We are a professional Low CET PCB manufacturing, we mainly produce ultra-small bump pitch substrate, ultra-small trace and spacing packaging.
Printed Circuit Boards (PCBs) play a vital role in the manufacturing of modern electronic devices. They not only provide support and connections for electronic components, but also implement various functions of the device. With the increasing awareness of environmental protection, Low CET (low odor, low corrosion, low pollution) technology has become an important trend in the field of PCB manufacturing. This article aims to introduce the key contents of Low CET PCB manufacturing and help readers gain a deeper understanding of this environmentally friendly PCB manufacturing technology.
What is low volatility PCB?
In the manufacturing of modern electronic equipment, low-volatility PCBs (Printed Circuit Boards) play a crucial role. They serve as a support and connection platform for electronic components, connecting individual components through wires, jumpers, and other connectors to build circuit structures. The emergence of low-volatile PCB is to solve the problem of volatile organic compound release that may occur during the manufacturing and use of traditional PCB, and to reduce the adverse effects on the environment and human health.
Low-volatility PCBs serve as the infrastructure and support for circuits in electronic devices. They not only provide stable electrical connections, but can also withstand the weight and pressure of electronic components. By arranging electronic components on the PCB and connecting them, low-volatility PCBs realize various functions of electronic devices, from simple household appliances to complex computer systems, which are inseparable from their support.
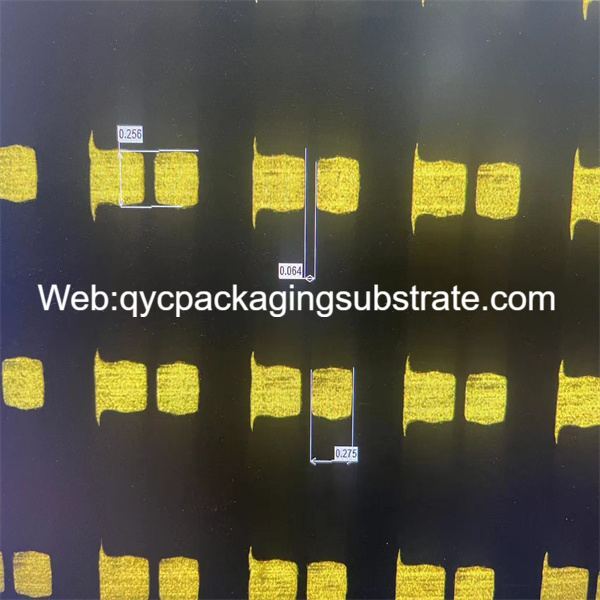
Low CET PCB manufacturing
Low-volatility PCB uses a series of environmentally friendly materials and processes to reduce the release of organic volatiles. These PCBs usually use materials such as low-volatile resin, environmentally friendly copper foil and lead-free solder, and reduce the release of harmful substances through strict manufacturing processes and quality control. This not only helps reduce environmental pollution, but also protects the health and safety of production workers and end users.
A series of environmentally friendly materials and methods are used in the manufacturing process of low-volatility PCBs, including low-volatility resins, environmentally friendly copper foil, lead-free solder, etc. These materials can reduce the release of organic volatile compounds during manufacturing and use, reducing their impact on the environment and human health. At the same time, manufacturers have also adopted strict quality control measures to ensure that the PCBs produced meet environmental standards and customer requirements.
The emergence of low-volatility PCBs has brought new possibilities to electronic equipment manufacturing, which not only meets modern environmental protection requirements, but also provides manufacturers and users with safer and more reliable solutions. With the continuous development of technology and the enhancement of environmental awareness, it is believed that low-volatility PCB will be more widely used and promoted in the future.
How to design low volatility PCB?
