Embedded Components PCB manufacturing, we mainly produce Embedded Cavity PCB from 3 layer to 30 layers. Put the IC or Components in the cavity(slot) in the boards.
In the electronics industry, embedded component PCB manufacturing plays a vital role. Embedded Components PCB manufacturing is a precise and complex process involving many aspects from design to cost estimation. This article will take you deep into all aspects of embedded component PCB manufacturing and present you with a comprehensive guide. Embedded component PCB technology not only improves the integration and reliability of circuit boards, but also provides greater flexibility and innovation space for the design and manufacturing of various electronic devices.
What is an embedded component PCB?
Embedded component PCB (Printed Circuit Board) is an innovative and advanced PCB manufacturing technology. It has attracted widespread attention in the electronics industry for its unique design concept and highly integrated features. Compared with traditional PCB manufacturing methods, embedded component PCB embeds electronic components directly into the PCB board, achieving a higher degree of integration and a more compact design.
In traditional PCB design, electronic components are usually connected to the surface of the PCB board through soldering and other methods. In embedded component PCB, electronic components are directly embedded inside the PCB board, on the same layer as the circuit board, thus achieving a more compact layout and more efficient space utilization. This design method can not only reduce the size and weight of the circuit board, but also improve the performance and reliability of the circuit.
So, how does embedded component PCB embed electronic components directly into the PCB board? This involves a series of sophisticated manufacturing processes and technologies. First of all, designers need to consider the embedded position and layout of electronic components during the design stage of the PCB board. Then, during the manufacturing process, electronic components can be precisely embedded into the internal layers of the PCB board through advanced processes and equipment. This usually involves the use of special embedded components and precise assembly processes to ensure reliable connection and stability of the electronic components to the PCB board.
The emergence of embedded component PCB technology has brought new possibilities to the design and manufacturing of electronic products. It not only improves the performance and reliability of electronic products, but also enables smaller and lighter designs. Therefore, in today’s highly competitive electronics market, embedded component PCB technology will undoubtedly become a popular choice pursued by manufacturers and designers.
What is the design process for embedded component PCB?
When designing a PCB with embedded components, designers need to follow a series of specific steps to ensure the stability, reliability, and performance of the circuit. The following is a typical design process:
Demand analysis: Designers first need to understand the customer’s needs and requirements, including circuit functions, performance indicators, size requirements, etc. This step is crucial for subsequent design work.
Schematic design: Based on customer needs, the designer begins schematic design. In the schematic diagram, the designer lays out each component according to the circuit connection relationship to ensure the correct connection and functional realization of the circuit.
Layout design: Layout design is to reasonably arrange the components in the schematic diagram on the PCB board to meet the circuit performance and space utilization requirements to the greatest extent. Designers need to consider factors such as component placement, signal transmission paths, and power lines.
Wiring design: After completing the layout design, the designer begins wiring design. Through CAD software, designers connect circuit connections through wires to ensure stable signal transmission and normal operation of the circuit.
Embedded component selection: Embedded component selection is critical to circuit performance. Designers need to select appropriate embedded components based on customer needs and circuit functions, taking into account factors such as size, power consumption, and performance.
CAD software design and simulation: Designers use CAD software to simulate and verify the completed PCB design. Through simulation software, designers can simulate the working status of circuits, discover potential problems and optimize them.
Verification and debugging: After completing the design, the designer needs to verify and debug the PCB. By using professional testing equipment and instruments, designers can check the performance and stability of the circuit and make necessary adjustments and optimizations.
Final file generation: After verification and debugging are completed, the designer generates the final PCB design file and sends it to the PCB manufacturer for production.
When designing embedded component PCB, designers need to fully consider the functional requirements, space constraints, performance indicators and other factors of the circuit, and conduct design and simulation through CAD software to ensure that the final PCB design meets customer needs and has good performance and stability .
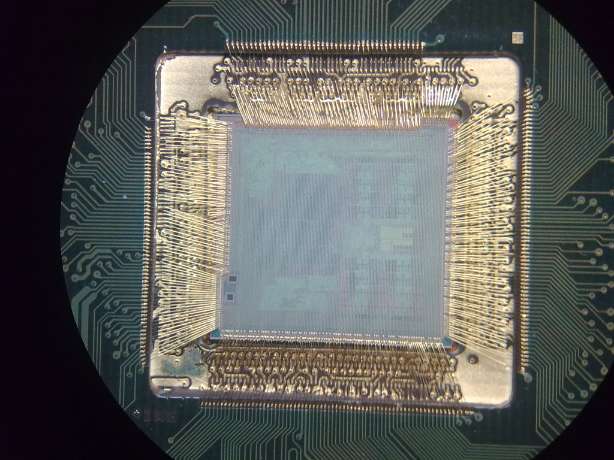
Embedded Components PCB
What is the manufacturing process of embedded component PCB?
The manufacturing process of embedded component PCB is a complex and precise process that requires multiple specific process steps. The main process steps for manufacturing embedded component PCBs and how they are completed will be introduced in detail below.
