A leading manufacturer in the realm of Flip Chip Ball Grid Array substrates, we specialize in crafting innovative solutions that redefine industry standards. With cutting-edge technology and meticulous craftsmanship, we engineer substrates of unparalleled quality and precision. Our dedication to excellence ensures optimal performance and reliability in every substrate produced. From concept to completion, we prioritize customer satisfaction, offering tailored solutions to meet diverse needs. As pioneers in the field, we continually push boundaries, driving advancements and setting new benchmarks for Flip Chip Ball Grid Array substrate manufacturing worldwide.
Flip Chip Ball Grid Array Substrate (FCBGA substrate) is an advanced integrated circuit packaging technology that plays a vital role in modern technology applications. This technology achieves high-performance, high-density circuit packaging by directly flipping the chip and using solder balls to connect the chip and the substrate. This article will delve into the definition, design principles, manufacturing process and wide range of application fields of FCBGA substrates to help readers fully understand the importance and advantages of this key technology.
What is Flip Chip Ball Grid Array Substrate?
Flip Chip Ball Grid Array Substrate (FCBGA) substrate is an innovative integrated circuit packaging technology. Its unique feature is that the chip is flipped directly on the surface of the substrate, and the chip and the substrate are connected through a series of tiny solder balls. This innovation in design concept brings many advantages. First of all, compared with traditional packaging methods, FCBGA substrates can improve the performance and reliability of circuits. By directly connecting the chip to the substrate, the transmission path is shorter and the signal transmission speed is faster, thereby improving the working efficiency and stability of the circuit. Secondly, the design of FCBGA substrate can also achieve higher integration. Because the chip is directly connected to the substrate without the need for additional wires or connectors, a more compact circuit layout can be achieved, saving space and improving system integration. In addition, the FCBGA substrate also has good heat dissipation performance. Since the chip is directly connected to the surface of the substrate, heat can be transmitted to the substrate more effectively and then dissipated into the external environment, thereby reducing the temperature of the circuit during operation and improving the stability and reliability of the system. In general, FCBGA substrate, as an advanced integrated circuit packaging technology, can not only improve the performance and reliability of the circuit, but also achieve higher integration and good heat dissipation performance, providing design and manufacturing of modern electronic products. A new solution.
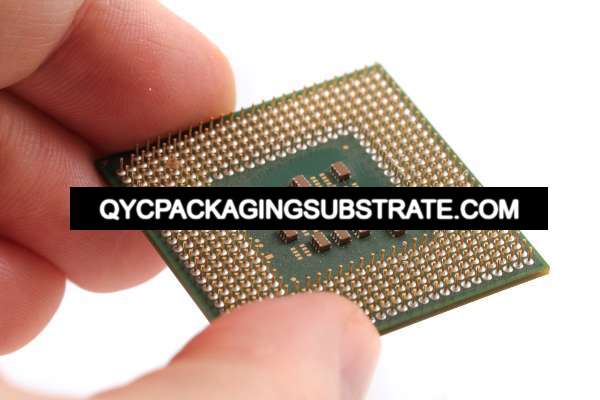
Flip Chip Ball Grid Array Substrate Manufacturer
Flip Chip Ball Grid Array Substrate design Reference Guide.
The design principle of FCBGA substrate is a complex and precise project, involving multiple considerations, including key elements such as chip wiring, solder ball arrangement, and substrate material selection. Designers must consider these factors comprehensively when designing FCBGA substrates to ensure that the final product can achieve optimal performance.
First, chip routing is one of the critical steps in the design process. Designers need to properly plan the circuit connections inside the chip to ensure smooth and stable signal transmission. By optimizing the wiring design, the performance and efficiency of the circuit can be maximized.
Secondly, solder ball arrangement is also one of the important factors affecting the performance of FCBGA substrate. The density, arrangement and connection method of solder balls will directly affect the heat dissipation effect of the substrate and the stability of signal transmission. Designers need to carefully design the solder ball arrangement based on specific application needs and technical requirements to achieve optimal performance.
In addition, the choice of substrate material is also crucial. Different substrate materials have different thermal conductivity, mechanical strength and dielectric properties, which directly affect the heat dissipation effect and signal transmission quality of the FCBGA substrate. Designers need to select appropriate substrate materials based on actual conditions to ensure the stability and reliability of the substrate.
To sum up, the design principle of FCBGA substrate involves multiple considerations, including key elements such as chip wiring, solder ball arrangement, and substrate material selection. Designers need to comprehensively consider aspects such as circuit layout, heat dissipation effect, and signal transmission stability to ensure that the final product can achieve optimal performance. Only with the comprehensive optimization of these key factors can the FCBGA substrate exert its greatest potential and provide solid support for the performance improvement and innovation of various electronic products.
