Micro cavity substrates manufacturing. the Package Substrate will be made with Showa Denko and Ajinomoto High speed materials.or other types
Microcavity substrates (MCS) are the backbone of leading electronic devices, enabling compact designs and superior performance. In this comprehensive guide, we dive into the complexities of microcavity substrate manufacturing, exploring the processes, materials and considerations that drive this critical aspect of PCB production.
What is a microcavity substrate?
Micro Cavity Substrates (MCS) are a special type of Printed Circuit Board (PCB) designed and manufactured to meet the requirements of modern electronic equipment for compact design, high performance and high-density integration. need. Compared with traditional PCBs, microcavity substrates are more complex in structure, with tiny and precise grooves (called “cavities”) that are used to house microelectronic components such as microchips, sensors and transistors.
Microcavity substrates play a vital role in electronic devices, and their main functions include the following aspects:
Improve space utilization: The design of the microcavity substrate allows electronic components to be arranged in a more compact space, effectively improving space utilization. This is especially critical for miniaturized and lightweight electronic devices, such as smartphones, wearable devices, etc.
Optimize thermal management: Microcavity substrates can achieve effective thermal management by designing the cavity structure and selecting appropriate heat dissipation materials. This is especially important for devices integrating high-power components to avoid performance issues or damage caused by overheating.
Improve signal integrity: By accurately designing the wiring and hierarchical structure of the microcavity substrate, signal interference and crosstalk can be minimized, thereby ensuring the signal integrity and reliability of electronic equipment.
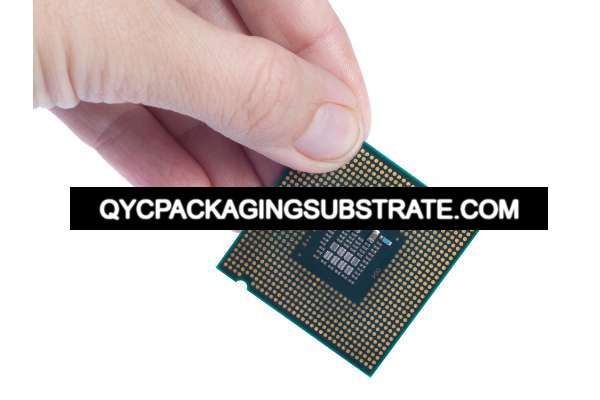
Micro cavity substrates manufacturing
Supports high-density integration: The design of the microcavity substrate allows more electronic components to be integrated into a smaller space, thereby achieving higher device density and functional integration. This provides the possibility for function expansion and performance improvement of modern electronic devices.
Provide specific environmental protection: For specific application scenarios, the microcavity substrate can be manufactured with special materials to provide additional environmental protection functions, such as waterproofing, dustproofing, high temperature resistance, etc., thereby enhancing the durability and reliability of the device.
Overall, microcavity substrates play a key role in modern electronic devices, and their precise design and manufacturing provide a solid foundation for the performance, functionality, and reliability of electronic products. Through continuous innovation and technological advancement, microcavity substrates will continue to promote the development and progress of the field of electronic devices.
What is the manufacturing process of microcavity substrates?
The manufacturing process of microcavity substrates is a precise and complex process involving multiple critical steps, each of which is critical to ensure the quality and performance of the final product. First, one of the key steps in fabricating microcavity substrates is material preparation. Selecting the appropriate substrate material is critical to the performance of the final product. Usually, the microcavity substrate can be made of ceramic, FR-4 or flexible materials such as polyimide, selected according to specific application requirements.
Next comes graphic design and template making. In this step, the design team uses computer-aided design (CAD) software to create blueprints of the microcavity substrate. These design drawings include key information such as circuit layout, microcavity location and size. The design is then converted into an actual template or mask using advanced techniques such as photolithography and laser cutting.
The next step in making a microcavity substrate is to form tiny cavities on the substrate through methods such as drilling or chemical etching. These microcavities often have micron-level size and precision requirements, requiring high-precision processing equipment and technology to ensure accuracy and consistency. Advanced laser drilling technology and precise chemical etching processes can achieve micron-level precision to meet the requirements of microcavity substrates.
After the microcavity is formed, surface treatment and connection metallization are required. These steps include surface cleaning, metallization, and welding to ensure that the microcavity substrate has a smooth surface, good conductivity, and reliable connection to electronic components. Finally, quality inspection and testing ensure that the microcavity substrate meets the design requirements and has stable performance and reliability.
In general, the manufacturing process of microcavity substrates requires the comprehensive use of advanced materials, processes, and equipment to ensure micron-level precision and stable performance. Through strict quality control and testing, manufacturers can produce microcavity substrates that meet high requirements and meet application needs in different fields.
How is the production of microcavity substrates performed?
The production of microcavity substrates is a complex and precise process involving a variety of technologies and engineering. To ensure consistency and reliability in production, manufacturers need to adopt a series of strict measures and standards. The key steps and related technologies for microcavity substrate production will be introduced in detail below.
