Embedded Cavity Substrate Manufacturer. Open a cavity or multi-cavity on the PCBs. or the BGA pads in the Cavity slot. we have made many this types Embedded Cavity PCBs or Embedded Cavity Package substrates with high quality.
Embedded cavity substrates are an important part of modern PCB engineering, and their innovative nature redefines the scope of electronic design and manufacturing. As a key solution, embedded cavity substrates play a key role in the manufacturing process of electronic devices. This substrate design has the ability to embed electronic components inside the substrate, thereby maximizing space savings and improving overall system performance and reliability.
In contemporary PCB layout, the significance of integrated recessed substrates cannot be overstated. Not only do they furnish a robust structural foundation, but they also proficiently shield and safeguard electronic elements, mitigating electromagnetic interference and signal interference. Moreover, integrated recessed substrates can enhance the thermal dissipation capabilities of electronic devices, consequently augmenting operational efficiency and dependability.
The manufacturing procedure of integrated recessed substrates is notably intricate, necessitating advanced manufacturing methodologies and materials. Through meticulous processes and state-of-the-art equipment, electronic components can be precisely embedded within the substrate and interconnected with adjacent circuits, resulting in elevated integration levels and optimized designs.
Regarding applications, integrated recessed substrates find extensive usage across various electronic apparatus, encompassing communication devices, industrial control systems, medical machinery, and more. Their adaptable design and high-performance attributes render them the preferred solution across numerous industries.
To obtain reliable embedded cavity substrates, you can cooperate with professional manufacturers and suppliers to ensure product quality and supply stability. These manufacturers usually have extensive experience and advanced production equipment to meet customers’ specific needs and provide comprehensive technical support and services.
This passage highlights the significance of embedded cavity substrate in contemporary PCB engineering. It emphasizes the importance of innovative design and widespread utilization in driving the advancement of electronic equipment. By delving into its intricacies and advantages, there’s an opportunity to optimize this crucial technology, thereby facilitating breakthroughs in electronics design and manufacturing.
What are the various variations of embedded cavity substrates?
Embedded cavity substrate is an important part of modern PCB engineering. Different types of embedded cavity substrates provide unique solutions for different design needs and industry applications. Here are the main embedded cavity substrate variations:
High Density Interconnect (HDI) Embedded Cavity Substrate
The application of HDI technology in embedded cavity substrates enables highly integrated electronic systems by enabling more connections and functions in a limited space. HDI embedded cavity substrates are known for their superior signal integrity and high performance and are suitable for applications requiring a high degree of complexity and density, such as communications equipment and computer servers.
Embedded cavity solutions based on organic substrates
This passage describes the utilization of organic substrate embedded cavity substrate, employing materials like FR-4 or polyimide (PI), known for their favorable thermal properties and mechanical strength. This approach is often preferred due to its cost-effectiveness and versatility, making it suitable for various applications such as consumer electronics and industrial control systems.
Other customized embedded cavity substrates
In addition to the common types mentioned above, there are many customized embedded cavity substrates to meet the needs of specific industries or special applications. These customized solutions can include special materials, special processes or designs optimized for specific environmental conditions.
Each embedded cavity substrate variant has its own unique features and benefits and can be selected based on project needs and performance requirements. Whether you’re looking for high performance, high density or affordability, you’ll find the right embedded cavity substrate solution. This diversity makes embedded cavity substrates ideal for meeting the needs of different industries and applications.
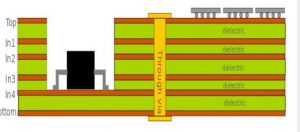
Embedded Cavity Substrate
What are the advantages of embedded cavity substrates?
As an innovative solution, embedded cavity substrates bring multiple advantages to electronic design and manufacturing, thereby optimizing the performance and reliability of electronic devices. The following are the main advantages of embedded cavity substrates:
The embedded cavity substrate design allows for a more compact circuit layout, thereby reducing signal transmission path length and resistance. This optimization can reduce signal transmission delays and improve signal stability and reliability, thereby enhancing the overall electrical performance of electronic devices.
This paragraph describes the benefits of embedding essential electronic components within a cavity. By doing so, circuits can be shielded from electromagnetic interference and crosstalk, which ultimately enhances signal integrity, prevents signal distortion and data loss, and contributes to overall system stability and reliability.
