FCBGA Substrate Manufacturer, More than 100 engineers, more than 20,000 employees, we produce variety of high layer FCBGA substrate, we have a professional packaging substrate production line and assembly equipment.
The acronym “FCBGA” in FCBGA Substrate denotes “Flip-Chip Ball Grid Array,” a name that aptly encapsulates its innovative nature and broad applicability. In this fiercely competitive and perpetually innovative field, FCBGA Substrate transcends being merely a technology; it embodies a trend-setting design concept.
Functioning as a distinctive form of printed circuit board, FCBGA Substrate leverages Flip-Chip packaging technology to directly invert the chip onto the substrate, establishing connectivity through a Ball Grid Array. This ingenious design not only enhances circuit board density but also effectively addresses issues related to signal integrity and heat dissipation that may arise in traditional packaging approaches.
The design concept of FCBGA Substrate is very consistent with the high performance and space requirements of current electronic products. In compact electronic devices, such as smartphones, servers and graphics processors, FCBGA Substrate’s high degree of integration and space efficiency have become outstanding advantages.
During the manufacturing process, key steps of FCBGA Substrate include substrate selection, lamination, metallization, etc. The precise control and high craftsmanship requirements of these steps ensure the excellent quality and reliability of the final product.
FCBGA Substrate is widely used in high-end electronic products. Its flexible design and excellent performance make it involved in various fields. From servers and network equipment to graphics processors, FCBGA Substrate provides superior support for these devices with its unique features.
Selecting a dependable FCBGA Substrate manufacturer is of paramount importance. Collaborating with a professional in this field not only ensures the receipt of high-quality products but also opens the door to tailored solutions that align with the unique requirements of your project.
Furthermore, comprehending the quotation for FCBGA Substrate is a critical element in the decision-making process for any project. Factors such as manufacturing processes, material selection, and project size must be carefully evaluated to strike a balance between cost-effectiveness and optimal performance.
In essence, FCBGA Substrate stands out as the preferred choice for PCB engineers engaged in the design of high-performance electronic devices.
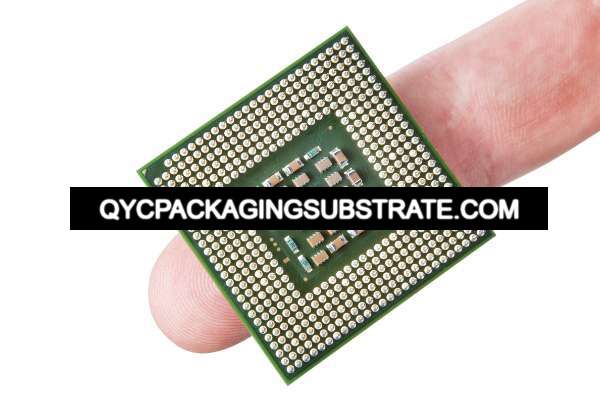
FCBGA substrate manufacturer
What types of FCBGA Substrate are there?
When exploring the world of FCBGA Substrate, we will find that this printed circuit board is not just a single concept, but a technological solution with many types to suit different application scenarios. As mentioned earlier, the diversity of FCBGA Substrate is mainly reflected in its different types, including single-layer, multi-layer and rigid-flexible structures.
First of all, the single-layer FCBGA Substrate is a relatively simple but very practical design. Its structure is relatively simple and suitable for some application scenarios that do not have particularly high density requirements. Single-layer structures are generally easier and less expensive to manufacture and are suitable for certain electronic products where performance requirements are not extremely stringent.
Additionally, the multi-layer FCBGA substrate represents a sophisticated and advanced design. Through the stacking of circuits across multiple levels, it achieves heightened integration and superior electrical performance. This substrate variant finds extensive use in fields demanding both high performance and stringent space constraints, such as in high-performance computers and communication equipment. The multi-layered configuration enhances the reliability of signal transmission, simultaneously mitigating the risk of electromagnetic interference.
Lastly, the rigid-flexible structure of the FCBGA substrate embodies a product that strikes a harmonious balance between flexibility and stability. This innovative design amalgamates rigid and flexible materials, facilitating a high degree of adaptability and reliability within confined spaces. Rigid-flexible structures are commonplace in scenarios necessitating accommodation for three-dimensional shapes or limited spaces, as exemplified in certain modern portable electronic devices.
