IPC Class III PCB Manufacturer, Military PCB, Aerospace PCB, Satellites PCB, we mainly produce ultra-small bump pitch and ultra-small trace Military substrate from 2 layer to 50 layers.
In modern electronic equipment, IPC Class III PCB (Printed Circuit Board) plays a vital role. They are not only the foundation of electronic equipment, but also one of the key factors in ensuring equipment performance, reliability and durability. IPC Class III PCBs are designed to operate in extreme environments such as aerospace, medical equipment, and military applications. They undergo strict quality control and testing to ensure stable operation under harsh conditions and are an important part of modern high-reliability electronic systems.
What is IPC Class III PCB?
IPC Class III PCB is a high-reliability printed circuit board that complies with IPC (Electronic Industries Consortium) standards. In electronics manufacturing, IPC standards are a key guide to ensuring product quality and consistency. IPC Class III PCBs are one of the highest-level circuit boards in the IPC standard. They are designed for mission-critical applications in extreme environments, such as aerospace, medical equipment, and military equipment.
The IPC Class III standard requires PCBs to have the highest levels of reliability and durability. This means that these boards must be able to operate under harsh conditions for extended periods of time without failure or performance degradation. Whether in extreme environments such as high temperature, low temperature, high humidity, strong vibration or high pressure, IPC Class III PCB must be able to maintain stable performance.
In the aerospace field, IPC Class III PCB is widely used in flight control systems, satellite communication equipment and spacecraft navigation systems. These systems require extremely high reliability of electronic components because they are directly related to the safety of the spacecraft and mission success.
In the field of medical equipment, IPC Class III PCBs are used in key equipment such as pacemakers, medical imaging equipment, and surgical navigation systems. These devices must operate reliably under a variety of harsh environmental conditions to ensure the smooth progress of medical procedures and patient safety.
In the field of military equipment, IPC Class III PCB is used in radar systems, missile control systems and military communication equipment. These systems need to withstand severe tests in battlefield environments, so they place extremely high requirements on the reliability and durability of PCBs.
In summary, the application range of IPC Class III PCBs covers many key areas, and their high reliability and durability make them an indispensable component in these areas.
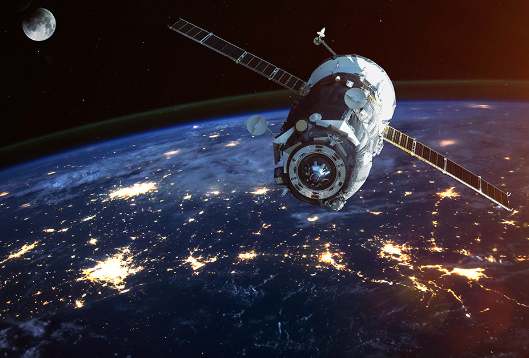
IPC Class III PCB
IPC Class III PCB design Reference Guide.
When designing an IPC Class III PCB, focusing on key factors is key to ensuring its high reliability and performance stability. Here are some suggestions from the IPC Class III PCB Design Reference Guide:
Place And Route
During the layout design stage, ensure a reasonable circuit board layout and minimize signal line lengths and crossovers to reduce the effects of signal crosstalk and electromagnetic interference. At the same time, rationally arrange power and ground wires to ensure good power distribution and ground plane.
Material Selection
Choosing high-quality materials is crucial for IPC Class III PCB. Use high-temperature-resistant and corrosion-resistant substrates, such as FR-4 fiberglass composite materials, to ensure stability in extreme environments. At the same time, high-purity copper foil is selected as the conductive layer to ensure good signal transmission and thermal performance.
Electrical Characteristics
Special attention should be paid to electrical characteristics during the design process to ensure that the PCB meets the required electrical requirements. This includes consideration of aspects such as signal integrity, power dissipation distribution, noise control, and electromagnetic compatibility. The stability and reliability of your circuit can be maximized through proper layout and signal integrity analysis.
Environmental Adaptability
Consider the circumstances in which an IPC Class III PCB will operate in a variety of extreme environments. Therefore, the design should consider factors such as temperature range, humidity, vibration and shock, and select materials and processes that comply with relevant standards and certifications. In addition, protective measures such as dustproof, waterproof and anti-corrosion treatments should also be considered in the design.