Designing low-volatility PCBs is a complex and critical task that requires the consideration of multiple factors to ensure compliance with environmental and health standards while maintaining good performance and reliability. During the design process, the following factors are crucial:
First, material selection is key to designing low-volatility PCBs. Engineers need to choose low-volatility substrate materials, copper clad materials, and soldering materials to minimize the harmful gases released by PCBs during use. In addition, you should also consider choosing materials that meet environmental requirements, such as environmentally friendly resin and copper foil, to reduce the negative impact on the environment.
Secondly, lamination design and wiring layout are also one of the key factors to consider when designing low-volatility PCBs. Reasonable lamination design can reduce the release of volatile substances inside the PCB, while good wiring layout can reduce electromagnetic radiation and electrical noise, thereby reducing the impact on human health.
In addition, using professional PCB design software is also the key to designing low-volatility PCBs. These software provide rich features and tools to help engineers perform precise routing design, laminate planning and signal integrity analysis to improve design efficiency and accuracy.
By using professional PCB design software, engineers can better control the PCB layout and lamination structure, thereby minimizing environmental pollution and human health risks. For example, software can help engineers optimize the layout of signal lines, reduce electromagnetic radiation, and reduce electrical noise, thereby reducing the negative impact on the surrounding environment and human health.
In general, designing low-volatility PCBs requires comprehensive consideration of multiple factors such as material selection, lamination design, wiring layout, and the use of professional PCB design software. Through reasonable design and process control, environmental pollution and human health risks can be minimized and sustainable development of PCB manufacturing can be achieved.
What is the manufacturing process of low volatility PCB?
The manufacturing process of low-volatility PCBs is significantly different from traditional PCB manufacturing in terms of material selection and process. First of all, the manufacturing process of low-volatility PCB pays more attention to environmental protection and human health factors. In terms of material selection, traditional PCBs usually use volatile organic compounds such as halides, solvents and fluxes, while low-volatile PCBs use materials such as low-volatile resins and environmentally friendly copper foil to reduce the emission of volatile organic compounds. In addition, lead-free solder is often used in low-volatility PCB manufacturing processes to avoid lead contamination.
In terms of process, manufacturing low-volatility PCBs requires strict control of pollutants in the production environment, including factors such as air quality, temperature, and humidity. Production workshops usually adopt a closed design and are equipped with effective ventilation systems and exhaust gas treatment facilities to ensure that volatile organic compounds and other pollutants emitted during the production process are effectively controlled.
In addition, the manufacturing process of low-volatility PCB also requires the use of special process technologies, such as vacuum forming, vacuum potting and high-temperature curing, etc., to ensure that the surface of the PCB board is smooth, bubble-free, and has good electrical performance and reliability.
During the production process, manufacturers will also strictly implement environmental protection standards and customer requirements, and strictly screen and test raw materials to ensure that they comply with relevant environmental regulations and quality standards. At the same time, manufacturers will also establish a complete quality management system and adopt comprehensive quality control measures, including raw material inspection, production process monitoring and finished product testing, to ensure that the PCBs produced meet customer requirements and expectations.
To sum up, the manufacturing process of low-volatility PCBs not only focuses on product quality and performance, but also focuses on environmental protection and human health protection. By using environmentally friendly materials and processes, strictly controlling pollutant emissions during the production process, and strictly implementing environmental standards and customer requirements, manufacturers can produce high-quality, low-volatility PCBs that meet environmental requirements and provide customers with more reliable and Sustainable solutions.
How much does a low volatility PCB cost?
The cost of manufacturing low-volatility PCBs may be slightly higher than that of traditional PCBs, mainly because of the use of more expensive environmentally friendly materials and processes. First, low-volatility PCBs require the use of special materials such as low-volatility resins and lead-free solders, which are more expensive. Secondly, producing low-volatility PCBs requires strict control of pollutants in the production environment, such as volatile organic compounds (VOCs) and harmful gases, which increases the cost of the production process. In addition, in order to meet environmental requirements and customer quality standards, manufacturers may need to conduct additional testing and certification, which will also increase manufacturing costs.
