What is DIP Package Substrate?
DIP Package Substrate Manufacture. we can produce the best samllest bump pitch with 100um, the best smallest trace are 9um. and the smallest gap are 9u. the best smallest via size are 50u. we also offer DIP package service.
DIP Package Substrate, that is, dual in-line packaging substrate, is an important component widely used in the field of electronic packaging. It plays the role of providing support for integrated circuits and other electronic components. Its unique dual-in-line design allows electronic components to be efficiently installed in it, thereby achieving efficient assembly and reliable electrical connections.
DIP Package Substrate is usually made of insulating materials such as FR-4 fiberglass composite or ceramic materials. Their design allows electronic components to be connected to the substrate via pins or leads on both sides, creating a dual-column arrangement. This design provides solid support and reliable connections, allowing electronic components to operate stably in different application scenarios.
DIP Package Substrate has a wide range of applications in the electronics industry, including consumer electronics, automotive electronics, industrial control and communication equipment and other fields. Whether it is used to manufacture smartphones, computer equipment or automotive control modules, DIP Package Substrate plays a key role.
Overall, DIP Package Substrate not only provides a solid platform to support electronic components, but also provides flexibility and reliability for the design and manufacturing of electronic products. Through its dual in-line design, DIP Package Substrate achieves efficient assembly and reliable electrical connections, thus playing an indispensable role in the electronic packaging process.
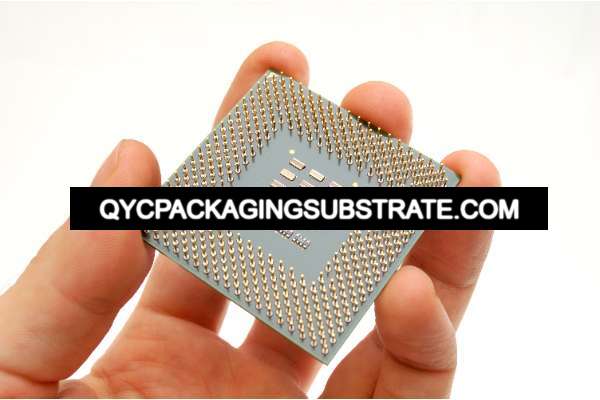
DIP Package Substrate
What types of DIP Package Substrate are there?
What types of DIP Package Substrate are there? DIP Package Substrate is a packaging substrate widely used in the field of electronic packaging, with different materials and configurations to meet various application needs. Common types include FR-4 DIP Substrate, Ceramics DIP Substrate and Metal Core DIP Substrate. Each type has its own unique properties, including thermal conductivity, dielectric strength and dimensional stability.
FR-4 DIP Substrate is one of the most common types. It is a glass fiber reinforced epoxy resin substrate with good mechanical strength and thermal stability. This material’s DIP Substrate is suitable for most general applications, providing reliable electrical performance and cost effectiveness.
Ceramics DIP Substrate is another common type, made from ceramic materials. This type of DIP Substrate has excellent thermal conductivity and dielectric strength and is suitable for high temperature, high frequency and high power applications. They are often used in demanding environmental conditions, such as in automotive electronics and aerospace.
Metal Core DIP Substrate is a DIP Substrate type with a metal core. The metal core provides better thermal conductivity, making it particularly suitable for high-power electronic devices that require excellent heat dissipation. Metal Core DIP Substrate is commonly used in fields such as LED lighting, power modules and electric vehicles.
To sum up, there are many types of DIP Package Substrate, each type has different characteristics and applicable scenarios. It is critical to select the type of DIP Substrate that suits your specific application needs to ensure the performance and reliability of your electronic device.
What are the advantages of using DIP Package Substrate?
There are multiple advantages to using DIP Package Substrate including enhanced thermal conductivity, improved electrical insulation, compact size, and enhanced mechanical strength. Let’s explore these aspects one by one:
First of all, DIP Package Substrate has outstanding performance in enhancing thermal conductivity performance. In high-temperature environments, the performance of electronic devices may be severely affected, but the design of DIP Package Substrate can effectively conduct heat to the external environment, thereby ensuring that the device maintains good performance and stability in high-temperature environments.
Second, DIP Package Substrate features improved electrical insulation, which helps reduce the risk of short circuits and signal interference. Good electrical insulation properties mean that the electrical connections between electronic components are more reliable and accidental short circuits will not occur in the circuit, thereby improving the reliability and stability of electronic equipment.
The compact size is another advantage of DIP Package Substrate, which helps achieve a high degree of integration of electronic devices. Since the DIP Package Substrate adopts a dual-in-line design, space can be used more efficiently, allowing electronic devices to achieve more functions in a smaller size, which is very important for applications that require compact design.
Finally, DIP Package Substrate features enhanced mechanical strength to maintain reliability and durability in harsh working environments. Whether in industrial sites or outdoor environments, electronic equipment may be affected by physical shock or vibration, but the rugged design of DIP Package Substrate can effectively protect the internal electronic components and ensure that the equipment can still operate normally under harsh conditions.
