Flip Chip (ABF) Substrate Manufacturer.Flip Chip (ABF) Substrate Manufacturer specializes in producing advanced packaging substrates that facilitate high-density interconnections for semiconductor devices. They focus on innovative design, precise manufacturing processes, and ensuring reliability in electronic assemblies.
In today’s digital world, Flip Chip (ABF) Substrate is an indispensable key component of electronic devices and plays a vital role. Understanding the definition, design and manufacturing process of Flip Chip (ABF) Substrate, as well as their wide range of applications and many advantages, is essential for professionals in the electronics and technology industries. This article aims to introduce Flip Chip (ABF) Substrate in depth, from basic knowledge to advanced applications, to fully demonstrate its importance and potential.
What is Flip Chip (ABF) Substrate?
Flip Chip (ABF) Substrate, the flip chip (ABF) substrate, is one of the key components in modern electronic devices. It consists of a flat plate of insulating material on which copper foil is etched using a precision process to form complex and detailed conductive lines, pads and other features for mounting and interconnecting electronic components.
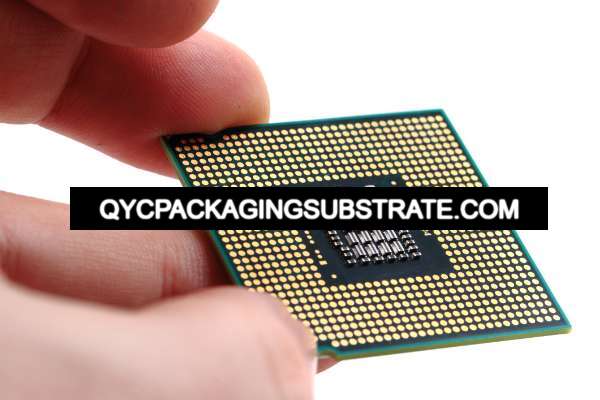
RF PCB Manufacturer
Flip chip technology is an advanced packaging technology that has significant advantages over traditional Wire Bonding technology. In Flip Chip (ABF) Substrate, the connection pins of the chip are directly connected to the pads on the substrate without using bonding wires. This design not only improves the performance and speed of the circuit, but also significantly reduces the size of the circuit, allowing electronic devices to be more compact and lightweight.
ABF (Ajinomoto Build-up Film) is a special substrate material with excellent thermal stability and mechanical properties, suitable for the manufacturing of high-density integrated circuits. Its manufacturing process includes multi-layer stacking and molding, which enables Flip Chip (ABF) Substrate not only to have good electrical properties, but also to operate stably under various environmental conditions.
Flip Chip (ABF) Substrate is widely used in communication equipment, computers, consumer electronics and industrial control systems. Its main advantages include high integration, good thermal conductivity and excellent signal integrity, making it widely used in applications with high frequency, high speed and high reliability requirements.
In short, Flip Chip (ABF) Substrate, as an important innovation in the field of electronic manufacturing, not only promotes the performance improvement and size reduction of electronic products, but also injects new vitality and possibility into modern scientific and technological progress.
Flip Chip (ABF) Substrate design Reference Guide.
The Flip Chip (ABF) Substrate Design Reference Guide is an important tool for engineers and designers when creating substrate layouts for electronic devices. This comprehensive handbook covers a range of key elements designed to ensure efficient and reliable Flip Chip (ABF) Substrate designs.
In Flip Chip (ABF) Substrate design, following best practices and design rules is critical. These rules cover layout optimization, signal integrity, electromagnetic compatibility (EMC), thermal management, and reliability design. For example, by optimizing layout and signal paths, signal interference and noise can be minimized, ensuring circuit stability and reliability.
Modern Flip Chip (ABF) Substrate design relies on advanced software tools such as PCB design software and simulation tools. These tools can help engineers with layout and routing, electrical rule checking (DRC), signal integrity analysis (SI), electromagnetic field simulation (EM), thermal simulation, etc. Through these tools, design teams can quickly iterate designs and discover and solve potential problems in advance, thereby improving design efficiency and quality.