First, the production of microcavity substrates begins with the preparation and accurate conversion of design files. Manufacturers must ensure a seamless transition from design files to the actual production process, often using computer-aided manufacturing (CAM) software to accomplish this step. CAM software can convert design files into instructions required for production to ensure accuracy and consistency in production.
Next comes the material preparation and handling stage. The fabrication of microcavity substrates typically uses high-quality substrate materials such as fiberglass-reinforced epoxy (FR-4) or high-temperature ceramics. At this stage, manufacturers need to carefully select and prepare materials to ensure they meet product specifications and quality standards.
This is followed by the formation of microcavities. This step typically uses advanced processing techniques such as laser drilling or chemical etching. Through a precisely controlled process, manufacturers are able to precisely create tiny cavities on the substrate surface to house tiny electronic components.
After the microcavity is formed, the next step is the production of circuit patterns. This step usually uses photolithography technology to precisely print the circuit pattern on the surface of the substrate. Manufacturers need to ensure the accuracy and consistency of the photolithography process to guarantee the quality and performance of the final product.
After completing the circuit pattern, it is time to enter the connection and assembly stage. This stage involves soldering components, connecting wires, and completing the final assembly. Manufacturers need to ensure the accuracy and reliability of connections to ensure the stability and performance of microcavity substrates.
Finally, the finished microcavity substrate needs to undergo strict quality inspection and testing. The manufacturer will conduct a thorough inspection of each production batch to ensure that the product meets design specifications and quality standards. By using advanced testing technology and equipment, manufacturers can promptly discover and resolve any potential quality issues to ensure product reliability and stability.
In summary, the production of microcavity substrates involves multiple key steps and technologies, requiring precision processes and strict control from manufacturers to ensure product consistency and reliability. Through careful design, material selection and process control, manufacturers are able to produce high-quality, excellent-performance microcavity substrates to meet the needs of various electronic devices.
What are the cost considerations for microcavity substrates?
The cost of microcavity substrates is the combined result of many factors that influence the design, manufacturing, and assembly processes. Understanding these factors and taking corresponding optimization measures can effectively reduce the cost of microcavity substrates while ensuring product quality and performance.
First, the material selection of the microcavity substrate plays a key role in cost. Different substrate materials have different properties and costs. For example, high-performance ceramic substrates are generally more expensive, but can provide excellent thermal conductivity and high temperature resistance, making them suitable for harsh environments. In comparison, standard materials such as FR-4 are lower cost and suitable for applications with general performance requirements. Therefore, when selecting substrate materials, cost and performance requirements need to be considered comprehensively to select the most cost-effective material.
Secondly, design considerations also directly affect the cost of the microcavity substrate. Reasonable design can reduce material waste and processing costs. For example, optimized layout and routing can reduce substrate area, thereby reducing material usage; carefully designed heat dissipation structures can reduce thermal management costs. In addition, the design takes into account the ease of manufacturing and assembly, which can reduce costs and man-hours in the subsequent production process and improve production efficiency.
In addition, production scale is also one of the important factors affecting the cost of microcavity substrates. Typically, large-scale production enables higher economics because fixed costs can be spread over more products. Therefore, for high-volume production of microcavity substrate orders, manufacturers can reduce unit product costs by adopting automated production equipment and process optimization.
In general, to control the cost of microcavity substrates, it is necessary to comprehensively consider material selection, design optimization, and production scale, and constantly seek innovative methods to improve efficiency and reduce costs. Through effective cost management strategies, manufacturers can provide cost-effective microcavity substrate products that meet customer needs while maintaining a competitive advantage.
What materials are used for microcavity substrates?
The material selection of the microcavity substrate is critical to its performance and range of applications. Typically, microcavity substrates can be made from a variety of materials, each with unique characteristics and applicability. The following are several common microcavity substrate materials and their characteristics:
Ceramic microcavity substrates have excellent high temperature resistance and good mechanical strength, and are suitable for electronic equipment in high temperature environments.
The material’s excellent thermal conductivity helps dissipate heat efficiently, making it widely used in high-power electronic devices.
FR-4 microcavity substrate is a common general-purpose substrate with good mechanical strength and wear resistance.
The material’s relatively low cost and proven manufacturing process make it suitable for many standard electronic applications.
Flexible polyimide microcavity substrates offer excellent flexibility and high temperature resistance for use in curved and foldable electronic devices.
This material is lightweight and has good chemical stability, making it suitable for application scenarios in some special environments.
Metal microcavity substrates, usually made of aluminum or copper, have excellent thermal conductivity and are suitable for high-power and high-frequency electronic devices.
This material has high thermal conductivity, which helps to quickly conduct heat to the surrounding environment and maintain the stable working condition of the equipment.
High-frequency microcavity substrates usually use special dielectric materials with excellent high-frequency characteristics and low loss.
This material has a low dielectric constant and small loss factor, allowing it to efficiently transmit high-frequency signals and is suitable for radio frequency and microwave applications.
When selecting microcavity substrate materials, it is necessary to comprehensively consider application scenarios, performance requirements, and cost factors. Different materials have unique advantages and limitations, so selection needs to be made on a case-by-case basis to ensure optimal performance and reliability.
Who are the major microcavity substrate manufacturers?