Each type of FCBGA Substrate has its own unique features and advantages. Single-layer Substrate is suitable for simple applications, while multi-layer Substrate is suitable for areas with higher performance requirements. The rigid-flexible structure is the product of finding the best balance point in design. This diverse selection provides engineers with more flexibility, allowing them to choose the most suitable Substrate type based on specific needs, thereby achieving the best balance of performance and reliability in their designs. These different types of designs of FCBGA Substrate provide precise solutions for different application scenarios, making it play an increasingly important role in the electronic field.
What advantages does FCBGA Substrate have over other circuit boards?
FCBGA Substrate, as a new star in the printed circuit board (PCB) field, shows obvious advantages over traditional circuit boards. Its clever design provides excellent performance and reliability for high-tech applications, making it one of the first choices in many fields.
First of all, FCBGA Substrate shows impressive characteristics in terms of density. By using Flip-Chip packaging technology, the substrate can achieve higher connection density and arrange components more compactly. This provides the possibility of miniaturization and lightweighting of electronic devices, especially in modern mobile devices and portable electronic products, and its advantages are particularly significant.
Secondly, FCBGA Substrate has excellent electrical performance. By using highly advanced materials and processes, the substrate provides excellent electrical conductivity and signal transmission performance. This provides ideal support for high-frequency, high-speed electronic applications, including graphics processors, communication equipment and other fields, allowing equipment to complete various tasks faster and more reliably.
Reliability is another key reason for FCBGA Substrate’s popularity. Its design not only considers the implementation of high-density connections, but also focuses on optimizing thermal management. This helps to effectively dissipate heat, reduce the operating temperature of components, extend equipment life, and reduce failure rates. In some applications that require extremely high stability and reliability, FCBGA Substrate is obviously superior.
Overall, FCBGA Substrate has brought a new design paradigm to the electronics industry with its high density, superior electrical performance and reliability. While meeting the performance, volume and reliability requirements of modern electronic equipment, the continuous development and application of this technology will drive the entire industry to a more innovative and efficient future.
Why choose FCBGA Substrate among many circuit boards?
As today’s electronics industry continues to evolve, it has become increasingly critical to select the appropriate circuit boards to support advanced electronic packaging technologies. Among the many circuit board options, FCBGA Substrate has become the first choice for PCB engineers due to its excellent features and performance.
First of all, FCBGA Substrate shows excellent advantages in heat dissipation performance. In high-performance applications, electronic devices often face intense heat dissipation challenges, and FCBGA Substrate effectively improves heat transfer efficiency through its uniquely designed flip chip ball grid array technology. This means that under high-load operation, FCBGA Substrate can dissipate heat more efficiently, ensuring that electronic components always work within an acceptable temperature range, thereby extending the life of the equipment.
Secondly, FCBGA Substrate stands out in terms of high-density connectivity. In modern electronic equipment, there is an increasingly urgent need for compact designs and high-density connections on circuit boards. FCBGA Substrate makes the connection more compact and reliable through its unique chip packaging method. This enables more circuit components to be implemented in a limited space and meets the continuous pursuit of miniaturization and lightweight of advanced electronic equipment.
It’s no coincidence that FCBGA Substrate is the ideal decision in performance and space-critical applications. Its design not only takes into account the improvement of performance, but also fully considers the effective use of space. This makes FCBGA Substrate particularly outstanding in a range of fields, such as high-performance computing, communication equipment, and graphics processors.
To sum up, FCBGA Substrate’s leading position in the field of electronic packaging is no accident. Its excellent thermal performance and high-density connectivity make it stand out among many board options. For those applications with extremely demanding performance and space requirements, choosing FCBGA Substrate is a wise and ideal decision. In the future design of electronic equipment, FCBGA Substrate will continue to play a key role and promote continuous innovation in electronic technology.
What is the manufacturing process of FCBGA Substrate?
The production of FCBGA (Flip-Chip Ball Grid Array) Substrate is a meticulously intricate process characterized by multiple critical steps, each exerting a significant influence on the ultimate performance and reliability of the end product. The comprehensive manufacturing process of FCBGA Substrate unfolds as follows:
Substrate Selection
The initial and crucial step involves the meticulous selection of the substrate. This decision holds paramount importance as it profoundly affects the physical and electrical properties of the entire substrate. Typically, high-performance dielectric materials are meticulously chosen to ensure optimal signal transmission performance, especially in high-frequency applications.
