FC-LGA Package Substrates Manufacturer. the Package Substrate will be made with Showa Denko and Ajinomoto High speed materials.
FC-LGA (Flip Chip Land Grid Array) packaging substrate is an indispensable and important component in modern electronic equipment. This article will delve into the critical role of FC-LGA packaging substrate and its wide range of applications in high-performance electronic devices. The design and manufacturing of FC-LGA packaging substrates are critical to ensuring device performance and reliability.
What are FC-LGA Package Substrates?
FC-LGA (Flip Chip Land Grid Array) packaging substrate is one of the indispensable key components in today’s high-performance electronic equipment. It is an important infrastructure for mounting chips and other electronic components. It uses flip chip connection technology to provide highly reliable connections for various electronic devices.
In the FC-LGA packaging substrate, the chip is flipped over and connected directly to the surface of the substrate instead of through solder pins like traditional packaging technology. This flip chip connection technology makes the electrical signal transmission path between the chip and the substrate shorter, reducing the delay and loss of signal transmission, thereby improving the performance and stability of electronic equipment.
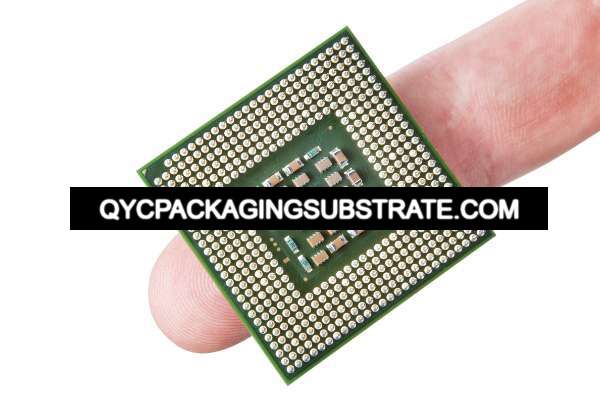
FC-LGA Package Substrates Manufacturer
FC-LGA packaging substrates usually use high-temperature ceramic substrates as the basic material, and their surfaces are covered with tiny solder balls or conductive adhesives. These solder balls or conductive adhesive act as a bridge between the chip and the substrate, ensuring good electrical connection and mechanical stability.
In addition to chip connections, the FC-LGA packaging substrate also provides interfaces for connecting other electronic components, such as capacitors, resistors and other integrated circuits. These interfaces are connected through a grid array arranged on the substrate to form a complete circuit board, which provides necessary support and connections for the normal operation of electronic equipment.
In general, FC-LGA packaging substrate has become an important part of modern electronic equipment due to its highly reliable connection, excellent performance and stability. Its application range covers various fields, including communications, computers, medical and industrial, etc., providing reliable electronic solutions for various application scenarios.
FC-LGA Package Substrates design Reference Guide.
When designing FC-LGA (Flip Chip Land Grid Array) packaging substrates, it is crucial to focus on key design principles, which help ensure that the designed substrates have high performance and reliability. The following are some design reference guides to help engineers effectively design FC-LGA package substrates:
Layout optimization
When designing the FC-LGA packaging substrate, layout optimization is crucial. Properly arrange circuit components, signal lines, and power layers to minimize signal interference and power noise while ensuring signal integrity and power supply stability.
Thermal management
Due to the direct connection between the chip and the substrate in the FC-LGA package substrate, thermal management is critical. The location and size of the heat sink should be considered during design to ensure that the chip can effectively dissipate heat and avoid performance degradation or failure due to overheating.
Power consumption optimization
When designing the FC-LGA packaging substrate, power consumption needs to be optimized. Minimize power consumption and increase battery life by rationally selecting circuit components and optimizing power distribution.
EMI/EMC management
Electromagnetic interference (EMI) and electromagnetic compatibility (EMC) are important issues that need to be considered when designing FC-LGA packaging substrates. Take appropriate shielding measures and ground wire design to reduce the system’s sensitivity to external electromagnetic interference and ensure the stability and reliability of the equipment in different environments.
Reliability test
After the design is completed, reliability testing is an essential step. Reliability tests are conducted on the substrate, including temperature cycle tests, vibration tests, and impact tests, to verify the stability and reliability of the design and ensure its long-term stable operation in practical applications.
Package selection
Selecting the appropriate package is critical to the performance and reliability of the FC-LGA package substrate. Consider factors such as the package’s materials, size, and thermal characteristics to meet the specific needs of the device and ensure compatibility with other components.
In summary, the above key design principles should be followed when designing FC-LGA packaging substrates to ensure that the designed substrates have high performance and reliability. Through reasonable layout optimization, thermal management, power consumption optimization, EMI/EMC management, reliability testing and packaging selection, the performance and reliability of the substrate can be effectively improved to meet the needs of different application scenarios.
What material is used in FC-LGA Package Substrates?
FC-LGA packaging substrate is an indispensable component in high-performance electronic equipment, and its excellent performance and reliability are inseparable from carefully selected materials. In the manufacturing process of FC-LGA packaging substrate, material selection is crucial, and a variety of high-performance materials are often used to ensure its stable performance and durability.
