High Frequency package Substrate Manufacturer. Some package Substrate will be made with High Frequency materials. Such as: Rogers materials package Substrate. or rogers cavity package substrate. Most of the Package Substrate will be made with BT base, Some were made with Showa Denko and Ajinomoto High speed materials. we can do this types substrates with high quality and fast lead time.
This passage highlights the importance of high-frequency packaging substrates within the electronics sector. These substrates play a vital role in supporting and interconnecting integrated circuits (ICs), especially in applications demanding high frequencies and performance levels. They are engineered with sophisticated materials and manufacturing methods to effectively manage high-frequency signals, thereby ensuring superior electrical performance and signal transmission across a variety of electronic devices.
High-frequency packaging substrates are defined as specialized circuit boards tailored to support and connect ICs while facilitating stable signal transmission and electrical performance. They typically operate within the microwave frequency range, adept at processing high-frequency signals and facilitating fast data transmission. Consequently, they find extensive use in communication equipment, radar systems, satellites, and other high-frequency applications.
In electronics, these substrates play a pivotal role in IC connectivity and support. They not only provide a physical platform for IC installation and connection but also ensure stable signal transmission at high frequencies, thereby guaranteeing device performance and reliability. Their design and manufacturing processes prioritize considerations such as electrical characteristics, thermal management, and signal integrity to meet customer requirements and application scenarios effectively.
Overall, high-frequency packaging substrates are instrumental in connecting and transmitting signals within the electronic realm, with their stable performance and reliability serving as crucial support for various high-frequency applications.
What are the types of high frequency packaging substrates?
This passage discusses the diversity of substrates within the realm of high-frequency packaging. It emphasizes the importance of understanding the distinct characteristics of each substrate type to make informed decisions tailored to specific requirements.
In essence, it suggests a detailed examination of substrate options to ensure optimal selection based on their individual attributes and suitability for particular applications in high-frequency packaging.
Single-layer Substrate
Single-layer substrates are the most basic type, comprising only one layer of substrate material. They find common use in uncomplicated circuit designs and applications where low frequencies are involved, such as in basic communication devices or consumer electronics. These substrates are favored for their straightforward construction and affordability, making them a popular choice for cost-conscious projects.
Double-layer Substrate
Double-layer substrates are made by stacking two layers of substrates, providing more space for electrical connections and wiring. This makes the double-layer substrate suitable for some scenarios that require more complex circuit design and higher frequency applications. For example, some industrial control systems or small communications equipment may use dual-layer substrates to meet their performance and layout needs.
Multilayer Substrate
Multilayer substrates are made of multiple layers of sheets, with electrical connections between each layer through interlayer connections. This structure enables multi-layer substrates to enable more complex circuit designs and higher density wiring while maintaining a small size. Multilayer substrates are usually used in applications with high performance, high frequency and high circuit layout requirements, such as communication base stations, satellite communication systems, etc.
This passage describes three different types of high-frequency packaging substrates commonly utilized across various applications:
High-Speed Digital Signal Substrate: Tailored for efficient transmission of high-speed digital signals, this substrate is engineered with optimized layouts for transmission lines and ground wires to mitigate signal distortion and crosstalk. It is predominantly employed in digital signal processing, computer network equipment, and other contexts demanding rapid data transmission.
Radio Frequency (RF) Substrate: Specifically designed for RF circuitry, RF substrates possess tailored characteristics conducive to high-frequency signal propagation. They are integral components in systems such as radar, satellite communications, wireless communication networks, and other domains reliant on RF signal processing.
Mixed-Signal Substrate: Offering versatility to accommodate both analog and digital signal processing requirements, these substrates are commonly employed in applications like sensor interfaces and audio processing, where the handling of both signal types is necessary.
In essence, the selection of the appropriate substrate type depends on project-specific requirements including frequency range, layout complexity, and cost considerations. Understanding the unique characteristics of each substrate type enables better decision-making for achieving optimal performance and reliability in diverse application scenarios.
What are the advantages of high-frequency packaging substrates?
This passage underscores the supremacy of high-frequency packaging substrates within the electronics sector, highlighting their outstanding attributes in signal propagation, consistency, thermal management, and adaptability in design.
Signal Propagation and Electrical Performance: High-frequency packaging substrates are intricately crafted to minimize signal degradation and distortion, ensuring a uniform propagation of high-frequency signals. This sets them apart from traditional substrates that may introduce signal loss and interference.
Signal Consistency: Consistency holds paramount importance in high-frequency applications, and these substrates excel in preserving signal integrity during transmission. They alleviate fluctuations and distortion through optimized configurations and material choices, rendering them ideal for crucial applications like communication devices and radar systems.
