent electrical characteristics provide reliable basic support for various application scenarios.
Secondly, the packaging substrate serves as a sturdy foundation, providing reliable mechanical support and safeguarding electronic components against damage from vibrations and shocks. It effectively shields and extends the lifespan of these components.
Thirdly, the packaging substrate boasts superior integration and performance. Its adaptable design enables the accommodation of multiple chips and components, fostering high circuit integration levels that enhance device functionality. This integrated approach also contributes to size and weight reduction, bolstering the product’s competitive edge.
Whether it is traditional soldering packaging or advanced microelectronic packaging, packaging substrates can meet different manufacturing needs. Its flexible design and manufacturing process make packaging substrates a universal solution in the electronics industry, providing reliable technical support for various applications.
In summary, packaging substrates have become an indispensable part of modern electronic equipment due to their good electrical connection and conductive properties, reliable mechanical support and protection, high integration and performance, and suitability for various packaging technologies and processes. missing key components.
Why choose packaging substrate?
Choosing a packaging substrate offers many advantages over other boards that are critical in the design and manufacturing of modern electronic devices. Here are the main reasons why packaging substrates are chosen:
First, the packaging substrate provides higher integration and performance. Because the packaging substrate can accommodate multiple chips and other electronic components, it becomes possible to achieve more functionality and performance in the same space. This high level of integration makes packaging substrates ideal for designing more complex electronic systems.
Packaging substrates offer several benefits in electronic device design and manufacturing. They facilitate higher integration and performance by enabling compact layouts. These substrates ensure reliable electrical connections through precise wiring and soldering techniques, crucial for stability in high-frequency and high-power applications. Additionally, they provide robust mechanical support and protection with multi-layer construction, safeguarding against environmental and mechanical damage. Moreover, packaging substrates accommodate various packaging technologies, from traditional surface mount to advanced three-dimensional methods, offering flexibility in manufacturing processes. In essence, packaging substrates are essential components in modern electronics, offering integration, reliability, protection, and adaptability across diverse applications.
What is the manufacturing process of packaging substrates?
The manufacturing process of packaging substrates is complex and involves several sequential stages. It starts with the design phase, during which engineers conceptualize the substrate layout and connections based on customer specifications. Factors such as circuit complexity, wiring tightness, and component placement are carefully considered during this phase.
Following design, the material preparation phase ensues, during which suitable substrates and metal layers are chosen and treated accordingly. Substrate selection significantly impacts electrical and mechanical properties, necessitating meticulous screening and testing.
Subsequently, the lamination process ensues, where pre-treated substrates and metal layers are stacked per design specifications, then subjected to heat and pressure for consolidation. This step ensures the structural integrity of the substrate, laying a robust foundation for subsequent processing.
Critical to the process is copper foil processing, where copper foil is tailored through cutting, punching, and etching to form requisite circuit connections and conductive pathways. Precision and quality in this phase directly influence electrical performance and substrate reliability.
Following copper foil processing, the solder mask stage follows, involving the application of a protective solder mask to the substrate surface. This layer not only prevents circuit shorting but also furnishes additional mechanical support, enhancing substrate longevity.
Finally, the process culminates in final processing and inspection, where substrates undergo meticulous scrutiny to verify compliance with specifications and quality standards. This encompasses checks for intact circuit connections, clear copper foil, and precise dimensions.
In summary, the manufacture of packaging substrates demands advanced technology and expertise to deliver products aligning with customer expectations and requirements.
In what application fields are packaging substrates widely used?
Packaging substrates are integral components in modern electronic devices, serving crucial roles across diverse applications. Packaging substrates play a vital role in enhancing connectivity and data transmission efficiency across a range of communication equipment, including base stations and modules for mobile, satellite, and network systems. In automotive electronics, they enable centralized control over diverse functionalities like engine management, safety protocols, and in-car entertainment systems, thereby improving overall vehicle performance and passenger comfort. Moreover, in consumer electronics such as smartphones, tablets, and televisions, packaging substrates facilitate the integration of multiple functions and components, thereby bolstering product capabilities and intelligence.Moreover, they find extensive use in medical equipment like pacemakers and imaging devices, ensuring stable electrical connections and data transmission for reliable medical operations. Additionally, in industrial automation and control systems, packaging substrates enable the automation and intelligence of production processes, offering high reliability and durability in harsh industrial environments. Overall, packaging substrates play a vital role in enhancing performance and functionality across communication, automotive, consumer electronics, medical, and industrial control sectors.
Where can I find CPCORE package substrates?
As a supplier to our company, accessing information about our diverse range of packaging substrates is convenient through various channels. Our commitment lies in delivering tailored solutions to global customers across a multitude of application fields.
Primarily, you can explore our packaging substrate products on our official website. There, you’ll find comprehensive details, specifications, and technical support information, all presented in a user-friendly format for easy browsing and learning about our product portfolio.
Furthermore, our dedicated sales team is readily available to assist you. Reach out to our sales representatives via phone, email, or online chat to inquire about packaging substrates, including pricing, delivery timelines, and customization options. The sales team is devoted to providing professional consultations and services, ensuring your satisfaction with our products and solutions.
In summary, as suppliers of CPCORE structures, our packaging substrate products are accessible through various channels. Whether you choose to buy from our official website, sales team, or partner channels, rest assured you’ll receive top-notch products and professional service to fulfill your requirements.
How is the quotation of packaging substrate calculated?
Quoting packaging substrates is a complex process influenced by various factors. As a manufacturer specializing in CPCORE structures, we understand our customers’ concerns regarding pricing and aim to provide clarity on how quotations are determined.
Firstly, the size of the packaging substrate significantly impacts its price. Generally, larger substrates require more raw materials and entail higher production costs, rendering them more expensive compared to smaller ones.
Secondly, the choice of material is pivotal in pricing packaging substrates. Different materials and metal layers incur distinct costs, and specialized materials may necessitate additional expenses due to unique handling requirements.
Additionally, the production process plays a crucial role in pricing. Diverse processes may involve varied equipment, technologies, and labor costs. Advanced techniques might entail more intricate operations, thereby escalating production expenses.
Moreover, customer-specific requirements influence pricing. Customized needs or supplementary services, such as special solder mask treatment or testing, contribute to the overall quotation.
Overall, packaging substrate pricing results from a comprehensive evaluation of factors including size, material, process, and customer demands. We encourage customers to provide project specifications for detailed quotation information.
Frequently Asked Questions (FAQS)
How can I contact CPCORE Structure Manufacturer to inquire about package substrates?
You can easily contact CPCORE Structure Manufacturer through our official website or by reaching out to our sales team via email or phone. We are committed to providing prompt and informative assistance to address your inquiries regarding package substrates.
What advantages does Package Substrate offer over other board types?
Package Substrates have several advantages, including superior electrical connectivity, reliable mechanical support and protection, high integration capabilities, and compatibility with various packaging technologies and processes.
Why should one choose Package Substrate over alternative boards?
Choosing Package Substrate offers benefits such as higher integration levels, more reliable electrical connections, better mechanical support and protection, and suitability for a wide range of packaging technologies and process requirements.
How are the quotes for Package Substrate determined?
The pricing of Package Substrate depends on factors such as size, materials, and manufacturing processes. Customers can obtain detailed quotes by reaching out to CPCORE Structure Manufacturer’s sales representatives.