We are a professional Global Semiconductor Substrate Manufacturer, we mainly produce ultra-small bump pitch package substrate, ultra-small trace and spacing. High quality and fast lead time.
Semiconductor substrates are fundamental components within the modern electronics industry, serving as essential materials for fabricating integrated circuits. Essentially, a semiconductor substrate acts as a foundational platform that accommodates and interconnects electronic elements within a chip, while also fulfilling supportive and conductive roles. Let’s delve deeper into the significance and functions of semiconductor substrates.
This fixed arrangement not only furnishes mechanical support to ensure the chip’s stable operation on the circuit board but also aids in regulating heat dissipation and voltage distribution within the circuit. Consequently, it plays a pivotal role in upholding the stability and dependability of electronic components.
Secondly, the semiconductor substrate provides connection and conductive functions between electronic components. Through the wires and connectors on the substrate, effective communication and data transmission can be carried out between various electronic components. This connection function not only allows electronic products to implement complex functions and operations, but also facilitates system expansion and upgrades to meet changing market demands.
Additionally, semiconductor substrates play a crucial role in facilitating the transmission of electrical energy and signals within electronic devices. By means of conductive layers and through holes embedded in the substrate, electrical energy is conveyed from power sources to various electronic components, while signals are exchanged between different elements to enable diverse functionalities. This conductive capability ensures the normal operation and external interaction of electronic devices, including signal reception and data transmission. In essence, semiconductor substrates not only provide support and interconnection for electronic components but also serve as vital conduits for electrical energy and signal transmission. Their stability, reliability, and functionality significantly impact the performance and quality of electronic products, rendering them indispensable in the modern electronics industry.
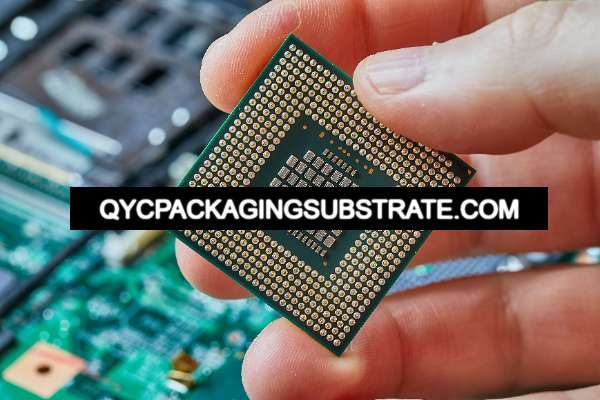
Global Semiconductor Substrate Manufacturer
What types of semiconductor substrates are there?
Compared with traditional printed circuit boards (PCBs), HDI boards have tiny lines and holes arranged on both the inner and outer layers. This design allows the HDI board to accommodate more components in the same size, providing higher integration and performance for electronic products.
HDI boards and Rigid-Flex panels offer distinct advantages tailored to specific requirements in electronic device design. HDI boards, including Microvia HDI and Build-up HDI, are characterized by their high-density interconnection, varying layers, apertures, and thicknesses. They excel in applications demanding superior signal integrity and performance, such as smartphones, computers, and communication equipment.
On the other hand, Rigid-Flex panels present a unique composition, blending rigid and flexible materials. The rigid core connects with flexible sections, allowing for adaptability to diverse shapes and sizes. This design is ideal for products requiring space efficiency and curved configurations, like wearable devices and camera modules. Moreover, Rigid-Flex boards shine in environments with mechanical bending demands, such as automotive electronics and medical equipment.
Recognizing the distinctive attributes and use cases of HDI and Rigid-Flex substrates empowers manufacturers and designers to make informed choices, driving innovation in the electronics industry forward. By leveraging the strengths of each substrate type, product development can push boundaries, delivering cutting-edge solutions to consumers.
Why choose semiconductor substrate?