What material is used in Flip Chip Ball Grid Array Substrate?
As an advanced integrated circuit packaging technology, Flip Chip Ball Grid Array Substrate (FCBGA)’s performance and reliability are directly affected by the selected materials. In the manufacturing process of FCBGA substrate, the following key materials are usually used:
Substrate material
The main carrier of FCBGA substrate is usually composed of glass fiber reinforced epoxy resin (FR-4). FR-4 substrate has good insulation properties, mechanical strength and heat resistance, making it suitable for most electronic applications.
Metal layer
FCBGA substrates usually need to be coated with a layer of metal for conductive connections to the circuit. Commonly used metals include copper, nickel, gold, etc., which have excellent electrical conductivity and corrosion resistance, ensuring the stability and reliability of circuit connections.
Solder ball
Solder balls are the key component connecting the chip to the substrate and are usually made of tin alloy. The material selection of the solder ball directly affects the stability of the welding process and the quality of the welding connection, so it is necessary to select an appropriate solder ball material to ensure the reliability of the connection.
Packaging materials
The packaging material of FCBGA substrate is usually composed of epoxy resin, silicone and other materials. The selection of packaging materials mainly takes into account their insulation performance, heat resistance and compatibility with other materials to ensure the packaging effect and appearance quality.
The material selection of FCBGA substrate directly affects its performance, reliability and cost, so it needs to be comprehensively considered during the design and manufacturing process. With the continuous advancement of science and technology and the continuous innovation of material technology, it is believed that the materials of FCBGA substrate will be continuously optimized and upgraded, bringing more advanced and reliable integrated circuit packaging solutions to the electronics industry.
What size are Flip Chip Ball Grid Array Substrate?
Flip Chip Ball Grid Array Substrate (FCBGA) substrate sizes vary depending on application needs and can be customized to specific chip packaging requirements. Generally speaking, the size of the FCBGA substrate usually depends on the size of the chip, the number of pins, and the requirements for system integration.
In practical applications, the size of the FCBGA substrate can range from a few millimeters to tens of millimeters, depending on the packaging density and functional requirements of the chip. For high-performance applications such as large data center servers or network equipment, larger size FCBGA substrates are usually required to accommodate more chips and pins to achieve higher processing capabilities and data throughput.
On the other hand, for lightweight applications such as portable devices and embedded systems, smaller size FCBGA substrates may be required to save space and enable more compact designs. In this case, designers often use higher-density chip packaging technology and more compact layouts to ensure the required functionality and performance within limited space.
In general, the size of the FCBGA substrate can be flexibly adjusted to a large extent to meet the needs of different application scenarios. Through a customized design and manufacturing process, precise control of the FCBGA substrate size can be achieved to achieve optimal performance and reliability. With the continuous advancement of technology and the continuous expansion of applications, we can expect that the size of FCBGA substrates will continue to develop in the direction of smaller and higher density in the future to meet the growing demand for electronic products.
The Manufacturer Process of Flip Chip Ball Grid Array Substrate.
Manufacturing Flip Chip Ball Grid Array Substrate (FCBGA) substrates is a complex and precise process involving multiple links to ensure the quality and reliability of the final product. The manufacturing process will be described in detail below.
Substrate production
The production of FCBGA substrate begins with the design and material selection of the substrate. High-quality fiberglass reinforced epoxy resin (FR-4) is typically used as the substrate material. First, a layer of copper foil is coated on the FR-4 substrate, and then the circuit pattern is transferred to the copper foil using photolithography technology. Unnecessary copper foil is then removed through chemical etching or mechanical cutting, leaving the desired circuit pattern.
Solder ball mounting
After the substrate is made, solder ball installation is the next critical step. The process involves adhering small balls of solder to pads on the substrate. These small balls are usually made of tin alloy, using sophisticated equipment and technology to ensure their precise arrangement and even distribution. The quality and precision of the solder balls are critical to the final quality of the solder.
Chip flipping
Next is the step of flipping the chip onto the substrate. This requires aligning the chip’s connection pins with the solder balls on the substrate and using a sophisticated hot-pressing process to solder the chip and substrate together. This ensures good electrical connection and thermal management while minimizing resistance and inductance between the chip and the substrate.
Encapsulation
Encapsulation is the process of protecting chips and substrates from mechanical damage and environmental factors. During the packaging process, epoxy or other packaging materials are typically used to cover the entire chip and substrate to form a protective shell. This ensures circuit stability and reliability while increasing product durability.
Test
The last critical step is to test the fabricated FCBGA substrate. This includes comprehensive inspection and testing of circuit connections, soldering quality, package integrity, and electrical performance. Only through rigorous testing can we ensure that the final product meets the design requirements and has stable and reliable performance.
