What is a Final Thin PCB?
Final Thin PCB Manufacturer.Final Thin PCB Manufacturer specializes in producing ultra-thin printed circuit boards (PCBs) tailored for high-performance electronic applications. With state-of-the-art technology and stringent quality control, they deliver reliable and efficient PCBs that meet the demands of modern electronics, including smartphones, wearables, and medical devices. Their commitment to innovation ensures superior product performance and customer satisfaction in the ever-evolving tech landscape.
A Final Thin PCB (Printed Circuit Board) is a specialized type of circuit board that is designed to be exceptionally thin, making it ideal for applications that require lightweight and compact electronic components. These PCBs are often used in high-density electronic devices where space constraints and weight reduction are critical, such as in smartphones, tablets, medical devices, wearable technology, and aerospace applications.
The Types of Final Thin PCBs
There are several types of thin PCBs, each designed to meet specific requirements:
Single-Layer Thin PCBs: These PCBs have one layer of conductive material. They are used in simpler electronic devices and are cost-effective and easy to manufacture.
Double-Layer Thin PCBs: Featuring two layers of conductive material, these PCBs are used in devices that require more complex circuitry than single-layer PCBs can provide.
Multilayer Thin PCBs: These PCBs consist of multiple layers of conductive material, allowing for complex circuit designs and are used in advanced electronic devices such as smartphones and medical equipment.
Flexible Thin PCBs: Made from flexible materials, these PCBs can bend and fold, making them ideal for applications where the board needs to conform to a shape or fit into a tight space, such as in wearable devices.
Rigid-Flex Thin PCBs: Combining both rigid and flexible sections, these PCBs offer durability and flexibility, suitable for devices that require both properties in different areas of the board.
The Advantages of Final Thin PCBs
Final Thin PCBs offer numerous advantages:
Their thin profile allows for more compact designs, enabling the creation of smaller and lighter devices.
The reduced thickness and material usage result in lighter PCBs, beneficial in applications where weight is a concern, such as aerospace and portable electronics.
Thin PCBs can be designed to be flexible, which is advantageous for applications requiring the board to fit into irregular spaces or move with the device, such as wearable technology.
The use of advanced materials in thin PCBs can improve thermal management and electrical performance, enhancing the overall functionality of the device.
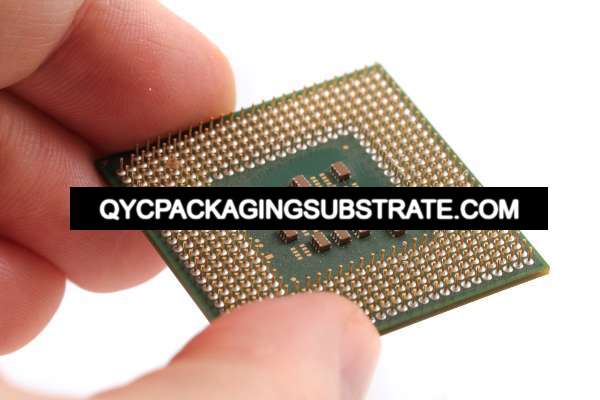
Final Thin PCB Manufacturer
Reduced material usage can lower manufacturing costs, making thin PCBs a cost-effective solution for large-scale production.
How to Design a Final Thin PCB?
Designing a Final Thin PCB involves several critical steps:
Choose materials that offer the necessary mechanical strength, thermal stability, and electrical properties while maintaining a thin profile.
Determine the number of layers needed based on the circuit’s complexity. Multilayer designs may be necessary for more advanced applications.
Optimize the layout of conductive traces to minimize resistance and signal loss. Pay attention to trace spacing to avoid short circuits and crosstalk.
Incorporate thermal vias and other cooling solutions to manage heat dissipation, especially in high-power applications.
Ensure the thin PCB has adequate mechanical support to prevent bending and breaking during manufacturing and use.
Collaborate with the PCB manufacturer to ensure the design is feasible and can be produced within the desired tolerances.
Why Use Final Thin PCBs Over Other Boards?
Using Final Thin PCBs offers several benefits over traditional PCBs:
They allow for the development of smaller, more portable electronic devices without sacrificing performance.
Thin PCBs reduce the overall weight of the device, which is crucial for applications like aerospace and wearable technology.
Thin and flexible PCBs can be used in applications where traditional rigid PCBs would be unsuitable.
The reduction in material usage can lead to lower production costs, especially in high-volume manufacturing.
Advanced materials used in thin PCBs can provide better thermal and electrical performance, leading to more efficient and reliable devices.
What is the Final Thin PCB Fabrication Process?
The fabrication process of Final Thin PCBs involves several precise steps:
Select and prepare thin laminate materials according to design specifications. These materials are typically thinner than those used in standard PCBs.
For multilayer PCBs, laminate the individual layers together under high temperature and pressure, ensuring proper alignment and bonding.
Drill holes for vias and component leads according to the design layout, ensuring precision to maintain the integrity of the thin PCB.
Plate the drilled holes and vias with copper to create electrical connections between the layers, ensuring reliable signal transmission and mechanical stability.
Use photolithography to transfer the circuit pattern onto the laminate material by coating it with a photosensitive film, exposing it to UV light through a mask, and developing the pattern.
Etch away the unwanted copper to reveal the desired circuit pattern, requiring precise control to ensure accurate and clean traces.
Apply a surface finish, such as ENIG (Electroless Nickel Immersion Gold) or HASL (Hot Air Solder Leveling), to protect the copper traces and ensure good solderability.
Perform electrical testing and visual inspection to verify the PCB’s performance and quality, including checking for impedance control, signal integrity, and overall functionality.
The Application of Final Thin PCBs
Final Thin PCBs are used in various high-end applications:
Found in smartphones, tablets, and wearable devices, where space and weight are critical.
Used in portable medical equipment and implants, requiring reliability and compactness.
Implemented in avionics and satellite systems, where weight reduction and performance are crucial.
Used in advanced driver-assistance systems (ADAS) and other electronic components in modern vehicles.
Found in high-frequency communication devices and networking equipment.
FAQs
What are the main advantages of Final Thin PCBs?
The main advantages include space efficiency, weight reduction, flexibility, enhanced performance, and cost-effectiveness.
What application areas are suitable for Final Thin PCBs?
Suitable areas include consumer electronics, medical devices, aerospace, automotive, and telecommunications.
What factors should be considered when designing a Final Thin PCB?
Consider material selection, layer configuration, trace layout, thermal management, mechanical support, and manufacturability.
Is the fabrication process of Final Thin PCBs complex?
Yes, the process involves multiple precise steps to ensure high-quality and high-performance PCBs.