What is the importance of micro LED substrates?
Micro LED Substrate Manufacturer , we mainly produce ultra-small trace and ultra-small spacing LED PCBs, small units size, smallest via holes size with 50um(2mil). we can produce the Micro LED PCB from 2 layer to 16 layers.
The rise of micro-LED technology is bringing revolutionary changes to the display industry. As the core component of Micro LED display, the importance of micro LED substrate cannot be underestimated. Below we will explore the importance of micro LED substrates and their role in Micro LED technology.
First of all, micro LED substrate is the key support for Micro LED display. Micro LED displays achieve higher brightness, higher resolution and lower energy consumption by integrating arrays of tiny LED lights directly onto the substrate. As the carrier of these LED lights and the basis for circuit connection, the micro LED substrate directly determines the performance and quality of the display.
Secondly, the design of micro LED substrate directly affects the manufacturing cost and reliability of Micro LED display. Reasonable substrate design can reduce manufacturing costs and improve production efficiency, while ensuring the stability and reliability of the display. Therefore, in the design and manufacturing process of Micro LED displays, it is crucial to choose a suitable micro LED substrate manufacturer.
In addition, the material and process selection of micro-LED substrates also have an important impact on the performance of the display. High-quality substrate materials can provide good heat dissipation and electrical performance, thereby ensuring the stability and long-term reliability of the display. Advanced manufacturing processes can improve the manufacturing accuracy and consistency of substrates, further improving the quality and performance of display screens.
Finally, the innovation and development of micro LED substrates promote the progress and application of Micro LED technology. With the continuous development of technology, the design and manufacturing technology of micro LED substrates are also constantly innovating and improving, laying a solid foundation for the wide application of Micro LED display technology. Therefore, as a key link in Micro LED technology, the importance of micro LED substrate will continue to increase with the development of Micro LED technology.
To sum up, micro LED substrate plays a vital role in Micro LED display technology. Its design, manufacturing and material selection directly affect the performance, cost and reliability of the display, while also promoting the continuous progress and application of Micro LED technology. Therefore, fully understanding and paying attention to the importance of micro LED substrates, choosing high-quality substrate manufacturers and appropriate design solutions will help achieve the successful application and promotion of Micro LED technology.
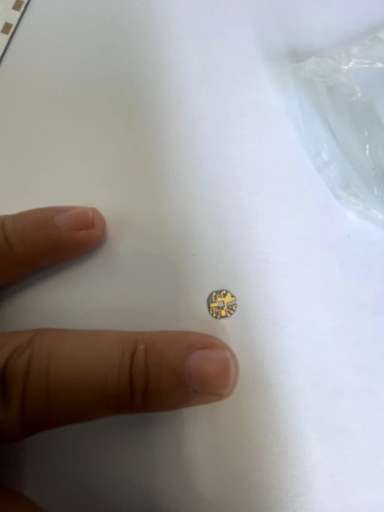
Micro LED Substrate
How to design micro LED substrate?
The design of micro LED substrate is one of the key steps in manufacturing high-quality Micro LED displays. Here are the key things to consider when designing micro LED substrates to ensure you are successful in the design process.
Before designing a micro LED substrate, you first need to clarify the circuit requirements. This includes determining the number, arrangement, drive circuit, power connection and possible additional functions of LED lamp beads. The key to this step is to understand the functional requirements of the Micro LED display and translate them into specific circuit design requirements.
When designing micro LED substrates, choosing the right software tools is crucial. Commonly used PCB design software such as Altium Designer, Cadence Allegro PCB, etc. provide a wealth of design functions and tools to help you complete complex circuit design and layout.
Schematic design in a software tool is the first step in designing a micro LED substrate. Convert circuit requirements into achievable circuit connections and functional structures by drawing circuit schematics. At this stage, factors such as the stability, reliability, and performance of the circuit need to be taken into consideration and ensure that design specifications and standard requirements are met.
Layout and routing is one of the key steps in micro LED substrate design. When designing the layout, factors such as the location, connection methods, signal transmission paths, and electromagnetic compatibility of circuit components need to be taken into consideration. Reasonable layout design can minimize signal interference and electromagnetic interference and improve the stability and reliability of the circuit.
After completing the layout design, circuit simulation and verification need to be performed. Through simulation analysis, the performance and stability of the circuit can be evaluated, and potential problems can be discovered and solved in a timely manner. The verification phase usually includes prototyping and experimental testing to verify the feasibility and correctness of the design.
Designing micro LED substrates is an iterative process that requires constant optimization and improvement. After problems are discovered during the verification phase, the design solution needs to be adjusted in time and simulated and verified again. Through continuous design optimization, the performance and reliability of micro-LED substrates can be maximized.