However, with the development of technology and the increasing awareness of environmental protection, the cost of low-volatile PCBs is gradually declining. First of all, with the continuous advancement of environmental protection technology, the environmentally friendly materials and processes required to produce low-volatility PCBs have gradually matured, and the costs have gradually reduced. Secondly, as the market demand for low-volatility PCBs increases, the expansion of production scale will also help reduce production costs. In addition, manufacturers continue to optimize production processes and technologies to improve production efficiency, which also helps reduce costs.
To take cost-saving measures, manufacturers can consider the following points. First, optimize supply chain management and find lower-cost material and component suppliers. Secondly, improve production efficiency and reduce waste and loss during the production process, such as optimizing layout and improving equipment utilization. In addition, develop a reasonable inventory management strategy to avoid inventory backlog and wastage of funds. Finally, continuously conduct cost analysis and evaluation to find potential opportunities for cost reduction and adjust production strategies in a timely manner.
In summary, although the manufacturing cost of low-volatility PCBs may be slightly higher, with the development of technology and the increase in market demand, the cost of such PCBs is gradually declining. By optimizing production processes, managing supply chains and improving production efficiency, manufacturers can take effective cost-saving measures to improve the competitiveness and sustainable development capabilities of low-volatile PCBs.
What are the materials for low-volatility PCBs?
In the manufacturing of low-volatility PCBs, commonly used materials mainly include environmentally friendly resins, low-volatility copper foil, and lead-free solder. These materials have certain characteristics in their selection and use to ensure that the PCB reduces the release of volatile substances as much as possible during the manufacturing and use processes, and maintains environmental friendliness and human health.
Characteristics of commonly used low-volatility PCB materials:
Environmentally friendly resin: Low-volatility PCBs often use environmentally friendly resins, such as epoxy resin or polyimide resin. These resins have low volatility, are not prone to releasing harmful gases, and comply with environmental protection requirements.
Low-volatile copper foil: Copper foil is one of the basic materials of PCB. Low-volatile copper foil usually has more stable chemical properties, reduces the release of volatile substances, and performs well in soldering and conductive properties.
Lead-free solder: In order to reduce environmental pollution, low-volatility PCBs usually use lead-free solder. This solder does not contain lead, which reduces the release of lead during manufacturing and use, protecting the ecological environment and the health of workers.
Performance and reliability advantages of these materials:
Stability: Low-volatility PCB materials have more stable chemical properties and can maintain consistent performance under different environmental conditions.
Environmental protection: PCBs made of environmentally friendly materials meet modern environmental protection requirements, will not cause pollution to the environment, and are in line with the development trend of green manufacturing.
Reliability: These materials undergo strict quality control during the manufacturing process, ensuring the reliability and stability of the PCB and reducing failure rates and repair costs.
With the continuous advancement of science and technology, low-volatility PCB materials are also constantly improved and optimized. In the future, we can look forward to the emergence of materials that are more environmentally friendly and have superior performance, bringing greater room for development to the electronics manufacturing industry. For example, we are developing more environmentally friendly resins and solders, and improving the high-temperature resistance and conductivity of materials to meet the growing requirements for PCBs in electronic products. With the application of new materials and process improvements, low-volatility PCBs will play a more important role in the future and become one of the mainstream products in electronic manufacturing.
Who is making low-volatility PCBs?
When it comes to manufacturing low-volatility PCBs, many companies are committed to providing high-quality products that meet environmental standards and customer needs. Among them, our company, as a professional PCB manufacturer, also plays an important role in this field.
First of all, our company uses advanced production equipment and technology to ensure the efficiency and accuracy of the production process. We pay attention to details and quality control, from raw material procurement to production of final products, strictly following international standards and customer requirements.
When manufacturing low-volatility PCBs, our company pays special attention to material selection. We use materials such as low-volatile resin, environmentally friendly copper foil and lead-free solder to ensure that the PCBs produced meet environmental standards and customer expectations. These materials not only reduce environmental pollution and human health risks, but also provide excellent performance and reliability.
