Micro LED PCB manufacturing. High speed and high frequency material Micro LED PCB and Micro HDI PCBs Vendor. we can make the best smallest vias holes size with 2mil(50um). and we also can produce the microtrace and smallest gap HDI PCBs from 4 layer to 30 layers.
In today’s electronic field, the rise of micro LED (Micro LED) technology is completely changing the pattern of the electronic display industry. As an important component supporting the application of micro-LED technology, printed circuit boards (PCBs) play a vital role. This article will delve into the manufacturing process, key materials, manufacturing-related costs and service quality of micro-LED PCB, providing readers with an in-depth understanding of the precision manufacturing process and industry development trends behind micro-LED technology.
What is Micro LED PCB?
Micro LED PCB is a printed circuit board specially designed for micro LED display technology. In the pursuit of higher image quality, lower power consumption and thinner display solutions, micro-LED technology has become the focus of the electronics industry. The design of micro-LED PCB has higher requirements than traditional LED PCB because micro-LEDs are smaller in size and have denser pixels, so they require more precise conductive paths and component connections. Micro LED PCB not only provides support and stable electrical connections for micro LED chips, but also needs to consider factors such as heat dissipation, optical matching, and mechanical stability.
In order to achieve high resolution and high image quality of micro-LED displays, the design of micro-LED PCBs needs to fully consider the layout of conductive paths, the design of laminate structures, and the selection of packaging technology. At micron-level dimensions, the width and spacing of wires must be precisely controlled to ensure stable transmission of electrical signals and good signal integrity. In addition, micro-LED PCB also needs to take into account special requirements in terms of high-frequency signal transmission, electromagnetic interference suppression, and anti-static capabilities.
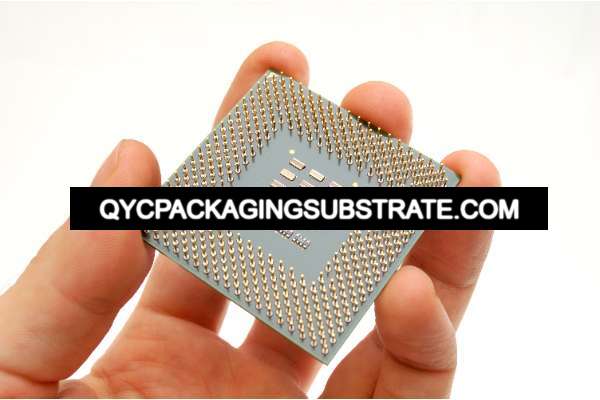
Micro LED PCB manufacturing
The manufacturing process of micro LED PCB is similar to traditional PCB manufacturing, but more complex and precise. From the selection of substrate materials to the control of electroplating processing, each step needs to be strictly controlled to ensure the quality and reliability of micro-LED PCBs. Especially when welding micro-sized micro-LED chips, advanced packaging technology and sophisticated automation equipment are required to ensure welding quality and production efficiency.
In short, micro-LED PCB, as a key component of micro-LED display technology, is crucial to achieving high-quality, high-performance display solutions. Through careful design and precision manufacturing, micro-LED PCB provides solid technical support and guarantee for the development of micro-LED displays.
How to design micro LED PCB?
Designing micro-LED PCB is a complex and critical process that requires rigorous steps and professional skills. First, the designer must capture a schematic of the circuit, which is the starting point of the design process. In the schematic diagram, the connection relationship of each component is clearly expressed, laying the foundation for subsequent layout and wiring.
Next is the component layout. The designer needs to reasonably arrange the position of each component on the PCB according to the functionality and space constraints of the circuit. This involves considering factors such as connections between components, signal transmission paths, and heat dissipation. Optimizing layout can maximize the performance of the circuit and help simplify subsequent wiring work.
Routing is another important step in design and involves translating the circuit connections in the schematic into an actual wire layout. Designers must carefully select wire paths to ensure stable and reliable signal transmission. In addition, wiring also needs to take into account issues such as power consumption, interference, and EMI of the circuit to ensure stable operation of the circuit.
After the wiring is completed, the designer needs to optimize the entire PCB layout. Using professional software, designers can adjust layouts to improve functionality, space utilization and manufacturability. The optimized layout can not only reduce PCB area and cost, but also improve manufacturing efficiency and product quality.
In general, designing micro-LED PCB is a comprehensive and highly technical task. Designers need to have rich circuit design experience and professional software operation skills to design micro-LED PCB products with excellent performance, stability and reliability.
How to make micro LED PCB?
The manufacturing of micro-LED PCB is a project that requires precise and meticulous operations. It involves multiple key links, each of which is crucial to the quality and reliability of the finished product. First, the manufacturing process begins with a preliminary design. At this stage, engineers capture and lay out circuit schematics based on customer needs and product specifications. They must take into account the special requirements of micro-LED display technology, such as high-density component layout and optimization of conductive paths.