When designing micro LED substrates, the actual requirements for manufacturing need to be taken into consideration. This includes selecting appropriate materials and processes, optimizing layout design to reduce manufacturing costs, improving production efficiency, etc. Working closely with manufacturers to understand their production capabilities and technology levels can help optimize designs and achieve better manufacturing results.
With the above key steps, you can better understand how to design micro LED substrates and be successful in the design process. Remember, designing micro LED substrates is a complex and critical process that requires comprehensive consideration of circuit requirements, software tools, layout and routing, simulation verification and other aspects to ensure that the final design meets the performance and quality requirements of Micro LED displays.
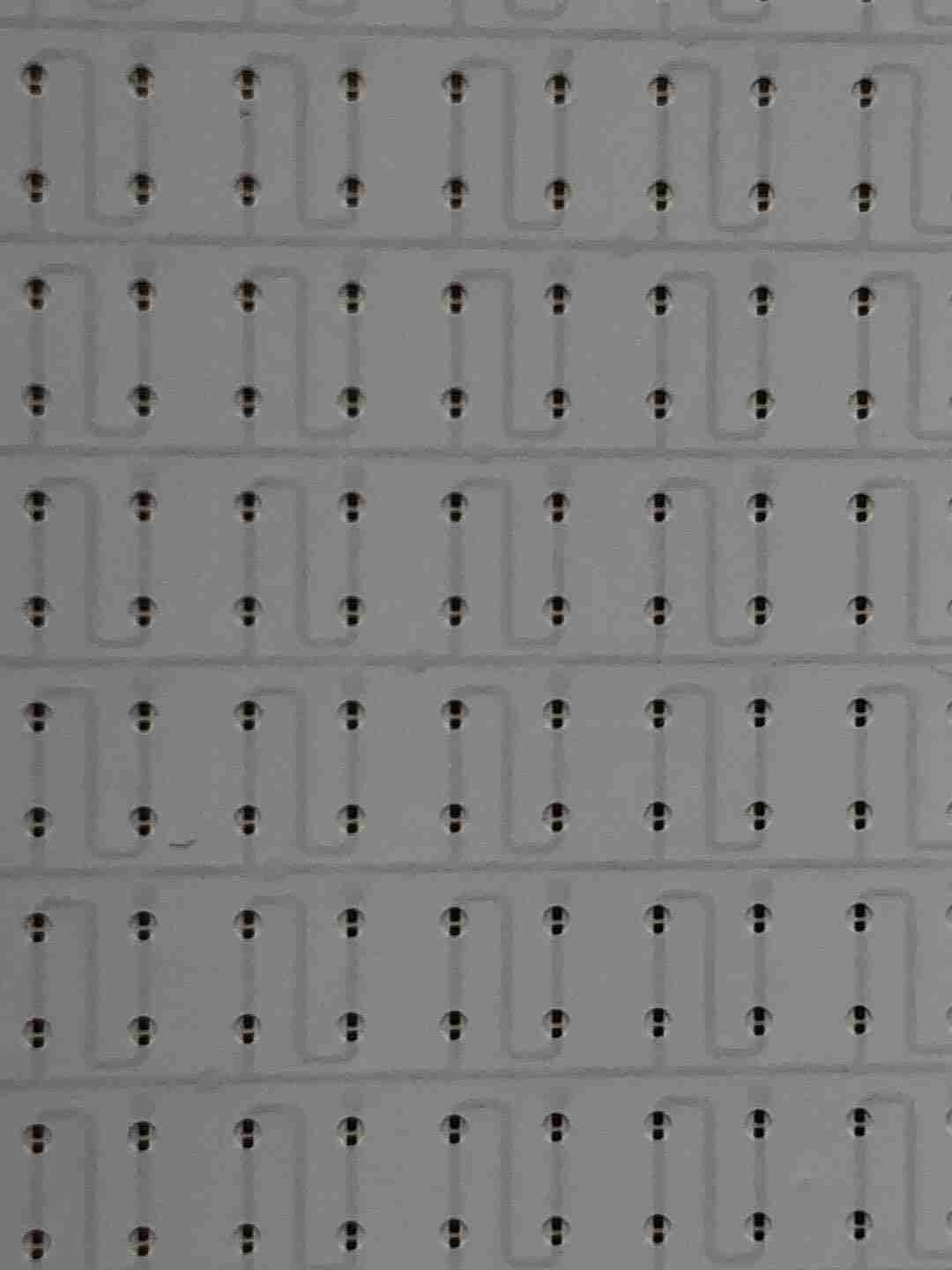
Micro LED Substrate
What is the manufacturing process of micro LED substrates?