Semiconductor substrates are preferred over other types due to several key factors. Firstly, they offer superior performance characteristics compared to traditional substrates, boasting higher density and improved signal integrity. This enables them to accommodate more electronic components and ensure more reliable signal transmission, crucial in today’s high-performance electronic devices and complex systems.
Furthermore, semiconductor substrates demonstrate exceptional heat dissipation capabilities. In a time characterized by the growing potency of electronic devices such as mobile gadgets and electric vehicles, proficient heat dissipation plays a crucial role. Semiconductor substrates adeptly conduct and disperse heat, ensuring the sustained stability of operating temperatures for chips and essential components. This, in turn, extends the lifespan of devices and boosts overall performance.
Moreover, semiconductor substrates offer high integration and flexibility. Advanced manufacturing technologies enable intricate designs and elevated levels of integration, meeting evolving market demands and customer needs. Their flexibility allows for diverse applications across various products and scenarios, providing customers with ample choices and possibilities.
In conclusion, semiconductor substrates are increasingly favored by industries and businesses due to their outstanding performance, efficient heat dissipation, high level of integration, and flexibility. Furthermore, their cost-effectiveness and short production cycles make them highly desirable, especially for companies prioritizing rapid time-to-market and budget considerations. As manufacturing technologies advance and costs decline, semiconductor substrate production becomes even more attractive. Consequently, these substrates are expected to play an even more significant role in the future, fueling ongoing innovation and progress within the electronics sector.
How are semiconductor substrates made?
Factors such as board dimensions, layer count, routing density, and component positioning are meticulously considered to optimize functionality and durability.
Material Preparation: Before fabrication, all necessary materials must undergo preparation. This typically involves substrate materials such as FR-4, metal foils, chemicals, and dielectrics. Each material undergoes thorough quality assurance testing to ensure compliance with exact specifications.
Mainboard and Base Material Fabrication: This pivotal phase encompasses the creation of the mainboard, the principal printed circuit board (PCB) that serves as the central hub for interconnecting electronic components, alongside the fabrication of the base material layer responsible for insulating and safeguarding the circuits.
Printed Circuit Board (PCB) Manufacturing:The production of PCBs involves a lamination procedure wherein slim layers of base material, metal foil, and insulating layers are assembled in accordance with design specifications and fused together through high-temperature and high-pressure bonding.
Etching and Processing: Subsequent to PCB formation, the subsequent step encompasses etching, where undesired portions of the foil are eliminated via chemical etching or mechanical means to delineate the circuit pattern. Additional processing steps such as drilling, cutting, and polishing refine the board to its ultimate dimensions.
Component Installation:In the final stage, electronic components are mounted onto the semiconductor substrate. This entails soldering the components onto designated locations on the PCB, ensuring proper connections. Automation is often employed to enhance efficiency and accuracy in this step.
In essence, the fabrication procedure of semiconductor substrates is complex and requires exactitude at each step, starting from blueprinting and material readiness to circuit board production, tempering, and assembly of parts. Proficiency and careful execution are indispensable for maintaining the caliber and efficiency benchmarks of the final output.
What are the application scenarios of semiconductor substrates?
Semiconductor substrates play a crucial role in numerous contemporary electronic devices, spanning from smartphones to automotive electronic systems, providing essential support for their operational efficiency and features.
These devices demand significant data processing capabilities and the ability to run complex software programs. Semiconductor substrates deliver robust computing and processing power while maintaining energy efficiency, ensuring efficient operation and prolonged battery life for these devices.
Furthermore, semiconductor substrates play a critical role in automotive electronic systems, which constitute another essential application area. In contemporary vehicles, an array of electronic devices and sensors are integrated to enable functionalities like autonomous driving, intelligent driving assistance, and Internet connectivity. Semiconductor substrates serve as a crucial facilitator for connecting and controlling diverse electronic components within automotive systems, thereby enhancing safety, comfort, and intelligent features in vehicles.