Lamination
Following substrate selection, the lamination stage takes center stage. This pivotal step involves the layer-by-layer stacking of multiple substrate layers, which are then pressed together with the conductive layer to forge a multi-layered structure. This intricate structure enhances circuit density, enabling the FCBGA Substrate to accommodate a greater number of connection points, thereby augmenting its integration and overall performance.
Metalization
Metalization stands as another critical phase in FCBGA Substrate manufacturing. During this step, specific areas are metallized to establish electrical circuits, conductive paths, and connection points. Typically, highly conductive metals like copper are employed to ensure low resistance and high conductivity, pivotal for optimal performance.
Additionally, quality control constitutes a pivotal component of the manufacturing journey. Leveraging advanced inspection and testing equipment, each manufacturing step undergoes stringent quality control measures to guarantee that the final FCBGA Substrate aligns with design specifications and performance requirements.
In summary, the manufacturing process of FCBGA Substrate is an exceedingly complex and precise endeavor, demanding meticulous accuracy and consistency at every phase. This commitment ensures that the end product attains exemplary performance and reliability.
In which application fields is FCBGA Substrate widely used?
In the realm of printed circuit boards (PCB) technology, FCBGA Substrate stands out as a cutting-edge innovation, demonstrating extensive and impactful applications in high-end electronic products. This advanced substrate design has not only garnered significant success in servers, network equipment, and graphics processors but has also showcased exceptional performance and adaptability across diverse application scenarios.
Within the server domain, FCBGA Substrate has emerged as the preferred choice, primarily attributable to its high density and superior performance. Given the substantial data processing and intricate calculations required in server operations, the design flexibility of FCBGA Substrate seamlessly caters to the diverse needs of various server architectures. Its high-density connectivity enables the implementation of more functional units within confined spaces, thereby enhancing the overall performance and efficiency of servers.
In terms of network equipment, FCBGA Substrate also plays an important role. Network equipment requires highly complex circuits to be implemented in a compact space while maintaining excellent signal transmission performance. FCBGA Substrate’s high performance, high-density connectivity and flexible design make it an ideal choice to meet these requirements, providing a solid foundation for innovation in network equipment.
Graphics processing unit (GPU), as the core component of high-performance computing and graphics processing, has particularly strict performance and design requirements for circuit boards. FCBGA Substrate plays a key role in the packaging and connection of GPUs through its superior thermal performance and flexible design. Its highly customizable nature allows for more flexible layout in GPU design, achieving better heat dissipation and thus improving graphics processing performance.
Overall, the wide application of FCBGA Substrate in the field of high-end electronic products demonstrates its important position in future technology development. Its design flexibility and high performance not only meet the needs of current high-demand electronic equipment, but also lay a solid foundation for more advanced and complex electronic products in the future. FCBGA Substrate is not only a cutting-edge choice, but also a key driver in promoting the advancement of electronic technology.
How and where to get reliable FCBGA Substrate?
In today’s electronics industry, the choice of a dependable FCBGA Substrate manufacturer is paramount for the success of your project. Given the widespread application of FCBGA Substrates in high-performance electronic products, partnering with experienced manufacturers, such as our company, directly influences the quality and performance of the end product.
The manufacturing of FCBGA Substrates involves intricate processes and precise technologies. To uphold product quality and reliability, selecting a seasoned and professional manufacturer is indispensable. In this domain, our company stands out due to its extensive years of expertise and technological innovation in PCB engineering.
High-Quality Products
Opting for a professional FCBGA Substrate manufacturer guarantees the delivery of high-quality products. Our company utilizes advanced production equipment and enforces rigorous quality control processes to ensure each manufacturing step meets industry standards. From substrate selection to metallization, each phase undergoes meticulous monitoring, ensuring the stability and reliability of the final product.
Customized Solutions
Collaborating with a professional manufacturer allows you to access customized solutions tailored to the specific needs of your project. Recognizing that every project possesses unique design and performance requirements, we offer flexible solutions to ensure FCBGA Substrates fully align with your specifications and expectations. Through close collaboration, we provide tailor-made designs to meet the diverse needs of various application scenarios.