When we use micro LED displays, few people think about the complicated manufacturing process behind them. However, the manufacturing process of micro LED substrates is a precise and complex process. Let’s take a deeper look at how micro LED substrates are manufactured.
The first step in manufacturing micro LED substrates is to prepare the required raw materials. These raw materials usually include substrate materials (such as glass, silicon-based materials, etc.), conductive materials (such as copper), insulating materials (such as resin), covering materials (such as light-curing resin), etc. The selection of these materials is critical to the performance and reliability of the substrate.
Before manufacturing micro LED substrates, detailed design and layout work is required. This includes determining circuit requirements, designing circuit schematics, layout and routing, etc. Accuracy during the design phase directly affects the performance and quality of the final substrate.
Once the design is complete, the next step is to print a conductive layer on the surface of the substrate. This is typically achieved by printing conductive ink or metal films onto the substrate surface. The accuracy and uniformity of the conductive layers are critical to the stability of the circuit.
After printing the conductive layer, chemical etching is required to remove excess metal to form the required circuit pattern. This step requires precise control of the concentration and temperature of the chemical solution to ensure accuracy and consistency of corrosion.
After completing the circuit pattern, holes need to be drilled into the substrate to mount the components. These holes may be used for soldering, inserting connectors, or mounting other electronic components. The accuracy and precision of drilling are critical to the stability and reliability of the circuit.
After drilling is completed, a layer of metal needs to be plated on the hole wall to ensure good electrical conductivity and connectivity. This is usually achieved by chemical deposition or electroplating methods.
After completing all manufacturing steps, the micro LED substrate needs to be subjected to final inspection. This includes checking circuit connectivity, uniformity of conductive layers, quality of holes, etc. Only after passing strict inspection can the substrate be considered qualified.
Through the above steps, micro LED substrate manufacturers can produce high-quality, reliable substrates, providing a solid foundation for the application of Micro LED display technology.
How much does a micro LED substrate cost?
The rapid development and widespread application of micro-LED technology makes the cost of micro-LED substrates become increasingly important. However, there are several factors to consider when understanding the cost of micro LED substrates. Let’s dig a little deeper.
The size and selected materials of the micro LED substrate are one of the important factors that determine the cost. Generally speaking, larger substrate sizes and the use of high-quality materials result in higher costs. For example, choosing high-quality substrate materials such as glass substrates instead of conventional substrate materials may increase manufacturing costs.
The number of layers and complexity of micro-LED substrates also have a significant impact on cost. Substrates with more layers and more complex wiring usually increase manufacturing costs. This is because increasing the number of layers increases complexity in the manufacturing process, and complex wiring requires more processing steps and precision equipment.
Production scale is another important factor affecting the cost of micro LED substrates. Generally speaking, mass production allows for greater efficiency and lower unit costs. Therefore, the cost of substrates for mass production may be lower than that for small-scale production.
Manufacturing micro LED substrates requires advanced technology and equipment. Manufacturers incur costs to invest in and maintain these technologies and equipment, and these costs will also be reflected in the final substrate price. Therefore, choosing advanced technology and equipment may result in higher manufacturing costs.
Some customers may have specific customization needs, such as special sizes, special materials, or special process requirements. Meeting these custom requirements may increase manufacturing costs as they may require additional engineering and production adjustments.
To sum up, the cost of micro LED substrates is affected by multiple factors, including substrate size and material, number of layers and complexity, production scale, technology and equipment investment, and customization requirements. Therefore, when selecting a micro LED substrate manufacturer, these factors need to be considered comprehensively to balance cost and quality to achieve the best production cost-benefit ratio.
What materials are micro LED substrates made of?
Micro LED substrate is the core component of Micro LED display technology, and its constituent materials are crucial. Let’s take a deeper look at what materials micro LED substrates are made of.
First of all, micro LED substrates usually consist of key materials such as substrate, conductive layer, insulating layer and covering layer. Among them, the substrate is the key component for support and electrical connection. Common substrate materials include glass, polyimide (PI), polyamide (PA), plexiglass (FR-4), etc. Different substrate materials have different performance characteristics, such as thermal stability, mechanical strength and electrical properties.
The conductive layer is another important component of the micro LED substrate, which is usually composed of copper foil or other conductive materials. The conductive layer is responsible for transmitting electrical signals to the Micro LED chip to achieve the light-emitting effect of the LED. Copper foil is one of the most commonly used conductive materials and is widely favored for its good conductivity and processability.
Insulating layers are placed above and below the conductive layers to isolate circuits between different layers and prevent short circuits and electrical interference. Common insulation materials include polyimide (PI), polytetrafluoroethylene (PTFE), epoxy resin, etc. These materials have excellent insulating properties and heat resistance, and can protect the circuitry of the substrate from the external environment.