First, the required PCB board materials need to be prepared, usually using materials such as FR-4. Then, the board is cut to the required size according to the design requirements to ensure it matches the circuit design.
Next, through printing or other methods, the surface of the PCB board is covered with a layer of conductive material to form the outline of the circuit layer and the connection lines.
The PCB board covered with the circuit layer is put into a chemical solution for etching, and the unnecessary parts are removed, leaving the desired circuit shape. After etching is complete, the board needs to be thoroughly cleaned to remove chemical residues.
Drill holes into the already formed circuit board for mounting electronic components and connecting wiring. The drilled surface is then metallized to enhance connectivity and conductivity.
This is a critical step in embedded component PCB manufacturing. Using special equipment, electronic components are embedded into the reserved space inside the PCB board to ensure that the components are flush with the board and tightly fixed.
After the components are embedded, welding operations are required to connect the components to the circuits on the circuit board to ensure the smoothness and stability of the circuit.
Finally, the PCB board is assembled and tested. Install the welded PCB board into the corresponding equipment or product, and conduct functional testing and performance verification to ensure that it meets the design requirements and quality standards.
Through the above process steps, the manufacturing process of embedded component PCB is completed. Each step requires highly specialized equipment and technical support to ensure the quality and performance of the final product. Manufacturers need to strictly control every link to ensure the smooth progress of the entire manufacturing process and provide customers with high-quality products and services.
How to estimate the cost of embedded component PCB?
The cost estimation of embedded component PCB is one of the key links in the manufacturing process, which directly affects the economy and feasibility of the project. Understanding the factors that influence embedded component PCB cost is an important step in ensuring the accuracy of cost estimates. Here are some of the key factors that influence embedded component PCB cost:
Material cost: The materials used in PCB manufacturing are one of the main factors that affect the cost. Different PCB materials have different prices, such as common FR-4, FR-5, polyimide (PI), polyetherketone (PEEK), etc. Choosing the right material depends on the project’s requirements and budget.
Manufacturing process: The process complexity of PCB manufacturing has a direct impact on the cost. For example, the use of more advanced processes and technologies (such as high-precision coating, exposure, and etching) may increase manufacturing costs, but at the same time improve product quality and performance.
PCB board type and quantity: The size, number of layers and quantity of PCB will all affect the cost. Generally speaking, larger and more complex PCB boards result in higher costs. In addition, mass production often results in lower unit prices, while small batch production may increase costs.
Embedded component type and quantity: The type and quantity of embedded components also directly affects the cost. Different types of components have different prices, and more components increase manufacturing complexity and cost.
Design complexity: The complexity of PCB design also has a great impact on cost. Complex designs require more engineer time and resources to complete, thus increasing costs.
Production cycle: If the project has tight delivery time requirements, it may be necessary to work overtime or speed up the production process, thereby increasing costs.
Other factors: There are some other factors that also affect the cost, such as supply chain management, transportation costs, labor costs, etc.
Therefore, an accurate estimate of embedded component PCB cost requires comprehensive consideration of the above factors and full communication and negotiation during the project planning stage to ensure that the final cost is in line with the budget and meets project requirements.
What materials are used in embedded component PCBs?
When manufacturing embedded component PCBs, commonly used materials cover a range of options. Each material has unique characteristics and applicable scenarios. Let’s take a look at it.
FR-4 (fiberglass reinforced epoxy): FR-4 is one of the most common PCB substrate materials. Its characteristics include high mechanical strength, excellent electrical properties and high temperature resistance. This material is suitable for most standard applications such as consumer electronics, communications equipment, etc.
FR-5 (fiberglass reinforced epoxy): Similar to FR-4, but FR-5 has a higher fiberglass content and mechanical strength, making it more suitable for applications with higher strength requirements, such as aerospace and automotive Electronics and other fields.
Polyimide (PI): Polyimide has excellent high temperature stability, chemical stability and mechanical strength, making it suitable for high temperature environments and special applications such as aerospace and medical equipment.
Polyetherketone (PEEK): PEEK has excellent heat resistance, chemical stability and mechanical properties, performs well in extreme environments, and is suitable for special industries such as petrochemicals and automotive electronics.
Aluminum substrate: Aluminum substrate has good heat dissipation performance and mechanical strength, and is suitable for electronic products that require efficient heat dissipation, such as LED lighting and power modules.
Each material has its unique advantages and applicable scenarios, and choosing the right material depends on specific application needs and performance requirements. When selecting materials, factors such as electrical performance, mechanical strength, high temperature resistance, and cost need to be comprehensively considered and matched with the requirements of PCB design.
In short, understanding the characteristics and applicable scenarios of different materials can help manufacturers and designers make the right material selection to ensure the performance and reliability of embedded component PCBs and meet the needs of various applications.
Who makes embedded component PCBs?
In today’s electronics manufacturing industry, the manufacturing of embedded component PCBs involves various suppliers and manufacturers. But for your company, a supplier that manufactures embedded component PCBs is crucial. Below we will explain why choosing the right supplier is so important for embedded component PCB manufacturing and how to ensure you choose the right supplier.
