Microtrace Package Substrates Manufacturing, we mainly produce ultra-small bump pitch substrate with 100um, Microtrace and spacing packaging substrate with 9um to 30um. and from 30 to 80um gap substrates will be more easy manufacturing.
In today’s highly developed electronic field, 30 micron substrates play a vital role. This thin yet strong substrate has excellent electrical properties and unique properties, making it a highly regarded and critical component of packaging technology.
The 30-micron substrate stands out for its exceptionally slim profile, a distinctive characteristic that contributes to the lightweight and compact design of contemporary electronics. Despite its minimal thickness, the 30-micron substrate excels in delivering outstanding electrical performance, establishing a sturdy foundation for the stable and efficient operation of electronic devices.
Moreover, the 30-micron substrate boasts remarkable thermal conductivity properties, a feature instrumental in managing the heat generated by electronic equipment during high-load operations. This makes it a preferred choice for chip packaging with high-performance and high-density layouts, offering reliable support for the prolonged and stable operation of electronic products.
With the escalating demand for thinner, lighter, and higher-performing electronics, the manufacturing process of 30-micron substrates has become a focal point in the realm of packaging technology. This article will delve into the intricacies of the manufacturing steps for 30-micron substrates, encompassing processes such as photolithography, thin film deposition, preparation processes, and copper foil bonding. This exploration aims to unveil the profound impact of each step on the final product’s performance.
This in-depth look at 30 micron substrate manufacturing is intended to provide readers with a comprehensive understanding of this critical packaging technology, highlighting its importance in driving the continued advancement of the electronics industry.
Definition of 30 micron substrate
In the field of packaging technology, 30 micron substrate refers to a substrate material with a thickness of 30 microns, which is usually composed of multi-layer films and composite materials. Substrates of this size play a key role in modern electronics manufacturing. The 30 micron substrate thickness is achieved through a precision manufacturing process whose precision and stability are critical to the performance of the packaging technology.
30 micron substrates are widely used in the manufacturing of various electronic devices in packaging technology. The substrate’s low profile design makes it ideal for advanced packaging solutions. Its main application areas include but are not limited to chip packaging, integrated circuit manufacturing and system packaging. In chip packaging, the 30-micron substrate provides a compact structure, helping to achieve highly integrated circuit layout and improve device performance and efficiency. At the same time, its use in system packaging makes electronic products thinner, lighter, more efficient, and suitable for increasingly miniaturized electronic devices.
The 30-micron substrate also shows strong potential in emerging technology fields, such as 5G communications, Internet of Things, and artificial intelligence. Its thin design maximizes the use of space between electronic components, providing higher performance and smaller size for a new generation of electronic products.
Overall, the application fields of 30-micron substrates continue to expand, and their key role in packaging technology drives the continuous innovation and development of the electronics industry.
Key steps in the manufacturing process
In the process of manufacturing 30 micron substrates, execution of key steps is critical to achieving high quality and reliability. Below is a detailed description of these key steps:
Lithography: the precise process that defines the structure of a substrate
Photolithography is a sophisticated pattern transfer process that uses light-sensitive substances and photoresists to precisely define the structure of a substrate. In this step, a photoresist layer is first covered with a mask and then exposed using ultraviolet light, which causes chemical changes in specific areas of the photoresist. Next, a development and etching step is performed to define the structure of the 30-micron substrate by removing unnecessary parts.
Thin film deposition: precise coverage of substrate surface material
Thin film deposition is a key process for depositing materials on a substrate surface. Ensure film uniformity and consistency by controlling deposition parameters such as temperature and gas concentration.
Preparation process: Prepare the substrate to a thickness of 30 microns
The preparation process involves preparing layers of material to a thickness of 30 microns. This may involve multiple rounds of deposition and etching steps to gradually achieve the desired substrate thickness. Precise control of parameters at each step, such as deposition rate and etch rate, is critical to ensuring the final thickness and flatness of the substrate.
Copper Foil Bonding: The Key Role of Copper Foil in the Manufacturing Process
The copper foil bonding process is integral to the manufacturing of 30-micron substrates, playing a crucial role in enhancing their electrical conductivity and heat dissipation properties. This step involves securely attaching the copper foil to the substrate’s surface under high temperature and pressure conditions. This not only elevates the electrical performance of the substrate but also reinforces its overall strength and durability.
The effective execution of these key steps is key to ensuring the success of 30 micron substrate manufacturing, providing a solid foundation for high-performance packaging technology.