The design of Flip Chip (ABF) Substrate also involves a variety of necessary technology and material selections. For example, how to choose suitable substrate materials (such as FR4 or high-frequency materials), conductor materials (such as copper), and surface treatment technologies (such as metallization) directly affect the performance and cost of the design. Engineers need to develop a deep understanding of the pros and cons of each material and technology to make the best choice based on specific application needs.
One of the key goals in the design of Flip Chip (ABF) Substrate is to ensure its quality and reliability. By adopting strict quality control standards and testing processes, such as raw material inspection, process control, finished product testing, etc., the defect rate during the manufacturing process can be effectively reduced and the performance stability and long-term reliability of each substrate can be guaranteed.
To sum up, the Flip Chip (ABF) Substrate Design Reference Guide is not only a manual about layout and connections, but also a guide about innovation and technological progress. By following best practices, leveraging advanced software tools, selecting appropriate technologies and materials, and ensuring quality and reliability, engineers and designers can effectively design and manufacture Flip Chip (ABF) Substrates that meet high requirements and advance electronics. Development and application in technological fields.
What material is used in Flip Chip (ABF) Substrate?
Flip Chip (ABF) Substrate, the flip chip (ABF) substrate, is a key electronic component substrate widely used in modern electronic devices. It usually uses FR4 (fiberglass reinforced epoxy laminate) as the main material. FR4 material is known for its excellent electrical insulation properties and mechanical strength, and is suitable for use in the manufacture of various rigid substrates.
The manufacturing process of FR4 involves impregnating fiberglass cloth with epoxy resin and pressing it under high temperature and pressure. This material can not only effectively isolate circuit layers and prevent short circuits between circuits, but can also withstand high mechanical stress and ensure the stable operation of electronic equipment in complex environments.
In addition to FR4, for flexible electronic applications, such as folding screens or flexible circuit boards in mobile devices, Flip Chip (ABF) Substrate can also be made of flexible materials such as polyimide (PI). Polyimide has excellent high temperature stability, chemical stability and flexibility, making it ideal for applications that require bending and deformation.
Overall, the material selection of Flip Chip (ABF) Substrate is related to the performance and reliability of its final application. FR4 provides a strong and stable support structure, while polyimide provides an ideal solution for flexibility and bending needs. As electronic technology advances and market demands continue to change, material selection for Flip Chip (ABF) Substrate will continue to evolve and innovate to meet a wider range of application needs.
What size are Flip Chip (ABF) Substrate?
The size of Flip Chip (ABF) Substrate varies due to the diversity of its application areas. Whether for micro applications in smartphones and wearables, or large applications in industrial equipment or power electronics, the dimensions of the substrate are precisely designed and customized based on the specific electronic component dimensions and the space available inside the device.
In modern mobile devices, such as smartphones and wearables, Flip Chip (ABF) Substrate is often very miniaturized. This is because these devices require compact circuit boards to accommodate a variety of complex electronic components such as processors, memories, sensors, etc. The miniaturized substrate not only saves space, but also contributes to the portability and portability of the device, meeting the needs of modern consumers for mobile devices.
In comparison, Flip Chip (ABF) Substrates used in industrial equipment and power electronics are generally larger. Electronic devices in these applications often need to handle higher currents and powers, requiring more space to accommodate more electronic components and complex circuits. The large base plate not only provides enough space to arrange components, but also ensures good thermal dissipation and electrical isolation performance to cope with various challenges and requirements in industrial environments.
Whether micro or large, the size design of Flip Chip (ABF) Substrate is crucial. Precise dimensional design can not only meet the functional requirements of the device, but also optimize circuit layout and improve overall performance and reliability. As technology advances and market demands continue to change, the dimensions of Flip Chip (ABF) Substrate will continue to evolve and be optimized to meet the needs of emerging applications and increasingly complex electronic devices.
In short, Flip Chip (ABF) Substrate is one of the key electronic components. Its flexible design and precise control of size provide powerful support and solutions for various application scenarios, promoting the continuous progress and innovation of electronic technology.
