IPC Class III Boards Manufacturer.IPC Class III Boards Manufacturer specializes in producing high-reliability printed circuit boards (PCBs) that meet stringent IPC Class III standards. We excel in manufacturing boards for critical applications requiring exceptional quality, durability, and performance under harsh conditions.
Driven by modern technology, printed circuit boards (PCBs) have become an indispensable core component of various electronic devices. In particular, IPC Class III PCBs have attracted much attention for their application in high reliability and harsh environments. This article will delve into the definition, design points, material selection, manufacturing process, application fields and advantages of IPC Class III PCB to provide readers with a comprehensive understanding and reference.
What are IPC Class III Boards?
IPC Class III PCB is a specific class of printed circuit boards (PCBs) that meet the highest reliability standards set by IPC (Association Connecting Electronics Industries). These PCBs are different from the low to medium reliability circuit boards used in general applications, but are designed and manufactured for harsh environments that require extremely high reliability and long-term stability. IPC Class III PCBs are widely used in fields such as aerospace, medical equipment, and national defense, which require extremely high reliability and performance of electronic equipment.
In the aerospace field, IPC Class III PCBs are used in flight control systems, navigation systems, and satellite communication equipment. Aerospace equipment works in extreme high-altitude, high-speed and temperature-changing environments, and has extremely strict requirements on the stability and reliability of electronic components and PCBs. IPC Class III PCB can ensure long-term stable operation under these extreme conditions through its strict design specifications and manufacturing standards.
In the field of medical equipment, IPC Class III PCBs are widely used in pacemakers, medical imaging equipment and implantable medical electronic equipment. These devices also have very high requirements on the stability and reliability of circuit boards because they are directly related to the life and health of patients. Through its high-quality material selection, strict manufacturing processes and precise testing standards, IPC Class III PCB can ensure that medical equipment will not malfunction or degrade in performance during long-term use.
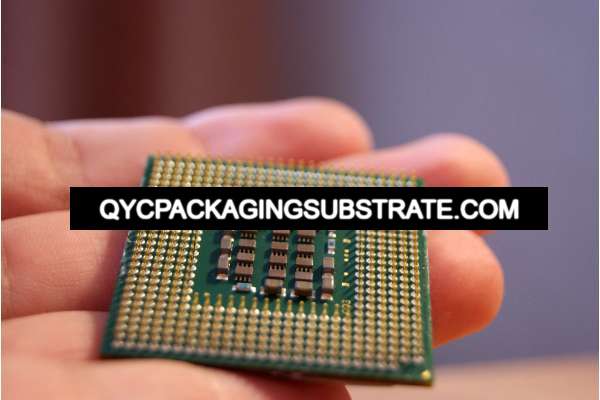
IPC Class III Boards Manufacturer
In the field of defense, IPC Class III PCBs are used in radar systems, missile control systems and military communications equipment. These devices often face extreme temperatures, humidity and mechanical shocks in battlefield environments, placing extremely high requirements on PCB reliability and durability. IPC Class III PCB, through its strong durability and high anti-interference ability, can ensure stable operation under harsh environmental conditions and ensure the safety and combat effectiveness of national defense systems.
In short, IPC Class III PCB is not only a component of electronic components, but also an indispensable key technical support in the modern high-tech field. Through strict standards and quality control, it provides reliable electronic solutions for key fields such as aerospace, medical health, and national defense security, promoting technological progress and development in these fields.
IPC Class III Boards design Reference Guide.
IPC Class III printed circuit board (PCB) design is critical and is particularly suitable for applications requiring extremely high reliability and long-term stability, such as aerospace, medical equipment, and defense. This guide is designed to help engineers and designers understand the design points and best practices for IPC Class III PCBs to ensure that the design meets strict industrial standards and reliability requirements.
The primary consideration in the design of IPC Class III PCB is to optimize the circuit layout and ensure signal integrity and electromagnetic compatibility (EMC). Reasonable circuit layout can reduce signal interference and crosstalk, and improve the stability and reliability of the circuit. Designers need to follow the layout rules of the IPC standard and rationally arrange electronic components and signal paths to minimize circuit delay and power loss.
IPC Class III PCB requires the use of high-end soldering and connection technologies, including surface mount technology (SMT) and through-hole technology. These technologies not only ensure welding quality and connection strength, but also improve the stability of PCBs in high vibration and high temperature environments. Precise welding control and process parameter adjustment are key to achieving high reliability PCB.
Choosing the right materials is critical to the design of IPC Class III PCBs. Commonly used substrate materials include FR4 and polyimide (PI), which have excellent thermal stability and mechanical strength and can withstand extreme temperatures and environmental conditions. In addition, high-quality copper foil materials and surface treatment technology are also important factors to ensure the stability of PCB performance.
The manufacturing process of IPC Class III PCB requires strict control and monitoring to ensure that every step meets industrial standards. From substrate pretreatment to copper foil layer deposition, photolithography etching, drilling and electroless copper plating, to assembly and testing, every step affects the quality and reliability of the final PCB. Advanced manufacturing equipment and precise process control are the keys to ensuring the high quality of IPC Class III PCBs.