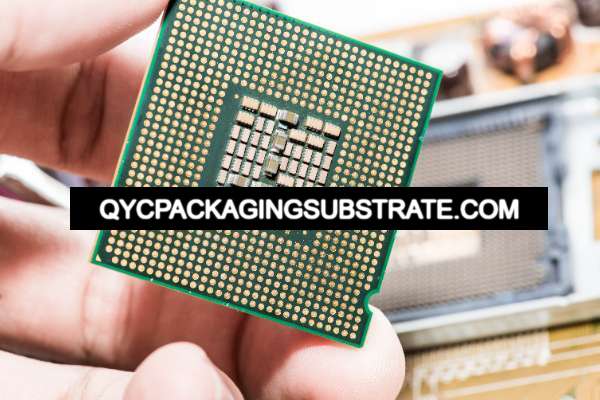
Microtrace Package Substrates
Selection of manufacturing materials
In the manufacturing process of 30 micron substrates, material selection is crucial and directly affects the performance, reliability and sustainability of the substrate. Here are the key material properties and sustainable practices involved in this manufacturing process.
Thin film material
Low Dielectric Constant: Choosing materials with low dielectric constant helps reduce signal attenuation during signal transmission.
Thermal stability: Materials are required to maintain stability in high temperature environments to ensure that they will not be deformed or damaged during manufacturing and use.
Copper foil
High conductivity: Use high conductivity copper foil to ensure the transmission efficiency of electrical signals on the substrate.
Good mechanical properties: Copper foil should have sufficient strength and toughness to cope with the mechanical stresses during manufacturing and use.
Thin film deposition materials
Uniformity: Ensure uniform distribution of materials during film deposition to prevent uneven films from causing unstable performance.
Green material selection
Prioritize renewable resources and recyclable materials to reduce reliance on limited resources.
Use materials that do not contain harmful substances to reduce the risk of environmental pollution.
Energy Efficiency
Optimize manufacturing processes by employing energy-efficient equipment to minimize energy wastage in production.
Investigate and implement the utilization of renewable energy sources to decrease reliance on non-renewable alternatives.
Circular economy principles
Design the substrate structure to make it easier to recycle and reuse.
Reduce waste generation and maximize resource utilization by optimizing the manufacturing process.
Careful selection of material properties and adoption of sustainable practices in 30 micron substrate manufacturing will help achieve high-performance substrates and drive the electronics industry in a more environmentally friendly and sustainable direction. This not only helps improve product quality but also helps meet growing sustainability standards and consumer expectations.
Technological innovations and trends
Cutting-edge photolithography technology has emerged as a critical factor in enhancing accuracy and production efficiency for the fine structures of 30-micron substrates. Employing advanced techniques like multi-beam lithography and extreme ultraviolet lithography enables manufacturers to achieve superior resolution and precision in substrate manufacturing.
Advanced preparation process: New preparation methods based on etching and etching bring higher production efficiency and cost-effectiveness to the manufacturing of 30-micron substrates. These innovations improve the controllability and stability of the preparation process.
Anticipate future trends, including possible improvements and adoption of new technologies
Flexible substrate materials: With the rise of wearable devices and flexible electronics, 30 micron substrate manufacturing may pay more attention to flexible substrate materials in the future. This includes the use of curved and foldable materials to accommodate increasingly diverse electronic product designs.
Anticipated as a significant stride toward sustainability, the future is poised to witness a surge in the application of biodegradable materials. This strategic shift is driven by a commitment to reduce environmental impact and represents an innovative trajectory within the substrate manufacturing industry, aligning with broader sustainability practices.
Overall, future trends will focus on higher precision, more flexible design, and more sustainable material selection, bringing broader development space to the field of 30-micron substrate manufacturing. These innovations will not only improve substrate performance but also drive the entire electronics industry toward a more sustainable and advanced future.
Application of 30 micron substrates in the electronics industry
30 micron substrates play a key role in electronics, providing superior performance and reliability for a variety of devices. Among them, mobile phones are a significant application area. Modern smartphones are becoming smaller and lighter, and the use of 30-micron substrates makes the design of mobile phone chips more compact, providing space for more advanced functions. In addition, consumer electronics such as tablets, portable audio equipment, and cameras also widely adopt 30-micron substrates to meet the demand for high performance and miniaturization.
In the industrial sector, embedded systems are another prominent application case. These systems require highly integrated electronic components to fit within tight space constraints and maintain superior performance. 30 micron substrates have enabled embedded systems to achieve great success in industrial automation, control systems and instrumentation by providing highly integrated solutions.
The incorporation of 30-micron substrates has markedly influenced the performance of electronic devices. Primarily, owing to its slim profile, the 30-micron substrate significantly diminishes the overall dimensions and weight of the electronic device, rendering it more lightweight and portable. Additionally, with its highly integrated design, the 30-micron substrate facilitates a more compact electronic path, thereby reducing signal transmission delays and enhancing the device’s responsiveness, particularly in high-frequency applications.
In addition, 30 micron substrates also have advantages in thermal management. Its thin design helps dissipate heat and improves the stability of the device under high-load operation. This is of great significance for electronic equipment that requires long-term high-performance operation, such as data center servers and high-performance computers.
In general, the widespread application of 30-micron substrates has brought smaller, lighter, faster and more stable performance to electronic devices, promoting the continuous innovation and development of the electronics industry.