Precision equipment and technical support are crucial throughout the entire process of manufacturing FCBGA substrates. Only through strict quality control and process control can FCBGA substrates that meet high standards be produced to meet the needs of different industries for high-performance and high-reliability electronic products.
The Application area of Flip Chip Ball Grid Array Substrate.
Flip Chip Ball Grid Array Substrate (FCBGA) substrate has a wide range of applications, covering many fields such as computers, communications, consumer electronics, and medical equipment. Its application in these fields benefits from its high density, high performance and reliability, making it the packaging technology of choice for a variety of electronic products.
In the computer field, FCBGA substrates are widely used in servers, workstations, personal computers and other equipment. Its high-density design allows for smaller package sizes, thereby providing necessary support for the high performance of the device. At the same time, the superior thermal management performance of the FCBGA substrate also makes it an ideal choice for processors and other key components, ensuring that the equipment maintains stable performance when operating under high loads.
In the field of communications, FCBGA substrates are widely used in network equipment, base stations, routers, switches and other communication equipment. Its high performance and reliability can meet the needs of communication equipment for data processing speed and stability, thus ensuring the smoothness and reliability of the communication network.
In the field of consumer electronics, FCBGA substrates are widely used in smartphones, tablets, cameras, game consoles and other products. Its small package size and high performance can meet consumers’ needs for thinness, portability and high performance, thereby providing greater flexibility and innovation space for the design of consumer electronics products.
In the field of medical equipment, FCBGA substrates are widely used in various medical diagnostic equipment, monitoring equipment, treatment equipment and other products. Its high reliability and stability can ensure the reliable operation of medical equipment at critical moments, thus providing an important guarantee for the development of the medical industry and human health.
To sum up, the wide application of FCBGA substrates in computers, communications, consumer electronics, medical equipment and other fields not only reflects its high performance and reliability, but also provides important support and guarantee for the development and innovation of various industries. With the continuous advancement of technology and the continuous expansion of application scenarios, the application prospects of FCBGA substrates will be broader, injecting new impetus into the development and intelligentization of electronic products.
What are the advantages of Flip Chip Ball Grid Array Substrate?
FCBGA substrate has a series of obvious advantages over traditional packaging technology. First, its small size and light weight allow electronic products to be more compact in design, resulting in a smaller and lighter form factor. This is particularly important for mobile devices, embedded systems and portable electronics, as users increasingly demand product lightness and portability.
Secondly, the FCBGA substrate has excellent heat dissipation effect. As the performance of electronic devices becomes higher and higher, heat dissipation issues become more and more prominent. The FCBGA substrate effectively promotes heat conduction and dissipation through its design structure and material selection, thereby reducing the operating temperature of electronic components, extending the service life of the equipment, and improving the stability and reliability of the system.
In addition, FCBGA substrates can also meet the high performance and reliability requirements of modern electronic products. Its structural design and manufacturing process can achieve high-density chip layout and connections, thereby improving circuit integration and operating speed. This is particularly important for application scenarios that require processing large amounts of data and complex operations, such as artificial intelligence, cloud computing, and high-performance computing.
In general, FCBGA substrate, as an advanced integrated circuit packaging technology, provides strong support for the design and manufacturing of modern electronic products. Its small size, light weight, good heat dissipation effect and high performance reliability make it the preferred packaging solution in various fields. With the continuous development of technology, it is believed that FCBGA substrates will play a more important role in the future, injecting new vitality into technological innovation and industrial development.
FAQ
What are the advantages of FCBGA substrate compared with other packaging technologies?
FCBGA substrate has higher integration and performance density than traditional packaging technologies (such as QFP, BGA, etc.). Its flip-chip packaging method enables shorter signal paths and better heat dissipation, thereby improving the speed and reliability of the circuit.
Is the manufacturing process of FCBGA substrate complicated?
The process of manufacturing FCBGA substrates is indeed complex and involves multiple links, including substrate production, solder ball installation, chip flipping, packaging and testing. Each link requires highly sophisticated equipment and technical support to ensure the quality and reliability of the final product.
What application fields is FCBGA substrate suitable for?
FCBGA substrates are suitable for a variety of electronic products that require high performance and reliability, including computers, communication equipment, consumer electronics, industrial control, and medical equipment. Its high density and high performance characteristics make it one of the preferred packaging technologies in these areas.
What aspects should be paid attention to when designing FCBGA substrate?
When designing an FCBGA substrate, multiple factors need to be considered, including chip layout, solder ball arrangement, substrate material selection, and heat dissipation design. Reasonable design can ensure the stability and reliability of the circuit and maximize the performance advantages of the FCBGA substrate.