In summary, using DIP Package Substrate can not only improve the performance and stability of electronic equipment, but also enable a more compact design and perform well in harsh working environments. This makes DIP Package Substrate the first choice for many electronic engineering projects, providing a solid foundation for innovation and development.
Why choose DIP Package Substrate?
In modern electronic design, selecting the appropriate packaging substrate is crucial, and DIP Package Substrate has unique advantages over traditional PCB boards, especially in applications that require compact size and high thermal performance. Here are a few reasons why DIP Package Substrate is an ideal choice for compact electronic devices such as engine control modules, sensor arrays, and more:
First, DIP Package Substrate adopts dual in-line configuration, which simplifies the assembly process. Through this dual in-line packaging form, electronic components can be easily inserted or removed, thereby greatly improving assembly efficiency. This is particularly important where frequent maintenance or replacement of components is required, while also reducing production costs and production time.
Secondly, DIP Package Substrate has excellent heat dissipation performance. In compact electronic devices, heat generation can lead to device performance degradation or even failure. The dual in-line design adopted by DIP Package Substrate helps to arrange more heat dissipation components on the board, effectively improving heat dissipation efficiency. This enables the DIP Package Substrate to maintain stable performance in high temperature environments, thereby ensuring the reliability and stability of the device.
In addition, DIP Package Substrate also has the advantage of compact size. Due to its dual in-line design, DIP Package Substrate can achieve higher component density, thereby housing more electronic components in a limited space. This makes DIP Package Substrate particularly suitable for electronic devices that require compact designs, such as engine control modules and sensor arrays.
In short, DIP Package Substrate has obvious advantages in compact size and high thermal performance applications. Its dual in-line configuration simplifies the assembly process. Excellent heat dissipation performance and compact size make it suitable for compact electronic devices such as engine control modules and sensor arrays. ideal choice.
What is the manufacturing process of DIP Package Substrate?
The manufacturing process of DIP Package Substrate is a complex and precise process involving multiple critical steps to ensure the quality and performance of the final product. These steps are detailed below:
The first is the substrate preparation stage. At this stage, it is crucial to select a substrate of appropriate material and perform cleaning and surface preparation. Cleaning ensures that the substrate surface is free of any contaminants, while surface treatment helps improve the material’s adhesion and electrical properties.
Next is circuit pattern making. The designed circuit pattern is transferred to the substrate surface by using photolithography or printing technology. This requires high-precision equipment and process control to ensure the accuracy and consistency of circuit patterns.
Then comes the component installation phase. At this stage, various electronic components, such as chips, resistors, capacitors, etc., are accurately mounted onto the substrate. This is usually done via automated production lines, which include precision positioning and welding techniques to ensure correct installation and reliable connection of components.
Finally is the quality control stage. At this stage, every step in the manufacturing process is rigorously inspected and tested to ensure that the product meets specifications and standards. This may include visual inspection, electrical testing, and thermal aging testing to ensure product stability and reliability.
The entire manufacturing process also involves the application of some advanced manufacturing technologies. For example, etching technology is used to remove unnecessary metal or insulating layers to form circuit patterns; gold plating technology is used to increase the conductivity and corrosion resistance of circuits; and soldering technology is used to ensure reliable connections between electronic components and substrates. .
Overall, the manufacturing process of DIP Package Substrate requires a high degree of technical and process control to ensure the quality and performance of the final product. Through precise manufacturing processes and strict quality control, DIP Package Substrate can meet the needs of various applications and provide reliable support for the stable operation of electronic devices.
What are the applications of DIP Package Substrate?
DIP Package Substrate is a packaging substrate widely used in various industries and plays an important role in automotive electronics, consumer electronics, industrial automation and telecommunications.
First of all, in the field of automotive electronics, DIP Package Substrate is widely used in engine control modules and sensor arrays. The engine control module requires highly reliable electronic components to ensure the normal operation of the engine, and DIP Package Substrate provides a reliable infrastructure so that these components can work stably. At the same time, in the vehicle’s sensor array, DIP Package Substrate also plays an important role, helping the vehicle monitor various parameters in real time and make corresponding adjustments.
Secondly, in the field of consumer electronics, DIP Package Substrate is often used in compact electronic equipment and smart home equipment. As consumer electronics become more popular and their functions continue to increase, the requirements for size and performance are also getting higher and higher. The compact design and reliability of DIP Package Substrate make it ideal for mobile phones, smart speakers, smart TVs and other devices.
In the field of industrial automation, DIP Package Substrate is used in control systems and monitoring equipment. Industrial automation systems have extremely high requirements for stability and reliability, and DIP Package Substrate can provide efficient electrical connections and excellent thermal management, thus ensuring the stable operation of equipment.