First of all, high-temperature ceramic substrate is one of the key materials commonly used in FC-LGA packaging substrates. This material has excellent high-temperature stability and electrical insulation properties, allowing it to maintain stable performance in extreme operating environments. The high-temperature ceramic substrate also has good mechanical strength and corrosion resistance, and can withstand complex working conditions, such as high temperature and high pressure, ensuring the long-term stable operation of the FC-LGA packaging substrate.
In addition to high-temperature ceramic substrates, conductive metal layers are also one of the indispensable materials in FC-LGA packaging substrates. The conductive metal layer is usually located on the surface of the substrate and is used to connect chips and other electronic components to form a complete circuit structure. These conductive metal layers are usually made of high-purity metal materials, such as copper, silver, etc., with excellent conductivity and weldability, which can ensure stable transmission and reliable connection of circuit signals, thereby improving the overall performance of the FC-LGA packaging substrate and reliability.
In the design and manufacturing process of FC-LGA packaging substrate, material selection is a crucial part. By selecting high-temperature ceramic substrates and high-quality conductive metal layers, it is possible to ensure that the FC-LGA packaging substrate has stable performance, excellent durability and reliable adaptability to the working environment, providing a solid foundation for the development of high-performance electronic equipment.
In summary, the high-performance materials used in FC-LGA packaging substrates, such as high-temperature ceramic substrates and conductive metal layers, provide stable and reliable performance guarantees in various working environments and have become indispensable in modern electronic equipment. important parts of.
What size are FC-LGA Package Substrates?
The size of the FC-LGA packaging substrate is a crucial part of the design. It is directly related to the performance, power consumption, and overall size of the electronic device. Dimensional flexibility gives FC-LGA significant advantages in meeting various application requirements.
During the design process of FC-LGA package substrates, two main size options are typically considered: standard sizes and custom sizes. Standard sizes are usually designed according to industry standards or common specifications, which facilitates supply chain management and modular design. Standard size FC-LGA packaging substrates are generally suitable for most general applications, with high versatility and replaceability, while reducing production costs.
Compared with standard sizes, custom-sized FC-LGA packaging substrates are designed and manufactured more based on the needs of specific applications. This means that aspects such as size, layout, and connection methods can be customized to the customer’s specific requirements. This kind of customized size FC-LGA packaging substrate is usually used in specific high-end application fields, such as cloud computing, artificial intelligence, high-performance computing and other fields, because they can better meet the requirements of performance, heat dissipation, and power consumption in these fields. stringent requirements.
In addition to standard and customized sizes, the size of the FC-LGA package substrate is also affected by other factors, such as the chip size used, connector layout, and heat dissipation requirements. Therefore, these factors need to be considered comprehensively during the design process to ensure that the final FC-LGA packaging substrate can perform optimally in practical applications.
In short, the size of FC-LGA packaging substrate is flexible and diverse, and can be adjusted according to application requirements to meet the needs of different fields. Standard size and customized size options provide customers with more choices, making FC-LGA packaging substrate one of the indispensable key components in the design of modern electronic equipment.
The Manufacturer Process of FC-LGA Package Substrates.
The manufacturing process of FC-LGA packaging substrate is a complex and precise process, covering multiple key steps such as design, manufacturing and testing. The precise execution of these steps is critical to ensuring the quality and performance of the final product.
Design phase
The first step in manufacturing FC-LGA packaging substrate is design. During the design phase, engineers utilize advanced computer-aided design (CAD) software to create blueprints of the packaging substrate. This includes determining key parameters such as substrate size, hierarchy, routing and connection point placement. The design process also involves taking into account how electronic components are arranged and connected to ensure optimal signal transmission and power management.
Manufacturing stage
After the design is complete, the manufacturing phase begins. This stage involves multiple processes, including substrate material selection, printing, chemical processing, electroplating, etching, and drilling. First, select a high-quality substrate material, usually a high-temperature ceramic or high-performance resin substrate, to meet the specific requirements of the device. Next, advanced printing technology is used to coat a conductive metal layer on the surface of the substrate and undergo chemical treatment to ensure the accuracy and reliability of the conductive layer. A plating and etching process is then performed to define the wires and connection points on the circuit board. Finally, holes are made in the substrate through drilling techniques to mount and connect electronic components.
Testing phase
After the manufacturing is completed, the FC-LGA packaging substrate enters the testing stage. At this stage, each manufactured substrate undergoes rigorous functional and performance testing to ensure it meets specifications and operates reliably. Testing typically involves electrical testing using automated test equipment to check circuit continuity and functionality. In addition, physical tests such as X-ray inspection or microscopic examination may also be performed to ensure that no manufacturing defects or defects are present. Only substrates that pass all tests are deemed qualified and can proceed to the next stage of production and assembly.
