Global package Substrate Manufacturer. Professional engineering team, large scale packaging substrate production line. the Package Substrate will be made with BT, Showa Denko and Ajinomoto High speed materials. or other types materials.
Package substrate, also known simply as substrate, constitutes a fundamental element in the packaging and interconnection of electronic devices. Comprising multiple layers of insulating material overlaid with conductive pathways and connection points, it serves to support and interconnect chips, devices, and other electronic components. Within electronic products, the package substrate functions as a nexus, linking diverse components such as chips, crystal oscillators, and resistors to construct a cohesive circuit system. This substrate furnishes stable foundational support and dependable electrical connections, thereby enhancing circuit performance and stability.
Moreover, the package substrate offers robust signal transmission channels, facilitating high-speed data transmission and signal processing. It aids in optimizing circuit layout and design, thereby augmenting overall system performance. Additionally, the substrate assumes a crucial role in heat dissipation, effectively dissipating heat generated by devices to maintain the system within its normal operating temperature range. This, in turn, prolongs the service life of electronic products.
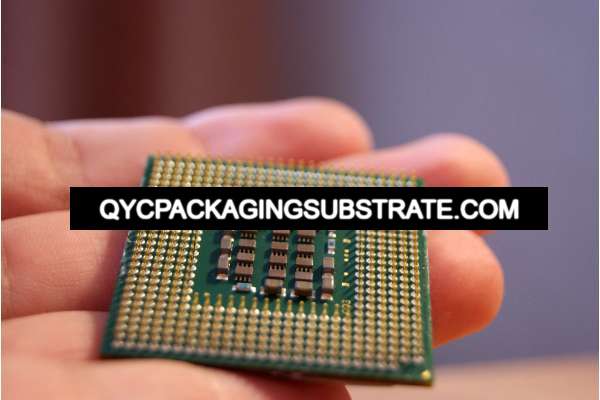
Global package Substrate Manufacturer
Package substrates play a crucial role in the electronics sector, serving as foundational elements in diverse electronic products while ensuring optimal performance and stability. As technology advances and electronic devices become more sophisticated, the demand for package substrates is expected to grow, opening up new avenues for industry development and innovation.
What are the different types of Package Substrate?
Globally, Package Substrate is a vital part of the electronics industry. As substrates for connecting and packaging electronic components, they play a key role in different application scenarios. The following are several common Package Substrate types and their characteristics:
HDI board is a high-density interconnect board with higher line density and smaller package size. Its main features include:
High density: HDI boards use advanced process technology to achieve more circuit levels and a more compact layout.
With a flexible structure, they come in various shapes and sizes, and their connection parts utilize special technology for good connectivity and durability. Rigid-Flex boards are commonly employed in electronic devices requiring bending or folding, such as foldable mobile phones and smart wearable devices.
Integrated Circuit (IC) packaging substrates, designed for IC packaging and connection, boast high integration through special packaging processes. With efficient heat dissipation capabilities, they are often integrated with high-power chips. IC packaging substrates find wide application in computers, communication equipment, automotive electronics, and other fields, providing essential support for diverse electronic products.
Beyond the mentioned types, there are specialized Package Substrates like high-frequency boards and metal substrates, each tailored for specific application scenarios with unique performance characteristics. Design, manufacturing, and application considerations vary across different types of Package Substrates, allowing customers to select the most suitable type based on their needs and application contexts for optimal performance and effects.
What are the advantages of Package Substrate?
Package Substrate offers distinct advantages over traditional circuit boards, positioning it as a crucial element in the contemporary electronics industry. Leveraging advanced multi-layer stacking technology, Package Substrate enables increased functional integration within a smaller footprint, resulting in more compact and lightweight electronic products. This high-density design not only boosts product performance but also facilitates easier portability and installation.
Furthermore, Package Substrate provides precise control over signal transmission paths, effectively mitigating interference, signal loss, and crosstalk. This improvement enhances overall signal integrity and system stability. Additionally, Package Substrate efficiently manages the dissipation of electronic device heat, preventing performance degradation and failures caused by overheating, ensuring long-term product reliability.