Through this guide, readers can gain a deeper understanding of the key design points and manufacturing processes of IPC Class III PCBs, providing reference and guidance for the development and application of high-reliability electronic devices.
What material is used in IPC Class III Boards?
IPC Class III printed circuit boards (PCBs) have strict requirements on material selection to ensure their stability and performance in extreme environments and high-reliability applications. The following are the main materials commonly used for IPC Class III PCBs:
IPC Class III PCBs usually use high-performance substrate materials, the most common of which is FR4 (fiberglass reinforced epoxy resin). FR4 has excellent electrical insulation properties, mechanical strength and heat resistance, and can maintain stability over a wide temperature range, making it suitable for most application scenarios.
The conductive layer of PCB usually uses copper foil, and its thickness can be determined according to design requirements. IPC Class III PCBs require high-quality copper foil, generally between 1 and 3.5 ounces thick, to ensure good electrical conductivity and reliable soldering connections.
The soldering film is a layer of material covering the surface of the PCB to protect the areas of the circuit board that do not need to be soldered to prevent short circuits and oxidation. For IPC Class III PCBs, the soldering film must have excellent heat resistance and chemical stability to ensure it will not be damaged or peeled off during high-temperature soldering.
Printing ink is used to mark component locations, polarity and other important information on PCBs. In IPC Class III PCBs, printing inks need to have good adhesion and abrasion resistance to maintain long-term readability and reliability.
For some special applications, such as high-frequency circuits, flexible circuit boards, or PCBs in high-temperature environments, special materials may be required. For example, polyimide (PI) is used in flexible PCBs and has excellent tensile strength and high temperature resistance, making it suitable for applications that require bending and folding.
In short, IPC Class III PCB pursues high quality, high performance and high reliability in material selection to meet the needs of various harsh environments and long-term stable operation. Through the appropriate combination of materials, the performance and service life of PCB can be effectively improved, ensuring the reliable operation of electronic equipment in various challenging environments.
What size are IPC Class III Boards?
IPC Class III printed circuit boards (PCBs) are versatile and flexible in size, often depending on their specific application needs and design requirements. These PCBs can cover a wide range from tiny electronic devices to large industrial equipment.
For IPC Class III PCBs, the determination of size is affected by the following key factors:
First, IPC Class III PCBs are typically used in applications requiring high reliability and complex performance, such as aerospace, medical equipment, and defense. In these areas, PCB dimensions are often designed precisely based on the functionality and space constraints of the device. For example, in the field of aerospace, PCB may need to adapt to the small space inside the spacecraft while ensuring its stability in extreme environments such as high radiation and low temperature.
Secondly, the size of the IPC Class III PCB is also affected by the type and density of the electronic components it carries. Modern electronic devices tend to be miniaturized and highly integrated, so PCBs need to be able to accommodate a large number of surface mount devices (SMT) or traditional through-hole components while maintaining a small enough size.
In addition, advances in manufacturing technology and improvements in materials have allowed IPC Class III PCBs to achieve higher performance and reliability in smaller sizes. For example, the application of high-density interconnect (HDI) technology allows the number of PCB layers to be increased to accommodate more circuit paths and connections in the same area.
To sum up, the size of IPC Class III PCBs can range from micro PCBs of a few millimeters, such as flexible PCBs used for medical implantable devices, to PCBs of tens of centimeters or even larger, such as those used in industrial automation equipment or large-scale Communication system board. This diverse size range ensures that IPC Class III PCBs can meet the strict requirements in different industries and applications, providing important support for the development of modern high-end electronic technology.
The Manufacturer Process of IPC Class III Boards.
IPC Class III PCB is a printed circuit board with the highest reliability requirements in the electronics industry. Its manufacturing process is strictly controlled to ensure stability and reliability in extreme environments and long-term use. The following are the main manufacturing process steps of IPC Class III PCB:
First, substrate pretreatment is one of the key steps in the entire manufacturing process. At this stage, it is necessary to ensure that the substrate surface is clean and flat so that subsequent process steps can proceed smoothly. Surface treatment of substrates usually involves removing surface contaminants and oxides to improve the adhesion and quality of the copper foil to the substrate.
Next comes the copper foil layer deposition. A thin copper foil is deposited on the surface of the substrate. This layer of copper foil will become the basis for future circuit pattern formation. The thickness and uniformity of copper foil are critical to the performance and reliability of the final circuit board.
Photolithography and etching technologies are the core steps in manufacturing IPC Class III PCB circuit patterns. Through photolithography technology, the required circuit pattern is formed on the surface of copper foil coated with photosensitive adhesive using light irradiation. The copper foil that is not protected by the photosensitive adhesive is then removed through an etching process to form precise conductive paths and circuit structures.
Drilling and electroless copper plating are steps performed to create holes for connecting components on the PCB and to enhance the strength of the connection. At the predetermined location, the required hole diameter is formed on the PCB through mechanical drilling or laser drilling technology. The walls of these holes are then chemically plated with a layer of copper to enhance electrical connections and mechanical strength.