By following the above recommendations and combining them with the requirements of the IPC Class III standard, the designed PCB will have higher reliability and performance stability, and can meet the application needs in various extreme environments.
What material is used in IPC Class III PCB?
IPC Class III PCBs typically use a range of high-quality, high-temperature-resistant materials to ensure their stability and reliability in extreme environments. Among them, the most common materials include FR-4 fiberglass composites and high-purity copper foil.
FR-4 fiberglass composite material is an insulating material whose main components are glass fiber and epoxy resin. This material has excellent mechanical strength and heat resistance, and can withstand the stress and pressure of high-temperature environments while maintaining stable electrical performance. FR-4 material also has excellent corrosion resistance and humidity resistance, and can operate stably for a long time in harsh working environments.
In addition, IPC Class III PCB also uses high-purity copper foil as the basic material of the conductive layer. High-purity copper foil has excellent electrical and thermal conductivity, and can effectively transmit current and dissipate heat, ensuring that the PCB maintains stable performance under high-power operation. In addition, high-purity copper foil also has good welding performance and can be firmly connected with other components to ensure the reliability and stability of the entire circuit.
Taken together, the materials used in IPC Class III PCB have excellent performance and reliability and can meet the strict requirements for high reliability and durability. The selection of these materials can not only ensure the stable operation of the PCB in extreme environments, but also improve the performance and reliability of the entire electronic device, providing reliable protection for various critical applications.
What size are IPC Class III PCB?
IPC Class III PCBs are sized according to the requirements of specific applications, which allows them to meet the needs of a variety of devices. In practical applications, IPC Class III PCBs can have a variety of sizes, ranging from small and compact designs to large and complex structures.
For some small electronic devices, such as portable medical equipment or smart wearable devices, the size of IPC Class III PCB is usually smaller. These small PCB designs often need to fit as many electronic components as possible in a limited space, so they are often very compact. Despite their smaller size, these PCBs still need to meet the high reliability and durability requirements of IPC Class III standards.
In contrast, some large electronic equipment, such as aerospace devices, industrial control systems or communication base stations, may require larger and more complex IPC Class III PCB designs. These PCBs usually have a multi-layer structure to accommodate a large number of electronic components and complex circuits. Their size may be significantly larger than PCBs used in small devices, but they also need to meet the stringent requirements of the IPC Class III standard to ensure their reliability and stability in extreme environments.
Whether it is a small or large IPC Class III PCB design, it needs to undergo rigorous verification and testing to ensure that it meets the requirements for high reliability and durability. Therefore, when selecting an IPC Class III PCB, in addition to size, you also need to consider its performance, quality standards and reliability guarantee in a specific application environment.
The Manufacturer Process of IPC Class III PCB.
The manufacturing process of IPC Class III PCB is a rigorous and precise process involving multiple critical steps to ensure the reliability and durability of the final product.
First, design verification is the first step in manufacturing IPC Class III PCB. During this stage, engineers design using advanced CAD software to ensure that the circuit board layout complies with specifications and meets the requirements of the specific application. This process includes consideration of aspects such as routing, component placement, power distribution, and signal integrity.
Next comes the prototyping phase. Once design verification is complete, engineers create a prototype board for testing and evaluation. The purpose of this phase is to verify the feasibility of the design and identify and fix any possible problems.
Circuit board forming is the next critical step in manufacturing IPC Class III PCBs. At this stage, the basic structure of the circuit board is formed by laminating fiberglass cloth and copper foil together. Material selection and lamination process are critical to the performance and stability of the final product.
Component mounting is another critical step in manufacturing IPC Class III PCBs. At this stage, the precisely arranged and soldered components are mounted onto the circuit board. This requires highly sophisticated automated equipment and technology to ensure the correct placement and reliable connection of each component.
Finally comes the testing phase. After completing the component installation, the IPC Class III PCB will undergo a series of rigorous tests, including functional testing, electrical testing and environmental testing. These tests ensure that the board operates reliably under a wide range of operating conditions and complies with the requirements of the IPC Class III standard.
The entire manufacturing process is subject to strict quality control and follows international standards such as ISO and IPC. Through these measures, manufacturers can ensure that each step meets the highest standards, thereby producing high-reliability PCBs that comply with IPC Class III standards.
The Application area of IPC Class III PCB.
