High speed package substrate supplier. Types of materials for high-speed packaging substrate. we have used the Showa Denko and Ajimomoto and BT base materials. or maybe Rogers high frequency materials.
Within the realm of contemporary electronics, laminates emerge as an indispensable technology. Serving as a fundamental component in the domain of packaging substrates, laminates assume a pivotal role in the fabrication of electronic devices. This article will provide a comprehensive exploration of the fundamental concepts surrounding laminates and shed light on their indispensable role in the production of packaging substrates.
Laminate and its role in the field of packaging substrates
Laminates are composite materials typically composed of multiple layers of various materials fused together. These layers can consist of different substrate materials like fiberglass, polyimide, and more. The primary function of laminates is to offer structural support and establish electrical connections, enabling the smooth operation of the diverse components within electronic devices.
In the domain of packaging substrates, laminates serve as vital connectors, acting as bridges that link semiconductor chips, circuit components, and other electronic elements together. Beyond providing mechanical support, laminates facilitate the transmission of signals and power within the circuit. As a result, the quality and performance of laminates are of paramount importance in ensuring the stable and reliable operation of electronic devices.
In the forthcoming discussion, we will delve into the specific applications of substrates in laminate manufacturing and packaging substrates. We will explore the different substrate materials, their roles in the manufacturing process, and their indispensable function in packaging substrates. Furthermore, we will delve into future trends concerning substrates, emphasizing how innovation and sustainable practices can propel advancements in the field of electronics.
Before we delve into laminate’s substrate uses, let’s first understand its central role in electronics manufacturing.
The role of substrates in laminate manufacturing
The substrate plays a central role in the laminate manufacturing process and its role cannot be ignored. This section will delve into the critical role of substrates in manufacturing laminates and how they impact laminate performance.
The central role of the substrate in the laminate process
The substrate can be thought of as the skeleton and support structure of the laminate. During the laminate manufacturing process, the substrate plays a key role in positioning and supporting the material. In addition, the substrate’s high stability and precision during production also make it ideal for manufacturing high-quality laminates.
Emphasis on its impact on laminate performance
The selection of the right substrate material holds a profound influence on the ultimate performance of the laminate. Various types of substrate materials can yield substantial disparities in electrical performance, thermal characteristics, mechanical robustness, and durability. For instance, opting for a substrate with excellent thermal conductivity can significantly enhance the laminate’s heat dissipation capabilities, making it suitable for high-temperature environments. Conversely, specific substrate materials may excel in high-frequency applications due to their superior dielectric properties. Hence, when choosing a substrate material, it is imperative to consider the intended application and the desired properties to ensure that the final laminate meets the requisite standards.
Furthermore, surface treatments and specialized coatings applied to the substrate can exert additional influence on laminate performance. For instance, anti-corrosion coatings can bolster the durability of laminates in challenging environmental conditions, while chemical treatments can enhance substrate surface adhesion and printability, critical aspects in circuit board manufacturing.
In sum, the substrate’s role in laminate manufacturing is pivotal, as it directly shapes the performance and reliability of the end product. The selection and processing of substrates are pivotal to the successful production of laminates and must be meticulously planned based on specific application requirements. This underscores the significance of ongoing innovation and sustainable practices within the electronics sector, ensuring that laminate technology continues to progress and adapt to evolving needs.
Variety of substrate materials
Modern laminate manufacturing hinges on the utilization of various substrate materials, such as fiberglass, polyimide, and a spectrum of other materials, each distinguished by its unique attributes and versatile applicability.
Fiberglass substrate
Fiberglass substrates are favored for their excellent mechanical strength and good thermal resistance. It is a strong and durable material suitable for a variety of laminate manufacturing needs. Its excellent insulation properties make fiberglass substrates widely used in the electrical field, especially in the manufacture of high-frequency circuits and electronic equipment.
Polyimide substrate
Polyimide substrate is a high-performance polymer material with excellent heat resistance, chemical stability and electrical insulation properties. This material is widely used in high-frequency circuits, high-speed communications, aerospace and other fields. Because of its low dielectric constant and dielectric loss, it can effectively reduce energy loss during signal transmission. Its excellent high temperature resistance makes it an ideal packaging substrate material, especially in environments requiring high temperature operation.
The diversity of these substrate materials provides the laminate manufacturing industry with a wide range of options to meet various needs in different application scenarios. Across different engineering and product designs, choosing the right substrate material is a key factor in ensuring performance and reliability. An in-depth understanding of the characteristics and uses of substrate materials can help engineers better select and apply appropriate materials to ensure high-quality product performance and reliability.
Substrate usage during manufacturing
The laminate manufacturing process is a highly complex project, in which the role of the substrate is crucial. The substrate plays a key role in several critical steps including layer assembly, heat pressing and curing, each of which has a profound impact on the performance and quality of the laminate.
Application of substrate in layer assembly
In the early stages of laminate manufacturing, layers of different materials (usually composed of resin and fiberglass) need to be combined in a precise sequence. Not only that, the quality and mechanical properties of the substrate material also affect the efficiency and success rate of layer assembly. Any substrate deviation or material defects can cause manufacturing issues, so choosing a high-quality substrate is critical.
The Importance of Substrates in Hot Pressing and Curing
Heat pressing and curing represent pivotal stages in the manufacture of laminates. After assembling the panels, the entire structure undergoes exposure to elevated temperatures and pressures, a process essential for achieving a strong and tightly bonded composite structure. In this intricate procedure, the substrate plays a crucial role, offering support and stability to ensure that the laminate retains its shape and structural integrity when subjected to the rigors of high temperatures and pressures. This is of utmost importance since the ultimate performance and reliability of the end product hinge directly on the consistency and robust bonding between the layers.