Advantages for Suppliers Choosing Our Company
Choosing our company as your FCBGA Substrates supplier brings notable advantages. In addition to delivering top-tier products and customized solutions, we prioritize open communication with our customers to deeply understand their requirements and offer timely assistance. Our customer service team, consisting of seasoned professionals, is committed to providing comprehensive technical support and valuable solution recommendations.
Overall, the choice of a reliable FCBGA Substrate manufacturer is a critical step in ensuring project success. Our company prides itself on superior manufacturing capabilities, high-quality products, and flexible solutions, committing to collaborative innovation in the electronics field.
What is the quotation of FCBGA Substrate?
Drawing on my decade of experience as a PCB engineer, I navigate these considerations with precision when evaluating FCBGA Substrate options.
Foremost, the manufacturing process emerges as a pivotal determinant in establishing the quotation for FCBGA Substrate. The quality of manufacturing processes holds direct sway over product performance and reliability. Incorporating advanced techniques such as multi-layer stacking, precision etching, and metallization during manufacturing ensures that the FCBGA Substrate not only meets design specifications but also enhances its longevity in service.
Additionally, material selection stands out as another critical factor influencing both the performance and cost of FCBGA Substrate. Opting for a substrate tailored to the specific application is paramount, ensuring that the material aligns with design requirements for electrical conductivity, heat resistance, mechanical strength, and other essential properties. This choice not only underpins product quality but also bears a direct impact on the quoted price.
When obtaining a quote for FCBGA Substrate, you also need to consider the size of the project. The size of production scale is directly related to production efficiency and cost sharing. Typically, large-scale production may result in lower unit prices, while small-scale production may result in higher unit prices due to relatively high cost sharing.
In addition, personalized customization is also an important factor affecting FCBGA Substrate’s quotation. If the project has customized requirements for specific requirements, such as special sizes, special processes, etc., this will have a direct impact on the quotation. Therefore, when choosing FCBGA Substrate, it is important to understand and clarify the specific customization needs of the project.
The pricing of FCBGA (Flip-Chip Ball Grid Array) substrates is not singularly determined by a solitary factor; rather, it results from a synergy of multiple elements including the manufacturing process, choice of materials, project scale, and customization demands. A profound comprehension of these factors, coupled with informed decision-making, becomes pivotal not only for ensuring product quality and performance but also for aligning with the project’s budget and specific requirements. In the swiftly evolving domain of electronic engineering, a holistic evaluation of FCBGA substrate quotations proves instrumental in steering the course toward successful project implementation.
Frequently Asked Questions (FAQs)
What kind of printed circuit board is FCBGA Substrate?
An FCBGA (Flip-Chip Ball Grid Array) substrate is a specialized printed circuit board meticulously crafted to accommodate and enhance the performance of Flip-Chip packaging technology. Distinguished by its unique structure and capabilities, this substrate is extensively utilized in high-tech domains, showcasing its importance in facilitating advanced electronic packaging solutions.
What types of FCBGA Substrate are there and what are their characteristics?
FCBGA Substrate is mainly divided into single-layer, multi-layer and rigid-flexible structures. Each type has unique design and advantages and can be selected according to specific application needs.
Among the many choices of circuit boards, why choose FCBGA Substrate?
FCBGA Substrate stands out among many circuit boards for its excellent heat dissipation performance and high-density connectivity, especially suitable for applications with stringent performance and space requirements.
In what fields is FCBGA Substrate widely used?
FCBGA Substrate is widely used in high-end electronic products, including servers, network equipment, graphics processors, etc. Its design flexibility and high performance make it a cutting-edge choice.
How to find a reliable FCBGA Substrate manufacturer?
Working with a professional FCBGA Substrate manufacturer is key to obtaining high-quality products and customized solutions, either through a supplier network or a manufacturer selection.
What are the factors to understand the quotation of FCBGA Substrate?
When getting a quote for FCBGA Substrate, you need to consider many aspects such as manufacturing process, material selection, and project size to make an informed decision.
By answering these questions in depth, we hope readers will gain a more comprehensive understanding of FCBGA Substrate’s features, benefits, and key role in modern electronic design.