Next comes the preparation phase of the substrate. In this step, choosing the appropriate substrate material is crucial to the performance of the micro-LED PCB. Common substrate materials include fiberglass-reinforced epoxy (FR-4), whose properties include excellent mechanical strength and electrical properties. Selecting the appropriate substrate thickness and size is also essential to ensure that the final micro-LED PCB meets the design requirements.
Next comes the process of copper layer deposition. The copper layer plays the role of a conductive path in micro-LED PCB, so its deposition quality directly affects the conductive performance of the circuit. Engineers use chemical methods or electroplating techniques to deposit a copper layer on the surface of the substrate, and then pattern it using photolithography to create the required conductive paths and connection points.
The next step in the manufacturing process is final inspection. At this stage, manufacturers conduct strict quality control and functional testing of the micro-LED PCB to ensure that it meets design specifications and customer requirements. The inspection process may include visual inspection, X-ray inspection, electrical testing and other methods to ensure the highest level of quality and reliability of the micro LED PCB.
In general, the manufacturing process of micro LED PCB requires careful control and coordination of all aspects. Only through precise operation and strict quality control can micro-LED PCB products with excellent performance, reliability and stability be manufactured, providing strong support for the application of micro-LED display technology.
How much does it cost to manufacture a micro LED PCB?
The manufacturing cost of micro LED PCB is a complex and multifaceted issue, which is affected by multiple factors. First of all, size is one of the important factors that determine the cost. Larger size micro-LED PCBs require more materials and processing time, so the cost is relatively high. In addition, complexity is also a key factor affecting cost. If the design of the micro-LED PCB is very complex, requiring dense wires and precise layout, then the manufacturing cost will rise. In terms of materials, the choice of substrate material, conductive material, and surface treatment will all have an impact on cost. For example, flexible substrates and metal substrates may be more expensive relative to traditional FR-4 substrates. In addition, quantity is also one of the factors affecting cost. Typically, high-volume production reduces the cost per unit, while low-volume production may result in higher unit costs.
Understanding these cost drivers is critical to budgeting and optimizing production costs. First of all, cost factors must be considered during the design stage, and costs can be reduced by simplifying the design or optimizing the layout. Second, choose the right materials and processing methods to balance cost and quality. At the same time, rationally plan production quantities and formulate appropriate production plans based on actual demand to avoid waste caused by overcapacity or undercapacity. In addition, working with suppliers to seek reasonable purchase prices and production cycles is also an important way to reduce costs.
To sum up, the manufacturing cost of micro-LED PCB is affected by multiple factors, including size, complexity, material and quantity, etc. Understanding and properly managing these cost drivers is of great significance to controlling production costs and improving competitiveness. Therefore, in the manufacturing process of micro-LED PCB, it is necessary to comprehensively consider various factors and formulate a reasonable production strategy to achieve dual optimization of cost and quality.
What are the manufacturing materials for micro LED PCB?
The material from which the Micro LED PCB is manufactured is a key factor in ensuring its performance and reliability. Usually, micro LED PCB uses a variety of materials, each playing a different role. From the substrate to the conductive path to the insulation protection, each material plays an important role.
First of all, one of the main substrate materials of micro-LED PCB is glass fiber reinforced epoxy resin (FR-4). FR-4 is a common substrate material with excellent insulation properties and mechanical strength, making it suitable for most micro-LED applications. Its stable performance and relatively low cost make it one of the preferred materials in PCB manufacturing.
Secondly, the conductive paths in micro-LED PCBs are mainly composed of copper. Copper is an excellent conductive material with good electrical conductivity and mechanical strength, which can ensure stable transmission of circuit signals. Copper is usually chemically etched or other processing processes to form the wires and connection points on the PCB, providing the necessary electrical connections for the micro-LEDs to function properly.
In addition, solder film is another important component in micro LED PCB for insulation and protection. Solder film is a material coated on the surface of PCB. It has excellent insulation properties and can effectively prevent short circuits between circuits and interference from the external environment. It can also protect copper wires from corrosion and mechanical damage, extending the life of micro-LED PCBs.
In addition to conventional materials, flexible substrates and metal substrates also play an important role in specific micro-LED PCB designs. Flexible substrates are made of soft materials and have the ability to bend and bend, making them suitable for applications that require curved shapes or where space is limited. Metal substrates have excellent heat dissipation performance and mechanical strength, and are suitable for micro-LED applications with high heat dissipation requirements, such as automotive headlights.