Finally, the overlay is used to protect the surface of the microLED substrate and provide additional protection and aesthetics. Common covering materials include photosensitive resin, polyimide film, etc. These materials have excellent weather resistance and optical transparency, and can protect LED chips from dust, moisture and mechanical damage.
Overall, micro LED substrates are composed of a variety of materials, each of which plays a key role in ensuring the performance and reliability of Micro LED displays. Choosing the right material combination and manufacturing process is critical to the successful application of Micro LED technology.
Who is making micro LED substrates?
For the manufacturing of micro LED substrates, choosing the right supplier is crucial. In this field, our company is committed to becoming your reliable partner. Our company is a professional micro LED substrate manufacturer, committed to providing customers with high-quality, high-performance substrate solutions.
Our manufacturing process strictly follows industry standards and incorporates the latest technology and innovation. We have advanced production equipment and technical team to meet the needs and requirements of different customers.
As your supplier, we will work with you to understand your specific needs and provide customized solutions. Our team will provide you with professional technical support and services to ensure your project goes smoothly and is successful.
The quality of our products has been widely recognized and deeply trusted and praised by customers. We constantly pursue excellence and constantly improve and enhance our product quality and service levels to meet the growing needs of our customers.
Choose us as your micro LED substrate manufacturer and you will receive high quality products, competitive prices, timely delivery and excellent customer service. We look forward to establishing a long-term and stable cooperative relationship with you and growing together.
What are the five qualities of great customer service?
Excellent customer service is one of the keys to the success of every business. It’s more than just responding to customers and solving problems, it’s the key to building long-term relationships and enhancing brand loyalty. Here are five key qualities that make up great customer service:
Professionalism: The number one quality of good customer service is professionalism. This includes having good product knowledge, skills and experience to be able to provide accurate, timely information and solutions. Professionalism is also reflected in communication with customers, expressed through courtesy, patience and respect.
Prompt response: In customer service, prompt response is crucial. Customers expect prompt responses and solutions when they encounter problems or have questions. Prompt responses not only solve problems but also enhance customer satisfaction and trust.
Personalized care: Personalized care is an important means to improve customer service quality. By understanding customer needs, preferences and history and customizing personalized solutions and services, customers can feel valued and cared for, thereby enhancing customer satisfaction and loyalty.
Problem Solving Skills: Another important attribute of great customer service is good problem solving skills. When customers encounter problems or difficulties, being able to solve the problem quickly and effectively and provide a solution that satisfies the customer is one of the keys to high-quality customer service.
Continuous Improvement: Continuous improvement is the foundation of excellent customer service. Enterprises need to constantly reflect on and improve customer service processes and experiences to adapt to market changes and changes in customer needs. Only by continuously improving customer service levels can we stand out in the fierce competition and win the trust and support of customers.
To sum up, the five characteristics of excellent customer service include professionalism, timely response, personalized care, problem solving and continuous improvement. Only enterprises with these characteristics can succeed in the fiercely competitive market and win the long-term support and trust of customers.
FAQS
How long does the manufacturing process of micro LED substrates take?
The manufacturing time of micro LED substrates depends on several factors, including design complexity, production scale and manufacturer’s production capabilities. Generally speaking, it can take anywhere from a few weeks to a few months to go from design to production of a complete micro-LED substrate.
How to choose the right micro LED substrate manufacturer?
Choosing the right micro LED substrate manufacturer is key. You can consider the manufacturer’s experience, technical level, production capacity, quality control system, and responsiveness to customization needs. It is best to choose a manufacturer with extensive experience and a good reputation.
What are the cost factors for micro LED substrates?
The cost of micro LED substrates is affected by multiple factors, including substrate size, material selection, number of layers, complexity, and production quantity. Manufacturers often provide customized quotes based on the customer’s specific needs.
How to optimize micro-LED substrate design to reduce costs?
To reduce the cost of micro-LED substrates, strategies such as reducing the number of layers, optimizing wiring and spacing, selecting cost-effective materials, and increasing production scale can be considered. In addition, working closely with manufacturers to seek their suggestions and optimization solutions is also an effective way to reduce costs.
In what application fields are micro LED substrates widely used?
Micro LED substrates are widely used in display technology, lighting, automotive electronics, smart wearable devices and other fields. With the continuous advancement of technology, the application fields of micro LED substrates are constantly expanding and deepening.
What professional equipment is needed to manufacture micro LED substrates?
Manufacturing micro LED substrates requires a series of professional equipment, including printing equipment, chemical etching equipment, drilling machines, metallization equipment, and inspection equipment. These equipment are usually provided and operated by professional PCB manufacturers.