IPC Class 3 PCB Manufacturer.An IPC Class 3 PCB manufacturer specializes in producing high-quality printed circuit boards designed to meet the rigorous standards set for critical applications. These manufacturers ensure that their PCBs are reliable and durable, adhering to IPC Class 3 specifications which demand the highest level of performance and quality. Suitable for use in aerospace, medical devices, and other demanding sectors, their products are engineered to withstand harsh environments and maintain integrity over time. The focus on precision, quality control, and advanced manufacturing techniques is essential to meet the stringent requirements of IPC Class 3 standards.
IPC Class 3 Printed Circuit Boards (PCBs) represent the pinnacle of quality and reliability in the PCB industry. These PCBs are designed for demanding applications where continuous operation, high performance, and exceptional reliability are critical. Industries such as aerospace, military, medical devices, and high-reliability industrial equipment rely on IPC Class 3 PCBs for their stringent requirements. This article explores the properties, standards, manufacturing process, applications, and benefits of IPC Class 3 PCBs.
What is an IPC Class 3 PCB?
IPC Class 3 PCBs are high-reliability printed circuit boards that meet the rigorous standards set by the IPC (Association Connecting Electronics Industries) for high-performance electronics. These standards ensure that the PCBs can withstand harsh operating conditions, provide long-term reliability, and maintain high levels of performance. Class 3 PCBs are characterized by their superior design, manufacturing, and inspection criteria, making them suitable for critical applications where failure is not an option.
The IPC Class 3 standard encompasses several aspects of PCB manufacturing, including material selection, design rules, fabrication processes, and quality control measures. The standard ensures that the PCBs have minimal defects, high precision, and robust performance, even in extreme environments.
Properties and Standards of IPC Class 3 PCBs
IPC Class 3 PCBs are defined by specific properties and standards that distinguish them from lower-class PCBs. These properties include:
IPC Class 3 PCBs are designed for applications where uninterrupted service and high reliability are crucial. They must meet stringent performance criteria to ensure long-term functionality without failure.
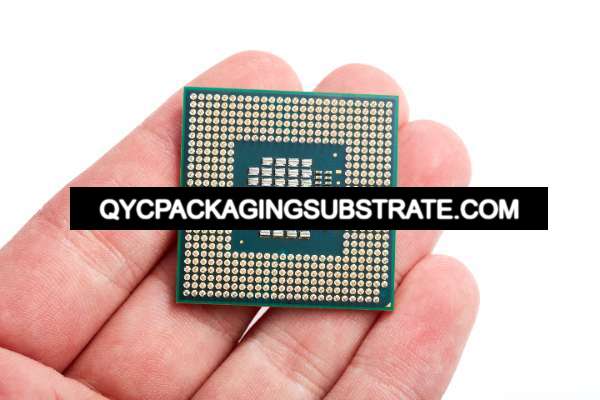
IPC Class 3 PCB Manufacturer
The manufacturing processes for IPC Class 3 PCBs require high precision and accuracy. This includes tight tolerances for component placement, trace widths, and spacing to ensure optimal performance and signal integrity.
IPC Class 3 standards mandate minimal defects in the final product. This includes strict control over factors such as voids, delamination, and contamination, ensuring the highest quality PCBs.
These PCBs are built to withstand harsh operating conditions, including extreme temperatures, vibration, and mechanical stress. The materials and processes used in their construction are chosen to enhance durability and longevity.
IPC Class 3 PCBs undergo rigorous inspection and testing procedures. This includes advanced testing methods like X-ray inspection, automated optical inspection (AOI), and electrical testing to verify the integrity and performance of the PCBs.
Structure of IPC Class 3 PCBs
The structure of IPC Class 3 PCBs is designed to meet the high standards required for critical applications. Key structural elements include:
High-quality substrate materials such as FR-4, polyimide, or ceramic are used to ensure thermal stability, mechanical strength, and electrical insulation. The choice of substrate depends on the specific application requirements.
The conductive layers are typically made of copper, which is chosen for its excellent electrical conductivity. The copper layers are etched to form the circuit traces and pads, with precise control over the trace widths and spacing.
PTHs are used to create electrical connections between different layers of the PCB. The plating process must ensure reliable and durable connections, with stringent control over hole wall integrity and plating thickness.
A solder mask is applied to protect the circuitry from environmental factors and prevent solder bridging during assembly. The solder mask must be applied uniformly and accurately to avoid any defects.
Surface finishes such as Electroless Nickel Immersion Gold (ENIG), Hot Air Solder Leveling (HASL), or Organic Solderability Preservative (OSP) are applied to the contact pads. These finishes enhance solderability and protect against oxidation.
Materials Used in IPC Class 3 PCBs
The materials used in IPC Class 3 PCBs are selected for their superior properties, ensuring the highest level of performance and reliability. Key materials include:
A widely used substrate material, FR-4 is a glass-reinforced epoxy laminate known for its good electrical insulation, mechanical strength, and thermal stability. It is suitable for a wide range of applications.