In summary, semiconductor substrates have pivotal functions across a spectrum of electronic products, encompassing smartphones, tablets, computers, and automotive electronic systems. They ensure stable circuit connections and deliver outstanding performance, propelling the progress and widespread adoption of modern technology. As advancements in science and technology persist and new application fields emerge, the significance of semiconductor substrates is poised to grow, bringing about greater convenience and innovation in our daily lives and work.
How to obtain semiconductor substrates?
When searching for semiconductor substrates, it’s essential to grasp the avenues for acquiring these vital components. Worldwide producers of semiconductor substrates provide their goods and services through various channels to accommodate different needs and preferences. Below are some typical approaches to acquiring semiconductor substrates, along with information about our supplier allies.
Engaging directly with semiconductor substrate manufacturers stands as a prevalent approach for procurement. By reaching out directly, customers gain access to comprehensive details about product specifications, customization possibilities, pricing structures, and more, facilitating direct communication with manufacturers to ensure tailored solutions. This method is particularly suitable for customers necessitating extensive customization or specialized specifications, as direct interaction with manufacturers can offer heightened flexibility in solutions.
An alternative avenue for obtaining semiconductor substrates is through intermediaries or brokers. Agents typically collaborate with multiple manufacturers, offering a diverse range of products and simplifying the purchasing process for clients. Utilizing agents can save time and energy, particularly for clients needing small quantities or standardized products, offering a convenient and effective solution.
As a supplier associated with our firm, we are committed to providing clients with top-quality semiconductor substrate products and outstanding services. We distribute our products to clients through both direct interaction and intermediary channels, delivering customized solutions based on specific needs. Our product portfolio includes a broad range of semiconductor substrates suitable for various application scenarios, supported by our extensive experience and expertise in addressing diverse customer requirements.
How much does a semiconductor substrate cost?
Primarily, material expenses stand out as a pivotal determinant of semiconductor substrate costs. Varied semiconductor substrates necessitate distinct materials in terms of type and quality, with material pricing directly dictating the ultimate product cost. For instance, premium-grade semiconductor substrates often demand pricier specialized materials, consequently elevating overall pricing to a certain degree.
Instances include semiconductor substrates necessitating multi-layer stacking, high-density interconnections, or specialized processing, all of which incur higher manufacturing costs, thus driving up prices.
Furthermore, order magnitude is another influential factor impacting semiconductor substrate pricing. Typically, bulk orders benefit from lower production costs as manufacturers can disperse fixed expenses across large-scale production runs, thereby diminishing per-unit costs. Consequently, sizable orders often secure more competitive pricing advantages, whereas smaller orders might entail higher price points.
In conclusion, semiconductor substrate pricing is subject to a plethora of factors, encompassing material costs, manufacturing intricacy, and order size. Grasping these determinants is imperative for clients as it empowers them to comprehend the rationale behind product pricing, facilitating more informed procurement decisions. Thus, when contemplating semiconductor substrate acquisitions, clients should holistically assess these factors and engage in thorough communication with manufacturers to secure the most competitive pricing and premium-quality products and services.
Frequently Asked Questions (FAQs)
How can I address issues related to substrate compatibility with other components in my electronic system?
Ensure thorough testing and compatibility assessments during the design phase. Collaborate closely with substrate manufacturers and other component suppliers to address any compatibility concerns and optimize system performance.
How can I address issues related to substrate compatibility and integration with other electronic components?
Collaborate closely with both substrate manufacturers and component suppliers to ensure compatibility testing, design validation, and effective integration strategies.
How can I address issues with substrate compatibility or integration?
Work closely with both substrate manufacturers and your design team to identify potential compatibility issues early in the design phase. Conduct thorough testing and validation to ensure seamless integration.
How do I choose the right semiconductor substrate?
Consider your specific project requirements, including performance needs, form factor constraints, and budget considerations. Additionally, consult with experts or suppliers to ensure compatibility with your design.