The design of the embedded cavity substrate provides a more efficient thermal conduction path to transfer heat away from critical components faster. This optimization helps reduce the operating temperature of components, extend their life, and ensure stable operation of equipment under high load conditions.
This paragraph discusses the benefits of utilizing an embedded cavity substrate in electronic device design. By employing this technology, it becomes possible to integrate more functions and components within the same space, thereby enabling a miniaturized design. This miniaturization not only enhances device integration and portability but also reduces both size and weight, catering to the growing demand for compact electronic devices.
Furthermore, the design of the embedded cavity substrate offers engineers greater flexibility in laying out and arranging circuit components to address various application scenarios and performance requirements. This flexibility accelerates product development cycles, enhances design efficiency, and provides additional options for meeting customized needs.
In summary, embedded cavity substrates provide opportunities for performance optimization and reliability of electronic devices by providing enhanced electrical performance, improved signal integrity, superior thermal management, miniaturization capabilities, and design flexibility. Important support drives the continuous progress and innovative development of the electronics industry.
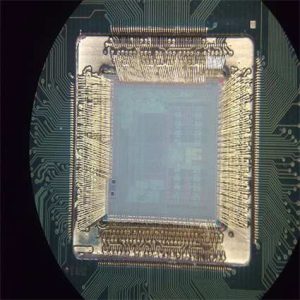
Embedded Cavity Substrate
What is the manufacturing process of embedded cavity substrates?
The manufacturing process of embedded cavity substrates encompasses several pivotal stages, with the production of motherboards standing out as a critical phase. This step entails a thorough examination of both subtractive and additive manufacturing methodologies. Subtractive manufacturing primarily employs cutting, milling, and drilling processes to shape the requisite circuit structures and device apertures on the substrate’s surface. On the other hand, additive manufacturing techniques involve the gradual deposition of materials layer by layer onto the substrate’s surface to craft intricate three-dimensional structures and voids. The fusion of these manufacturing approaches ensures the intricacy and precision of the substrate surface, laying a robust groundwork for the creation and alignment of embedded cavities.
In order to ensure the best performance of the embedded cavity, the motherboard manufacturing process also integrates advanced materials and processes. These materials and processes are designed to ensure optimal cavity formation and alignment. By using high-precision machining equipment and advanced materials, the manufacturing process enables precise formation of the cavity and ensures its accurate alignment with other devices, thereby maximizing the performance and reliability of the embedded cavity substrate.
This passage outlines the significance of substrate production within the manufacturing process of embedded cavity substrates. It emphasizes the importance of high-density interconnects and embedded cavities, achieved through advanced technologies and materials selection such as FR-4, polyimide, and specialty laminates. These materials offer desirable electrical, mechanical, and thermal properties necessary for complex designs. Through the integration of advanced manufacturing processes and quality materials, the production process ensures high performance and reliability of embedded cavity substrates, thereby facilitating the development of electronic devices.
What are the applications in various industries?
As an innovative solution, embedded cavity substrates have shown a wide range of applications in various industries. From telecommunications and aerospace to automotive and medical devices, these substrates demonstrate versatility and adaptability in different environments, providing a reliable foundation and superior performance for electronic devices in various industries.
In the telecommunications industry, embedded cavity substrates are widely used in communication equipment, such as routers, switches and base stations. These devices often require high-density circuit layout and excellent signal integrity, and embedded cavity substrates can meet these needs and provide good thermal performance while maintaining device compactness.
In the aerospace field, embedded cavity substrates are used in various aerospace devices, including flight control systems, satellite communication equipment, and navigation systems. These devices have strict weight and space constraints, and the miniaturized design and excellent performance of the embedded cavity substrate make it an ideal choice.
This paragraph discusses the widespread adoption of embedded cavity substrates across different industries, particularly in automotive and medical equipment manufacturing. In the automotive sector, these substrates are utilized in various electronic systems such as in-car entertainment and vehicle control units, offering stability, reliability, and enhanced system integration. Similarly, in the medical field, embedded cavity substrates find applications in medical imaging, patient monitoring, and treatment equipment, meeting stringent requirements for stability, reliability, compactness, and performance. Overall, the paragraph emphasizes the significant potential and growing importance of embedded cavity substrates in electronic design and manufacturing, driven by technological advancements and expanding application domains.
Where to get reliable embedded cavity substrates?
