FC-LGA Substrates Manufacturer.As a leading FC-LGA substrates manufacturer, our company specializes in producing high-performance flip-chip land grid array substrates. We leverage advanced technologies and stringent quality controls to ensure optimal reliability and efficiency in electronic packaging. Our substrates are integral in supporting the latest semiconductor innovations, providing essential connectivity and stability for cutting-edge devices. Dedicated to customer satisfaction, we deliver tailored solutions to meet diverse industry needs, from consumer electronics to telecommunications.
FC-LGA substrate is a special form of Printed Circuit Board (PCB). It uses Flip Chip technology to flip the chip directly and solder it to the solder ball array on the substrate. Due to its high-density and high-performance characteristics, FC-LGA substrates are widely used in high-performance electronic devices and systems, such as smartphones, tablets, and network servers. This article will delve into the characteristics, applications and manufacturing processes of FC-LGA substrates to help readers more fully understand the important role of this key component in the modern electronics industry.
What are FC-LGA Substrates?
FC-LGA substrate is a printed circuit board that uses advanced Flip Chip technology to flip the chip directly and solder it to the solder ball array on the substrate. This design places the active components of the chip toward the substrate and connects them to contact points on the substrate through soldering, without the need for traditional wire harness connections. This innovative design not only effectively reduces the size of electronic devices, but also improves circuit integration and performance.
The traditional wire harness connection method occupies a considerable space in electronic devices, and has problems such as slow signal transmission speed, inductance and crosstalk. The use of FC-LGA substrate overcomes these problems, shortens the distance between the chip and the substrate to a minimum, and greatly improves signal transmission speed and circuit performance. In addition, Flip Chip technology can also achieve denser circuit layout, further improve the integration of equipment, and provide the possibility for miniaturization and lightweight of electronic products.
By directly flipping the chip and welding it to the solder ball array on the substrate, the FC-LGA substrate effectively reduces the connection distance, reduces signal transmission delays, and improves the response speed and stability of the system. At the same time, this design also reduces the inductance and crosstalk of circuit wiring, reduces signal distortion and interference, and ensures the reliability and performance of electronic devices.
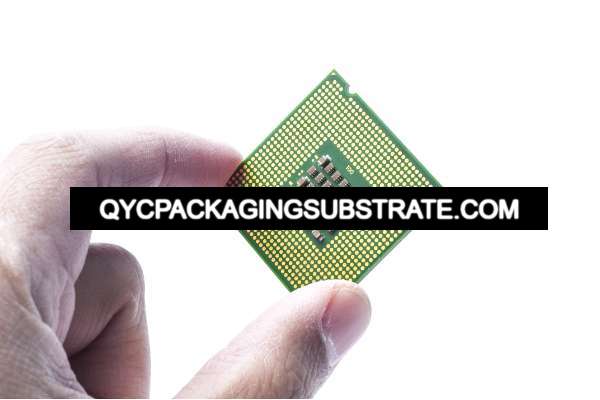
FC-LGA Substrates Manufacturer
In general, FC-LGA substrate, as an advanced printed circuit board technology, uses Flip Chip technology to achieve direct connection between the chip and the substrate, which greatly improves the integration, performance and reliability of electronic devices. In the rapid development and iterative updates of today’s high-tech electronic equipment, FC-LGA substrates are playing an increasingly important role, injecting new vitality and power into the development and progress of the electronics industry.
FC-LGA Substrates design Reference Guide.
FC-LGA (Flip Chip Land Grid Array) substrate design is a crucial part of modern electronic equipment. Its design directly affects the performance, reliability and cost of the equipment. The following are some important considerations regarding FC-LGA substrate design:
Chip layout and arrangement
When designing an FC-LGA substrate, you first need to consider the layout and arrangement of the chips. Reasonable chip layout can maximize the performance and reliability of the circuit, while ensuring that the interconnection paths between chips are as short as possible and reducing signal transmission delays.
Signal integrity
FC-LGA substrate design needs to pay attention to signal integrity, including reducing impedance mismatch of signal transmission lines, reducing signal reflection and crosstalk, etc. Signal integrity can be effectively improved by optimizing signal transmission paths with appropriate line widths, spacing, and inter-layer distances.
Thermal management
Due to the high integration and high-performance characteristics of electronic devices, FC-LGA substrate design must fully consider thermal management. Reasonable heat dissipation design can effectively reduce chip temperature, extend the service life of the device and improve performance stability.
Manufacturing feasibility
When designing the FC-LGA substrate, the feasibility of the manufacturing process needs to be considered. Reasonable selection of substrate material, number of layers, line width, spacing and other parameters can reduce manufacturing costs and improve manufacturing efficiency.
Reliability and maintainability
The design of FC-LGA substrate needs to take into account the reliability and maintainability of the equipment. Reasonable design can reduce assembly errors, improve equipment reliability, and facilitate later maintenance and repair.
To sum up, FC-LGA substrate design is a complex project that comprehensively considers factors such as performance, cost, manufacturing process, and reliability. By in-depth understanding of the above key factors, combined with practical application needs and technological innovation, FC-LGA substrates with superior performance, reliability and stability can be designed to promote the development and progress of electronic equipment.