In terms of manufacturing, Package Substrate benefits from automated and intelligent processes, enhancing production efficiency and significantly reducing manufacturing costs. Through optimized design, technology utilization, and minimized material wastage and labor input, customers can access competitively priced products, ultimately increasing profit margins.
Furthermore, Package Substrate offers customization options tailored to specific customer requirements, catering to diverse application scenarios such as communication, medical, and automotive electronics. This flexibility enables innovation and competitive differentiation.
Another key advantage is the shortened product development cycle and faster time to market facilitated by Package Substrate’s efficient design and manufacturing processes. This allows customers to seize market opportunities swiftly, driving business growth and ensuring sustainable development.
In summary, Package Substrate stands out across multiple fronts, including integration, signal integrity, thermal management, manufacturing efficiency, customization, and expedited time to market. These advantages not only improve product performance and cut down costs but also strengthen enterprise competitiveness, promoting sustainable growth.
How is Package Substrate made?
Global package substrate manufacturers typically follow a detailed manufacturing process comprising several critical stages to ensure the quality and performance of their products.
Firstly, the process initiates with the design phase. Designers utilize specialized software to craft design blueprints for the package substrate. This entails establishing hierarchy, layout, wire paths, connection points, and other pertinent aspects. These design blueprints serve as a roadmap for subsequent manufacturing phases.
Following this, the manufacturing process progresses to lamination, a pivotal stage where various materials are layered according to design specifications. The layered materials undergo high temperatures and pressures to guarantee proper adhesion and stability between the layers.
After completing the lamination process, attention turns to drilling and metallization. This involves creating holes in the package substrate and applying metal coatings where necessary to establish wire paths and connection points essential for linking chips, devices, and other electronic components.
The manufacturing process undertaken by global package substrate manufacturers involves several critical stages, including design, material procurement, lamination, drilling, metallization, and processing/testing. Throughout each phase, precise execution and rigorous quality control procedures are essential to ensure compliance with design specifications and industry standards. This comprehensive approach guarantees that the final product meets the high-quality and performance expectations of customers.
In what fields is Package Substrate applied?
Package substrate offers a broad spectrum of applications across various sectors, owing to its versatility and exceptional performance characteristics. Let’s delve into some key domains where package substrate enhances product performance and functionality:
Communications Industry: Package substrate finds extensive usage in mobile phones, base stations, and communication equipment. Its utilization enables higher integration and smaller package sizes, leading to lighter and more portable devices. Additionally, its superior signal transmission capabilities and effective thermal management enhance the performance and stability of communication equipment, ensuring reliable and high-quality signal transmission.
Computer and Data Centers: In this domain, package substrate is prevalent in servers, network equipment, and storage systems. It facilitates higher integration and processing performance, thereby enhancing data processing and storage efficiency. Moreover, package substrate optimizes circuit layout and signal transmission paths, bolstering system stability and reliability even under high load conditions.
Automotive Electronics: Package substrate is extensively employed in automotive entertainment systems, driving assistance systems, and vehicle communication equipment. It facilitates the creation of compact package sizes and heightened integration levels, leading to improved performance and functionality in automotive electronics. Moreover, its robustness against vibrations and temperature variations in challenging environmental conditions ensures the stability and reliability of electronic systems in vehicles.
Medical Equipment: Within the realm of medical equipment, package substrate finds application in diagnostic tools, monitoring devices, and treatment systems. It enables enhanced accuracy and quicker data processing, thereby elevating diagnostic precision and treatment effectiveness. Additionally, package substrate exhibits resistance to electromagnetic interference and vibrations prevalent in medical settings, ensuring the dependable operation of equipment in clinical environments.
In summary, package substrate plays a crucial role in advancing and innovating across the communications, computer, automotive, and medical sectors by enhancing product performance and functionality. As technology progresses and application domains expand, package substrate will remain a driving force propelling the electronics industry forward.
How to get Package Substrate?
As a customer, obtaining Package Substrate is an important part of realizing the design and production of electronic products. When choosing the right vendor for a high-quality Package Substrate, there are several key factors to consider.