Overall, the manufacturing process of FC-LGA packaging substrates requires a high degree of expertise and technology to ensure the quality and performance of the final product. Through careful design, precise manufacturing and rigorous testing, these substrates can play an important role in various high-performance electronic devices, supporting and promoting the development of modern technology.
The Application area of FC-LGA Package Substrates.
As a key electronic component, FC-LGA (Flip Chip Land Grid Array) packaging substrate is widely used in various high-performance electronic devices to meet the needs of different industries. Its specific applications in servers, network equipment, communication equipment and other fields will be discussed below.
Server
In the server field, FC-LGA packaging substrate plays an important role in connecting and supporting high-performance processors. The performance and stability of servers are crucial for data center and enterprise-level applications, and the high reliability and dense layout of FC-LGA package substrates make it an ideal choice for building high-performance servers. Whether used for cloud computing, big data processing or enterprise applications, FC-LGA packaging substrates can provide stable and reliable electronic connections to ensure efficient operation of servers.
Internet equipment
In the field of network equipment, FC-LGA packaging substrates are widely used in routers, switches, firewalls and other equipment. These devices need to handle large amounts of data traffic and maintain a high degree of reliability and stability. FC-LGA packaging substrate can meet these requirements, provide high-speed data transmission and reliable connection, and has excellent heat dissipation performance to adapt to long-term, high-load working environment.
Communication device
In the field of communications, FC-LGA packaging substrates are widely used in key facilities such as base stations, wireless communication equipment, and optical fiber communication equipment. These devices need to handle complex signal processing and data transmission tasks while maintaining a high degree of stability and reliability. FC-LGA packaging substrate provides a stable electronic foundation for communication equipment through its compact design and reliable connection technology, supporting the implementation of various communication standards and protocols.
In general, FC-LGA packaging substrate plays a vital role in high-performance electronic equipment, and its application range covers servers, network equipment, communication equipment and other fields. By providing stable and reliable electronic connections and excellent performance characteristics, FC-LGA packaging substrates provide a solid foundation for technological innovation and development in various industries.
What are the advantages of FC-LGA Package Substrates?
As a key component in modern electronic equipment, FC-LGA packaging substrate (Flip Chip Land Grid Array) has obvious advantages. Compared with traditional packaging methods, FC-LGA packaging substrates have shown obvious advantages in many aspects, making them the first choice in electronic device design.
First, the FC-LGA packaging substrate has higher reliability. Using flip chip connection technology, the FC-LGA package substrate can achieve a more stable and reliable connection. By directly connecting the chip upside down to the solder joints on the substrate, it not only reduces the signal transmission path length and signal loss, but also improves the anti-interference ability of the circuit and reduces the risk of circuit interruption or damage, thus ensuring the stability of the device. and reliability.
Secondly, the FC-LGA packaging substrate has a more compact design. Compared with traditional packaging methods, the design of FC-LGA packaging substrate is more compact and effectively utilizes space resources. By directly connecting the chip to the surface of the substrate without the need for additional leads or spacing, the overall size of the circuit board is smaller, allowing more functional modules to be accommodated in a limited space, achieving higher integration and improving device performance. and function.
In addition, the FC-LGA packaging substrate has easier assembly. Due to the use of flip chip connection technology, the FC-LGA package substrate does not require complex welding operations during the assembly process. The chip can be simply flipped and connected to the surface of the substrate to complete the assembly. This not only saves assembly time and costs, but also reduces operational risks during the assembly process and improves production efficiency, thereby bringing products to market faster.
To sum up, FC-LGA packaging substrate has obvious advantages over traditional packaging methods in terms of reliability, design compactness and ease of assembly. These advantages make FC-LGA packaging substrate an indispensable part of the design of modern electronic equipment, providing strong support for the performance improvement and function expansion of electronic equipment.
FAQ
How reliable is the FC-LGA packaging substrate?
The FC-LGA packaging substrate is manufactured using advanced connection technology and high-performance materials, resulting in excellent reliability. Its flip-chip connection design ensures a solid electrical connection, effectively reducing the risk of disconnection or disconnection. In addition, the manufacturing process of FC-LGA packaging substrates is strictly controlled to ensure the stability of product quality and performance.
What should we pay attention to when maintaining FC-LGA packaging substrate?
When maintaining the FC-LGA package substrate, care should be taken to avoid mechanical damage and electrostatic discharge. Regularly check connections for loose or damaged connections and avoid contact with corrosive substances to ensure long-term stability and reliability.
How to recycle FC-LGA packaging substrates?
Since FC-LGA packaging substrates are composed of a variety of materials, including metals and plastics, effective material separation and processing are required during recycling. Generally, professional electronic waste recycling agencies can properly handle and recycle FC-LGA packaging substrates to minimize the impact on the environment.
What is the environmental impact of FC-LGA packaging substrate?
The manufacturing process of FC-LGA packaging substrates requires a certain amount of energy and resources, and discarded FC-LGA packaging substrates may have a certain impact on the environment. Therefore, during the manufacturing and use processes, energy consumption and waste generation should be minimized, and sustainable production and management measures should be adopted to minimize negative impacts on the environment.