What material is used in FC-LGA Substrates?
FC-LGA substrate is a core component in modern high-performance electronic equipment. Its material selection is crucial and directly affects the performance and reliability of the circuit board. In the manufacturing of FC-LGA substrates, common materials include FR4 (fiberglass reinforced epoxy resin), polyimide (PI) and ceramics.
First, FR4, as a widely used substrate material, has excellent mechanical strength and heat resistance. Its main components are glass fiber and epoxy resin, which makes the FC-LGA substrate have good durability and stability and can meet the requirements of most electronic equipment. In addition, the cost of FR4 materials is relatively low and suitable for mass production.
Secondly, polyimide (PI) materials are favored for their excellent high temperature stability and chemical stability. In high-temperature environments, PI substrates can maintain good mechanical and electrical properties and are not easily deformed or aged, making them suitable for applications with higher temperature requirements. In addition, the low dielectric constant and low dielectric loss of PI substrate give it excellent signal transmission performance in high-frequency circuits.
Finally, ceramic materials are widely used in FC-LGA substrates that require extremely high performance and reliability. Ceramic substrates have excellent thermal conductivity and mechanical strength, allowing them to maintain stable performance in extreme environments. Due to their high cost and manufacturing complexity, ceramic substrates are often used in specialized fields such as aerospace and defense.
In general, the material selection of FC-LGA substrate depends on the requirements and performance indicators of the specific application. Whether using FR4, polyimide or ceramics, ensure that the material has good electrical properties, thermal properties and mechanical strength to meet the needs of high-performance electronic equipment for stable and reliable circuit connections.
What size are FC-LGA Substrates?
The size of the FC-LGA substrate depends on the needs of the specific application and the design requirements of the device. Since FC-LGA substrates are typically used in high-density, high-performance electronic devices, their sizes tend to be relatively small to accommodate compact device layouts and space constraints.
Generally speaking, the size of FC-LGA substrate can vary from a few millimeters to tens of millimeters. For small consumer electronics, such as smartphones and tablets, the size of the FC-LGA substrate may be only a few millimeters on a side. This small size substrate can achieve higher integration, making the device thinner and lighter.
For some large computer servers or network equipment, the size of the FC-LGA substrate may be larger to accommodate more electronic components and more complex circuit designs. In these applications, FC-LGA substrates may reach dimensions of tens of millimeters or even larger to meet the performance and functional requirements of the device.
In addition to size, the density of FC-LGA substrate is also a key factor. Because it uses Flip Chip technology, the devices can be more densely laid out on the substrate, so more functions and connections can be implemented in a limited space. This high-density design helps improve device performance and functionality while reducing the overall size of the device.
In general, the size and density of FC-LGA substrates are designed and selected based on specific application requirements. Whether it is small consumer electronics or large network equipment, FC-LGA substrates can provide high-performance, high-reliability circuit connection solutions to meet the compact, efficient, and reliable requirements of modern electronic equipment. With the continuous advancement and innovation of technology, FC-LGA substrates will continue to play an important role in various application fields and promote the continued development of the electronics industry.
The Manufacturer Process of FC-LGA Substrates.
The manufacturing process of FC-LGA substrates involves a series of complex and precise steps, the correct execution of which is crucial to ensure the performance and reliability of the final product.
First, manufacturing FC-LGA substrate requires multi-layer stacking. This involves stacking multiple sheets of substrate material, such as FR4 or polyimide (PI), together through a lamination process. During this process, each layer needs to be precisely aligned to ensure that the final circuit board structure is complete and stable.
Next is the copper foil film processing stage. In FC-LGA substrate manufacturing, copper foil plays an important role in forming the conductive path of the circuit. Therefore, a layer of copper foil needs to be coated on the surface and inside of the substrate and processed through chemical methods or mechanical processing to ensure that its flatness and conductive properties meet the requirements.
Graphic printing is one of the key steps in manufacturing FC-LGA substrates. At this stage, the designed circuit pattern is printed on the copper foil on the surface of the substrate through printing technology. This requires the use of photolithography and chemical etching processes to remove unwanted parts, creating conductive paths and connection points.
Next is the preparation of the solder ball array. The solder ball array is a key component used to connect chips on the FC-LGA substrate. Its accuracy and quality directly affect the reliability and stability of the welding. This step typically involves applying a layer of solder paste to the surface of the substrate and using sophisticated processing equipment to convert it into a series of evenly distributed solder balls.
Finally, the chip is flipped and soldered. In this step, the chip is flipped over and precisely positioned on the substrate so that it connects to the array of solder balls. This usually requires high-precision automated equipment to ensure accurate chip alignment and solid welding.
In general, the manufacturing process of FC-LGA substrate requires a high degree of professional technology and strict quality control. Only through precise process control and high-quality materials can we ensure that the final product has excellent performance and reliability to meet the needs of high-density electronic equipment.
The Application area of FC-LGA Substrates.