As a customer, there are several channels available to acquire Package Substrate. One option is direct contact with manufacturers or suppliers to explore their product range, quality standards, and delivery times. Alternatively, Package Substrate can be obtained through reseller channels, offering more flexibility and choice. Moreover, suitable suppliers can be discovered through online platforms and industry exhibitions.
Choosing the appropriate supplier is vital for guaranteeing the quality of package substrate. Initially, it is crucial to validate the supplier’s reputation and trustworthiness by reviewing customer feedback and industry accolades. Secondly, the supplier should provide product varieties and specifications that match your needs, with the inclusion of customization possibilities. Furthermore, evaluating the supplier’s production capabilities and ensuring a stable supply is essential to prevent any disruptions to your production timeline.
This ensures the provision of high-quality Package Substrate along with timely technical support and after-sales service. Establishing long-term, stable partnerships is recommended to access more resources and support, facilitating mutual product innovation and quality enhancement.
In conclusion, as a customer, selecting the right supplier and choosing appropriate channels for obtaining Package Substrate are crucial steps in ensuring product quality and production efficiency. By carefully evaluating supplier reputation, product quality, and service levels, you can secure high-quality Package Substrate tailored to your needs, fostering business development opportunities and value creation.
What are the considerations for getting a quote for Package Substrate?
When acquiring a quote for Package Substrate, it’s essential to consider various key factors to secure the best offer. Firstly, understanding the product’s specifications and requirements is crucial. Different types of Package Substrate may have distinct design needs and technical standards. Hence, clear specifications aid manufacturers in accurately estimating costs and providing corresponding quotations.
Secondly, material selection and quality significantly impact both performance and cost. Therefore, assessing a supplier’s material sources, quality control, and certifications is vital. Premium materials not only ensure product stability and reliability but also minimize future maintenance and replacement expenses.
Moreover, the production process and technical expertise are critical determinants of the quotation. Advanced production methods and technical equipment enhance efficiency and lower manufacturing costs, resulting in more competitive quotations. Hence, evaluating a supplier’s production capacity and technical prowess is necessary to meet product quality and delivery demands.
Moreover, the size of the quotation is influenced by the volume of orders and delivery timeframes. Generally, larger orders result in lower unit prices, but expedited delivery may incur higher processing costs for manufacturers.
In conclusion, effective negotiation and collaboration play pivotal roles in obtaining the best offer. Establishing a robust cooperative relationship and engaging in proactive and constructive communication and negotiation with suppliers allow both parties to identify solutions that optimize benefits. Additionally, staying informed about market conditions and competitors’ prices ensures access to the most competitive quotations.
In summary, when obtaining a quotation for Package Substrate, customers should thoroughly consider factors such as product specifications, material quality, production processes, order volume, delivery timelines, etc. Active and effective communication and collaboration with suppliers are essential to ensure the most favorable price quotation, ultimately leading to a mutually beneficial outcome.
What are the frequently asked questions about Package Substrate?
How can Package Substrate reliability be improved?
Enhancing Package Substrate reliability involves rigorous quality control measures, comprehensive testing protocols, and continuous improvement in manufacturing processes. Additionally, collaborating closely with material suppliers and adopting industry standards contribute to improved reliability.
What are the common challenges associated with Package Substrates?
Package Substrates, while offering numerous advantages, may encounter some common challenges. Understanding these issues is crucial for effective utilization.
How does thermal management impact Package Substrates?
One common concern is thermal management. Achieving optimal heat dissipation is vital for maintaining the reliability and longevity of electronic components on Package Substrates.
Are there signal integrity issues with Package Substrates?
Signal integrity is a critical factor. Users may face challenges related to signal quality, crosstalk, and impedance matching when using Package Substrates.
What about compatibility with different components and technologies?
Ensuring compatibility with various electronic components and emerging technologies is essential. Users may encounter issues when integrating Package Substrates into diverse systems.
How can reliability be affected during the manufacturing process?
Manufacturing processes may introduce challenges related to product reliability. Understanding and addressing these issues are crucial for maintaining consistent quality.