The Manufacturer Process of Flip Chip (ABF) Substrate.
The manufacturing process of Flip Chip (ABF) Substrate is a complex and precise project involving multiple key steps, each of which has an important impact on the quality and performance of the final product.
First, the process of manufacturing Flip Chip (ABF) Substrate starts with substrate preparation. The commonly used substrate material is FR4 (fiberglass reinforced epoxy laminate), which has good mechanical strength and electrical insulation properties and is very suitable for the manufacture of electronic equipment. Substrates require rigorous cleaning and surface treatment before manufacturing to ensure good adhesion and stability of the final product.
Next comes the deposition of the copper layer. On the surface of the substrate, a thin layer of copper foil is deposited through chemical or electrochemical methods. This layer of copper foil will become the conductive layer for subsequent circuit connections. Its good conductivity and good soldering performance are crucial to the performance of the entire circuit board.
Photoresist application and exposure are the next critical steps. A layer of photoresist is coated on the copper foil, and then photolithography is used to expose it through a template, so that the photoresist forms a pattern in the area that needs to be etched. This step determines the precision and accuracy of subsequent etching, which directly affects the electrical performance and stability of the circuit board.
This is followed by an etching step, where the parts of the copper foil that are not protected by the photoresist are removed through chemical etching to form the pattern and structure of the circuit connections. The control of the etching process requires precise chemical concentration and time control to ensure that the etched circuit pattern is clear and precise.
Next comes drilling. On the already formed circuit board, holes need to be drilled in order to mount the electronic components and connect the wires between the different layers. The location and diameter of the drill holes need to be precisely controlled to ensure the accuracy and stability of subsequent component installation and welding.
Then comes the installation and welding of the components. Electronic components are accurately installed at predetermined positions through automated equipment and connected to the wires of the circuit board through soldering technology (such as surface mount technology (SMT) or through-hole mounting technology). This step requires highly precise equipment and operations to ensure the correctness of each component and the overall reliability of the circuit.
Finally comes the testing phase. The manufactured Flip Chip (ABF) Substrate will undergo rigorous functional and performance testing to verify the correctness, stability and durability of the circuit. Conduct electrical testing and functional verification through automated test equipment to ensure products meet design requirements and end-user expectations.
In summary, the manufacturing process of Flip Chip (ABF) Substrate is a highly technical and precise process, covering substrate preparation, copper layer deposition, photoresist application and exposure, etching, drilling, component mounting, and welding and testing. The precise control and process optimization of these steps directly determine the quality and performance of the final product, which is suitable for various high-demand electronic applications.
The Application area of Flip Chip (ABF) Substrate.
Flip Chip (ABF) Substrate, as a key technology in modern electronic equipment, has been widely used in many industries and has become an important part of various equipment. Its flexibility and performance advantages make it the basis for many innovative products, from consumer electronics to high-end industrial applications.
In the field of consumer electronics, the application of Flip Chip (ABF) Substrate is particularly prominent. High-density circuit boards in smartphones and tablets leverage their compact design and efficient heat dissipation properties to enable device miniaturization and high performance. These substrates also support complex processor and graphics chip layouts, providing users with superior computing and graphics performance.
Flip Chip (ABF) Substrate is also widely used in the communications industry. In mobile communication equipment, base stations and communication network equipment, these substrates provide reliable signal transmission and processing capabilities, support fast data transmission and network connection stability, and meet the needs of modern communication technology for high-speed and high-frequency transmission.
In the automotive industry, applications for Flip Chip (ABF) Substrate cover everything from in-vehicle infotainment systems to vehicle safety and control systems. Not only are they resistant to harsh environmental conditions and vibrations, they also provide efficient electrical performance and thermal management, ensuring the stability and reliability of vehicle electronic systems.
The requirements in the aerospace field are more stringent, and Flip Chip (ABF) Substrate plays an important role in avionics and satellite platforms through its lightweight, high performance and radiation resistance properties. These substrates not only provide advanced circuit functions, but are also able to withstand extreme temperature and pressure environments, ensuring long-term stable operation of aerospace equipment.