To sum up, the manufacturing materials of micro LED PCB include conventional materials such as glass fiber reinforced epoxy resin (FR-4), copper, and solder film, as well as advanced materials such as flexible substrates and metal substrates, which together constitute the core of micro LED PCB. The foundation provides solid support for the development and application of micro-LED technology.
Who will make the micro LED PCB?
In the context of the rapid development and widespread application of micro-LED technology, the importance of micro-LED PCB manufacturing has become increasingly prominent. To ensure the quality and reliability of micro-LED products, choosing the right manufacturer is crucial. In this regard, our company plays a key role.
As a leading electronics manufacturing service provider, we are committed to providing our customers with the highest quality micro LED PCB manufacturing solutions. We have advanced production equipment and technical teams capable of meeting micro-LED PCB manufacturing needs of various sizes and complexities.
Our manufacturing process strictly follows international standards and industry best practices to ensure that each micro LED PCB meets the highest quality standards. From material procurement to production process control, we strictly control every detail to ensure product stability and reliability.
In addition, our company has a professional customer service team that can promptly respond to customer needs and problems and provide customers with thoughtful technical support and solutions. We are committed to establishing long-term and stable cooperative relationships with our customers and providing reliable support and guarantee for their business development.
In short, as a leader in micro-LED PCB manufacturing, our company will continue to improve its technical level and service quality, provide customers with better products and services, and jointly promote the development and application of micro-LED technology.
What are the five qualities of great customer service?
Excellent customer service is a key component to the success of any business. It is not only the provision of products or services, but also the process of establishing and maintaining customer relationships. Here are five key attributes of great customer service, each of which is critical to ensuring customer satisfaction and loyalty.
Responsiveness: In today’s highly competitive business environment, prompt and effective responses to customer inquiries and questions are critical. Whether by phone, email, social media, or other channels, responding quickly to customers builds customer trust and satisfaction.
Empathy: Treating customers with compassion and understanding is crucial when dealing with their needs and issues. Employees should be able to put themselves in the shoes of customers and understand their feelings and needs to better meet their expectations.
Reliability: Consistently keeping promises and commitments to customers is the basis for building trust. Whether it’s a promise about product delivery time, service quality, or something else, companies must ensure their reliability and are critical to their customers’ trust.
Communication: Clear and transparent communication is key to building good customer relationships. During the service process, providing customers with the required information in a timely manner, explaining the details of the product or service, and warning customers of possible problems when possible can enhance customer trust and satisfaction with the company.
Problem Solving: Proactive problem solving and striving to achieve customer satisfaction are at the core of great customer service. When customers face difficulty or dissatisfaction, employees should be willing to take responsibility, take proactive steps to resolve the problem, and ensure that the customer is satisfied with the solution.
To sum up, great customer service is not just a behavior, but a culture and attitude. Through key traits such as responsiveness, empathy, reliability, communication, and problem-solving, businesses can build strong customer relationships, increase customer satisfaction, and succeed in a competitive market.
Frequently Asked Questions
What is the difference between Micro LED and traditional LED displays?
Micro LED displays differ from traditional LED displays primarily in their size and structure. While traditional LED displays utilize individual LEDs as pixels, Micro LED displays employ much smaller LED chips, typically less than 100 micrometers in size, allowing for higher pixel densities and enhanced image quality. Additionally, Micro LED displays offer superior brightness, contrast, and energy efficiency compared to their traditional counterparts.
How does the manufacturing process of Micro LED PCBs differ from standard PCBs?
The manufacturing process of Micro LED PCBs involves additional steps and higher precision compared to standard PCBs. Micro LED PCBs require ultra-fine conductive pathways and micro-sized components to accommodate the miniature LED chips. Specialized equipment and techniques are employed for precise placement, soldering, and encapsulation of the Micro LEDs, ensuring optimal performance and reliability of the final display.
What are the key challenges in manufacturing Micro LED PCBs?
Manufacturing Micro LED PCBs presents several challenges, including achieving uniformity in LED chip placement and bonding, managing heat dissipation in densely packed displays, and ensuring the integrity of ultra-fine conductive traces during fabrication. Additionally, handling and processing micro-sized components require advanced automation and quality control measures to minimize defects and ensure yield rates.
Can Micro LED PCBs be integrated into flexible displays?
Yes, Micro LED PCBs can be integrated into flexible displays, thanks to advancements in flexible substrate materials and manufacturing techniques. Flexible substrates such as polyimide allow for bending and shaping of the display, enabling innovative form factors and applications in wearable devices, curved screens, and automotive displays.
What are the advantages of Micro LED PCB displays over OLED displays?
Micro LED PCB displays offer several advantages over OLED displays, including higher brightness, longer lifespan, better color accuracy, and superior energy efficiency. Additionally, Micro LED displays are less susceptible to image burn-in and degradation over time, making them ideal for applications requiring continuous operation and high reliability.