In the world of microcavity substrate (MCS) manufacturing, finding a manufacturer you can trust is crucial. Many companies are committed to providing high-quality microcavity substrate solutions, and some of them stand out as industry leaders. Here are some of the major microcavity substrate manufacturers:
The company has established a good reputation in the field of microcavity substrate manufacturing. We have advanced equipment and technology and focus on providing customized microcavity substrate solutions to meet customers’ unique needs and specifications. Our manufacturing process strictly follows international standards and is equipped with strict quality control measures to ensure the quality and reliability of each product.
As a microcavity substrate manufacturer, we focus on technological innovation and continuous improvement. Our team consists of experienced engineers and technicians who are committed to continuously exploring new manufacturing technologies and materials to meet the evolving market needs.
Our customer service team adheres to a professional, responsible and dedicated attitude and is always committed to providing customers with satisfactory services. We focus on communication with customers, actively listen to their needs and feedback, and strive to provide customers with efficient and timely support and solutions.
In short, as a microcavity substrate manufacturer, our company is committed to providing high-quality, innovative products and excellent customer service, working tirelessly for customer success and satisfaction.
What are the characteristics of great customer service?
Excellent customer service plays a key role in microcavity substrate manufacturing. Its characteristics are not only related to customer satisfaction, but also directly affect product quality and corporate image. Here are a few important characteristics of good customer service and how they translate into microcavity substrate manufacturing:
The first element of great customer service is technical professionalism. The customer service team needs to have deep technical knowledge and be able to understand customer needs and provide professional advice and solutions. In microcavity substrate manufacturing, the customer service team needs to understand the characteristics, design requirements, and manufacturing processes of different materials in order to provide customers with accurate technical support and consulting services.
Responding to customer needs promptly and quickly is one of the important manifestations of quality customer service. When customers raise questions or needs, they hope to receive timely responses and solutions. In microcavity substrate manufacturing, the customer service team needs to ensure rapid response to customers’ design modifications, material selection, order status and other issues to meet customer needs.
Good customer service should be able to provide customized services that are flexible and adaptable to the customer’s specific needs and requirements. In microcavity substrate manufacturing, customers may have different design requirements, material selection, and production volume requirements. The customer service team needs to be able to provide personalized solutions based on the customer’s specific situation to meet the customer’s specific needs.
Reliability is one of the core components of great customer service. Customers want to be able to rely on the products and services provided by suppliers with confidence, and do not want their own production processes to be affected by supplier problems. In microcavity substrate manufacturing, the customer service team needs to ensure the stability and consistency of product quality, as well as the timeliness of order delivery, so that customers can cooperate with confidence.
Professionalism is the basic quality of a customer service team. Customer service personnel need to have good communication skills, teamwork spirit and a high sense of responsibility, and be able to communicate and collaborate effectively with customers in a professional and courteous manner. In microcavity substrate manufacturing, the customer service team needs to work closely with customers to understand their needs and solve problems in a timely manner, providing customers with all-round support and assistance.
Through the embodiment of the above characteristics, high-quality customer service can not only improve customer satisfaction and loyalty, but also help companies establish a good reputation and brand image, thereby standing out in a fiercely competitive market and winning more customers and market share.
Frequently Asked Questions
What are the key benefits of using micro cavity substrates?
Micro cavity substrates offer several key benefits, including enhanced miniaturization of electronic devices, improved thermal management, and optimized signal integrity. By accommodating components within precisely engineered cavities, MCS enables higher component density, leading to more compact and lightweight devices. Additionally, the thermal properties of micro cavity substrates help dissipate heat efficiently, ensuring reliable performance even in demanding applications. Furthermore, the controlled impedance characteristics of MCS contribute to improved signal transmission and reduced electromagnetic interference, enhancing overall device performance.
How do micro cavity substrates differ from traditional PCBs?
Micro cavity substrates differ from traditional PCBs primarily in their design and functionality. While traditional PCBs consist of flat, uniform layers with components mounted on the surface, micro cavity substrates feature intricately engineered recesses or “cavities” that house components within the substrate. This design allows for tighter integration of components and improved thermal management, making micro cavity substrates ideal for compact and high-performance electronic devices.
What factors should I consider when selecting a micro cavity substrate material?
When selecting a micro cavity substrate material, several factors should be considered, including thermal conductivity, mechanical strength, dielectric properties, and compatibility with manufacturing processes. Materials such as ceramics offer excellent thermal conductivity and high temperature resistance, making them suitable for applications requiring robust thermal management. Alternatively, flexible materials like polyimide provide flexibility and bendability, ideal for applications with complex form factors or flexible designs.
Can micro cavity substrates be used in high-frequency applications?
Yes, micro cavity substrates can be used in high-frequency applications, provided they are designed and fabricated to meet the specific requirements of such applications. By carefully selecting substrate materials with low dielectric loss and optimizing design parameters such as trace width and spacing, micro cavity substrates can achieve the impedance control necessary for high-frequency signal transmission. Additionally, advanced fabrication techniques such as laser drilling and controlled impedance routing help ensure signal integrity and minimize electromagnetic interference in high-frequency circuits.