The final step is assembly and testing. At this stage, precise electronic components are mounted onto the already fabricated PCB. Automated equipment is often used for precise location mounting and soldering of electronic components. After assembly, the PCB undergoes rigorous testing and quality control procedures to verify its electrical performance and reliability, ensuring compliance with the high reliability requirements of IPC Class III.
To sum up, the manufacturing process of IPC Class III PCB is not only technically demanding, but also includes multiple precise process steps. The precise execution and strict control of these steps are key factors to ensure that the final product can operate stably and be used for a long time in various harsh environments.
The Application area of IPC Class III Boards.
IPC Class III PCB is a printed circuit board that meets the highest reliability standards. Its application fields cover a number of key industries, especially playing an important role in fields that require extremely high stability and reliability.
In the aerospace field, IPC Class III PCBs are widely used in flight control systems and spacecraft electronic equipment. These devices have extremely high requirements on the reliability and performance of electronic components and must be able to operate stably in extreme temperature, pressure and radiation environments. For example, in aerospace missions, PCBs must be able to withstand extreme space environments and ensure the accuracy and stability of various sensors, communication and control systems.
The application of IPC Class III PCB in medical equipment is particularly important, such as pacemakers, medical imaging equipment, etc. These devices have strict requirements on the safety and stability of electronic systems and must ensure that they will not malfunction during long-term operation to protect the health and lives of patients. IPC Class III PCB can provide highly reliable circuit connections and ensure the long-term stable operation of electronic equipment, so it is widely used in key equipment in the medical industry.
In the field of national defense, IPC Class III PCB also plays an indispensable role. Defense applications require electronic equipment that can remain efficient, stable and safe in extreme battlefield environments. For example, military equipment such as communication equipment, radar systems, and navigation systems have extremely high requirements on the reliability and anti-interference capabilities of PCBs. IPC Class III PCB ensures the reliable operation of these critical devices under various complex and harsh conditions through strict design standards and high-quality manufacturing processes.
In short, IPC Class III PCB is widely used in many important fields such as aerospace, medical equipment and national defense due to its key reliability and performance advantages in high-end electronic equipment. They not only meet the industry’s strict requirements for the stability and safety of electronic systems, but also promote the continuous progress and innovation of technology, providing solid basic support for modern high-tech applications.
What are the advantages of IPC Class III Boards?
IPC Class III PCB has significant advantages compared with other levels, which are mainly reflected in the following aspects.
First of all, high reliability is one of the distinctive features of IPC Class III PCB. During the design and manufacturing process of this type of PCB, IPC’s highest reliability standards are strictly followed to ensure long-term stable operation in various extreme environments. Whether under high temperature, low temperature, high humidity or strong vibration conditions, IPC Class III PCB can maintain its electrical performance and mechanical strength and will not fail due to environmental changes, thus ensuring the stability and reliability of the equipment.
Secondly, IPC Class III PCB has been rigorously designed and tested and has excellent durability. During the manufacturing process, high-quality substrate materials such as FR4 and special high-temperature materials are used to ensure that the PCB can work stably for a long time in complex applications. In addition, the welding and connection technology uses the most advanced surface mount technology (SMT) and through-hole technology to ensure the firmness and reliability of the welded joints, further enhancing the service life of the PCB in challenging environments.
IPC Class III PCB is also in a leading position in technology. Advanced production equipment and processes are used in the manufacturing process, such as precise photolithography and etching technology, high-precision automated assembly lines, and sophisticated testing and verification procedures. These advanced technologies not only improve production efficiency, but also ensure the quality and consistency of each PCB to meet the most demanding industrial standards.
To sum up, IPC Class III PCB has become the first choice for many industries, especially aerospace, medical equipment and national defense due to its high reliability, excellent durability and leading technical advantages. They not only play an important role in key equipment and systems, but also promote the continuous innovation and progress of electronic technology in various fields.
FAQ
How is IPC Class III PCB different from other classes?
Compared with other levels, IPC Class III PCB mainly lies in its higher reliability and durability requirements. They must be designed and manufactured to more stringent standards to maintain stability in extreme environments and long-term use.
Which industries are IPC Class III PCB suitable for?
This type of PCB is widely used in high-reliability fields such as aerospace, medical equipment, and national defense. For example, it is used in flight control systems and satellite communication equipment in aerospace, in medical equipment for pacemakers and medical imaging equipment, and in the defense field for communication equipment and radar systems.
What aspects should be paid attention to when designing IPC Class III PCB?
When designing an IPC Class III PCB, special attention needs to be paid to the optimization of the circuit layout, the selection of soldering and connection techniques, and the high temperature resistance and mechanical strength of the materials. Ensure that every step meets the strict requirements of IPC to ensure high reliability of the final product.
What are the key steps in the manufacturing process of IPC Class III PCB?
The key steps in manufacturing IPC Class III PCBs include substrate pretreatment, copper foil layer deposition, photolithography and etching, drilling and electroless copper plating, assembly and testing, etc. Each step must be precisely controlled to ensure the final PCB meets design requirements and standards.