As a company’s key partner, embedded component PCB manufacturers directly affect product quality, performance and reliability. They not only provide PCB board manufacturing services, but may also provide important advice on design, material selection, and process optimization. Therefore, choosing the right supplier is crucial to a company’s product quality and competitiveness.
Professional embedded component PCB manufacturers usually have extensive experience and expertise and are able to provide customized solutions based on customers’ specific needs. They understand the latest manufacturing technologies and processes and can ensure product quality and performance meet customer requirements.
For companies, the stability and reliability of the supply chain are very important. Choosing a manufacturer with a good reputation and stable supply capacity can reduce production risks and ensure the smooth progress of the production plan. At the same time, a stable supply chain can also increase customers’ trust in the company and help establish long-term cooperative relationships.
High-quality embedded component PCB manufacturers usually have complete quality control and certification systems to ensure that products comply with relevant international standards and customer requirements. They may have relevant certifications such as ISO 9001, ISO 14001, UL certification, etc. These are all factors to consider when choosing a supplier.
In addition to product quality and supply capabilities, suppliers’ after-sales service and support are also very important. An excellent manufacturer should be able to respond to customer needs and questions in a timely manner, provide technical support and after-sales service, and ensure customer satisfaction and product reliability.
When selecting an embedded component PCB manufacturer, the company needs to comprehensively consider the above factors and fully communicate and cooperate with potential suppliers. By cooperating with excellent manufacturers, companies can obtain high-quality products and professional technical support, thereby increasing product competitiveness and market share.
What are the five key characteristics of great customer service?
As customers, how do we judge the customer service quality of an embedded component PCB manufacturer? What are the key features we need to focus on?
The first key characteristic of good customer service is the manufacturer’s ability to respond promptly to customer needs and questions. When customers have any questions, problems or emergencies, manufacturers should be able to respond quickly and provide effective solutions. This includes promptly responding to emails, phone calls or online chats, and providing emergency support and service when necessary.
An excellent embedded component PCB manufacturer should have extensive industry knowledge and professional skills. They should have knowledge of various PCB manufacturing technologies, material properties, design standards, etc., and be able to provide professional suggestions and solutions to customers. Through communication and communication with manufacturers, customers can evaluate their professional level and technical capabilities.
Different customers have different needs and requirements, so a good manufacturer should be able to provide customized solutions to meet the customer’s specific needs. They should be able to understand customer needs and carry out personalized design and manufacturing according to customer requirements to ensure that the final product fully meets customer expectations.
Good communication is the key to good customer relationships. An excellent manufacturer should maintain close communication with customers, promptly update manufacturing progress, answer customer questions, and provide regular progress reports. Through effective communication, customers can better understand the manufacturing process, make comments and suggestions, and ensure projects are completed on time.
Finally, great customer service also includes comprehensive after-sales support. The manufacturer should be able to provide the necessary technical support, training and maintenance services after the customer receives the product to ensure the normal operation of the product and customer satisfaction. They should be able to promptly resolve any issues raised by customers and ensure that customers are satisfied with the quality of products and services.
As customers, we should focus on the above key features when choosing an embedded component PCB manufacturer. By evaluating the manufacturer’s service level and capabilities, we can select a truly high-quality partner to achieve project success.
Frequently Asked Questions
Are there any specific design considerations for Embedded Components PCBs?
Designing Embedded Components PCBs requires careful consideration of factors such as thermal management, component placement, and routing of traces. Special attention must be paid to ensure that embedded components are properly encapsulated and insulated to prevent short circuits and ensure reliability. Designers should also optimize the layout to minimize signal interference and maximize the efficiency of the embedded components.
What are the common applications of Embedded Components PCBs?
Embedded Components PCBs are widely used in various industries, including aerospace, automotive, telecommunications, and consumer electronics. They are particularly suitable for applications where space is limited, and high performance and reliability are critical, such as in miniaturized electronic devices, medical implants, and IoT (Internet of Things) devices.
How does Embedded Components PCB differ from traditional PCBs?
Embedded Components PCBs differ from traditional PCBs primarily in their construction. Unlike traditional PCBs where components are soldered onto the surface, embedded components are integrated directly into the PCB substrate during the manufacturing process. This integration reduces the overall size and weight of the final product, improves electrical performance, and enhances reliability.
What is the maximum size of Embedded Components PCBs?
The maximum size of Embedded Components PCBs can vary depending on the manufacturing capabilities of the supplier. However, with advancements in technology, manufacturers can produce Embedded Components PCBs in sizes ranging from small-scale applications to larger, more complex designs. It’s recommended to consult with the manufacturer to determine the specific size limitations for your project.
What are the minimum line width/spacing requirements for Embedded Components PCBs?
The minimum line width and spacing requirements for Embedded Components PCBs depend on several factors, including the manufacturing process and the specific design requirements. Generally, manufacturers can achieve line widths and spacing as small as a few mils (thousandths of an inch) using advanced manufacturing techniques such as laser direct imaging and fine-pitch soldering. However, it’s essential to work closely with your PCB manufacturer to ensure that your design meets the necessary specifications.