IPC Class III PCBs are widely used in industries with extremely high reliability requirements, including aerospace, medical equipment, defense and industrial control systems. In the aerospace field, IPC Class III PCBs undertake the important task of connecting critical avionics equipment. Avionics equipment needs to operate stably in extreme environments (such as high temperature, low temperature, high humidity, high pressure, etc.), and the high reliability and durability of IPC Class III PCB ensures the normal operation of these equipment and provides a solid foundation for flight safety. protection.
In the field of medical equipment, IPC Class III PCB is widely used in various medical diagnostic and treatment equipment. For example, devices such as pacemakers, medical imaging equipment, and surgical robots all rely on high-quality PCBs to ensure their stable performance and reliable operation. The normal operation of medical equipment is directly related to the life safety and health of patients, so the reliability requirements for IPC Class III PCBs are more stringent.
In the field of national defense, IPC Class III PCB is used to manufacture various military electronic equipment, such as communication systems, navigation systems, radars and fire control systems. These devices need to operate reliably in harsh battlefield environments, so the high reliability and durability of IPC Class III PCBs are indispensable. The normal operation of defense equipment is crucial to the success of military operations, so the quality and reliability of PCBs are extremely high.
In the field of industrial control systems, IPC Class III PCB is used to manufacture various industrial automation equipment and control systems, such as PLC (programmable logic controller), sensors, actuators, and monitoring systems. These devices need to operate stably for a long time to ensure normal production of factories and production lines, so the reliability and stability of IPC Class III PCBs are extremely high.
Overall, IPC Class III PCB plays a vital role in these key areas, ensuring the safe operation and stable performance of the equipment. Its high reliability, durability and stability make it the first choice in these industries, providing solid support and guarantee for various critical applications.
What are the advantages of IPC Class III PCB?
IPC Class III PCBs offer many advantages that make them the preferred choice in many critical applications.
First, IPC Class III PCB has high reliability. They are designed and manufactured to meet strict IPC standards to ensure stable performance in extreme environments. Whether in high temperature, low temperature, high humidity or low humidity environments, IPC Class III PCBs can operate reliably and are less prone to failure.
Secondly, IPC Class III PCB has high temperature resistance. They use high-quality materials and advanced manufacturing processes, allowing them to work in high-temperature environments for a long time without being affected. This makes them ideal for applications that require operation at high temperatures, such as aerospace and automotive electronic systems.
Additionally, IPC Class III PCBs are shock and vibration resistant. They are designed with high strength and can withstand external shock and vibration, ensuring the stability and reliability of the equipment during transportation and use. This allows them to maintain good performance in harsh working environments, such as military equipment and industrial control systems.
Overall, IPC Class III PCB has the advantages of high reliability, high temperature resistance, impact resistance, and vibration resistance, making it the preferred choice in many critical applications. They can meet stringent industrial standards and requirements to ensure safe operation and stable performance of equipment in various extreme environments.
FAQ
What are the differences between IPC Class III PCBs compared to other classes of PCBs?
IPC Class III PCB has higher reliability and durability than other classes of PCB. They are rigorously designed and manufactured to meet the needs of extreme environments such as high temperature, high pressure and vibration. Compared with IPC Class I and IPC Class II, IPC Class III PCB requirements are more stringent and suitable for applications that require extremely high performance and reliability.
How much does an IPC Class III PCB cost?
Because the design and manufacturing process of IPC Class III PCB is more complex and requires the use of high-quality materials and strict quality control, its cost is usually higher. However, given its importance in the field of high reliability, its cost can be viewed as a guaranteed investment in equipment performance and stability.
How is IPC Class III PCB quality tested?
IPC Class III PCBs undergo strict quality control and testing during the manufacturing process. This includes multiple stages such as raw material inspection, design verification, finished product inspection and reliability testing. Common testing methods include X-ray testing, ultrasonic testing, electron microscopy, and thermal shock testing to ensure that the PCB meets the requirements of the IPC Class III standard.
How to maintain and repair IPC Class III PCB?
Maintenance and repair of IPC Class III PCBs needs to be carried out in strict accordance with the manufacturer’s recommendations and guidelines. This typically involves regular cleaning, checking the condition of connectors and solder joints, and replacing damaged components. For severely damaged PCBs, it is recommended to seek professional technical support to ensure the effectiveness and safety of repair operations.