Our company focuses on technological innovation and continuous improvement, and is committed to providing the most advanced manufacturing technology and the highest quality products. We have an experienced and skilled team that can meet the diverse needs of our customers and provide customized solutions. Through strict quality control processes and inspection standards, we ensure that each batch of products can meet customer requirements and expectations.
As a customer-first company, we always put our customers’ needs and satisfaction first. We provide timely and thoughtful customer service to solve problems and answer questions for customers to ensure that they can get a satisfactory shopping experience and high-quality products.
In the process of manufacturing low-volatility PCBs, our company adheres to the concept of quality first and customer first, and constantly strives to innovate and improve to provide customers with better products and services. We will continue to be committed to the development and promotion of environmentally friendly technologies, and work with our customers to promote the electronics manufacturing industry in a more environmentally friendly and sustainable direction.
Five Characteristics of Great Customer Service
Excellent customer service is a key component of any successful business. It means more than just providing a product or service. It is an important means of building and maintaining customer relationships. Here’s a closer look at five characteristics of great customer service:
Be Responsive: Good customer service starts with timely feedback. Customers expect a quick response when raising questions or inquiries. An efficient customer service team should ensure that customers’ emails, phone calls, or online chats are responded to in the shortest possible time in order to resolve customer issues and provide support.
Professional knowledge: Service personnel should have rich professional knowledge and be able to answer various technical questions raised by customers. Whether a customer is facing a simple consultation or a complex technical challenge, the service team should be able to provide accurate and clear solutions to help customers solve their problems and achieve success.
Personalized service: Every customer is unique, so great customer service should be personalized to the customer’s specific needs. This means service teams need to have a deep understanding of their customers’ businesses and preferences to provide the most appropriate solutions. Through personalized services, companies can build closer relationships with customers and increase customer satisfaction and loyalty.
Problem-solving skills: Great customer service is not just about answering questions, it’s about solving problems. The service team should have problem-solving capabilities and be able to respond quickly and effectively to various difficulties and challenges encountered by customers. This may involve technical support, troubleshooting, after-sales service, etc. The service team needs to proactively work with customers to solve problems and ensure customer satisfaction.
Communicate effectively: Good communication is the foundation of great customer service. Service staff should be good at listening to customers’ needs and opinions and conveying information clearly. Timely communication can help eliminate misunderstandings, strengthen cooperation, and build trust and resonance. Through effective communication, companies can establish good relationships with customers and improve customer satisfaction and loyalty.
To sum up, great customer service is not just about providing a product or service, it’s about building and maintaining good customer relationships. Through prompt response, expertise, personalized service, problem-solving capabilities and effective communication, companies can provide customers with an excellent experience, establish a good brand image and achieve sustained business success.
FAQs (Frequently Asked Questions)
What is the typical lead time for manufacturing Low CET PCBs?
The lead time for manufacturing Low CET PCBs varies depending on factors such as the complexity of the design, the quantity ordered, and the manufacturing capabilities of the supplier. Typically, lead times can range from a few days to several weeks.
Are Low CET PCBs more expensive than traditional PCBs?
Generally, Low CET PCBs may have slightly higher manufacturing costs compared to traditional PCBs due to the specialized materials and processes involved in their production. However, the price difference is often justified by their environmental benefits and enhanced performance.
What are the environmental benefits of using Low CET PCBs?
Low CET PCBs are manufactured using materials and processes that emit fewer volatile organic compounds (VOCs), reducing air pollution and minimizing the environmental impact of electronic device manufacturing. Additionally, these PCBs contribute to safer working conditions for workers in manufacturing facilities.
How do Low CET PCBs contribute to sustainable electronics manufacturing?
By reducing the emission of harmful chemicals and pollutants during production, Low CET PCBs support sustainable electronics manufacturing practices. They align with global initiatives aimed at reducing the environmental footprint of electronic devices and promoting a circular economy.