As a high-performance, high-density printed circuit board, FC-LGA substrate plays a vital role in the field of modern technology. It is widely used in various high-density electronic devices, providing reliable circuit connection solutions for these devices and promoting the continuous development and progress of science and technology.
In the field of consumer electronics, FC-LGA substrates are widely used in smartphones, tablets, digital cameras and other devices. These devices have extremely high requirements for the performance and reliability of circuit connections, and FC-LGA substrates can meet these requirements and provide consumers with a stable and efficient electronic product experience.
In the field of communication equipment, FC-LGA substrates are used to manufacture network routers, switches, base stations and other equipment. These devices need to handle a large amount of data traffic and have very strict requirements on the speed and stability of circuit connections. The FC-LGA substrate can provide high-speed and reliable signal transmission to ensure the normal operation of communication equipment.
In the field of computer servers, FC-LGA substrates are widely used in data center servers, enterprise-level storage systems and other equipment. These devices have extremely high requirements for computing and storage capabilities, and FC-LGA substrates can provide high-density, high-performance circuit connections, providing key support for improving the performance of server systems.
In the field of medical equipment, FC-LGA substrates are used to manufacture key equipment such as medical imaging equipment and life monitoring equipment. These devices have extremely high requirements for the stability and reliability of circuit connections, and FC-LGA substrates can provide high-quality circuit connection solutions to ensure the accuracy and reliability of medical equipment.
In the field of industrial automation, FC-LGA substrates are widely used in control systems, sensor equipment, robots and other equipment. These devices have extremely high requirements for the stability and durability of circuit connections, and FC-LGA substrates can provide high-quality circuit connection solutions to ensure the reliable operation of industrial automation equipment.
In general, FC-LGA substrate plays an irreplaceable role in various high-density electronic devices, providing strong support for the development and progress of modern technology. With the continuous advancement of technology and the continuous expansion of application fields, FC-LGA substrates will continue to play an important role in promoting the development of the electronics industry in a more intelligent and efficient direction.
What are the advantages of FC-LGA Substrates?
The advantages of FC-LGA substrates are obvious and they play a key role in modern electronic devices. Compared with the traditional wire harness connection method, FC-LGA substrate has brought many significant improvements. The following are some of the main advantages:
First, the FC-LGA substrate has a higher level of integration. By using Flip Chip technology, the chip is directly flipped and soldered to the solder ball array on the substrate, which can achieve a high degree of integration of electronic devices in a smaller space, thus making the overall size of the device smaller and lighter, making it more suitable for devices such as smartphones. , tablet computers and other products with strict volume requirements.
Secondly, FC-LGA substrate has faster signal transmission speed. Since the direct connection method of the solder ball array eliminates signal transmission delays and losses in traditional wire harness connections, the FC-LGA substrate can achieve faster and more stable signal transmission, thereby improving the device’s response speed and data processing capabilities.
In addition, FC-LGA substrate also has excellent thermal management capabilities. Since the chip is directly connected to the substrate, heat transfer is more efficient and heat can be dissipated to the surrounding environment more effectively, thereby reducing the operating temperature of the device, extending the service life of the device, and also improving the stability and reliability of the system. .
In addition, FC-LGA substrate can effectively reduce the inductance and crosstalk of circuit wiring. By directly connecting the chip and the substrate, the length and complexity of the circuit signal transmission path is reduced, and the probability of occurrence of inductance and crosstalk is reduced, thereby improving the signal integrity and anti-interference ability of the overall system.
To sum up, FC-LGA substrate has become an indispensable and important part of modern electronic equipment due to its many advantages such as high integration, fast signal transmission, excellent thermal management, and reduced circuit wiring inductance and crosstalk. With the continuous advancement and innovation of technology, it is believed that FC-LGA substrate will continue to play an important role in the future, driving the electronic industry forward.
FAQ
What is FC-LGA substrate?
FC-LGA substrate is a printed circuit board that uses Flip Chip technology to achieve high-density circuit connections by flipping the chip directly and soldering it to the solder ball array on the substrate.
How is FC-LGA substrate different from other types of PCB?
The FC-LGA substrate uses Flip Chip technology to directly connect the chip to the substrate. Compared with traditional PCB, it has higher integration, smaller size, faster signal transmission speed and better thermal management. ability.
What is the manufacturing process of FC-LGA substrate?
The process of manufacturing FC-LGA substrate includes steps such as multi-layer stacking, copper foil film processing, graphic printing, solder ball array preparation, and chip flip welding. These processes require high precision and strict quality control.
What are the application fields of FC-LGA substrate?
FC-LGA substrates are widely used in consumer electronics, communication equipment, computer servers, medical equipment, industrial automation and other fields, providing high-performance, high-reliability circuit connection solutions for these devices.
What are the advantages of FC-LGA substrate?
Compared with traditional wire harness connection methods, FC-LGA substrate has higher integration, smaller size, faster signal transmission speed and better thermal management capabilities. In addition, it can reduce the inductance and crosstalk of circuit wiring, improving the overall performance and stability of the system.