Microtrace RF Circuit Board Manufacturer.Microtrace RF Circuit Board Manufacturer specializes in producing high-quality RF circuit boards with advanced microtrace technology. Our cutting-edge manufacturing processes ensure precise signal integrity and superior performance for a wide range of applications, from telecommunications to aerospace. Trust Microtrace for innovative solutions that meet the most demanding RF requirements.
Microtrace RF Circuit Boards are specialized printed circuit boards (PCBs) designed for high-frequency and high-performance applications. These boards are critical in sectors such as telecommunications, aerospace, defense, and advanced consumer electronics, where precise signal integrity and minimal interference are paramount. Microtrace RF Circuit Boards incorporate advanced materials and manufacturing techniques to ensure optimal performance in demanding environments.
What is a Microtrace RF Circuit Board?
A Microtrace RF Circuit Board is a type of PCB specifically designed to handle radio frequency (RF) signals, which typically range from 1 MHz to 300 GHz. These boards are characterized by their ability to support fine-line traces, which are essential for maintaining signal integrity and minimizing loss at high frequencies.
High-Frequency Capability:Designed to handle RF signals efficiently with minimal loss and interference.
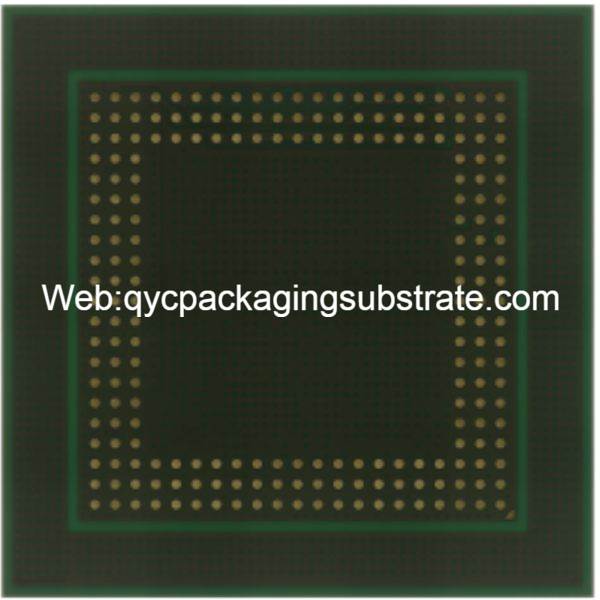
Microtrace RF Circuit Board Manufacturer
Fine-Line Traces:Supports very fine conductive traces, crucial for maintaining signal integrity at high frequencies.
Advanced Materials: Utilizes specialized materials with low dielectric constants and low loss tangents.
Thermal Management:Incorporates efficient heat dissipation techniques to ensure stable performance.
Precision Manufacturing: Employs advanced fabrication techniques to achieve the necessary precision and performance.
The Design Reference Guide for Microtrace RF Circuit Boards
Designing Microtrace RF Circuit Boards involves meticulous planning and advanced engineering to meet the stringent requirements of high-frequency applications.
Substrate Materials:High-performance materials such as PTFE (Polytetrafluoroethylene), Rogers, and other low-loss laminates are used to ensure minimal signal loss and stable performance.
Conductive Materials: High-purity copper is commonly used for traces due to its excellent electrical conductivity.
Multi-Layer Construction:Often involves multiple layers to support complex circuits and high-density interconnections.
Controlled Impedance:Essential for maintaining consistent signal quality, especially in high-frequency applications.
Heat Dissipation Techniques:Use of thermal vias, heat sinks, and advanced materials with high thermal conductivity to manage heat effectively.
Thermal Simulation:Advanced simulation tools are used to predict and manage heat distribution across the board.
Minimizing Signal Loss:Achieved through careful material selection, precise trace width control, and proper impedance matching.
EMI Shielding: Techniques such as ground planes and shielding layers are employed to protect signals from external noise and interference.
Advanced Lithography:High-precision lithography techniques are used to define fine-line traces accurately.
Etching and Plating: Precision etching and plating processes ensure the accurate formation of conductive paths.
What Materials are Used in Microtrace RF Circuit Boards?
Microtrace RF Circuit Boards are constructed using materials that provide optimal performance at high frequencies.
PTFE (Polytetrafluoroethylene): Known for its low dielectric constant and low loss tangent, making it ideal for high-frequency applications.
Rogers Laminates:A range of high-performance materials designed for RF and microwave applications, such as Rogers 4350B and 5880.
Ceramic-Filled Laminates:Provide a combination of low dielectric constant and high thermal conductivity, suitable for high-power applications.
High-Purity Copper:Used for signal traces due to its excellent electrical conductivity and minimal signal loss.