The thermal conductivity properties of the substrate also hold significance as they facilitate the uniform distribution of temperature, guaranteeing even heating throughout the structure during the hot pressing and curing phases.
It’s not just the inherent material characteristics of the substrate that need to be considered; factors like flatness, dimensional stability, and thermal conductivity are equally crucial. Success in these aspects is the linchpin for the production of top-tier laminates that fulfill the requirements of diverse applications.
In the concluding section, we’ll encapsulate the pivotal role of the substrate in the laminate manufacturing process, underscoring its far-reaching influence on the overall production process. Simultaneously, we advocate for the perpetual exploration of innovative substrate materials and technologies to foster the sustained advancement of the electronics field.
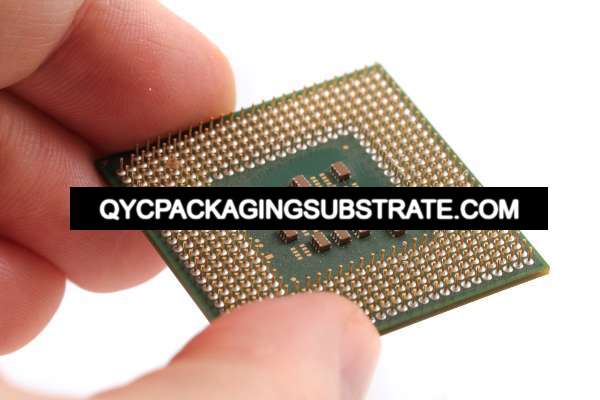
high-speed packaging substrate
The role of substrate in packaging substrate
Substrates play a vital role in packaging substrates, and their versatility and critical position play a decisive role in the performance and reliability of electronic devices.
Introduce the role and function of the substrate in the packaging substrate
The substrate acts as a support structure for the package substrate, carrying electronic components and wires while providing insulation and isolation. It has the following key features:
Circuit Support: Circuit layers on a substrate provide a support structure for electronic components, allowing them to connect to each other and work together.
Signal transmission: Wires on the substrate are used to transmit electronic signals, allowing data and power to be exchanged between individual components. This transmission is critical for communication within and between devices.
Thermal Management: The substrate can effectively disperse and transfer heat, helping to keep the temperature of electronic components within a safe range. This is essential to avoid overheating and increase the life of electronic devices.
Mechanical Support: The substrate not only supports the electronic components but also withstands the physical stress and vibration of the device. This helps protect electronic components from damage.
Isolation and protection: The insulating properties of the substrate can isolate circuit layers and reduce interference and mutual interference between electronic devices. In addition, it provides a level of protection against damage to electronic components caused by environmental factors such as moisture, dust or chemicals.
Explain its critical role in electronic devices
The role of the substrate is not limited to the packaging process, it also plays a key role in electronic devices. Electronic equipment manufacturing and modern technology are inseparable from the key role of substrates:
Performance Optimization: The design and quality of the substrate directly affects device performance. By selecting appropriate substrate materials, wiring structures, and manufacturing processes, performance can be maximized, such as higher processing speeds, lower energy consumption, and higher reliability.
Device miniaturization: The compact design and high integration of the substrate help reduce the size of the device, making the device smaller and lighter, thus meeting the needs of modern consumers and the market for miniaturized devices.
Sustainability: Continuous innovation and sustainable practices in substrate manufacturing technology play a key role in reducing resource waste, improving energy efficiency, and lowering carbon footprints, helping to drive the electronics industry in a more sustainable direction.
In short, the role and function of substrates in packaging substrate manufacturing and electronic devices are crucial. It not only supports the functions of electronic components, but also has a profound impact on the performance, reliability, and sustainability of electronic devices. As technology continues to develop, substrates will continue to play a key role in promoting progress in the electronics field.
Future trends in substrates
In modern electronics, substrate technology has been at the forefront of constant evolution. As technology advances, future trends in substrates will impact the performance, sustainability and environmental friendliness of electronic devices. The following is a discussion of future trends in substrate technology:
Discuss the development trends of substrate technology
High-density interconnection and miniaturization: Future substrates will continue to evolve toward high-density interconnection and miniaturization. This includes more layers, smaller vias and higher signal transmission speeds to accommodate more compact electronic device designs.
Flexible substrates: Flexible substrate technology will continue to develop to meet the needs of bendable and foldable electronic devices. This substrate can adapt to new device shapes, paving the way for innovative electronic products.
Higher frequency and lower loss: The design of substrates will pay more attention to high-frequency applications, such as 5G communications and radio frequency technology. At the same time, reducing losses in signal transmission will also become an important development direction.
Material innovation: The application of new materials will promote the advancement of substrate technology. For example, low-k materials will reduce signal cross-talk and improve performance.
Green manufacturing: Substrate manufacturers will continue to seek more environmentally friendly production methods. Waste reduction, energy efficiency improvements, and low-pollution processes are the future trends. The use of renewable energy and reduction of carbon footprint will become standard in the industry.
Sustainable Materials: The use of renewable, degradable and environmentally friendly materials will continue to evolve. Biodegradable substrates and sustainable sourcing practices will drive the electronics industry in a more sustainable direction.
Recycling and reuse: The electronic waste problem is becoming increasingly serious, so recycling and reusing substrates will become a future trend. Substrate design will pay more attention to easy decomposition and recycling to reduce resource waste.
Environmental regulations compliance: Due to the strengthening of environmental regulations, substrate manufacturers will pay more attention to compliance to ensure that products meet environmental standards. This will help protect the ecosystem and reduce environmental pollution.
In summary, future trends in substrate technology will focus on high performance, sustainability and environmental protection. These trends will push the electronics industry in a more innovative and eco-friendly direction, laying a solid foundation for us to create smarter and more sustainable electronic devices.