Thermal Regulation: Efficient thermal regulation is indispensable in high-frequency applications. These substrates employ materials with high thermal conductivity and incorporate effective thermal management strategies, guaranteeing stable operation even under demanding conditions. Consequently, this bolsters system reliability and long-term performance.
Flexible Design and Manufacturing: High-frequency packaging substrates offer versatile design and manufacturing capabilities, accommodating intricate system designs such as single, dual, or multi-layer substrates. This adaptability ensures optimal performance tailored to specific applications, making them suitable for a wide array of projects and industries.
In summary, high-frequency packaging substrates are preferred in many high-frequency applications due to their outstanding electrical performance, signal stability, heat dissipation capabilities, and flexible design options. They outperform other alternatives by meeting the demands of complex system designs while delivering stable and reliable performance, thus facilitating the advancement and innovation of electronic products.
Why choose high frequency packaging substrate?
When faced with the choice of various electronic components, why should high-frequency packaging substrates be given priority? High-frequency packaging substrates stand out among many options with their unique advantages, and their advantages are fully reflected in practical applications.
This passage outlines the benefits of high-frequency packaging substrates in electronic applications:
Excellent Electrical Properties: High-frequency packaging substrates ensure stable and reliable signal transmission through optimized design and material selection, reducing signal distortion and improving system performance.
EMI Suppression Capabilitie: Special design and materials effectively suppress electromagnetic interference, ensuring equipment operates stably without signal transmission issues.
Good Heat Dissipation Performance: High-frequency substrates dissipate heat efficiently through well-designed structures and materials, keeping equipment temperatures within safe limits and extending service life.
This paragraph describes the benefits of high-frequency packaging substrates, highlighting their smaller size and weight achieved through advanced processes and materials. These substrates offer superior electrical performance, EMI suppression, and heat dissipation while being compact and lightweight, making them ideal for a range of high-frequency applications. Their attributes ensure the reliability and performance of electronic devices, enhancing equipment portability and applicability.
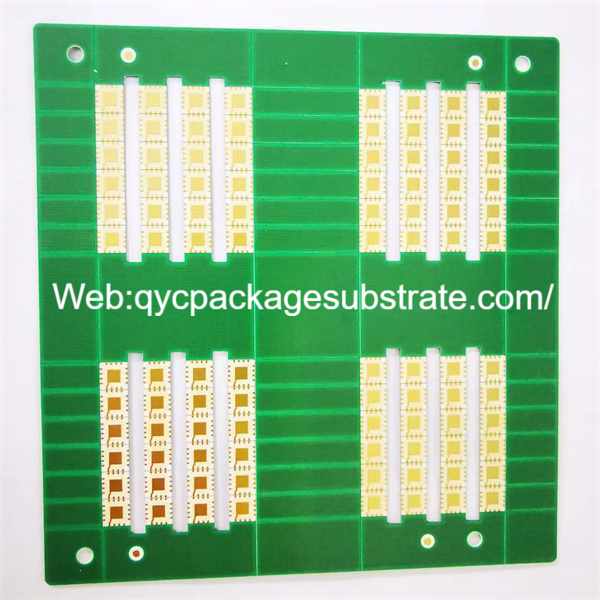
High Frequency package Substrate
How to manufacture high-frequency packaging substrates?
The manufacturing process of high-frequency packaging substrates is a detailed and complex procedure essential for meeting demanding performance and reliability criteria. It commences with the meticulous selection and quality evaluation of raw materials including fiberglass cloth, epoxy resin, and copper foil.
Initially, fiberglass cloth is saturated with epoxy resin to form prepreg. At the same time, a thin coat of photosensitive paint is applied to the copper foil to create a substrate where the copper foil encases the photosensitive film.
In this step, light exposure through a pattern mask forms the required pattern on the photosensitive film. Following photolithography, etching is employed to eliminate the unexposed photosensitive film and copper clad layer, revealing the copper foil and defining the circuit pattern.
Chemical treatments like pickling and copper plating are then employed to cleanse and enhance the adhesion of the copper foil surface, ensuring optimal electrical conductivity and connectivity.
The chemically treated substrate undergoes shaping and hot pressing in a press under high temperature and pressure conditions. This process melts the epoxy resin in the prepreg, binding the substrate layers into a robust structure.
Post hot pressing, any undesired material is removed through milling and drilling to attain the final design specifications.
Ultimately, the manufactured high-frequency packaging substrate undergoes exhaustive final inspection and testing encompassing appearance evaluation, dimensional measurement, and electrical performance assessment to guarantee adherence to specifications and customer requirements.
Through these intricate stages, high-frequency packaging substrates are meticulously crafted from raw materials to finished products, providing a reliable foundation for the high performance of electronic devices.
What are the application fields of high-frequency packaging substrates?