Gold Plating: Sometimes used for surface finishes to enhance conductivity and protect against oxidation.
Low-Dk Dielectrics:Materials with low dielectric constants minimize signal delay and distortion, ensuring high-speed data transmission.
Thermal Interface Materials: Enhance heat dissipation between the board and heat sinks or other cooling solutions.
What Size are Microtrace RF Circuit Boards?
The size of Microtrace RF Circuit Boards varies based on the application and design requirements, but they are generally designed to be compact and efficient.
Custom Dimensions:Designed to fit specific applications, ranging from small, intricate designs for portable devices to larger formats for more complex systems.
Panel Sizes: Fabrication often starts with standard panel sizes, which are then cut and processed to the required dimensions.
Thin Layers:The total thickness can be as low as a few mils, depending on the design and application.
Variable Thickness: Depending on the number of layers and the specific requirements, the overall thickness can be adjusted to balance performance and mechanical stability.
The Manufacturing Process of Microtrace RF Circuit Boards
The manufacturing process of Microtrace RF Circuit Boards involves several precise steps to ensure the final product meets high-frequency performance standards.
CAD Design: Detailed design using computer-aided design (CAD) software, incorporating all components, layers, and electrical paths.
Simulation: Electrical, thermal, and mechanical simulations are conducted to optimize the design for performance and reliability.
Substrate Preparation: High-quality substrates are prepared, often involving multiple layers for complex designs.
Lamination: Layers are laminated together using advanced processes to ensure uniformity and adhesion.
Photolithography:High-precision photolithography is used to define the circuit patterns on the substrate.
Etching:Chemical or plasma etching processes remove unwanted material to form the conductive traces and structures.
Micro Drilling:Laser or mechanical drilling creates vias and holes for inter-layer connections.
Plating: Copper and other materials are plated onto the vias and holes to establish electrical connectivity.
Surface Finish:Applying surface finishes such as ENIG (Electroless Nickel Immersion Gold) or HASL (Hot Air Solder Leveling) to protect the copper and enhance solderability.
Assembly:Components are mounted using surface-mount technology (SMT) or through-hole technology (THT) as required.
Electrical Testing:Rigorous tests are conducted to ensure all connections are intact and the board functions as intended.
Thermal Testing: Thermal tests verify the board’s ability to dissipate heat and maintain performance.
Final Inspection:A thorough inspection ensures the board meets all design specifications and quality standards.
The Application Area of Microtrace RF Circuit Boards
Microtrace RF Circuit Boards are used in various high-performance applications where precise signal integrity and minimal interference are essential.
Telecommunications: Used in RF modules, antennas, and base stations for mobile networks and wireless communication systems.
Aerospace and Defense: Deployed in radar systems, communication equipment, and electronic warfare systems where performance and reliability are critical.
Medical Devices:Integrated into medical imaging equipment, diagnostic instruments, and wireless medical devices, where precision and reliability are essential.
Automotive:Used in advanced driver-assistance systems (ADAS), vehicle-to-everything (V2X) communication, and infotainment systems, where high-frequency performance is required.
Consumer Electronics:Found in smartphones, tablets, and wearable devices, where compact design and high-frequency performance are needed for advanced functionality.
What are the Advantages of Microtrace RF Circuit Boards?
High-Frequency Performance: Optimized materials and construction techniques ensure minimal signal loss and distortion, providing superior high-frequency performance.
Space and Weight Savings: The fine-line traces and compact design allow for more compact and lightweight devices.
Thermal Management:Efficient heat dissipation techniques maintain performance and reliability in high-power and high-frequency applications.
Reliability: High-quality materials and precise manufacturing processes ensure long-term reliability and performance in demanding environments.
Versatility:Can be tailored to specific applications with custom dimensions and layer stack-ups, providing flexibility in design.
FAQ
What materials are used in Microtrace RF Circuit Boards?
Microtrace RF Circuit Boards use advanced materials like PTFE, Rogers laminates, ceramic-filled substrates, and high-purity copper foils.
How are Microtrace RF Circuit Boards manufactured?
The manufacturing process involves CAD design, material preparation, photolithography, etching, drilling, plating, finishing, and rigorous testing and quality control.
In which industries are Microtrace RF Circuit Boards most commonly used?
They are commonly used in telecommunications, aerospace and defense, medical devices, automotive, and consumer electronics.
What are the main benefits of using Microtrace RF Circuit Boards?
The main benefits include high-frequency performance, space and weight savings, thermal management, reliability, and versatility.
What sizes are available for Microtrace RF Circuit Boards?
These boards can be custom-designed to specific dimensions, with thicknesses as low as a few mils, depending on the application and performance requirements.