Finally, in the field of telecommunications, DIP Package Substrate is widely used in network equipment and data transmission modules. With the popularity of the Internet and the continuous increase of data traffic, the demand for network equipment and data transmission modules is also increasing. The DIP Package Substrate can provide efficient signal transmission and reliable electrical connections, thus meeting the performance and stability requirements of these devices.
Overall, DIP Package Substrate plays an important role in various industries, providing a reliable foundation for the performance and stability of electronic devices.
Where can I find DIP Package Substrate?
When looking for a reliable DIP Package Substrate, it is crucial to choose reputable suppliers and manufacturers. At our company, we are committed to providing various types of DIP Package Substrate to meet the specific application needs of our customers.
As a professional electronic materials supplier, we have many years of experience and expertise, able to provide customers with high-quality products and excellent services. Our DIP Package Substrate covers a variety of materials and configurations, including FR-4, ceramic and metal core types, to meet the needs of different application scenarios.
Whether you need a standard off-the-shelf substrate or a custom solution, we have flexible options for you. Our team will work with you to understand your needs and provide customized solutions to ensure the product fully meets your requirements.
By choosing us as your supplier, you can purchase DIP Package Substrate with confidence because quality and performance are always our first priority. We strictly control the production process of our products to ensure that each substrate meets the highest standards and undergoes strict quality inspections.
Whether you are looking for a high-performance DIP Package Substrate or require a custom solution, we can meet your needs. We are committed to providing the best solutions to our customers and establishing long-term and solid cooperative relationships with them.
By choosing our company as your DIP Package Substrate supplier, you can rest assured to purchase high-quality products and enjoy high-quality service and technical support. We look forward to working with you and providing you with satisfactory solutions.
What is the quote for DIP Package Substrate?
When determining the quote for DIP Package Substrate, several factors need to be considered, including changes in material, size, and quantity. Because the manufacturing of DIP Package Substrate is somewhat customized, its cost will vary depending on the type of material selected, substrate size and production quantity. Here are some of the key factors that influence DIP Package Substrate quotes:
Different types of materials can have a significant impact on costs. For example, using high-performance ceramic materials may result in higher costs compared to conventional FR-4 substrates.
Additionally, metal-core materials can be more expensive than traditional organic materials but offer advantages in thermal management.
The size of the substrate directly affects the amount of material used and the process requirements during the manufacturing process. Generally speaking, larger substrate sizes result in higher manufacturing costs.
Likewise, requiring a specific size substrate for a specific application may result in additional customization costs.
Production quantity is another important factor that affects the quotation. Generally speaking, high-volume production can result in lower unit costs, while small-volume production may result in higher costs.
Suppliers often offer different quantity order pricing options to meet the varying needs of customers.
Interested customers can obtain specific quotes on DIP Package Substrate by submitting an inquiry to the supplier. During the inquiry process, customers can provide detailed information about the project, including required material type, substrate size and expected production quantities. Suppliers will provide customized quotes based on this information to ensure customers receive the most cost-effective solution.
In short, the quotation of DIP Package Substrate is affected by multiple factors, including changes in materials, size and quantity. By working with suppliers and providing detailed project requirements, customers can receive customized quotes to select the solution that best suits their needs.
Frequently Asked Questions (FAQs)
Can DIP Package Substrates be customized to specific designs?
Yes, DIP Package Substrates can be customized to meet specific design requirements. Manufacturers often offer customization options for substrate materials, dimensions, and configurations to suit the needs of different electronic applications.
Are DIP Package Substrates suitable for high-frequency applications?
DIP Package Substrates can be designed to accommodate high-frequency applications, but their suitability depends on various factors such as material properties, circuit layout, and signal integrity requirements. Proper design considerations and material selection are essential to ensure optimal performance in high-frequency environments.
How do DIP Package Substrates compare to other package substrate types in terms of thermal performance?
Compared to other package substrate types, DIP Package Substrates offer competitive thermal performance due to their efficient heat dissipation capabilities. The dual in-line configuration facilitates effective thermal management, making DIP Package Substrates suitable for applications requiring robust thermal performance.
Are there any limitations or drawbacks associated with using DIP Package Substrates?
While DIP Package Substrates offer many advantages, they may have limitations depending on the specific application requirements. Common limitations include limited space for component placement and potential challenges in routing complex circuitry. Careful design and layout considerations can help mitigate these limitations.
How can I ensure the quality and reliability of DIP Package Substrates for my project?
Ensuring the quality and reliability of DIP Package Substrates involves selecting reputable suppliers, conducting thorough testing and inspection procedures, and adhering to industry standards and specifications. Collaboration with experienced manufacturers and thorough quality assurance processes can help mitigate risks and ensure the desired performance and reliability of DIP Package Substrates in your project.
What are the typical lead times for procuring custom DIP Package Substrates?
Lead times for custom DIP Package Substrates vary depending on factors such as material availability, production capacity, and complexity of the design requirements. It is advisable to consult with suppliers early in the project planning phase to assess lead times and plan accordingly.