The field of medical equipment has extremely high requirements on the reliability and safety of electronic devices, and Flip Chip (ABF) Substrate is widely used in these equipment. From medical imaging equipment to portable medical diagnostic tools, these substrates support complex sensors and data processing devices, providing precise and reliable technical support for healthcare.
The industrial automation field is also adopting Flip Chip (ABF) Substrate due to its requirements for reliability and durability. Industrial control systems, robotics and automation equipment use these substrates to achieve efficient data processing and control functions, promoting factory intelligence and improving production efficiency.
To sum up, Flip Chip (ABF) Substrate, as a core component of modern electronic technology, not only meets the needs of many industries for high-performance, high-reliability electronic solutions, but also promotes the innovation and development of products in various industries. As technology advances and application fields expand, these substrates will continue to play an important role in future electronic devices.
What are the advantages of Flip Chip (ABF) Substrate?
Flip Chip (ABF) Substrate has significant multiple advantages over traditional wiring methods in the design and manufacturing of electronic devices.
First, the compactness of Flip Chip (ABF) Substrate is one of its outstanding features. By using this technology, electronic components can be arranged more closely on the substrate, effectively miniaturizing and lightweighting the device. This compact design not only saves space, but also improves device performance and efficiency, especially in applications that require high-density integration, such as mobile devices and wearable technology.
Second, Flip Chip (ABF) Substrate ensures a high level of reliability and consistent quality through standardized manufacturing processes. Automation technology and strict quality control measures in the manufacturing process effectively reduce the possibility of manufacturing defects and ensure the stability and reliability of each production unit. This is particularly important for applications that require long-term stable operation and high reliability, such as medical equipment and aerospace systems.
Third, Flip Chip (ABF) Substrate has the advantages of high assembly efficiency and easy assembly. Compared with traditional through-hole mounting technology, Flip Chip technology can achieve a faster and more accurate automated assembly process, greatly shortening the production cycle, reducing labor costs, and improving overall production efficiency.
In addition, Flip Chip (ABF) Substrate has strong customization capabilities. Designers can customize designs based on specific application needs, including complex circuits and the integration of multiple components. This flexibility makes Flip Chip technology particularly suitable for a variety of different application scenarios, from consumer electronics to industrial automation, and can meet the needs of different industries.
Finally, Flip Chip (ABF) Substrate is able to significantly reduce unit costs due to its ability to adapt to mass production. Through efficient production processes and affordable material selection, Flip Chip technology makes large-scale manufacturing possible, bringing significant cost advantages to enterprises, especially in the consumer electronics market that requires mass production.
To sum up, Flip Chip (ABF) Substrate not only brings significant progress in technology, but also has obvious advantages in economic benefits and production efficiency, providing important support for the design and manufacturing of modern electronic equipment. and driving force.
FAQ
What is Flip Chip (ABF) Substrate?
Flip Chip (ABF) Substrate is a common basic component in electronic devices that supports and connects electronic components. It etches copper foil on an insulating substrate to form conductive paths and connection points for assembly and interconnection of electronic components.
How is Flip Chip (ABF) Substrate different from other substrates?
Compared with traditional circuit boards, Flip Chip (ABF) Substrate has a higher integration level and compact design. It allows for shorter signal transmission paths by directly flipping chip connections, improving circuit performance and reliability.
What applications is Flip Chip (ABF) Substrate suitable for?
Flip Chip (ABF) Substrate is widely used in high-performance electronic equipment, such as communication equipment, servers, high-density storage devices and network equipment. Its compact design and high-speed signal transmission characteristics make it particularly suitable for applications requiring speed and reliability.
What are the main advantages of Flip Chip (ABF) Substrate?
The main advantages of Flip Chip (ABF) Substrate include compact layout, high-performance signal transmission, reliable connections and good thermal management capabilities. It can also achieve a high degree of integration of complex circuits and multi-level component connections, improving the functionality and competitiveness of devices.