This excerpt delineates the benefits of a firm specializing in embedded cavity substrates, accentuating its dedication to pioneering, quality assurance, tailoring, streamlined production, and client-centric approaches.
This passage describes the company as a leading producer of embedded cavity substrates, emphasizing its commitment to innovation for maintaining a competitive edge. It highlights the use of cutting-edge manufacturing machinery and a skilled technical workforce to meet diverse client demands. Quality is a core principle, with a rigorous assurance framework ensuring high standards throughout the production process. The company prides itself on offering tailored solutions to meet specific client requirements, making it appealing to various markets. Efficiency in production is also emphasized, reflecting a dedication to timely delivery and cost-effectiveness. Lastly, the company positions itself as a collaborative partner prioritizing client satisfaction, showcasing a commitment to innovation, quality, customization, efficiency, and exceptional client service.
We excel in providing tailored solutions, crafting embedded cavity substrates to precise customer specifications. Whether for specific industry applications or personalized designs, our expertise ensures professional customization.
This passage highlights our commitment to efficiency and customer satisfaction in our production processes. We prioritize timely delivery while maintaining high product quality, whether handling small or large orders. Our customer-centric approach emphasizes communication and collaboration to understand and meet customer needs effectively. From initial consultation to technical support and after-sales service, we provide responsive solutions. We assure comprehensive support and guarantee high-quality products and services for your project. We eagerly anticipate the opportunity to collaborate with you.
Cost considerations and quotes
When selecting an embedded cavity substrate as a core component of an electronic device design, it is critical to understand the associated cost factors and quotes. The following will discuss the main factors that affect the quotation of embedded cavity substrates to help readers effectively formulate project budgets.
The type of embedded cavity substrate has a significant impact on its cost. Different types of substrates have different manufacturing processes, materials and technical requirements, so prices will vary. For example, embedded cavity substrates using high-density interconnect (HDI) technology may be more expensive than traditional substrate types, but they offer significant advantages in high performance and complex designs.
Substrate complexity is another important cost factor. Complex designs require more machining steps and precise manufacturing processes, which can increase costs. For example, substrates with multiple layers of embedded cavities and dense wiring may require more processing time and labor costs, resulting in a higher quote.
This passage highlights the significance of production volume in determining the quotation of embedded cavity substrates. Generally, higher production volumes lead to a lower cost per unit of substrate, as the overall cost can be distributed across a larger number of units. In contrast, lower production volumes tend to incur higher costs, as manufacturers must allocate fixed costs over a smaller quantity of units.
Understanding factors such as substrate type, complexity, and production volumes are important when quoting embedded cavity substrates. By considering these factors, readers can better budget their projects and select the embedded cavity substrate solution that best suits their needs.
Answers to frequently asked questions
Are Embedded Cavity Substrates compatible with standard electronic components and assembly processes?
Yes, Embedded Cavity Substrates are compatible with standard electronic components and assembly techniques. Design considerations are taken to ensure compatibility with common manufacturing processes, enabling seamless integration into existing electronic systems and assembly workflows.
What is the primary function of Embedded Cavity Substrates in PCBs?
Embedded Cavity Substrates serve as a foundational element in modern PCBs, housing delicate electronic components within integrated cavities. This innovative approach optimizes space utilization and enhances the overall performance of electronic devices.
How does the manufacturing process of Embedded Cavity Substrates differ from traditional PCBs?
The manufacturing process involves both motherboard and substrate production, employing subtractive and additive techniques. Advanced materials and technologies are integrated to ensure precise cavity formation and alignment, distinguishing it from traditional PCB manufacturing.
Where can one reliably source high-quality Embedded Cavity Substrates?
Readers can procure reliable Embedded Cavity Substrates from reputable manufacturers and distributors specializing in these advanced solutions. Seeking established sources ensures the quality and performance of the substrates for diverse projects.
What factors influence the cost considerations and quotations for Embedded Cavity Substrates?
Cost considerations are influenced by variables such as substrate type, complexity, and production volume. Understanding these factors enables readers to budget effectively for projects involving Embedded Cavity Substrates.
Are Embedded Cavity Substrates customizable to meet specific project requirements?
Yes, Embedded Cavity Substrates offer customization options to meet diverse project specifications. This adaptability ensures compatibility with various design needs and facilitates the integration of specific functionalities.