Polyimide substrates offer excellent thermal stability and are used in high-temperature applications. They are more flexible than FR-4 and provide better performance in demanding environments.
Ceramic substrates provide superior thermal conductivity and electrical insulation. They are used in applications requiring high heat dissipation and reliability, such as aerospace and military electronics.
Copper foil is used for the conductive layers due to its excellent electrical conductivity. The thickness and quality of the copper foil are critical to the performance of the PCB.
High-quality solder masks and surface finishes are used to protect the circuitry and ensure reliable solder connections. The choice of surface finish depends on the specific application requirements and environmental conditions.
The Manufacturing Process of IPC Class 3 PCBs
The manufacturing process of IPC Class 3 PCBs involves several critical steps, each essential for achieving the high precision and reliability required for these PCBs. The process includes:
The design and layout process involves creating detailed circuit diagrams and PCB layouts using advanced CAD software. The design must meet the IPC Class 3 standards for trace widths, spacing, and component placement.
High-quality materials, including substrates, copper foils, and solder masks, are selected and prepared for manufacturing. This includes cutting the substrate to the required dimensions and preparing the copper layers for etching.
The copper layers are etched to form the circuit traces and pads. This process involves applying a photosensitive film, exposing it to UV light through a mask, and developing the exposed areas to reveal the circuit pattern. The substrate is then etched to remove the unwanted copper. Plated through-holes are created by drilling and plating the holes with copper to ensure reliable electrical connections.
A solder mask is applied to protect the circuitry and prevent solder bridges during assembly. The solder mask is typically applied using screen printing or photo-imaging techniques and then cured to harden it.
Surface finishes are applied to the contact pads to enhance solderability and protect against oxidation. Techniques like ENIG, HASL, or OSP are used to ensure reliable solder joints and long-term durability.
The final PCBs undergo rigorous inspection and testing to ensure they meet all performance and reliability standards. This includes visual inspection, automated optical inspection (AOI), X-ray inspection, and electrical testing to verify the integrity and performance of the PCBs.
Application Areas of IPC Class 3 PCBs
IPC Class 3 PCBs are used in a wide range of applications across various industries due to their high-reliability and performance characteristics. Key application areas include:
In aerospace, IPC Class 3 PCBs are used in avionics, communication systems, and navigation equipment. Their ability to withstand extreme temperatures, vibration, and mechanical stress makes them ideal for aerospace applications.
The military relies on IPC Class 3 PCBs for critical systems, including radar, communication, and weapons systems. These PCBs provide the reliability and durability required for mission-critical applications.
IPC Class 3 PCBs are used in medical devices, such as imaging equipment, diagnostic instruments, and patient monitoring systems. Their high reliability ensures accurate and continuous operation in medical environments.
High-reliability industrial equipment, such as automation systems, power supplies, and control systems, use IPC Class 3 PCBs. These PCBs provide the necessary performance and durability for demanding industrial applications.
Advantages of IPC Class 3 PCBs
IPC Class 3 PCBs offer several advantages that make them a preferred choice for high-reliability applications. These advantages include:
IPC Class 3 PCBs are designed to provide superior reliability in demanding environments. They meet stringent performance criteria and undergo rigorous testing to ensure long-term functionality without failure.
The manufacturing processes for IPC Class 3 PCBs require high precision and accuracy, ensuring optimal performance and signal integrity. Tight tolerances for component placement, trace widths, and spacing are maintained.
IPC Class 3 standards mandate minimal defects in the final product. Strict control over factors such as voids, delamination, and contamination ensures the highest quality PCBs.
IPC Class 3 PCBs are built to withstand harsh operating conditions, including extreme temperatures, vibration, and mechanical stress. The materials and processes used in their construction enhance durability and longevity.
FAQ
What distinguishes IPC Class 3 PCBs from other classes?
IPC Class 3 PCBs are distinguished by their high-reliability and stringent performance standards. They undergo rigorous inspection and testing, have minimal defects, and are designed to withstand harsh operating conditions, making them suitable for critical applications.
Can IPC Class 3 PCBs be used in high-temperature environments?
Yes, IPC Class 3 PCBs are suitable for high-temperature environments. The materials and construction techniques used ensure thermal stability and reliability, making them ideal for applications such as aerospace and military electronics.
How do IPC Class 3 PCBs ensure reliable performance in demanding environments?
IPC Class 3 PCBs ensure reliable performance through high-quality materials, precise manufacturing processes, and rigorous inspection and testing. These factors minimize defects, enhance durability, and provide superior performance in demanding environments.
What industries benefit the most from using IPC Class 3 PCBs?
Industries that benefit the most from using IPC Class 3 PCBs include aerospace, military, medical devices, and high-reliability industrial equipment. These industries require high-reliability and performance, which IPC Class 3 PCBs provide.