This paragraph discusses the diverse applications of high-frequency packaging substrates across various fields, emphasizing their pivotal role in advancing technology. In the communications sector, these substrates enhance data transmission speed and stability, benefiting mobile communication base stations and satellite communication systems. They facilitate faster and more reliable signal transmission, contributing to improved communication quality and supporting the progression toward a digital society.
Furthermore, in radar technology, high-frequency packaging substrates drive significant performance enhancements. They enable radar systems to process intricate signals more effectively, leading to improvements in detection accuracy and response speed. This is particularly beneficial in domains such as military defense, air traffic control, and weather monitoring, where reliable and efficient radar systems are paramount.
In satellite systems, high-frequency packaging substrates ensure that satellites can efficiently transmit and receive data through superior signal transmission performance. This not only promotes the popularity of satellite communications, but also provides a reliable basis for data exchange on a global scale.
In the medical field, high-frequency packaging substrates provide support for innovation in medical electronic equipment. From high-frequency medical image transmission to remote medical monitoring, these substrates make medical equipment more precise and efficient through their superior electrical performance.
This passage discusses the extensive usage of high-frequency packaging substrates across diverse industries such as communications, radar, satellite communications, and medical electronic equipment. These substrates not only improve the performance of current technologies but also accelerate the innovation of new technological advancements.Their exceptional electrical performance and versatility position them as vital catalysts for innovation within the electronics industry today. As manufacturers of high-frequency packaging substrates, our dedication lies in furnishing cutting-edge solutions to diverse industries, enabling our customers to thrive in today’s fiercely competitive market landscape.
How to find high frequency packaging substrate manufacturers?
This passage emphasizes the importance of selecting a dependable supplier when seeking a high-frequency packaging substrate manufacturer. It provides guidance on finding the right manufacturer to meet a company’s specific requirements.
Choose companies that have extensive experience in high-frequency packaging substrate manufacturing, especially those with good reputations and success stories.
Make sure the supplier has advanced technical capabilities to meet the requirements of your project. Understand their technical level in material selection, process control and quality management.
This paragraph outlines the considerations involved in selecting a reliable manufacturer for high-frequency packaging substrates. It emphasizes several key factors:
Quality Standards and Certifications: Ensuring that suppliers comply with industry quality management system standards like ISO 9001.
Customization Capabilities:Choosing a manufacturer capable of providing tailored solutions to suit specific project requirements.
Delivery Times and Production Capabilities: Verifying that the supplier can meet deadlines and handle projects of varying sizes.
Cost:Balancing product quality with affordability and understanding pricing structures.
Technical Support and After-sales Service:Expecting prompt technical assistance and effective support post-purchase.
Customer Feedback and Case Studies:Reviewing experiences of other clients to gauge operational and service quality.
In summary, the passage underscores the importance of thorough evaluation to select a manufacturer that aligns with the needs and standards of the project, ultimately ensuring its success.
How to get a quote for high frequency packaging substrate?
The provided passage outlines a systematic approach for obtaining a comprehensive quote for high-frequency packaging substrates. The key steps include first determining project needs by specifying quantity, technical requirements, and delivery time. Next, it suggests researching and reaching out to multiple suppliers, comparing quotes and services. Emphasizing the importance of providing detailed design documents, such as technical specifications and CAD drawings, ensures suppliers understand project requirements accurately.
Upon receiving quotes, the passage advises thoroughly reviewing them to identify included costs like shipping, taxes, and sample fees. Additionally, it recommends inquiring about delivery times and payment options to align with project timelines and financial considerations. The passage concludes by emphasizing the importance of requesting samples for quality verification before making a final decision, ensuring the chosen supplier can deliver high-quality products meeting project standards. Overall, the outlined steps aim to guide individuals or businesses in making informed decisions when selecting a supplier for high-frequency packaging substrates.
Frequently Asked Questions
What distinguishes high-frequency package substrates from conventional ones?
High-frequency package substrates are specifically designed to meet the demands of applications requiring superior signal transmission and electrical performance at higher frequencies. Unlike conventional substrates, they excel in minimizing signal distortion and electromagnetic interference.
How are high-frequency package substrates manufactured?
Manufacturing high-frequency package substrates involves advanced fabrication processes. It typically includes techniques such as layering, etching, and metallization to create precise circuit patterns and ensure optimal electrical performance.
How are high-frequency package substrates manufactured?
Manufacturing high-frequency package substrates involves advanced processes and techniques. Key steps include motherboard and substrate manufacturing, which ensure high-quality products meeting stringent performance and reliability standards.
How can I obtain a quote for high-frequency package substrates?
Before making a decision, it’s essential to request detailed quotes from potential manufacturers. These quotes should include manufacturing costs, delivery times, and any additional service fees to help evaluate the overall investment.